2019年24日都内にて内田洋行ITフェア2019が開催された。
その中で「製造のプロセス全体をデジタル化〜AI/IoT/BIを活用したデジタル化で工場が変わる、経営が変わる〜」と題した講演を紹介する。
この講演では、IoTNEWS代表 小泉耕二がモデレーターとして、ウィングアーク1st 営業カスタマーサクセス本部 製造企画営業部 部長 荏原光誠氏、富士通 シニアエバンジェリスト 及川洋光氏、内田洋行 ビル事業推進部 部長 山本哲之氏を迎え、ディスカッションが行われた。
このパネルディスカッションでは、事例やソリューションの紹介しつつ、具体的なデータの取得や見方、KPIの立て方やまとめ方、実践方法などが語られた。
その結果、「デジタル」「人」「目的意識」と、共通する項目が浮かび上がってきた。
データの取得方法と目的の明確化
IoTNEWS 小泉が、1つ目のテーマを「足元で起きている製造業の変化」として、現在の状況を3者に聞いた。
ウィングアーク1stの荏原氏は、「多くの企業はデータの取得はしてるものの、そのうち整理されているデータは2割にすぎないという課題を持っている。」と語る。
整理されているデータとは、生産管理システムのデータベースに入っているようなもので、目的に合わせて検索をかければ出てくるようなデータのことだ。一方整理されていない非整理データは、設備のデータや日々の作業の日報、紙のレポートなどを指す。
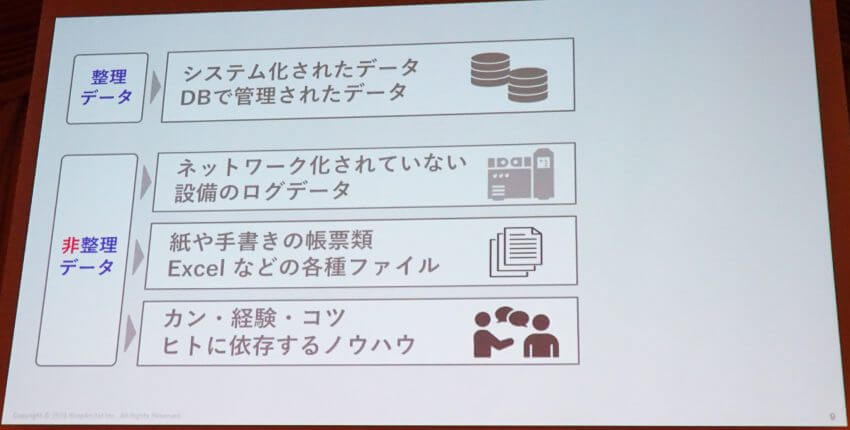
ここで重要なのは単純に非整理データを、整理した状態にすればよいわけではないという点だ。
そもそも「何のためにデータを取るのか」という目的をはっきりさせなければ、どんなデータを取得してもあまり意味はないということだ。
一方で、新しい投資をするためには、ROIが明確であることが重要だ。目的を明確にし、既にあるソリューションをうまく組み合わせて、段階的に展開していくことが必要になってくるのだという。
事例から取るべきデータと見方を示していく
そこでウィングアーク1stでは、レガシー機器に外付けセンサーをつけ、タブレットで比較的簡単に見える化できるソリューションを展開している。
そして取得したデータをどう見ていくのかという点に関しても、PoCをしていると時間がかかるため、目的と見方の例をテンプレートにして参考にしてもらうことで時間削減を測っている。
ここで荏原氏は、在庫管理の課題解決を行なったパナソニックの事例を挙げた。在庫コスト削減は多くの事業者が取り組もうとする一方、部材が多いとどこから手をつければいいのかわかりづらいという問題があると指摘する。
調達などはいくらデジタルを取り入れても結局は人が行う作業なので、いかに人が判断する材料を揃え支援をしていくかが重要になってくる。
そこでデータに色をつけ、意味を与えることで作業者が気づくことができるテンプレートを提案しているという。
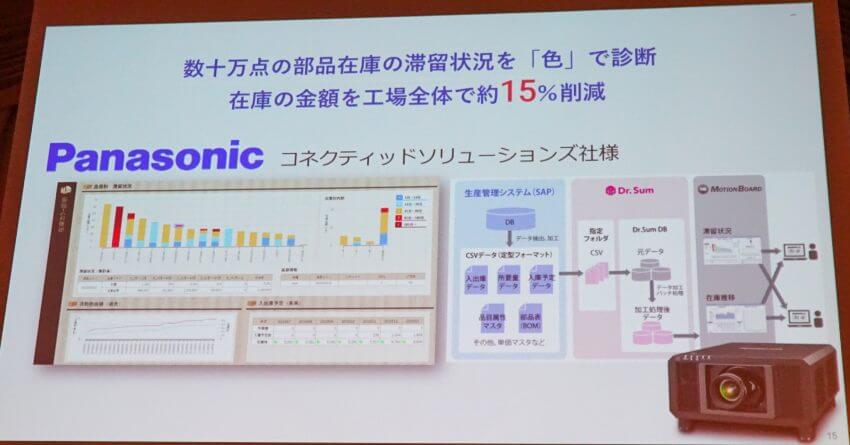
この図はパナソニックのプロジェクターの例で、左のグラフにはプロジェクターの部材が並んでいる。
左上のグラフは、在庫を金額に換算した際、その金額が大きい部材から並んでいる。棒グラフの色は、「滞留期間」をあらわしているのだ。調達してまだ間もないものは青、濃い赤になる程滞留期間が長いことを示している。
このグラフをみれば、高い金額の部材で長期間置いているものから順に何らかの対応が必要だという意識がわく。
在庫が滞留してしまう理由としては、資材部や製造部は欠品を出したくないため、部品の調達を前倒ししたり、多めに調達する傾向があるからだ。また、金額が高い部材は自社オーダーのカスタマイズ品などで、発注から納品までのリードタイムがかかるようなものも多いという。
並び順は金額ごとになっており、棒グラフをクリックすると完成品の需要データと掛け合わせ、今後の部材の使用量予測が表示されるのだ。
これは、滞留時間が長い部材であっても、今後使用される予定があるのであれば必要な在庫だという判断に使うのだ。
このように、「データ収集をして、可視化をすることで今を知るだけでなる、どのような見方をすれば良いのか、どこがいつもと違うのか、ということを伝えていくということが大切だ。」と荏原氏は言う。
現場に入り込んでデータの見方を模索する
次に、「データを見たうえでの改善活動はどういうことを具体的にしているのか」とIoTNEWS 小泉が質問した。
その問いに対しウイングアーク1stの荏原氏は、「確かにこれまではデータを出すが、その判断は顧客に委ねていたところがある。そこで顧客に入り込んで改善活動をしていこうという取り組みをした事例がある。」と、タイの工場で行なったプロジェクトの事例について語った。
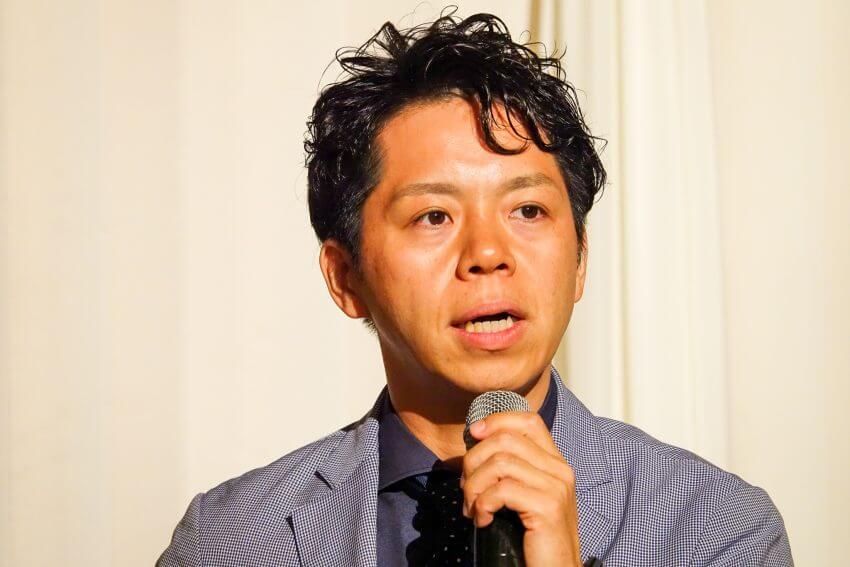
タイの工場では設備が古かったため、産業機械の稼働状態に関しては、光センサーをパトライトに巻きつけ、光った回数や時間を計った。また、マグネットセンサーを用い、仕上がった製品が通過する扉が開閉した回数を計測、何個製造できたのか、を計測するというシンプルなデータ取得から始めたのだという。
そのデータをクラウドにあげ、日本からでも生産個数や生産性のデータを見れるようにしたのだ。
ここで行なわれた具体的な改善活動は、「箱を10個入りから20個入りのものに変えて、箱の入れ替え回数を減らしたり、機械のスタートボタンの高さを合わせて効率性をあげるといったことだったという。
データを見て、改善内容について話し合う際も、毎日前日の状況データを見ながら改善について話し合ったのだという。
その結果、4ヶ月で56%から71%まで生産性が向上したのだ。
このようにウィングアーク1stでは工場における改善活動を積み重ね、うまく行った事例を汎用させながら、イレギュラーな状況に対しては現場に入り込んで改善し、また事例を増やしていくという取り組みを行っているのだ。
次ページは、「デジタル化することのメリット」
無料メルマガ会員に登録しませんか?
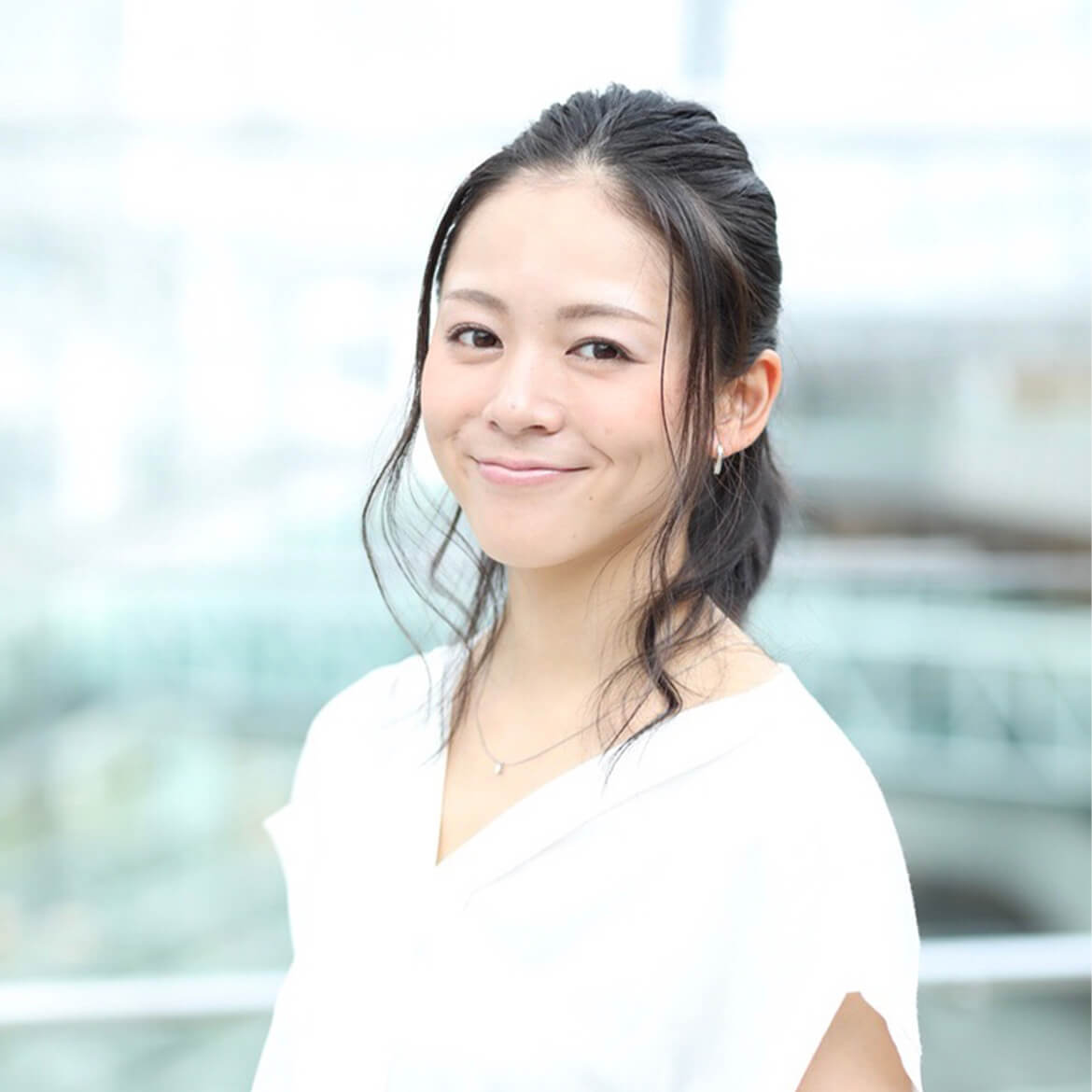
現在、デジタルをビジネスに取り込むことで生まれる価値について研究中。IoTに関する様々な情報を取材し、皆様にお届けいたします。