栃木県小山市にメーカー横断でのロボット展示が行われているショールーム「スマラボ」はある。
このショールームは、IoTデバイスなどとも組み合わさっていて、スマートファクトリーを「今つくるとこうなる」ということがわかる展示スペースとなっている。来訪する企業担当者はこれを見て、自社の工場をどうするのか、という議論を始めるのだという。
前編では、「ファクトリービルダー」の役割を具体的にお話しいただいた。後編では、工場設備を刷新するという、多額の投資の前にシミュレーションができるということで、シミュレーションの実態について、スマラボを運営するFAプロダクツ代表取締役会長の天野眞也 氏と、高見守 氏にお話を伺ってきた。
工場をシミュレーションするケーススタディ
小泉: 具体的に工場をシミュレーションする場合のケーススタディを教えてください。
天野: 例えば、搬送用ロボットが1台だけ稼働している金属加工工程に、ロボットを一台増設することで、省人化と生産能力増強を図るケースがあるとします。増設したロボットは従来人手で行っていた加工機への投入と取り出しを担うイメージです。
以前はこの様に設備やロボットを追加する際に、空きスペースを確認するため「工場の寸法を測る」だけでも大変でした。しかし、現在では3Dスキャナーで実際の寸法が簡単に読み取れるようになったので、レーザースキャンで現場をスキャンしておけば、現場の状態がわかります。
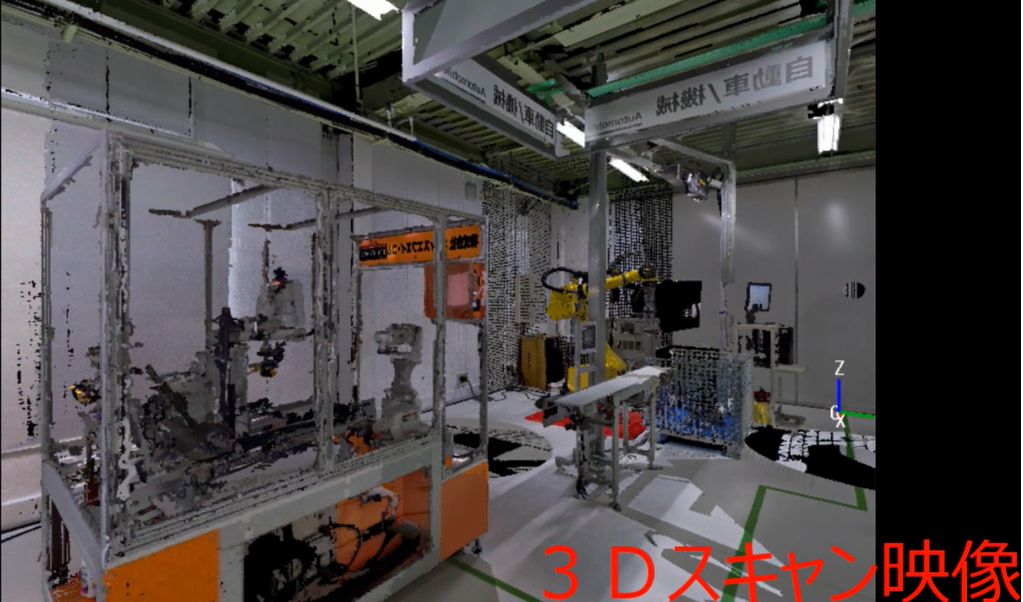
装置の能力増強は、プラントシミレーションによる成立性検証と、3Dスキャナーで取り込んだデータを用いて、プロセスシミュレーションによる干渉チェック、動作チェックを並行して行います。つまり、「その設備の能力が適切かどうか」「限られたスペースに、ロボット一台と加工機が入るかどうか」というのを両方見るわけです。
稼働状態のシミュレーションもPC上で行います。さらに進んだケースだと、前後工程含め、全ての装置能力を増強し終わった状態を再現します。
こうやって、工場の「デジタルツイン」を実現します。
右:デジタルで作られた工場
お客様にはこの能力増強が終わった姿をデジタルでお見せして、ソフトウェアまで含めてこう動きます、と提示します。ここで了承を頂ければお客様との齟齬はありません。入れてみたけどやっぱり違った、ということがなくなります。
しかし現実問題は、自動化機器を入れるための投資が難しい中小企業様が多いのが現状です。
ですから、工場の効率化だけを提案してほしいという場合は、全て人手で行うような作業改善をご提案することもあります。例えば「工程の位置を変える」とか、「人が歩き回っているなら最短の徒歩ルートを提案する」というようなことです。
その中で、今後人材が減少していくと予測される箇所など、自動化を入れた方がいいだろう、というところは別途提案していく形を取っています。
小泉: 具体的なイメージをシミュレーターでもってもらって、その上で実現可能な線について、コスト面を考慮して現実的に提案していくのですね。
天野: お客様は、新しい機械を導入するのを悩むものです。そこで、具体的に価格がいくらで、セットだとこうなります、ということをイメージしてもらうためにスマラボを作りました。
特に新規ラインは、納品されるまでお客様も何が納品されるか分からない状態です。私たちはお客様の期待値に対して対価を頂き、こういったラインを作る、とご提案するのですが、お客様は見るまで本当の全体像は分かりません。そういったところを、もっとお客様にイメージしてもらいたいと思っています。
そのメインになるのが南相馬で実現しようとしているスマラボをもっと発展させた形のショールームで、加工工場、組立工場、そしてグローバル人材の教育もしていくという施設です。弊社の緊密なパートナーである「オフィス エフエイ・コム」と、私が代表を務める「ロボコム」の合弁会社「ロボコム・アンド・エフエイコム」の南相馬工場として今年の夏に着工して、来年秋ごろ竣工予定です。
小泉: ライン設計をするときにそれぞれのシュミレーションソフトの操作が簡単ではないとおっしゃっていましたが、そこが差別化余地になるということですしょうか。
天野: おそらく他の会社は、こういったライン構築の事業に参入をすること自体難しいと考えています。なぜなら、日本の製造業というのは誤解を恐れずにいうと基本的には下請け構造にあるからです。
自動車を例にすると、最上位には完成車メーカーがあり、その傘下に「部品下請け」があります。
一方、私たちは「技術下請け」で、言われた技術はなんでも納める便利屋的な存在です。
部品下請けは、基本的には親会社に「言われた仕様」で「言われた通り」に作るので、親会社に対して提案することはありません。それは「技術下請け」も同様です。
なぜなら、言われた通りにやらないで、うまくいかなかったらこちらの責任になってしまうからです。
実際、当社では、社内で1年、2年構想したが、いい案が出ず、最後の最後に「プロに頼もう」、というお客様に多く来て頂いております。
また、自動化設備を全く入れたことがないお客様ですと、全てをおまかせ頂ける事もあります。
次ページは、「ラインシミュレーションで活躍するソフトウェア」
ラインシミュレーションで活躍するソフトウェア
ラインシュミレーションで活躍するソフト上は、上図のようなものがある。ここで、それぞれがどういう役割を果たすのか見ていく。
プロジェクト管理
プロジェクト管理ソフトウェアは、今後弊社でも注力していこうとしている分野です。例えば100人社員がいたとしても、配線作業に関してある難易度の仕事ができる人間は限られてきます。能力によって対応期間も変わってきます。そういった現場でのプロジェクト管理です。
例えば何かの資材が納品されないだけでも、納期はズレが生じてしまったりする。ですから、こういったアクティブなプロジェクト管理を回しておかないと、納期は遅れる一方です。
ある企業では、月の生産能力をフル稼働させれば2億円の売り上げになるほどのサイズだとすると、年間24億円の売り上げになるほど作れるはずです。しかし、実際作っているのは11億円だったりします。暇そうにしているのかというとそういうことではなく、今月来月の受注残を足した、余剰生産能力がわからず、営業がいくら受注できるのかを知るすべがないのです。
その結果、かなり余裕を持って受注をしまうことになる。その結果、製品は単純計算して倍の値段で売っている状況になるのです。
そこで、このプロジェクト管理システムを導入すれば、もっと先の予定も組めるし、途中で何かが入れ替わっても、組み替えをしながら製造できるのです。
小泉: 作るものがある程度分かっているのに、どのタイミングでどう段取り変えするか、ここでこの生産機械がいるという話がギリギリになって始まり、段取り良く進んでないという現実もあるのですね。
工程設計
天野:工程設計においては、AGVで搬送するのか、一貫ラインで組むのか、ということをまず決めます。そして、ラインに何の加工機、製造機をどこに置くのかということを決めます。
設備設計
設備システムは、CADシステムで装置の設計のことです。
ロボットシュミレーター
ロボットが動いた時、ぶつかるか、ぶつからないかを、シュミレーションするものです。
生産シュミレーション
通称プラントシュミレーションとも言っていて、各装置や人のパラメーターを細かく入れて、アルゴリズムで計算させることで、生産性を見ることができます。
パラメーターが細かく入れば入るほどほど、実ラインとの齟齬が減っていきます。
しかし限界があり、例えば、ある産業機械の停止時間が10%となっていたとします。これは、一時間に6分間止まったのか、10時間かけて間隔をあけて複数回1、2分止まったのかによって状況は全く異なります。この装置が20台、30台並んでくると、現実は動いたり止まったりしているので、そこに本当はIoTで状況を細かくとることで、その答えとなります。
これまでは、人が日報をつけていた結果をエクセルなどで集計して、この機械は9割でこの機械は8割動いている、といったことを入れていきます。そうすると実際にはラインとのズレが出てきます。
そこで、ずれた数値は直接センサーから取得するデータを入れて、シミュレーションにフィードバックしてあげるとほぼズレがなくなります。
ですから、本当は「IoTありき」ではなく、本当はずれているところにIoTで取得したデータを入れてあげるのが1番だと考えています。
八子: 本来設計された生産能力に対して、ずれがあるところを重点的に状況把握するためにIoTを使うということですね。
天野: はい。それがまさにこのソフトウェアです。例えば、設備2がボトルネックになっていることがわかったとします。
次ページは、「シミュレーションを行うことで、設備増強が不要となるケーススタディ」
シミュレーションを行うことで、設備増強が不要となるケーススタディ
通常、設備2がボトルネックで、待ち時間が多いから設備2を能力増強しましょうとなるのですが、これは、乱暴なやり方です。一方でこの情報だけ見ると設備2の能力増強をしましょうと言えば納得してしまいます。
しかし実は設備2を増強しなくても、この後ろのラインがストップしている時間が問題なので、中間在庫を増やしてあげれば、生産能力だけはあげることができます。
加工時間、故障率、一時間当たりの生産数などわかっている数字があればあるほど、ここには細かく数字を入れていけます。コンベアのバッファー能力なども入れて10時間動かすと、これで実際に571個しか作れないことが分かります。こんな簡単なラインでも人間では計算できません。
例えば一旦10個にしてみます。そうすると639個作れるので、中間在庫を増やすだけだと、設備2をフル稼働させている状態でのラインの最大生産量です。
逆に639個よりも作りたいという目標を課せられたら設備2をいじるしかなくなります。
最大値がこれで分かりましたが、本当に知りたいのは630個ぴったり作れ、かつ中間の在庫が最小なものです。そこで最小計算をする際、GAというアルゴリズムで計算し、最適な値を計算しています。
小泉: こんな計算ができるなら、投資対効果も最大化できやすそうですね。
右:IoTNEWS 八子知礼
天野: ところが、実際の工場の場合、設備1課、2課、3課、4課、5課と異なる課がそれぞれでラインを管理しています。自分がもし製造3課の課長で、故障が起きる機械を使っているとします。そうすると、当然故障率を改善することに予算つけることになりますよね。
しかし、先ほどのシミュレーションでも見た通り、実際この工場は、機械をいくら良くしても、スループットは変わりません。こういった問題を切り分けず、ロボット化したい、自動化したいという工場が大半です。
先ほど自動化はなくてもいいというお話しをしましたが、このシミュレーションは、人の作業でも可能です。人が全部作っていたとしても、先ほどのパラメーターは人の能力で入れていけばいいだけです。作業者のレベルも全部細かく設定ができるので、例えば設備2のところで人がこれをやっていれば、人の投入量を最小にして、ということも出せます。
この、ラインシュミレーターというソフトウェアは、数社から出ています。しかし買おうと思うと一千万円以上します。
各都道府県の県庁さんから講演依頼が来ると、私は必ずこれを見せて、「県で取り組まれた方が良い」と話します。そうすれば県内の生産が一目で分かるからです。
そして実際に産業機械をIoTでつなぐと、リアルタイムに県の生産量が把握できます。そうすると海外など外側からの受託をする際にも役立ちます。
一足飛びに下請けの中小企業の会社が、全く違う業態に転身するのは不可能だと思っています。ですから県が補助し、自分たちで生産ラインを決めれば、どこがボトルネックかすぐに把握でき、能力増強したらどうなるかもすぐに分かります。
八子: これはあくまでも製造業中心の話ですが、製造工程に似たような構造であれば応用できますか。例えば農作物など、大量にものが流れてくるもの、多品種少量が流れていくようなものであれば対応は可能でしょうか。
天野: はい、可能です。元々は銀行の待ち列を解消するために作ったアルゴリズムでした。ですからどういった現場にも対応できると考えています。
小泉: 本日は、ありがとうございました。