モノを製造する過程では、「どんなものを」「いつ」「どのくらい作るか」といった生産管理を行う必要があります。
そして前回、データをもとに計画を立て、生産管理を支援してくれる生産管理システムを紹介しました。
今回は、この生産管理システムで立てた計画の管理や、現場で実行・監視・フィードバックを行うMESというシステムについて紹介します。
MESとは?
MESは、Manufacturing Execution Systemの略で、製造実行システムと訳されます。
生産管理システムやERPなどで計画された、全社的な視点での計画内容をさらに細かく管理したり、現場での作業を実行・監視・最適化したりするシステムです。
MESの役割
MESは主に、「管理」と「実行」という二つの役割があります。
管理系MES
管理系MESは、生産管理システムやERPなどで収集された、ヒト(人事)・モノ(在庫管理)・カネ(財務状況)といった全社的な情報をもとに、より細かな生産計画の策定し、その計画の進捗管理に加え、品質管理や在庫管理などを行います。
実行系MES
実行系MESは、管理系MESから指示された生産計画に基づき、現場の生産活動を制御するシステムです。計画どおりに設備を制御したり、設備や人の作業をリアルタイムで監視したり、必要に応じて調整を行ったりします。
そして、実行系MESは、現場で収集したデータを管理系MESにフィードバックすることで、計画の精度向上や改善活動に貢献します。
例えば、設備の稼働データを収集して分析することで、次回の生産計画に反映させたり、現場での作業効率を向上させたりといった取り組みが可能になります。
なぜMESが必要なのか
生産管理システムやERPといった上位層のシステムから、直接現場の制御ができた方がシンプルで良いのは?と感じるかもしれません。
しかし、バリエーションが多い製品を少量ずつ生産する「多品種少量生産」や、製品の種類や生産量が変動する「変種変量生産」といったカスタマイズ対応が求められる現代では、収集するデータや制御しなければならない要素が膨大なため、たったひとつのシステムで全てを行うのは難しいのです。
また、上位層のシステムは、全社的なデータを日単位、週単位、月単位といった大きな単位で収集して分析しますが、実際の現場では分単位やリアルタイムな制御が求められます。
さらに、上位層のシステムと現場のシステムではデータフォーマットやインターフェースなども異なるため、この間を取り持つためにも、MESが必要となるのです。
製造プロセスにおけるMESの位置付け
より具体的にMESの役割を理解するために、製造プロセスを「計画層」「実行層」「制御層」に分けて説明します。
この層の中でMESは「実行層」に位置し、前述した「管理」と「実行」という役割を果たしています。
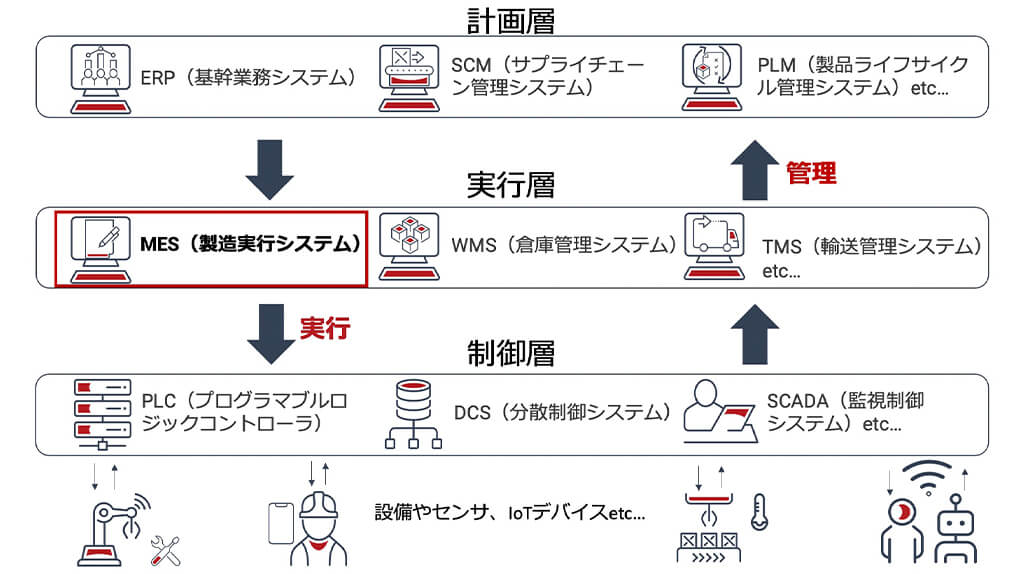
計画層では、生産管理システムに加え、企業全体のリソースを統合的に管理するERP(基幹業務システム)や、サプライチェーン全体の計画を最適化するSCM(サプライチェーン管理システム)、ライフサイクル全体を通じた情報共有を行うPLM(製品ライフサイクル管理システム)などが位置します。
そして、実行層では、計画層の情報を管理したり、計画層の指示を具体的な作業に落とし込んで生産計画を立案したりして、制御層へと指示を出します。この実行層に位置するのがMESです。
実行層にあたるその他のシステムとしては、倉庫内の在庫管理や入出庫の作業指示などを行うWMS(倉庫管理システム)や、生産現場への輸送計画を管理するTMS(輸送管理システム)などがあります。
制御層では、実行層から得た指示をもとに、現場の設備や機器を直接動かし、リアルタイムでの制御を行います。
制御層に当たる主な機器や装置としては、各製造装置や生産ラインの制御を行うPLC(プログラマブルロジックコントローラ)や、工場全体のプロセス制御を統合的に管理するDCS(分散制御システム)、設備の監視やデータ収集を行い、制御層と計画層や実行層とをつなぐSCADA(監視制御システム)が挙げられます。
そして、これらの制御層がセンサや設備から温度、圧力、振動などのデータを収集したり、モータやバルブなどのアクチュエータを直接制御したりすることもあります。
データの流れとしては、計画層での計画をもとに、実行層で具体的な作業に落とし込み、実際に制御層で設備や機器を制御します。そして、制御層で収集したデータは実行層を通じて計画層にフィードバックされ、次回の計画の改善に活用されます。
MESの導入ステップ
ここでは、MESを導入する際の大まかなステップについて紹介します。
現状分析と課題の明確化
まずは、「生産性の低下」「品質管理の不備」「トレーサビリティの欠如」など、現在の製造プロセスや設備管理における課題を特定します。
そして、現場で収集されているデータの種類や量、活用状況を確認し、改善の余地を見つけます。
導入目的の設定とデータ収集の設計
次に、MES導入によって達成したい目標と、その目標を達成するために必要なデータを定めます。
例えば、詳細なスケジュールを立案して欲しいなら、製品の種類や納期、優先順位、設備や作業者の情報、原材料の在庫状況などのデータが挙げられるでしょう。
設備や人を配分して、状況を監視したいなら、設備の細かな性能や稼働状況、作業者のスキルや稼働可能時間、経験値や作業効率などのデータが必要となります。
そして、これらの必要となるデータを、どれくらいの頻度やタイミングで、どのように収集するかを詳細に設計する必要があります。
コード体系の設計
MESは、計画層と制御層の橋渡しの役割も果たすという説明をしましたが、橋渡しをするためには、収集したデータを計画層や制御層にも分かる形にする必要があります。
そこで、製品を一意に識別するための「製品コード」や、工程番号や作業内容、設備IDを組み合わせた「工程コード」、工場名、ライン番号、機械IDを組み合わせた「設備コード」など、コード体系を設計します。
すでに計画層のシステムで独自の識別方法が確立されている場合や、コードを後から設定する前提での導入初期段階ではこのステップは省かれますが、他システムや設備と連携するためには必要な工程となります。
現場スタッフの業務や運用フローの影響を考慮
MESは、導入すると現場の作業に直接影響を与えるシステムです。
そのため、「現場への作業指示や進捗確認の方法を現場で使いやすい形にするにはどうすべきか」「MES導入後にスタッフの負担が軽減されるような設計になっているか」など、現行の運用フローを詳細に把握した上で、どのようにMESを導入して効率化・最適化するかを検討する必要があります。
トラブルシューティングのための現状理解
一連の製造プロセスにおいて、万が一トラブルが発生した場合に、MESがどのように対応するかを設計します。
例えば、過度の振動や温度変動といった設備の異常、生産遅延、品質の問題など、トラブルの兆候が現れたときにリアルタイムで警告を発するよう設定するといったことや、MESが特定の設備に対して再調整を指示するなどのアクションが考えられます。
また、MESが他のシステムと連携してトラブルシューティングを行う場合、どの情報をどのタイミングで共有するかを定義します。これにより、関連するシステムが一貫した対応をとれるようになります。
さらに、トラブル発生後に得られたデータをもとに、次回の生産計画や作業の改善に役立てることも重要です。適切なデータを収集してその情報をフィードバックすることで、継続的な改善プロセスを支援します。
MESの導入形態
MESの導入形態は「オンプレミス型」と「クラウド型」の2つに分類できます。
オンプレミス型MES
オンプレミス型MESは、自社のサーバやインフラを使用してシステムを構築・運用する形態です。
導入時にハードウェアやソフトウェアを自社で購入・設定する必要があり、主に大規模工場や高度なカスタマイズが必要な現場で採用されることが多いです。
メリット
生産プロセスや独自の業務フローに合わせた柔軟なカスタマイズが可能です。
また、データが自社内に保存されるため、セキュリティ管理を自社内で完全に行えるのもメリットのひとつです。
デメリット
ハードウェアやソフトウェアの購入費用、インフラ構築費用が必要で、初期コストが高い傾向にあります。
また、運用に関しても、サーバの管理やシステムのメンテナンスを自社で行う必要があるため、コストや手間がかかります。
クラウド型MES
クラウド型MESは、インターネットを通じてクラウド環境上でシステムを利用する形態です。サーバやインフラの管理はクラウドサービスプロバイダが行い、月額料金や使用量に応じた課金モデルが一般的です。
メリット
オンプレミス型と比べ、初期費用を抑えつつ、必要な機能をスピーディーに利用開始することができます。
また、生産拠点の拡張や利用ユーザの増減に対応可能なほか、運用時にもプロバイダーがシステムを定期的にアップデートすることで、常に最新の機能を利用可能な点が挙げられます。
デメリット
パッケージでの提供の場合、特定の業務フローや業務プロセス変更に合わせたカスタマイズが難しい場合があります。
また、データが外部サーバに保存されるため、情報漏洩リスクやデータ所有権に関する課題が発生する可能性があります。
これら両者のメリット・デメリットを踏まえ、自社の規模や求める機能とすり合わせ、最適なMESを選択する必要があります。
MESのメリット
ここでは、MESを導入することで得られるメリットをいくつか紹介します。
リアルタイムな生産状況の把握
MESは、製造プロセスの実行を担うため、基本的に生産ラインの状況を常時監視しています。これにより、進捗状況、機械の稼働状況、作業の遅延などが把握でき、問題が発生する前に対処することができます。
リアルタイムで情報を取得することで、迅速な対応が可能になり、製品の納期遅延や品質問題を防ぐことができます。
効率的な生産計画とスケジュール管理
MESは、計画層で計画された内容を基に、計画通りに生産を進行していきますが、作業の進捗によっては予定変更や調整が必要な場合もあります。
こうした場合にもMESは柔軟に対応することができます。
品質の向上とトレーサビリティの強化
各製品の製造過程や使用した原材料、設備の状況などをデータとして記録することで、トレーサビリティ(追跡可能性)を提供します。
これにより、品質問題が発生した場合でも、問題の発生原因を特定しやすくなり、改善活動や再発防止策を迅速に講じることができます。
設備稼働率の向上とメンテナンス管理
設備の稼働状況を監視することで、定期的なメンテナンスのスケジュール管理や、故障発生時の原因分析に役立つデータを提供し、稼働率の向上をサポートします。
これにより、突発的な故障やダウンタイムを減らします。
データ駆動型の意思決定支援
製造現場から得られる膨大なデータを蓄積して分析するため、企業の経営層や生産管理者は、リアルタイムなデータに基づいた意思決定を行うことができます。
例えば、無駄な工程や時間帯を発見したり、人が最適配置されていない箇所を特定したりと、生産性向上のための最適化ポイントやコスト削減の機会をデータから見つけ出すことができる可能性があります。
MESの課題
MESは、計画層と制御層の橋渡しの役割であるが故に、導入や運用においては、IT(情報技術)とOT(運用技術)の両方の観点を考慮する必要があります。
これらの領域が交差するため、MESの導入には特有の課題が存在します。
ITとOTのシステム統合の難しさ
ITとOTは、異なる目的や仕様で設計されたシステムです。ITは主にデータ処理や情報管理、ビジネスプロセスを支えることを目的としていますが、OTは製造現場の機器や設備の制御を中心に設計されています。
MESは、これら二つの領域に関わるため、システムを連携させるには、データフォーマットやインターフェースの違いを理解した上で、ITシステムとOTシステムの異なる通信プロトコルを統合する必要があります。
さらに、古い設備や独自の制御システムを使用している工場では、ITシステムとOTシステムの互換性が低く、連携が困難なこともあります。
リアルタイムデータの取り扱い
MESは多くの場合、現場からリアルタイムでデータを収集し、即時に処理やフィードバックを行います。
この際、ITとOT間でデータの伝送や処理がスムーズに行われなければなりませんが、OT側の設備から収集したデータがITシステムに伝送される際に遅延が生じると、リアルタイムでの生産管理が難しくなるという課題があります。
また、ITシステムとOTシステムの間でデータの整合性を保つことが重要ですが、データが異なる形式で管理されている場合や、リアルタイムで同期されていない場合には、データの一貫性を維持するのが難しくなります。
セキュリティの問題
ITとOTが連携することにより、サイバーセキュリティのリスクが増大します。
製造現場のOTシステムは、物理的な設備や機器と直接接続されているため、外部からの攻撃が現場の設備に影響を及ぼす可能性があります。
そのため、MESを含むITシステムがOTシステムと接続されることで、新たなセキュリティリスクが生じることが考えられます。
異なる技術スタックと専門知識
ITとOTでは、扱う技術が異なるため、それぞれの領域に特化した専門知識が必要です。
ITのエンジニアはソフトウェアやシステム設計に詳しい一方、OTのエンジニアは機器や製造プロセスに精通しています。
MESの導入にあたり、両者の協力が不可欠ですが、技術スタックや知識の違いがコミュニケーションの障壁となることがあります。
システムの柔軟性とスケーラビリティ
製造業の現場では、設備や製造プロセスが常に変化しています。
新しい機械やラインが導入されたり、生産ラインの仕様が変更されたりするため、MESはその変化に柔軟に対応できる必要があります。
しかし、ITとOTの両方に対応するシステムの柔軟性を保つことは容易ではありません。
これらの課題を克服するためには、ITとOTの連携強化や、データの整合性、セキュリティの強化、柔軟なシステム設計が重要です。
MES導入を成功させるためには、両領域の協力体制を築き、システム全体の統合を進めていくことが不可欠です。
業界別の導入例
MESは、幅広い業界で導入され、それぞれの業界の特性に応じた形で活用されています。
ここでは、各業界ごとにMESがどのように活用されているのか、その一部の具体例を紹介します。
自動車業界
自動車業界は、多品種少量生産や厳格な品質管理が求められる業界です。MESは、複雑な生産ラインを最適化し、品質向上や生産効率化を実現するために利用されています。
多品種少量生産の現場では、需要予測の変動、受注量の変更、新しい顧客の追加など、日々様々な変更が起こります。
こうしたサプライチェーンや販売計画の変更が発生した際、まずはERPなどの計画層でその変更内容が更新されます。
そして、計画層で更新された情報がMESに送られ、「どの製品をどのくらいの量生産するか」「いつまでに生産を完了する必要があるか」「資材の使用計画」といった情報をMESが受け取り、実行層での具体的な作業計画に変換します。
この作業計画に沿って、生産ラインの変更指示や作業者へのタスク配分、設備への制御指示を行い、これらの進捗、異常、設備稼働状況などをMESがリアルタイムで状況を監視し、必要に応じてさらに調整を行います。
品質管理に関しては、MESが生産中の各部品や車両の状態を記録し、いつ、どこで、どの作業が行われたかを追跡することで、不具合が発生した場合、迅速に原因を特定し対策を講じることができます。
異常が検知された場合には、該当する車両や部品を生産ラインから即時除外し、原因が解決されるまで次の工程に進ませない仕組みを構築することもできるでしょう。
食品・飲料業界
食品・飲料業界では、品質と安全性を保つことが求められます。MESは、原材料の管理から製品の出荷までを一貫して監視し、規制への準拠をサポートします。
例えば、食品衛生法やHACCPといった規制の要件に対応するため、MESで製造プロセスを記録し、必要なデータを提出可能にすることができます。
また、原材料の仕入れ先から出荷された最終製品に至るまで、ロット単位でデータを記録することで、万が一問題が発生した場合にも影響を受けたロットを特定し、効率的にリコールを実行することが可能です。
製薬業界
製薬業界では、製品ごとに異なる製造手順があり、手順を正確に守らないと品質不良や規制違反が発生してしまいます。
そこで、MESに製品ごとの製造手順を登録しておき、作業者には電子的に標準化された手順を提供します。
例えば、錠剤を製造する際、配合比率や混合時間が指示として画面に表示され、手順通りに進めるといったことや、各工程ごとにMESが進捗を監視し、次工程に進む前に必要な条件(温度や時間の測定結果など)が満たされているかを確認します。
また、特定の工程には専門資格を持つ作業員が必要なケースがありますが、MESが資格情報を管理することで、適切な人員を割り当てることができます。
半導体業界
半導体製造は、ナノメートル単位の超高精度が求められる業界であり、その製造プロセスは多段階かつ複雑です。
数百〜数千段階の工程がある上に、工程ごとに異なるパラメータ(温度、圧力、時間など)を厳密に管理する必要があります。
そこで、MESにより各工程における製造条件(レシピ)を一元管理し、製造装置へ正確なパラメータを自動的に送信することで、どの製品でも同じ条件で加工を実行することができます。
また、新しい設計仕様や製品要求が発生した場合にも、MES経由で変更を全装置へ展開することができます。
その他にも、化学業界や電子機器業界など、様々な業界において、進捗管理やトレーサビリティ、規制準拠や品質管理、データ分析やメンテナンスの自動化などの支援を行っています。
MESのトレンド
MESの課題では、ITとOTの統合の難しさを挙げましたが、この課題を解決するべくノーコード・ローコード化したMESが登場しています。
また、作業者情報を正確に記録・蓄積するために、顔認証技術を導入したMESや、データ分析にAIを活用したMESなど、新たな技術を搭載していく流れも生まれています。
一度MESを導入すると、新たなシステムに変えるのは容易ではありませんが、新しいトレンドもチェックしながら、費用対効果に見合った拡張や改変を考え続けることも重要です。
無料メルマガ会員に登録しませんか?
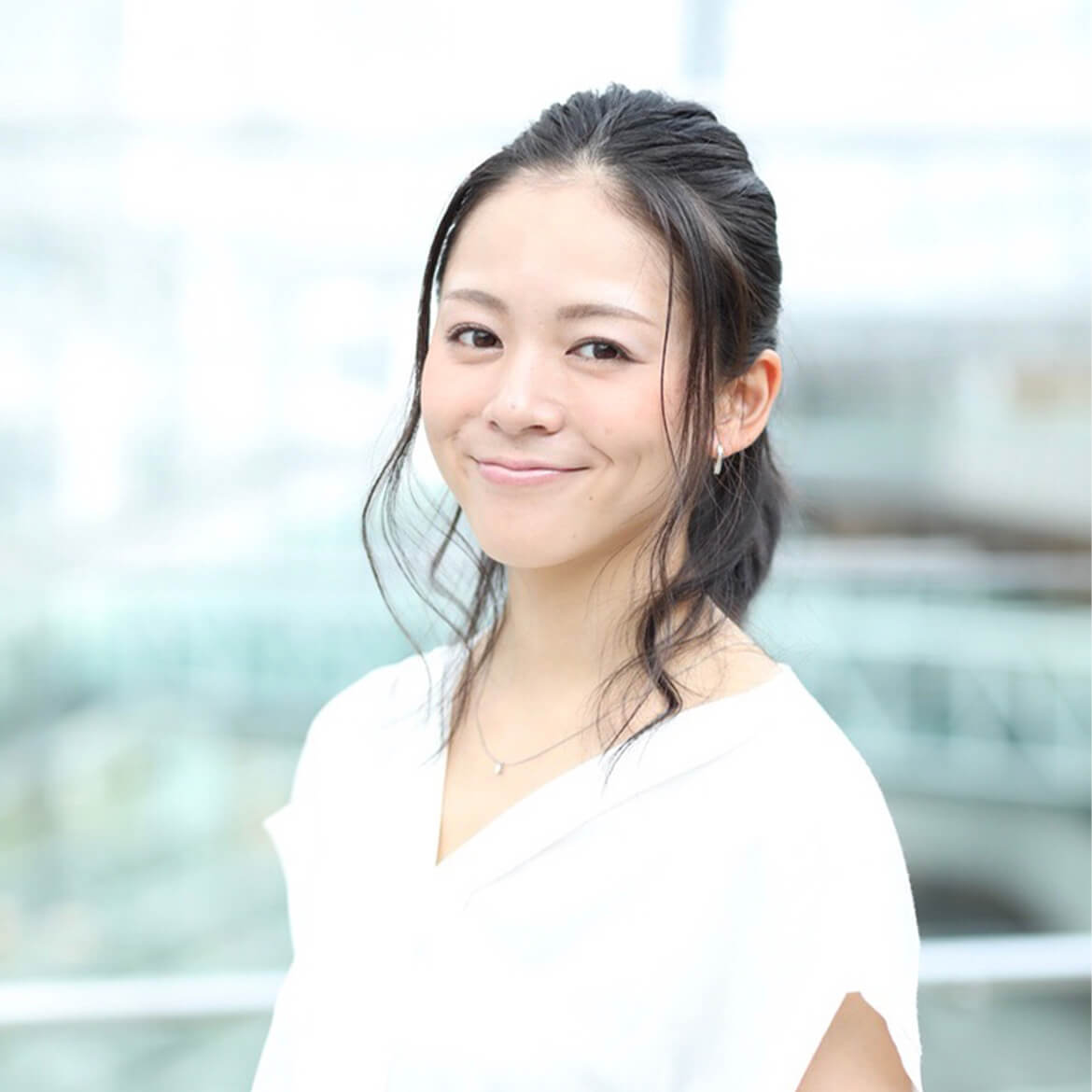
現在、デジタルをビジネスに取り込むことで生まれる価値について研究中。IoTに関する様々な情報を取材し、皆様にお届けいたします。