11月1日〜11月6日の間に開催されていた、JIMTOF2018。
日本の製造業の底力を見せるとも言える、産業機械メーカーの競演が行われたが、その会場となったビッグサイトは、全館を使っているにも関わらず来場者でいっぱいだった。
そんな製造業の中でも、製造機械を展示している展示会なのだが、もっとも興味深かったのは、70社にも及ぶ展示されている産業機械をつないでいたことだ。
しかも、情報を吸い上げるプラットフォームは、ファナックのField Systemをはじめとして、DMG森精機のADAMOS、Edgecross、など様々なプラットフォームに接続した上で相互接続も実現できるという展示が行われていた。
トップダウンアプローチのドイツ、インダストリー4.0における取り組みとは逆に、ボトムアップ型となる日本の製造業でのIoTへの取り組みだが、今時点で一定の成果が確認されたといってもよいだろう。
では、全部の生産機械をつないで、状態を可視化した後に待っているコトとはなんなのだろうか?
ドイツ、インダストリー4.0について、語られる場面でよく登場するのが、e.GOという企業だが、この企業はEV(電気自動車)を作っている企業だ。
この企業では、設計と開発のフェーズに着目をして効率化を図っているのだ。
ものづくりにおいて一般的には、設計、開発、製造というプロセスを踏むことになるが、日本の企業が製造のプロセスに注目しているのに対して、前行程に注目していることとなる。
ドイツにおいては、ボッシュのような企業があるので、EVくらい作るノウハウはあるということなのだが、3DCADで製作した設計図面に対して物理的なテストをバーチャル場でシミュレーションして、その結果を設計図面にフィードバックして行くというやり方をとっているところが興味深いのだ。
通常、設計した図面は、開発チームに持ち込まれ、モックアップを作って課題を設計チームにフィードバックされる。さらに設計チームがブラッシュアップしたものを開発チームは作って見るわけだが、こうやってなんども往復していると当然オーバーヘッドが大きくなる。
しかし、昨今のコンピューターパワーであれば、自然現象や物理現象などのテストはバーチャル場で概ね終わって、開発の過程では、実際にモノにふれて確認する、という工程へと変化するのだ。
そうやってデジタル上で完成度を高められた製品を、実際の製造の現場に落とし込む際も、実際の工場をバーチャル場でシミュレートできる環境を持っていれば、どこで問題が発生しそうか、時間がかかりそうか、といったことも緻密に計算することができる。
こうやって、生産の現場もトップダウンで最適化した上で生産にかかることで、マスカスタマイゼーションにも対応していくという考えなのだ。
さて、冒頭の話に戻って、日本の生産現場についてだが、多くは既設の設備の状態監視を行っているということになる。
「その先は?」という問いがよくあるのだが、現場の可視化ができたら、生産拠点間の比較などまだまだやることは山積みだ。
しかし、e.GOのような企業が製造の主役となってきた場合、生産の現場ばかりを改善しつづけてきた企業は困らないのだろうか。
設計図面ありきで合理的な生産ラインを構築するようなことが当たり前になったら、現在の生産ノウハウに関して、大きな見直しが必要となる日が来る可能性が高い。
足元を見ることはとても大切で、生産性の改善は目の前の課題であることは明確だが、そもそも生産を依頼するメーカーがやり方を変えてきたら、どう対応するのか、ということについても、考えておくことが重要になる。
無料メルマガ会員に登録しませんか?
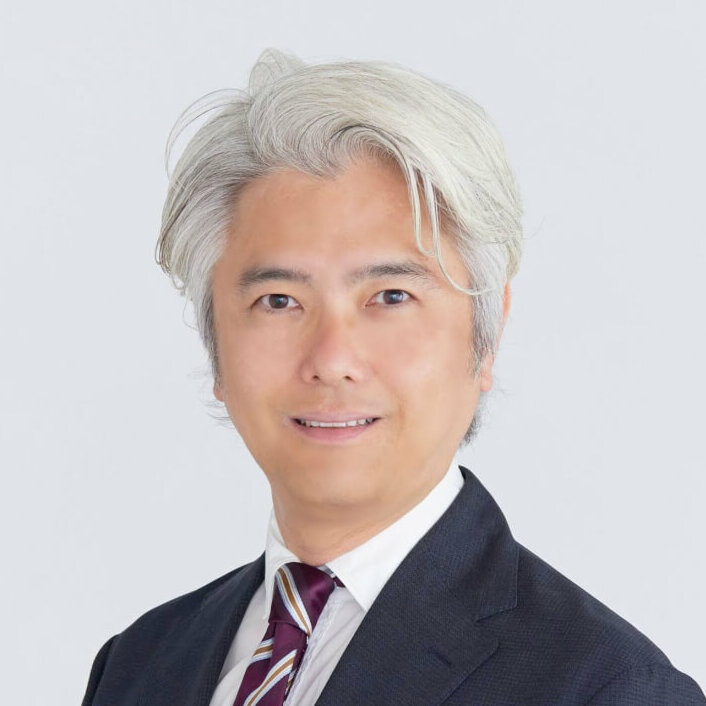
IoTNEWS代表
1973年生まれ。株式会社アールジーン代表取締役。
フジテレビ Live News α コメンテーター。J-WAVE TOKYO MORNING RADIO 記事解説。など。
大阪大学でニューロコンピューティングを学び、アクセンチュアなどのグローバルコンサルティングファームより現職。
著書に、「2時間でわかる図解IoTビジネス入門(あさ出版)」「顧客ともっとつながる(日経BP)」、YouTubeチャンネルに「小泉耕二の未来大学」がある。