NECは、IoTやAIなどの先進技術を活用した次世代のものづくりを具現化する共創型体験スペース「NEC DX Factory」を本年6月に同社玉川事業場(川崎市中原区)に開設した。そして昨日(11月21日)、開設当初に体験可能だった11のソリューションを15へ拡大。NECが見据える「デジタルツイン」を前提としたものづくりの世界観へさらに近づいた。
このほど、「NEC DX Factory」を体験するため同社を訪問。同社ものづくりソリューション本部 事業主幹の関行秀氏(写真右)と、同じくものづくりソリューション本部 技術主幹の北野芳直氏(写真左)に案内していただいた。
NECだからできる、デジタルツインのデモ環境
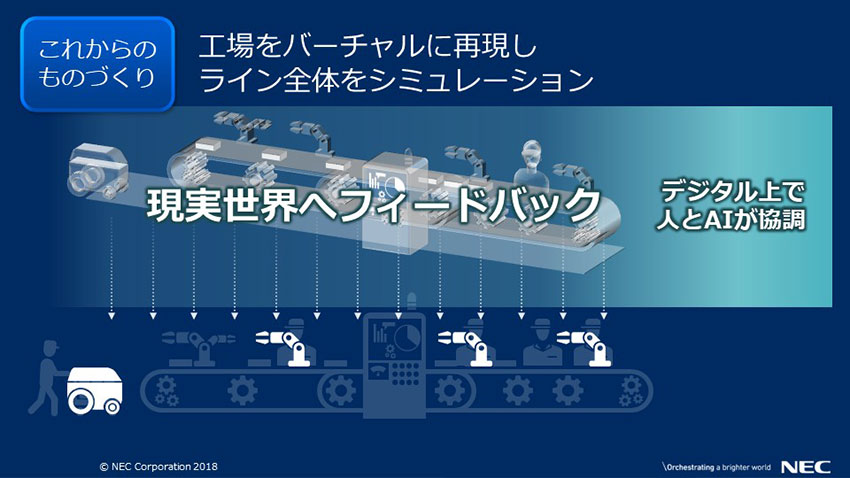
「NEC DX Factory」のコンセプトは、「デジタルツイン」を前提とした次世代のものづくりだ。現実空間(フィジカル空間)のモノやヒト、設備をデジタル空間に再現。設計から生産ライン、出荷、物流までのバリューチェーン全体をシミュレーションしたうえで、生産ラインを自律制御する。これにより、生産性の向上や納期の短縮のみならず、「マスカスタマイゼーション」(多品種少量生産)への対応が可能となる。
デジタルツインを実現するには、バリューチェーンの各システムを統合した環境が必要だ。「NEC DX Factory」では11月21日からのリニューアルにより、新たに「PLM-SCM-MES/IoT連携」の機能を追加(詳しくは後述)。これにより、デジタルツインを前提とした生産ラインのデモ環境を構築した。NECは既にこのしくみを自社工場のモデルラインで実践し、50%の生産性向上を実証済みだ。電機メーカーとしてものづくりの革新に取り組みながら、そのノウハウをもとにシステム開発も行ってきた「両輪」を持つNECだからこそ実現したデモ環境だと言える。
「NEC DX Factory」は、同社が2012年10月から行ってきた「ものづくり共創プログラム」の一環である。このプログラムの重要な取り組みの一つは、NECの「匠」によるパートナーの改革支援だ。NECはものづくりを行うメーカーであり、独自の改革ノウハウがある。そこで、実際にNECの生産革新に関わった「匠」と称される担当者がパートナーの現場に赴いて改革支援を行うのだ。
そして、同プログラムの根幹となる取り組みが「ものづくり研究グループ」だ。会員は1,133社、4,435名(本年10月31日時点)。7割強が製造業の会社だ。「ロジスティクス分科会」や「Industrial IoT研究会」など9つの分科会・研究会に分かれ、毎回、個別のテーマについて議論を行ったり、会員企業の工場見学を行ったりする場を提供してきた。
こうした「共創」の取り組みを通して、IoTに関して言えば、「ようやくつながり始めた」と関氏は感触を述べる。そして、次はいよいよデジタルツインだという。
「デジタルツインの世界観について、資料やパワーポイントを使って説明しても、製造業のお客様にはなかなかイメージを持ってもらえません。また、カタログスペックとして可能であっても、実際に試してみると前後の工程の調整やロボットのティーチングなど考慮しなければならないことが多く、うまくいかないことがほとんどです。実物を見ながら議論をしないと机上の空論になってしまいます」(関氏)
そこで誕生したのが「NEC DX Factory 共創スペース」だ。「実機があるとお客様から色々な発想が生まれてきます。こんなことはできないか、もっとこうした方がいいのではないかと、NECだけでは気づかないことをフィードバックしていただけます。私たちもそうした気づきを通して自社の改革を行い、さらにそれをソリューションとしてお客様に提供してきたいと考えています」と関氏は説明する。
マスカスタマイゼーションに対応した生産ラインを体験
では、「NEC DX Factory」に実装されているソリューションについて、生産ラインの工程に沿って紹介していこう。多くがNEC独自の技術だが、同社だけで完結できないものも当然ある。そこで、他社のさまざまな技術が実装されており、そうしたソリューション側の「共創」も「NEC DX Factory」の特徴だ。
まず、オムロン製のAGV(自動搬送機)が、部品(半導体の基板)を届けにくる。このAGVはデジタルツインと連携しており、デジタル空間にある生産計画と位置情報にもとづいて自律的に動く。
次に、AGVが届けた基板をデンソーウェーブ製の人協働ロボット「COBOTTA」が器用につかむ。COBOTTAはその基板をコンベアの上にのせて搬送する前に、小型カメラの前に運びだす(下の写真右)。何をしているのだろうか。
ここで使われているのは、NECが世界で初めて開発した「物体指紋認証技術(GAZIRU)」だ。部品の表面に自然発生する微細な紋様(物体指紋)から個々の部品を高精度に識別するしくみだ。初めにその紋様をデータベースに登録しておく。すると、それ以降の工程でもう一度その基板の物体指紋を見れば、それが何番の個品であるかわかる。これにより、ロット単位ではなく「個品単位でのトレーサビリティ」が可能になり、品質管理を強化することができる。
基板はコンベアにのって物体指紋認証を行い、管理IDを確認。その後もコンベアにのって搬送される。途中、ロボットがトレイの上に基板をのせる。トレイと一体となった基板はさらにコンベアにのって組立工程へと送られる。
組立工程は人の作業となる。トレイの上にのった基板のRFIDが読み取られ、これから何の作業が必要かシステムが認識し、人に作業指示を行う。この際、作業指示はプロジェクションマッピングにより手元に映し出されるため、担当者は迷うことなく作業が可能。また、指示は次の技術によって音声によっても出される。
それは、NEC独自の技術である耐騒音性音声認識エンジン「VoiceDo」だ。騒音の激しい工場内でも、ヒトとシステム(デジタル空間)の間で音声によるコミュニケーションを可能にする。作業者が発する「OK」などの声がそのまま作業実績として登録される。ハンズフリーで作業実績を残せるため、いちいち手を止める必要がなく、作業がスムースになる。NECはモデルラインにこのしくみを適用し、作業時間を20%削減した。
また、作業の開始時にはNECの顔認証技術「NeoFace」が使われている。まず、社員証に貼付されたQRコードを読み込ませる。次に、タブレットに搭載されたカメラで個人の「顔」を認識する。この際、各社員の「顔」のデータベースがあるわけではなく、社員証のQRコードに登録された顔の特徴データと照合する。QRコードに登録された社員の情報を読み込み、今から行う作業がその人に任せられる作業なのかをシステムが判断し、認証する。
ここでさらに、NECは「感情分析ソリューション」を提案する。作業者にウェアラブルデバイス(TDK製)をつけ、心拍変動データから感情分析を行うしくみである。心電データから「眠い/眠くない」と「快/不快」かがわかる。さらにその2軸で、作業者の感情を「興奮・喜び」「穏やか・リラックス」「憂鬱・疲労」「ストレス・イライラ」の4象限に分け、作業者がどんな感情なのか特定。そのデータから作業者に安全、安心を促すとともに、感情から作業の「やりにくさ」などもわかるため、生産性改善に活かせる。
これまで紹介してきたように、人が行う作業工程には多くの技術が使われている。なぜここまで万全にする必要があるだろうか? 実はここでも「マスカスタマイゼーション」が想定されている。関氏は次のように述べる。
「つくる製品の種類が次から次へと変われば、人のミスが多くなる可能性があります。また、ロボットの活用が進むことによっても、人が作業を行う頻度が減り、久しぶりの作業が多くなるためにミスが増える可能性があります」(関氏)。
そのため、あらかじめ「絶対にミスをしないしくみ」を用意していくことが必要なのだ。
組立が終わると、最後は完成品の「外観検査」だ。NECのディープラーニング技術「RAPID機械学習」を用い、撮影した完成品の画像から「正常」か「不良」を判定する。カメラはキヤノン製だ。このしくみを導入した他社工場では、外観検査にかかる工数、人件費を60%削減したという。
実機を見て議論すれば、「現場」と「情シス」も課題を共有できる
以上が、今回体験した生産ラインの一連の流れだ。また、この生産ラインには各所にセンサー(温度・振動など)が仕掛けられており、そのデータは三菱電機製のPLCを経て、NEC製のサーバに送られる。そこで、データをリアルタイムに加工・集約するのはエッジクロスコンソーシアムが提供するソフトウェア「Edgecross」だ。ここで、整えられたデータはさらに上位のプラットフォーム「NEC Industrial IoT Platform」に送られる。
「NEC Industrial IoT Platform」に集まってきたデータは、さらに各業種や用途に合わせてテンプレートが用意されている分析プラットフォーム「NEC Advanced Analytics Platform」によって、分析や予知保全などさまざま活用が可能だ。データの分析について、北野氏は次のように説明する。
「データの分析と言っても、人が見ればすぐにわかる場合もあれば、AIを使った方が早い場合もあります。たとえば、ある時間の出来高が悪い場合、その時間の不良率が悪くければ、不良品がたくさん出たから出来高が悪いのだとわかります。さらにその時間帯の稼働状況まで深堀して、もしチョコ停が多いのであれば、原因は機械の不調にあるとわかります。これは人が時系列データを見ればわかることです」(北野氏)
しかし一方で、AIを使った方が早く原因を特定できる事象もあるという。そこで、北野氏が有用性を実感しているのがNECの「Analytics AI」という機能だ。プラットフォームに集まってきたさまざまなデータから、ルールとパターンを自動で見つけだし、予測するという。需要予測や品質分析、故障要因分析などに活用される。
たとえば、品質分析の場合。今回のデモでは、ロボットがトレイの上に基板をのせた。その際に、置く位置がわずかにずれる場合がある。その「位置ずれ」の幅が大きいと不良品になってしまう。なぜずれてしまったのか、その原因は人間にはなかなかわからない。そこで北野氏は、「Analytics AI」を使って分析を行った。
北野氏自身は、基板を切断する加工工程に原因があると考えていた。しかしAIが出してきた答えは、ロボットアームに原因があるというものだった。実際に調べてみると、ロボットが作業を繰り返しているうちに、基板を置く位置がずれることがわかった。
「最初は意外でしたが、よく調べていくとAIが正しいことがわかりました。AIも完璧ではありませんが、技術屋が思っているところ以外から気づきを与えてくれます。人だけで原因を調べようとすると時間がかかりますが、ある程度AIが選択肢を用意してくれれば、効率的な分析が可能になります」(北野氏)
最後に、「PLM-SCM-MES/IoT連携」について紹介する。NECが構築したこのしくみでは、設計(PLM)とサプライチェーン(SCM)、製造(MES)の各システムとヒトやモノ、設備のデータが集約されたIoTプラットフォームが連携している。PLMシステムには、日本の製造業900社以上が利用するNECの「Obbligato III」が使われている。
設計部門が新製品の設計を行う場合。まず、PLMでつくった設計データをもとに、BOP(部品毎の工程計画)とBOM(部品表)を導き出す。そのBOP/BOMにもとづき、生産技術部門がライン設計を行い、デジタル空間でシミュレーションを行う。そこで確定したBOP/BOMをMES(製造実行システム)につなげてフィジカルの生産ラインを動かす。またこの際、SCMと連携し、「需要予測を行った結果、この製品を10万個生産する必要がある」といったことがわかる。それに対し、「一部の部品は3Dプリンタで製造すべきだ」といった最適な生産フローが見えてくる。
同ラインで製造品目を急遽変更する場合は、PLMのデータにもとづいてBOP/BOMを変更。ラインの組み換えは人が手動で行うが、その指示内容は自動で変更される。マスカスタマイゼーションに対応したものづくりのしくみが構築されている。
6月のオープン以降、既に「NEC DX Factory」を体験した企業の感想について、北野氏は次のように述べる。
「現場の担当者と情報システムの担当者が一緒にこられることが多いですが、情報システムの方は、デモを体験することで現場が何に価値を置いているかがわかり、課題感を共有しやすいとおっしゃいます。また、経営層の方もいらっしゃいますが、実機を見ると話がはずみ、意見が出やすいと好評価をいただいています」(北野氏)
また、関氏はNECの取り組みについて次のように語る。
「私たちはこの共創スペースにきてもらうだけではなく、お客様(パートナー)のところにも伺います。もし、サプライチェーン全体の最適化がお客様の目的であれば、北野のような「匠」が現地の工場だけでなく、仕入れ先にも出向きます。そうした現場に密着した共創の取り組みがNECの価値だと考えています」(関氏)