デジタルソリューションは、コンピュータ上で物理現象をシミュレートし、不具合の要因分析を行うCAE技術を活用した構造解析や流体解析を主体に、ソフトウェア開発、自動車のモデルベース開発といった数値解析事業を展開している。
そうした中、広島県が提供するAIやIoTを起点とした実証実験フィールド「ひろしまサンドボックス」に応募し、中小製造企業がつながることで企業価値を高める「つながる中小製造業でスマートものづくり」プロジェクトを発足した。
そこで本稿では、ひろしまサンドボックスに応募したきっかけや、「つながる中小製造業でスマートものづくり」プロジェクトの内容、今後の展望などについて、デジタルソリューション株式会社 執行役員 高下和浩氏、ソフトウェア開発部 マネージャー 橋詰公太氏にお話を伺った。(聞き手:IoTNEWS代表 小泉耕二)
同じ志を持ち、プロジェクトを立ち上げる
IoTNEWS 小泉耕二(以下、小泉): もともとひろしまサンドボックスに応募したきっかけは何だったのでしょうか。
デジタルソリューション 高下氏(以下、高下): 弊社はこれまで、解析を中心に事業を展開していましたが、新たにAIやIoTを活用した事業展開を構想していました。
そこで、広島県中小企業診断協会が発足している、ニューロビジネス研究会というニューロビジネスの活用を検討する研究会に参加していました。
その研究会には中小製造業の方々も参加しており、共にAI、IoTの実証実験に実際に取り組んでみようという話になりました。
そこで弊社が代表企業として、「つながる中小製造業でスマートものづくり」というプロジェクトを提案し、中小製造業の方々にはコンソーシアムメンバーとして参画いただき、ひろしまサンドボックスに応募しました。
ひろしまサンドボックスの取り組みが終わった後も、コンソーシアムメンバーの方々と共に改良を続けながら、サービス展開を行っています。
小泉: 応募当時の内容はどういったものだったのでしょうか。
デジタルソリューション 橋詰氏(以下、橋詰): 中小製造業の様々な生産データを収集し、可視化および分析をしていくという内容です。そして、各企業のデータを連携し、企業間を跨いだ効率的な作業計画の立案により、生産工程の最適化をしていく、という構想でした。
その背景には、中小製造企業ではなかなか工場のAIやIoT活用が進んでいないという課題がありました。導入が進まない理由のひとつは、予算や導入メリットが明確でないためです。
そこでなるべく低コストで導入障壁の低いシステムを構築し、それを個々社で導入するのではなく、連携しながら生産効率の向上を図れないか、という構想のもと立ち上がりました。
助け合い、生産現場の価値を高めたいというニーズ
小泉: つながることでの生産性向上は、具体的にどのように実現していこうとしたのでしょうか。
橋詰: 当初は受発注の伝票を共通伝票にするなどの案が出ていましたが、実際にヒアリングしてみると、企業間の物の貸し借りや、繁忙期に空いている工場にヘルプしてもらうといった、生産現場のスケールメリットを出していきたいというニーズがあることがわかりました。
そのためにはまず、各工場の稼働状況を知る必要があります。しかし、多品種少量生産を行っている中小製造企業では、日々の稼働状況が変動的で、稼働率がどの程度か正確に把握できている企業はほとんどありませんでした。
そこで、各企業が自社の稼働状況を把握できるように、稼働率を可視化することができるツールの構築を行いました。
小泉: 具体的にどのようにデータ収集を行っているのでしょうか。
高下: ひろしまサンドボックスのコンソーシアムメンバーは金属加工のメーカーが多く、製造現場には稼働表示灯が付いた工作機械がありました。
そこでまずは、工作機械の稼働表示灯にセンサーをつけて点灯状態を把握することで、機械を改造することなく稼働状況を判断する取り組みを始めました。
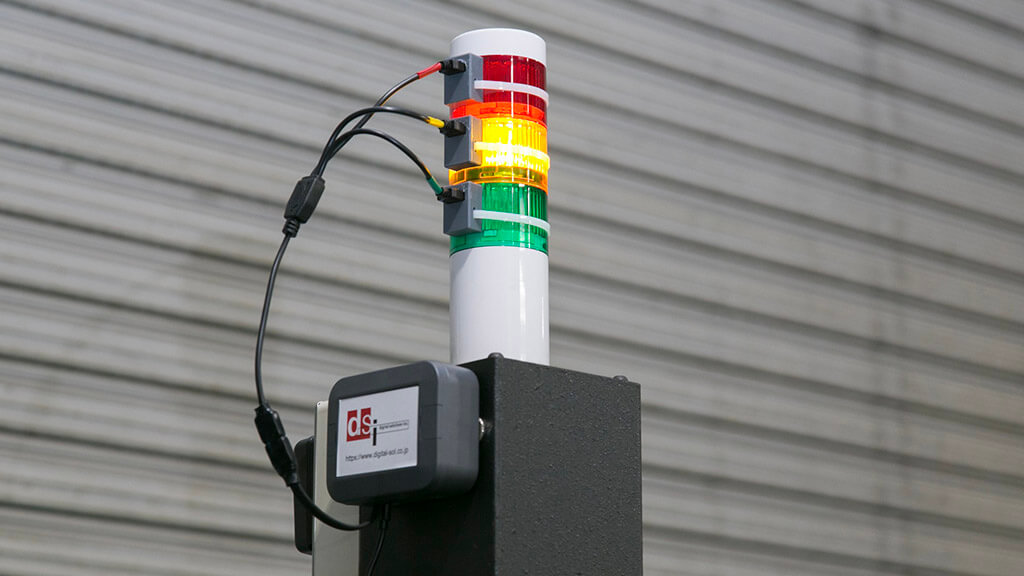
具体的には、なるべく安価で簡単に導入できるようなIoTデバイスの開発を行い、配線やネットワークなどを試行錯誤しながら稼働表示灯への取り付けを行いました。
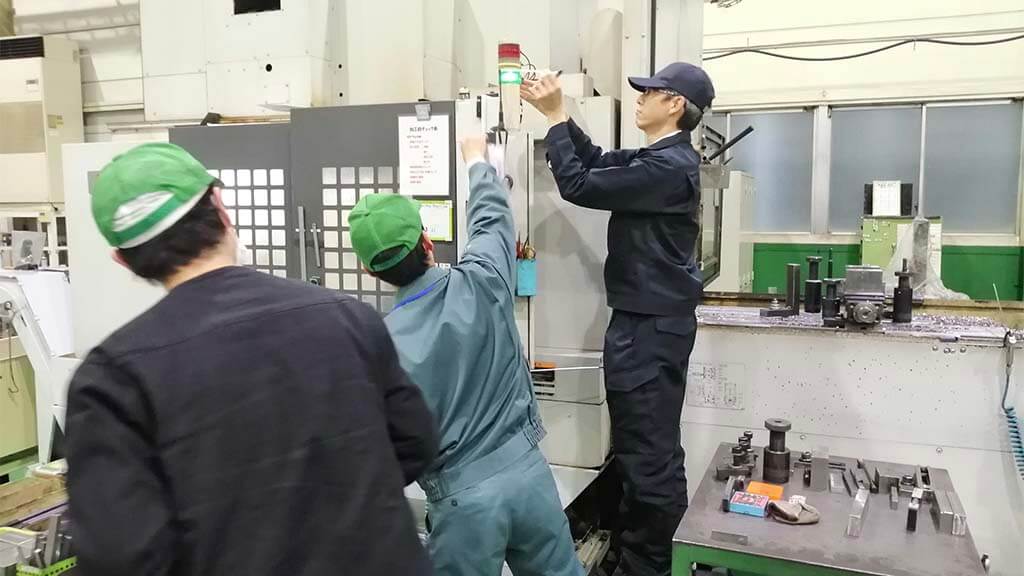
現在では、クラウドにてデータ収集および集計することで、ダッシュボードで情報を確認することができます。
ダッシュボードでは、現時点での機械の稼働状況が分かるガントチャートや、1日の履歴を見ることができます。
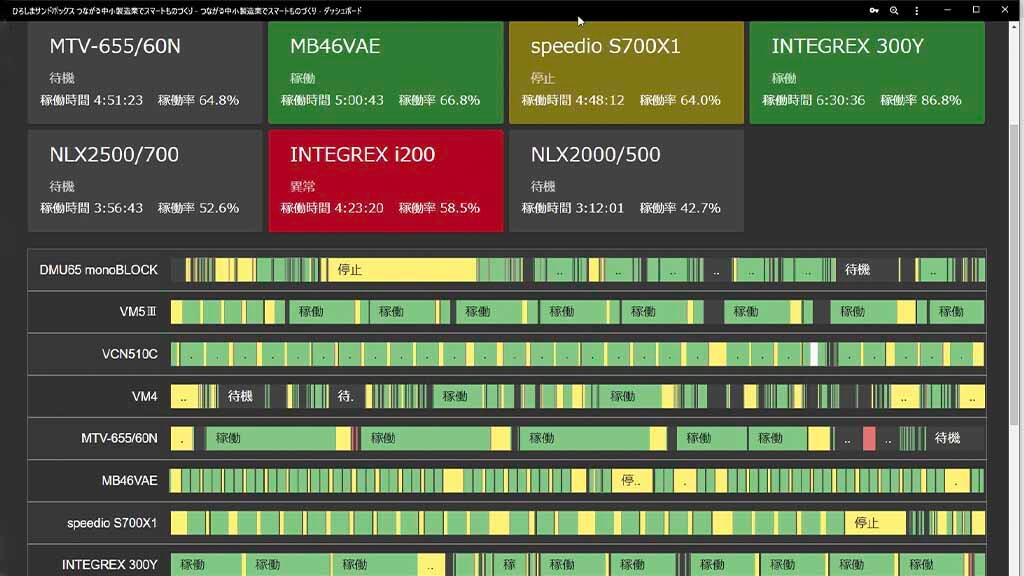
また、過去の履歴データも1日ごとで見ることができます。
さらに、集計の機能があり、例えば1ヶ月の稼働時間の集計や、稼働率の集計といった情報を確認することができます。
このように可視化されることで、これまで感覚的に判断していた稼働状態を、数字で判断できるようになったため、それをもとに次の改善活動を考えることができます。
様々な業界に発展させる構想
小泉: 低コストかつ汎用性の高い形でデータ収集を実現させているのですね。当初は金属加工業での稼働表示灯を活用した可視化ということでしたが、そこから発展した事例はありますか。
橋詰: 現在では、食品加工業の企業にも導入されています。具体的には、商品を流すベルトコンベアに光電センサーを設置し、商品がいくつ通ったかカウントできる仕組みを構築しました。
不良品を振り分ける箇所の手前と後ろの2カ所に光電センサーを設置して個数をチェックすることで、全体に対する不良率を表示できるようにしています。
このように、知りたい情報に合わせてセンサーの種類を変えて構築することで、様々な現場に対応することができると考えています。
小泉: 着々と可視化が行える仕組みを構築されているのですね。当初ひろしまサンドボックスで構想されていた、企業間をつなげることでの価値創造に関して取り組んでいることはありますか。
高下: ひろしまサンドボックスのコンソーシアムメンバーは、現在でも月1回のミーティングを続けています。そこで、集計したデータの活用方法についてなどの情報共有を行っています。
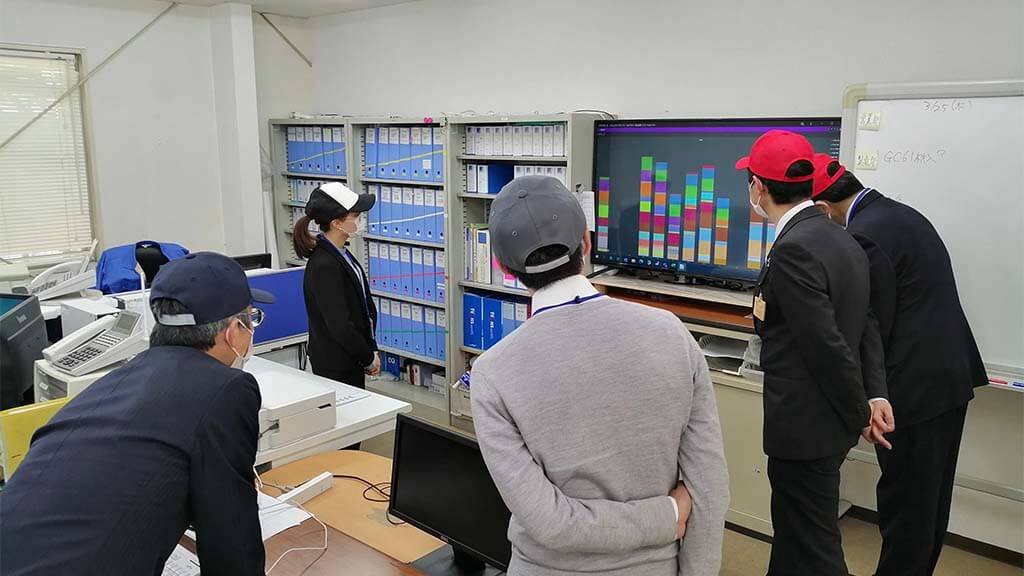
データを元に生産管理や営業の施策を考えるなど、うまく活用されている企業の事例をもとに、他の企業も活用方法を考案しています。
小泉: 情報共有は重要ですね。成功事例の共有も大切ですが、失敗した事例も、今後様々な業界の現場で導入される際に活かすことができそうですね。
現場の理解を得ることがスマート工場への第一歩
小泉: それでは最後に、今後の展開や展望について教えてください。
橋詰: まずは多くの企業に導入してもらうことが大切だと考えています。実際に導入していただき、意見を聞きながら、皆さんの改善活動につながる仕組みに育てていきたいです。
そのためには、経営層だけでなく、現場にもメリットのある仕組みづくりが重要です。
多品種少量の製造現場では、段取り時間などの機械が停止している時間や、停止している理由を把握したいという要望が出ています。こうしたさらに踏み込んだ可視化を実現するためには、工場内の人の動きも把握する必要があります。
そうした際に、稼働率の低い箇所の追求や改善も大切ですが、同時に稼働率の向上や改善といった、「良い結果」にフォーカスをしていくことも、現場の理解を得て、導入を促すポイントだと思います。
そうして利用する企業が増えてくれば、エコシステムが大きくなり、できることもどんどん増えていきます。
目の前の課題をひとつずつクリアしていくことで、当初構想していた「つながる中小製造業でスマートものづくり」が実現されていき、より大きなものとなっていくと考えています。
無料メルマガ会員に登録しませんか?
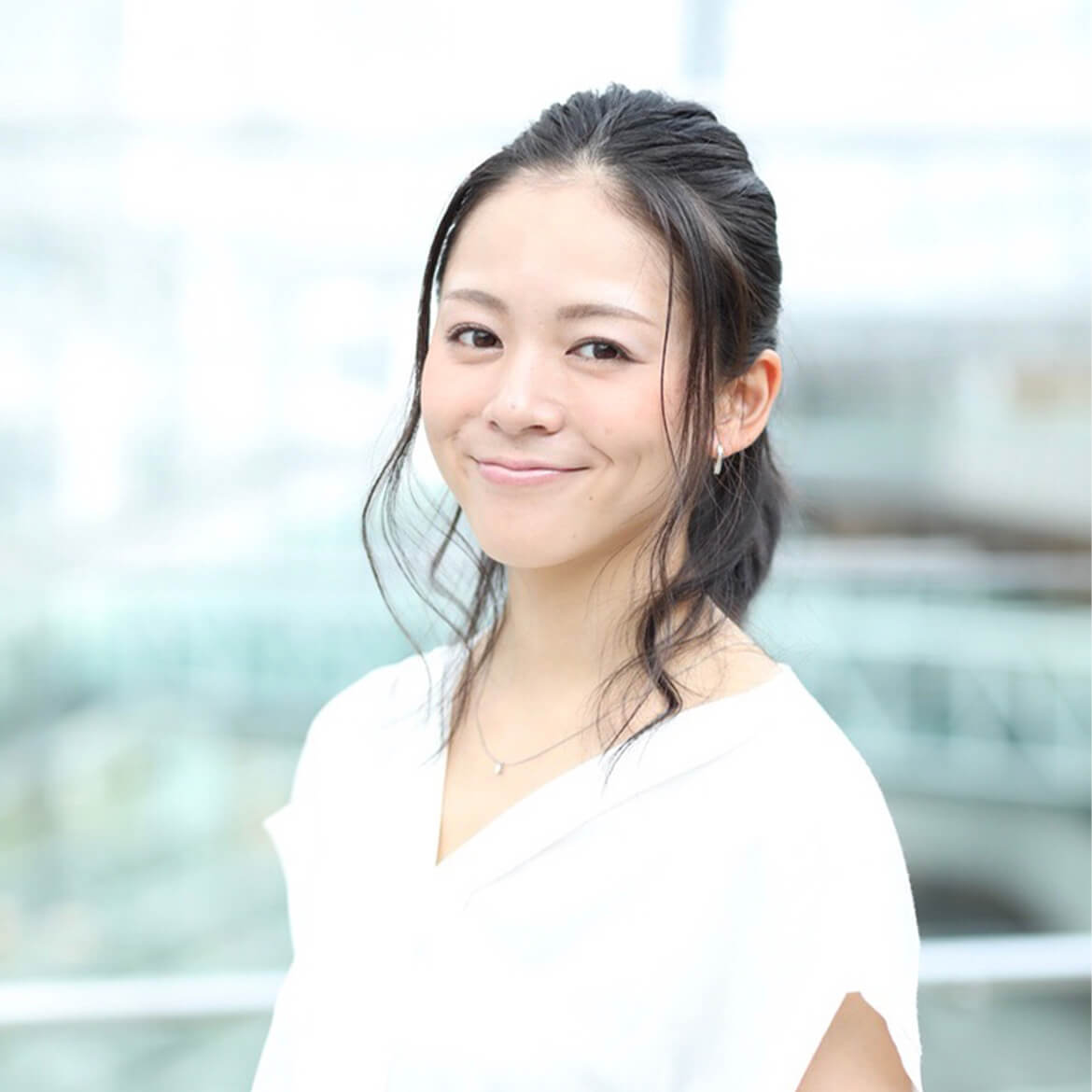
現在、デジタルをビジネスに取り込むことで生まれる価値について研究中。IoTに関する様々な情報を取材し、皆様にお届けいたします。