製造業の現場では、少子高齢化による労働力不足は深刻化し、長年培われた熟練技能の継承が危ぶまれています。
これにより、特定の従業員でなければ対応できない「属人化」の問題が、多くの現場で顕在化しています。
また、グローバル競争の激化や、予期せぬ事態によるサプライチェーンの混乱など、事業を取り巻く不確実性は増しています。
こうした状況下における打ち手の一つとして、生産プロセスの「標準化」と「デジタル化」が挙げられます。
生産プロセスを標準化することで、誰でも一定以上の品質で作業できる体制を整え、さらに標準化されたプロセスをデジタル化することで、作業手順やノウハウに容易にたどり着くことができます。
本稿では、属人化を防ぐために「標準化」と「デジタル化」がなぜ重要なのかに加え、具体的な進め方について解説します。
関連記事:属人化の課題と標準化の重要性については、こちらの記事も参考にしてみてください。
属人化とは?属人化が起きる原因やデメリット、デジタルを活用した具体的な解消方法などを解説
生産プロセスにおける標準化の重要性
まずは、生産プロセスを標準化することの価値を整理したいと思います。
生産プロセスの標準化とは、特定の作業や工程について、最も効率的かつ安全で、安定した品質を保つための最適な手順や方法を定め、それを文書化し、全ての関係者がその定めに従って実行する仕組みを構築することです。
標準化が行われていない現場では、同じ業務内容でも担当者によってやり方が異なったり、長年の経験を持つベテラン作業員の暗黙知や勘(カン)に頼ったりすることが多くなります。
これはいわゆる「属人化」が進んだ状態であり、品質のばらつきや生産性の低下、教育の非効率や問題の原因究明の困難化などを引き起こす可能性があります。
また、改善活動を行いたくたくても、そもそもの「標準」がなければ、現状を正しく把握し、どこをどう改善すれば良いのかを決めることすらできません。
このように、標準化は、個人のスキルや経験に依存する属人化から脱却し、組織として安定した生産活動を行うための土台となるものです。
生産プロセスを標準化することで、品質の安定、生産性の向上、安全性の確保、人材育成の効率化、継続的な改善活動を推進します。
しかし、この標準を定めるだけでは十分ではありません。定められた標準が現場に正確に伝わり、遵守され、そして時代の変化や改善に基づいて常に最新の状態に保たれる必要があります。
標準化された生産プロセスをデジタル化する重要性
生産プロセスの標準が出きたとしても、従来の紙ベースのマニュアルや、個人のローカルPC内に分散した状態での管理では、標準の維持や管理に限界があることが少なくありません。
上述したような従来型のドキュメント管理では、以下のような問題が起きているのではないでしょうか。
- 仕様変更や改善があっても、マニュアルの改訂・配布に時間がかかり、現場に最新の情報が行き渡らない
- 必要なマニュアルがどこにあるか分からず、探すのに時間がかかる、あるいは結局見ずに自己流で作業してしまう
- 紙のマニュアルでは、複雑な工程や微妙なニュアンスを含む作業が伝わりにくく、理解にばらつきが生じる
こうした問題が発生してしまうと、せっかく生産プロセスを標準化しても、生産性の低下、品質のばらつき、教育コストの増加を引き起こす要因となる可能性があります。
そこで、標準化した生産プロセスを現場に届け、活用し、改善していくために不可欠となるのが「デジタル化」です。
デジタルドキュメントのメリット
では、標準化された生産プロセスがデジタル化されたドキュメント(以下、デジタルドキュメント)を活用することで得られるメリットは、どのようなものがあるのでしょうか。
まずは、情報のリアルタイム性と最新性が挙げられます。
生産プロセスは、変更や改善が行われることがありますが、従来型のドキュメント管理では、迅速に反映することが難しく、結局個人の頭の中にあるという属人化を生みがちです。
デジタルドキュメントであれば、変更点や改善点をインターネット上から更新でき、閲覧が許可された関係者全員に迅速に共有することができます。
閲覧する側も、インターネット接続があればPCやタブレット、スマートフォンなどの様々なデバイスからいつでもアクセスすることができます。
また、キーワード検索やカテゴリ分類により、必要な情報にすぐにたどり着けます。作業中に不明点が発生した場合でも、その場ですぐに正しい手順を確認できるため、作業の中断を最小限に抑え、確実な作業遂行を支援します。
さらに、デジタルドキュメントは、テキストや静止画だけでなく、動画、音声、3Dモデルといったインタラクティブな要素を組み込める点もメリットのひとつです。
これにより、文字だけでは伝えにくい微妙な作業のコツや、複雑な手順も視覚的・聴覚的に分かりやすく伝えることができます。
特に、新しい作業者への教育においては、理解度と習得スピードを向上させる効果が期待できます。
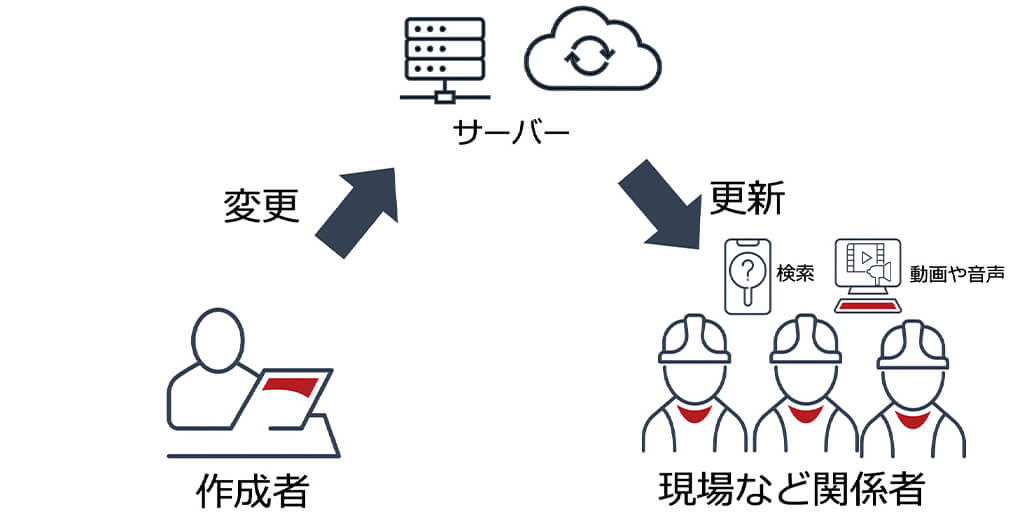
加えて、デジタルドキュメントを継続的な改善基盤として活用することもできるでしょう。
例えば、誰がどのような内容を閲覧したかなどのデジタルドキュメントの利用状況と、IoTから収集される実際の作業データなどを紐づけて分析することが可能です。
これにより、「どの手順が守られていないか」「どのステップで時間がかかっているか」「どの部分の理解が進んでいないか」といった課題を客観的に把握し、継続的なプロセス改善やマニュアル自体の改善に繋げることができます。
このように、デジタルドキュメントは、単に情報を記録するだけでなく、現場の生産性や品質の向上に加え、人材育成を効率化するなどのメリットがあります。
生産プロセスの標準化とデジタル化のステップ
この章では、デジタルドキュメントを実際にどのように作成し、現場で「使える」状態にするのか、具体的なステップの一例について紹介します。
対象プロセスの選定と範囲定義
まずは、どのプロセスを標準化するかを明確にする必要があります。
例えば、「属人化の度合いが高い」「品質や生産性に大きな影響を与えている」「安全上のリスクがある」といった優先度の高いプロセスから着手するのが効果的でしょう。
改善効果が大きい、あるいはリスクが高いプロセスを特定し、「不良率〇%削減」「作業時間〇%短縮」など、その標準化によって何を達成したいかを明確にします。
生産管理システムやMESなど、すでにシステムを活用している場合は、蓄積された実際の稼働データや作業ログを分析し、標準から外れた作業が多いプロセスや、ボトルネックとなっている工程を客観的に特定するのに役立ちます。
また、各工程の生産タクトタイム(理想的な生産ペース)、不良発生率、設備稼働率などを監視し、標準化による改善インパクトが大きいプロセスを特定することも有効です。
関連記事:生産管理システムやMESなどについて知りたい方はこちらの記事も参考にしてください。
生産管理システムとは?導入プロセスやメリットをわかりやすく解説
MES(製造実行システム)とは?機能や導入ステップ、課題などをわかりやすく説明
現状プロセスの把握と分析
どのプロセスを標準化するか決まったら、現在の作業が実際どのように行われているかを正確に把握する必要があります。
この段階では、属人化された暗黙のルールやベテランのコツなど、「人」に紐づく情報を引き出すことが重要です。
例えば、作業者の実際の作業風景を動画や写真で記録し、ベテラン熟練者の手の動きや体の使い方、注意点などを視覚的に捉えることで、文字だけでは伝わりにくい詳細な手順やコツを把握して記録します。
また、標準化対象のプロセスの作業手順、判断基準、作業時間、使用ツールなどを把握し、無駄や非効率な部分、属人化している要素を洗い出します。
理想的な標準プロセスの設計と合意形成
現状分析で暗黙のルールやベテランのコツ、課題を明らかにしたら、安全性、品質、効率性を最適化した「こうあるべき」という標準プロセスを設計します。
無駄を排除し、安全で効率的、かつ安定した品質を保証できる作業手順を設計しましょう。
この際、現場の意見を取り入れ、関係者間の合意を形成することが、その後の定着に不可欠です。
合意形成をとるために、業務や作業のプロセス(流れ)を視覚的に分かりやすい図として作成するためのフローチャートやプロセスマップなどを用いるのも有効です。
デジタルドキュメントの作成
標準プロセスを設計したら、いよいよデジタルドキュメントの作成です。
効果的なデジタルドキュメントを作成し、現場に定着させるためには、適切なツールの選択が非常に重要です。
様々なツールがありますが、特に製造現場での利用を考慮した場合、以下の点を基準に選定することをお勧めします。
現場作業者にとっての使いやすさ(閲覧側)
デジタルドキュメントは、現場の作業員が迷うことなく、直感的に必要な情報を探し出し、手順を確認できるインターフェースであるかが鍵となります。
タブレットやスマートフォンなど、現場で使用するデバイスでの表示や操作に最適化されているかといったことに加え、文字サイズやボタン配置などを確認しましょう。
また、現場の通信環境が悪い場合、インターネット接続が不安定な環境でも利用できるオフラインアクセス機能があるかどうかも重要な要件となります。
作成者にとっての使いやすさ
現場での使いやすさに加え、デジタルドキュメントを作成する側のインターフェースも重要です。
例えば、新規作成や改訂が容易であるか、直感的な操作でテキスト、画像、動画などを配置できる編集機能があるかなどを確認するといいでしょう。
また、これまでWordやExcelを活用してドキュメント管理していた場合、これらを容易にインポート・変換できる機能があると、移行の負担を軽減できます。
他にも、最新のバージョン管理や改訂履歴の記録、承認ワークフロー機能など、運用していく中であると便利な機能も確認しておくといいでしょう。なお、現場には常に最新版のみが配信される仕組みが理想的です。
既存システムとの連携性
すでに、生産管理システムやMES、IoT プラットフォームやナレッジ共有ツールなどを導入している場合、他のシステムと連携できるかどうかも重要なポイントです。
例えば、作業指示とデジタルドキュメントを紐付けたり、デジタルドキュメントの利用データと生産実績を組み合わせて分析したりする際には連携が必要となります。また、API(アプリケーション同士をつなぐインターフェース)が公開されているかといったことも確認するといいでしょう。
運用・管理機能
作成したマニュアルや標準プロセスを、効率的に管理・運用するための機能が充実しているかを確認します。例えば、カテゴリ分類やタグ付け、検索機能や利用状況のレポート機能などが挙げられます。
ポイントは、数が増えても管理が破綻しない仕組みであるかどうかという点です。
また、生産プロセスの中には、独自のノウハウや、外部に知られてはならない機密性の高い情報が含まれている場合があります。
こうした場合、誰が「閲覧」「編集」「削除」「承認」「公開」といった操作を行えるかを制限・設定する権限管理機能が搭載されている必要があります。
ベンダーのサポート体制と製造業への理解
導入時や運用中に適切なサポートを受けられるか、ベンダーが製造業固有のワークフローや課題を理解しているかどうかも重要な選定基準です。製品の導入事例なども参考にすると良いでしょう。
これらの選定ポイントを踏まえ、自社の規模、予算、標準化の対象範囲、そして何よりも「誰が、どこで、どのようにデジタルドキュメントを使うのか」という現場のニーズに最も合ったツールを選択することが、「使える」デジタルドキュメント作成の第一歩となります。
改善し続けられる運用環境の構築
デジタルドキュメントを作成し、現場で活用されるようになっても、それで終わりというわけではありません。
デジタルドキュメントの内容自体の改善や、使いやすいインターフェースへのさらなる改善など、より良い形に進化し続ける体制を構築することが望ましいでしょう。
例えば、デジタルドキュメント上に作業ステップのチェックボックスや、測定値の入力フィールド、写真や動画の添付機能などを設けることで、作業者が指示に従っているかを確認できるほか、作業結果や気づきをその場でデジタル情報として記録することができます。
また、現場の声をフィードバックするために、コメント機能、専用のフィードバックフォーム、あるいは音声入力などを活用し、作業中に気づいた改善点や疑問点を容易にシステムに投入できるようにしておくことも有効です。
そして、収集されたフィードバックや改善提案は、自動的に担当者に通知し、システム上でレビューや検討、承認プロセスが実行できるようにしておくと、さらに便利です。
これにより、関係部門間での情報共有や承認状況の確認がスムーズに行え、改訂にかかるリードタイムを短縮することができます。
さらに、デジタルドキュメントの活用データと実際の生産データを組み合わせることで、設計した「標準」が現場でどのように機能しているかを客観的に評価し、さらなる改善点を発見することができるでしょう。
例えば、「特定のステップで作業時間が長くなっている」「特定のドキュメントを参照した後に不良が発生している」「デジタルドキュメントの導入がタクトタイムにどう影響したか」といった分析を行います。
これにより、どの部分が理解されにくいか、あるいは非効率であるかをデータに基づいて特定できる可能性があります。
他にも、蓄積された大量の作業データやデジタルドキュメントの利用データをAIが分析し、より効率的で安全な作業手順を提案したり、将来的なトラブルリスクを予測して予防的な改訂を促したりすることも考えられるでしょう。
このように、一度作成した内容を、継続的に改善することができる環境を整えることが重要です。
デジタルドキュメントから派生する可能性
こうして生産プロセスが標準化し、その情報がデジタル化されていると、さらなる価値創造へと繋がる可能性があります。
例えば、IoTデバイスから収集されるリアルタイムの設備稼働データやセンサー情報と、デジタル化された標準作業手順を紐づけることで、異常が発生した際に必要な対応手順を自動で表示したり、AIが特定の条件に基づいて最適な作業指示を生成したりすることが可能です。
また、AR(拡張現実)やVR(仮想現実)といった技術と組み合わせることで、作業現場で必要な情報や手順をリアルタイムにオーバーレイ表示したり、没入感のあるトレーニングを提供したりするなど、標準作業の伝達や習得のあり方を変えることもできるでしょう。
このように、生産プロセスを標準化し、デジタル化することは、単に技術やノウハウを記録・共有するだけでなく、新しい価値を生み出す可能性を秘めています。
無料メルマガ会員に登録しませんか?
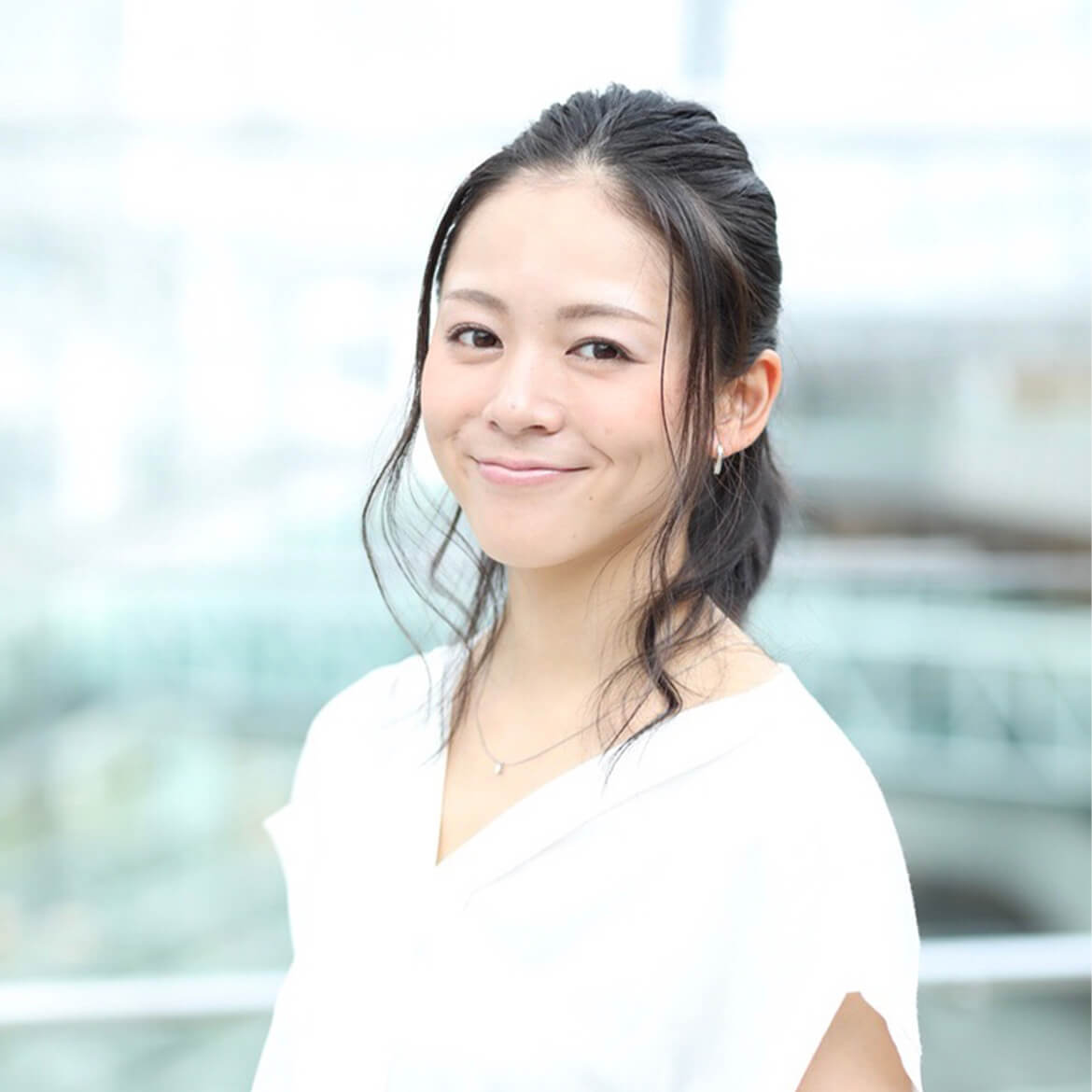
現在、デジタルをビジネスに取り込むことで生まれる価値について研究中。IoTに関する様々な情報を取材し、皆様にお届けいたします。