製造業の現場における、改善とは
小泉: 多くの中小製造業では、停止を記録しないものなのでしょうか?
木村: 我々のお客様では8-9割記録していないといえます。「1日何個作ったか?」という生産個数は記録していても、停止は書いていない場合がほとんどです。
たとえば、ある日は停止時間が少なかったとしても、原因の追究のしようがない。改善もできないということになります。
しかも、それを次の日にフォローするならまだしも、1週間くらいためてやるのと、当日のことは忘れてしまっていることが多く、とても詳細をフォローすることはできません。
小泉: では、現在、旭鉄工では、その日のうちにすべて解決しているのでしょうか。
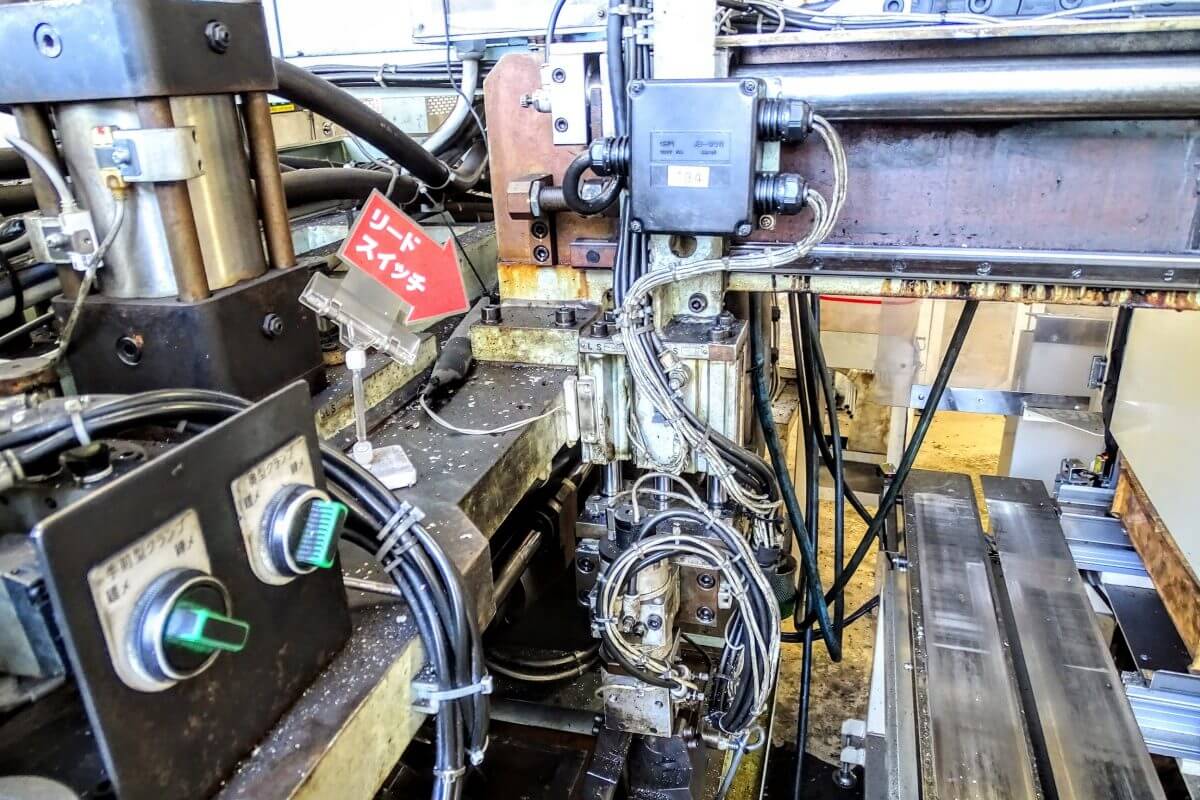
木村: 残念ながらそこまではできていないです。現状では、次の日に前の日のデータを見て、停止の原因や対策について、「ラインストップミーティング」という会議を開いて話し合っています。
本当は、もっとリアルタイムに細かくやりたいのですが、それは難しいのです。しかし、前の日であれば、現場に聞けば状況がわかります。
しかし、1週間ためると、もう思い出せない。十分とは言えなくても、遅くても次の日に対策できればよいと思います。
小泉: 現場の職人は、「ある時刻で、ある時間止まった」という事実が分かれば、原因がわかるものなのでしょうか?
木村: 通常「停止というのはそんなものだ」「いつものことだ」となってしまいます。
一方、これが表に出て、「これはなにが起きたの?」と、顕在化することで、知恵がでてきます。
問題点は「表に出す」ことが重要なのです。
小泉: まずは、問題が起きていることを顕在化して、そこについていろんな知恵を持ち寄って、課題をあぶりだし、そこから対応すべきということですね。
木村: はい。「見えない問題は直らない」といつも言っております。
小泉: ところで、こういった生産性の改善に関するノウハウは、木村社長がトヨタ生産方式を業務としてやってらっしゃったからわかることなのか、他社の工場でもみんなで話し合えばわかるようなものでしょうか。
木村: 日本の人はまじめなので、問題が見えれば考えられます。例えば、トヨタの生産調査部にいたとき、東日本大震災が起こった際、南相馬の会社に行ったことがあります。
私は、震災にも負けず、そこの工場を止めないことが、私のミッションでした。実際に現地に行くと、当時、問題点が見える化されていなかったのですが、工夫をして問題点を見える化し、共有したところ、「ここはもうちょっとこうやったら」、という改善に向けての話し合いを自分たちで始めていた、ということがあります。
無料メルマガ会員に登録しませんか?
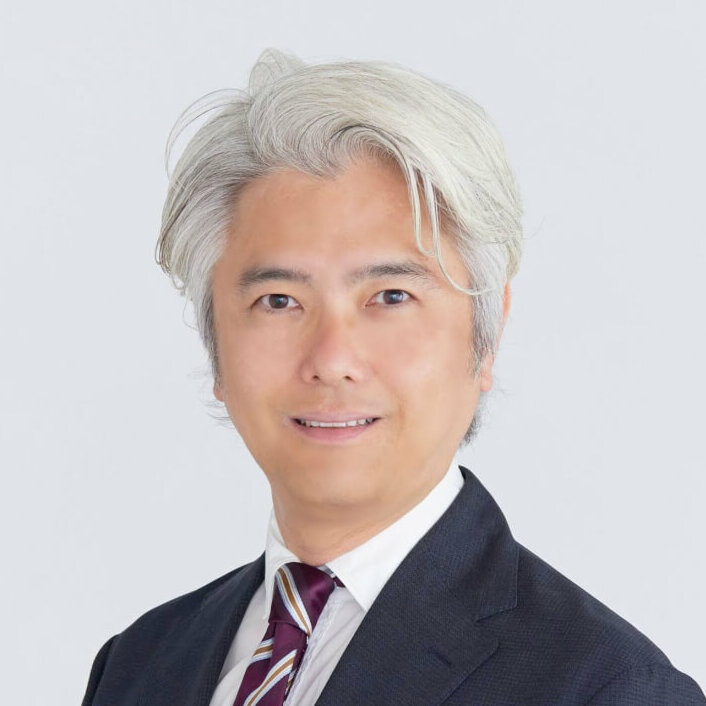
IoTNEWS代表
1973年生まれ。株式会社アールジーン代表取締役。
フジテレビ Live News α コメンテーター。J-WAVE TOKYO MORNING RADIO 記事解説。など。
大阪大学でニューロコンピューティングを学び、アクセンチュアなどのグローバルコンサルティングファームより現職。
著書に、「2時間でわかる図解IoTビジネス入門(あさ出版)」「顧客ともっとつながる(日経BP)」、YouTubeチャンネルに「小泉耕二の未来大学」がある。