儲かる工場には、原価に着目した収益管理も必要
小泉: 今後御社としての展望を教えてください。
佐野: 在庫という観点で言うと、ある電機メーカーさんにこのソリューションを紹介したら、「まさにこれだ」と言っていただきました。特に組み立て製造業様にフィットすると感じています。
「全く同じ課題です」と言われることが多くなってきているので、横への広がりという展開ができると思います。
また、冒頭でもお話ししましたが、弊社としては在庫に特化していくというよりは、収益性向上が最終目的です。
その1つの手段が在庫管理なのですが、もう1つのテーマが製造原価です。変動費と固定費で分けてというアプローチです。
在庫管理ソリューションを提案しても、全く響かないお客様もいます。たとえば受注生産方式ですと、基本的には事前に在庫を確保しません。
一方、受注生産方式の企業では、案件ごとの収益が分析できていないケースがよく見られます。
そこで、標準原価と実際の原価の差異を受注案件ごとに可視化し、最後になってから赤字だった、ということを防ぐためのアプローチでご提案をしています。実はこのような案件が在庫の案件より増えています。
原価は特に変動費に着目した収益管理で、在庫適正化に続く第二のソリューションです。
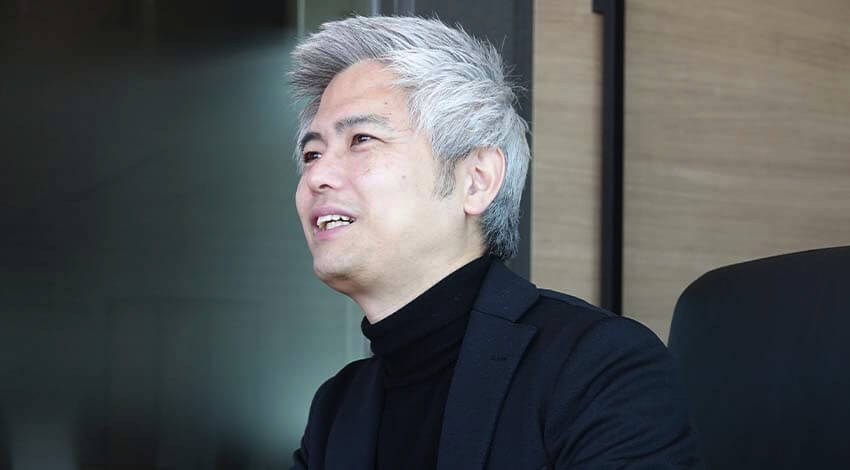
小泉: 具体的にはどのような内容なのでしょうか。
佐野: このソリューションでも、まずは受注のデータ、明細といった生データをいただきました。
そこで明細を見てみると、受注品目ごとの販売金額と、製造原価予算がたてられています。原価の中には固定費と変動費があり、変動費の中の材料費がいくらで、外注費がいくらくらいかという予算がたてられています。
一方でその受注した品目、例えば機械製品などは、製造には一定のリードタイムがかかりますので、材料や作業費が日々投入されることになります。
そこで初めて、実際の原価がその時点でわかります。ですから、もともと目標に立てていた原価と実際の原価で差異が出てくるわけです。
はじめに目標をある程度立て、そこに対してどう進捗しているかということを見ていき、今後使う予定の部品の費用なども計算していくと、納入のタイミングで、目標設定額を超えるかどうかというタイミングはどこかで見えてきます。
そこである一定の額を超えた時にアラートを上げるというものです。
このソリューションのポイントは、予算超過が見込まれる案件を予算内に収める為のものではありません。作りかけている製品の材料や労務費をを減らすわけにもいきませんので。
ただし、次の類似した案件に活かすことはできます。受注生産といっても繰返し受注生産形態や、類似した製品の場合、使用される部品や材料の、標準原価の見直しを行い、見積もりを精緻化していくことができます。
このソリューションも、紹介させていただくと全く同じ課題感を持っていたというお客様がいて、ニーズがあることを感じています。
今後のDXに向けて
小泉: 今まではSAPのデータは現場で持っている様々なデータとつなげるのが難しいというところで止まっていたと思います。
しかしここにきてIoTが盛んになったことで、製造業の現場の方たちもデジタル化を行い「つなぐこと」でのメリットを理解して、導入してもいいというマインドになってきているという意味ではやりどきなのかもしれませんね。
佐野: 以前はIT側とFA側が断絶されているケースが多かったですね。
小泉: そうですね。FAをわかっていながらIT技術がある人材というのは希少だと思います。だからこそ御社のような会社がIT系のシステムとOT系のシステムの間を取り持つことで、DXがより現実味を帯びてくると感じます。
佐野: 数年前まではデータを集めるという領域でしたが、いよいよデータを活用する時代に突入してきたなと感じます。
小泉: 今回の在庫管理システムでも集めたデータではなく、前からあったデータをうまく活用しているということで、まだまだできることの余地があると感じます。
原価の状況がきちんと見えて、見積もりの精度を上げ、さらに本来持たなくていい在庫も減縮されてくれば、BSもPLも改善されますので経営にかなりのインパクトがありますね。
今後も進捗があれば是非お話を伺いたいです。
本日はありがとうございました。
無料メルマガ会員に登録しませんか?
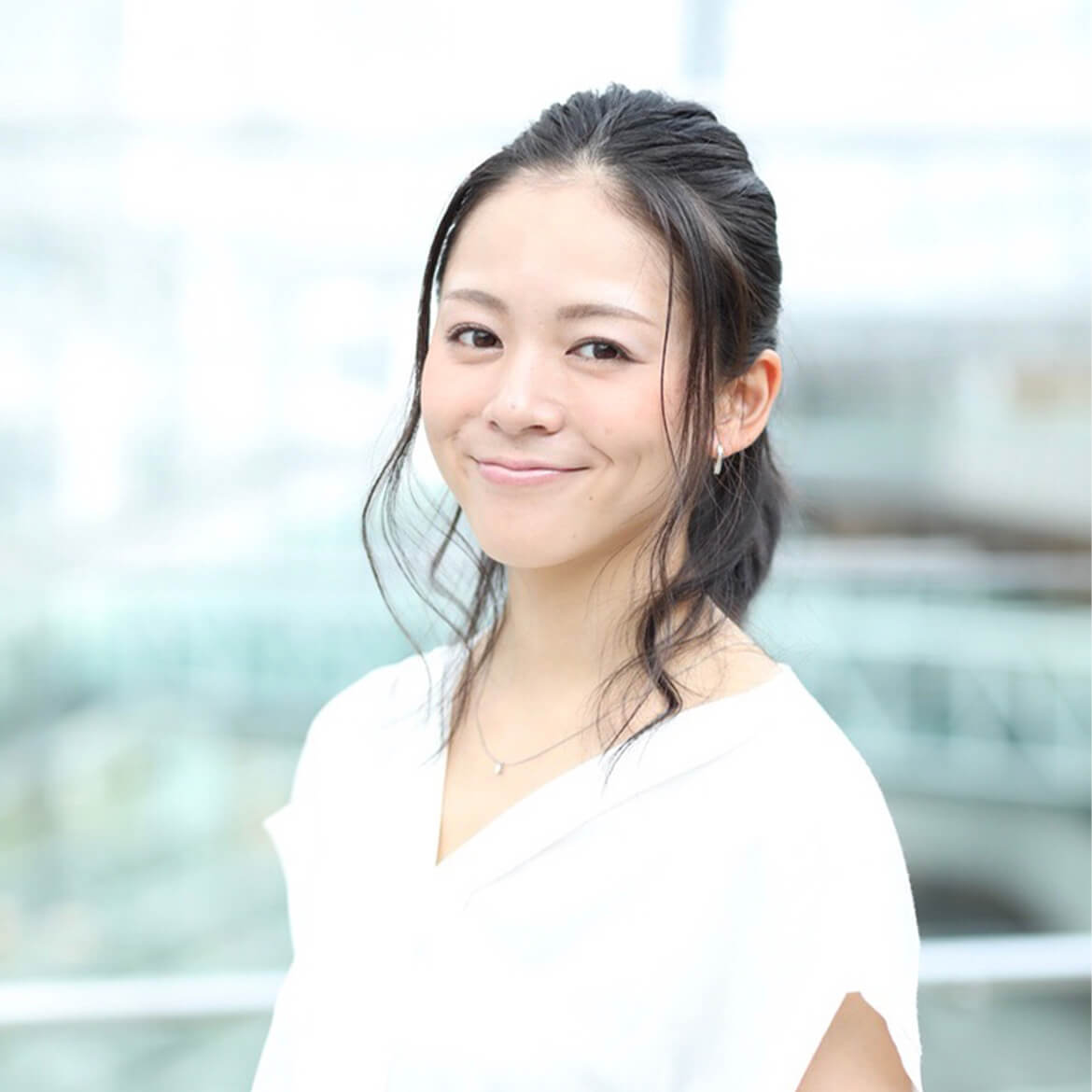
現在、デジタルをビジネスに取り込むことで生まれる価値について研究中。IoTに関する様々な情報を取材し、皆様にお届けいたします。