VOLVOの例に見る、デジタル・スレッドの例
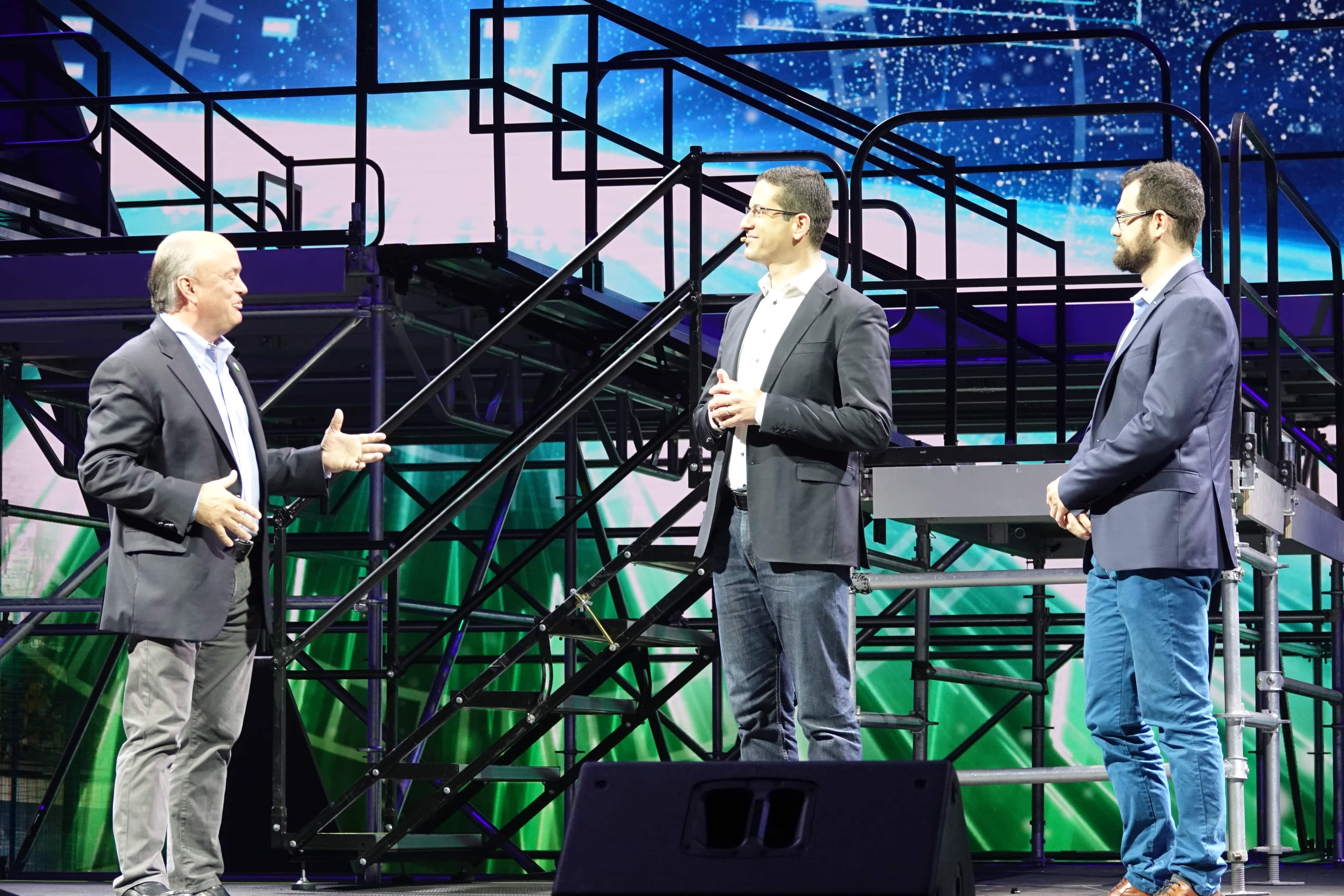
例えば、VOLVOの例では、「乗用車の部品が6,000個ほどであるのに対して、トラックは20,000個ある」「さらに、トラックではカスタマイズがとても多い」ということだ。
製造のフェーズやサポートのフェーズにおいて、設計データに基づく部品管理が行われた状態で、1台のトラックに必要なカスタマイズを加えることができれば、作業手順上次にどの部品をどう作業して良いかが明確になるため、作業上のミスも低減するし、ARで情報を補完することで、作業品質も向上する。
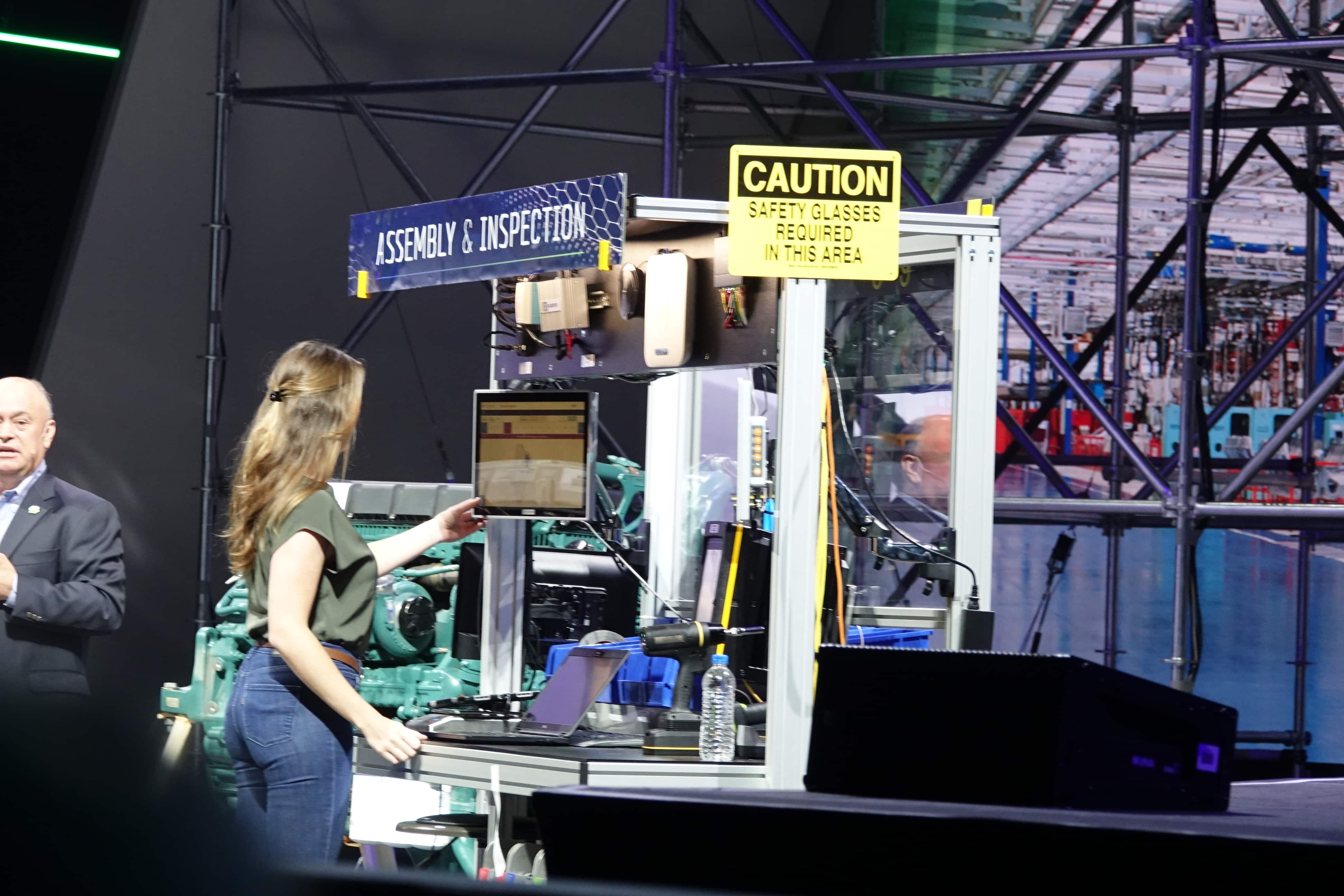
実際に作業をする際には、PTCではARのツールとして「Vuforia」と呼ばれるソフトウエアを提供している。CADで作成された設計データを保持しておくことで、ARを実現するためのデジタル部品として再利用するのだ。
その結果、現実世界のエンジンと、CADで作られたエンジン部品のデータをARで重ね合わせることができる。
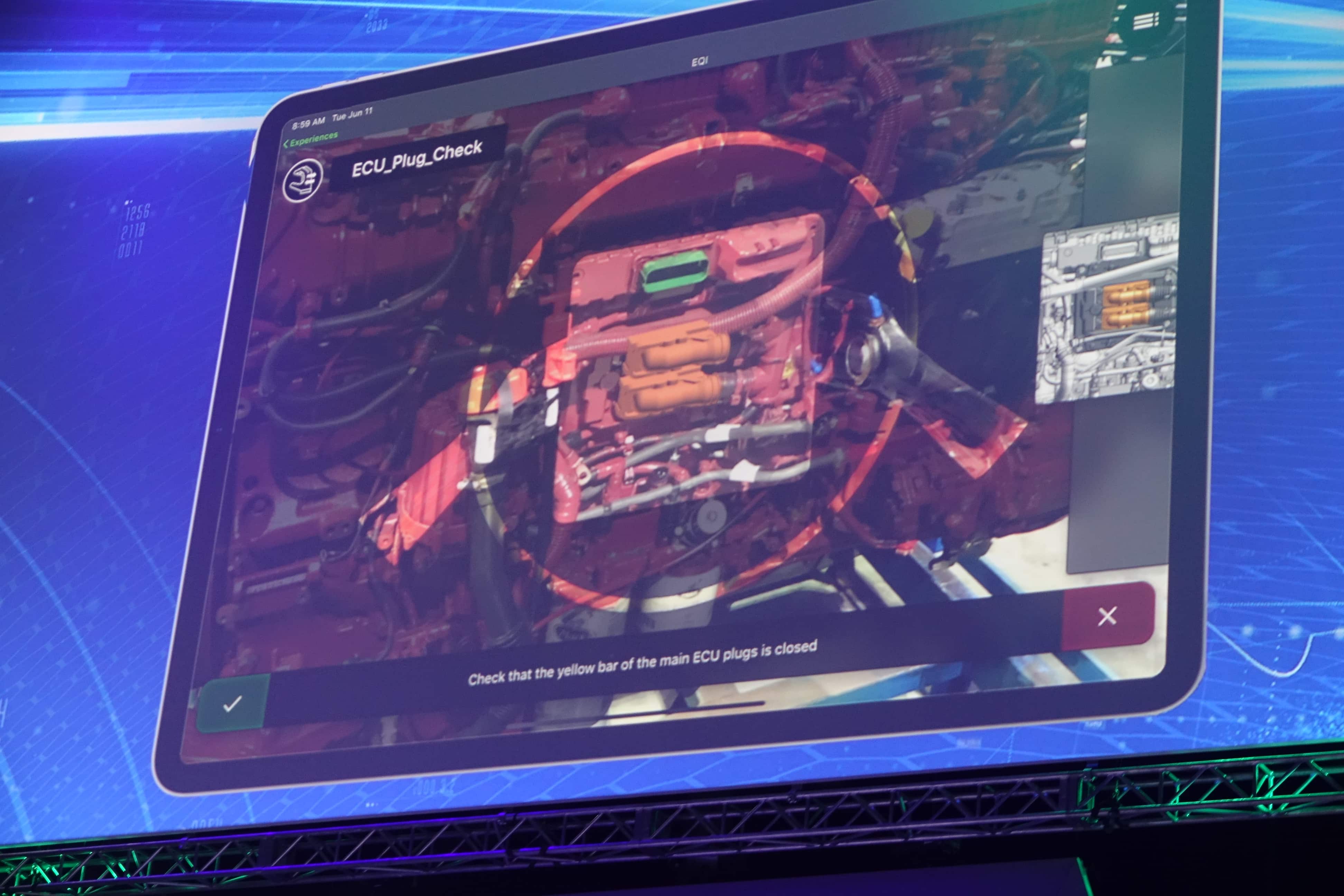
そして、現実世界のエンジンが吐き出すデータをIoTで吸い上げ、ユーザがARを通して見ている仮想空間上に重ね合わせることで、単にリアルとバーチャルを掛け合わせた映像を見るだけでなく、現実世界の物体の状態(温度や振動など、様々な物理情報)を、数値やグラフで可視化することができるのだ。
PTCではこの、現実世界のデータをIoTで吸い上げ、分析などを加える部分をIoTプラットフォーム「ThingWorx」が担当している。
つまり、デジタル・スレッドを実装することで、製造におけるビジネスプロセス全体を最適化し、コスト削減や品質工場も可能となるのだ。
次ページ「設計をデジタルで行いシミュレーションするメリット」
無料メルマガ会員に登録しませんか?
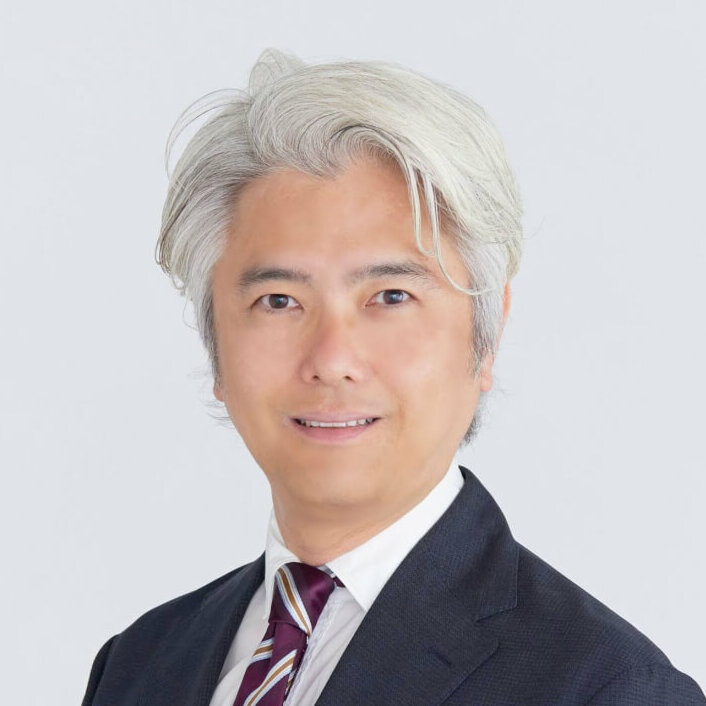
IoTNEWS代表
1973年生まれ。株式会社アールジーン代表取締役。
フジテレビ Live News α コメンテーター。J-WAVE TOKYO MORNING RADIO 記事解説。など。
大阪大学でニューロコンピューティングを学び、アクセンチュアなどのグローバルコンサルティングファームより現職。
著書に、「2時間でわかる図解IoTビジネス入門(あさ出版)」「顧客ともっとつながる(日経BP)」、YouTubeチャンネルに「小泉耕二の未来大学」がある。