東洋ビジネスエンジニアリング(B-EN-G)が主催する、MCFrame Day 2016で、製造業を中心に、生産管理や品質管理のコンサルテーションを行い、「スマートファクトリー」という考え方を提唱している、エイムネクストの清氏のお話を伺った。
【登壇者】
エイムネクスト株式会社 代表取締役 清 威人 氏
IoTはツールなので、本来の目的ではない。日本の製造業の課題は、
- 新興国メーカーに対して、どうコスト・品質において競争優位性を確保するか
- 世界中に広がる生産拠点、顧客をどうマネジメントしていくのか
- ハードウエアからサービスへのシフトの中で、生き残りのためにどういうふうにビジネスモデルを変えるか
なのだという。
製造の現場において、IoTを活用することで、「人の能力を超えた数や種類、粒度などのこと」「プロセスや組織の壁今の状態に至るまでの情報」「時間の壁」を可視化することが可能になるのだという。
ものづくりにおける日本の優位性は、「飽くなき改善活動」につきる。これが日本の企業の独特の文化であり、強みだとも言える。
清氏は、Industory4.0が提唱される以前の、2008年ころから「スマートファクトリー」という考え方に着手している。スマートファクトリーでは、従来の工場でバラバラになっていた関連性を、保持しながらデータを蓄積していくことができるというのだ。これまで、様々なデータと基幹システムと接続し、リアルタイムで処理するもの、統計分析するものをやってきたということだ。
今回の公演では、「生産性をあげるための5つのアイデア」と「データに基づく改善機会の発見」が、スマートファクトリーを使った例を用いて紹介された。
チョコ停を計測することで生産性向上を見直す
工場内の工程において、ちょこっと停止するという、いわゆる「チョコ停」が発生するケースが多い一方で、チョコ停による総停止時間はといった情報はキチンと測定されていない場合が多い。
厳密に測定した想定し時間と従来マネージメントが把握していたチョコ停の時間と比較すると、10倍の時間がチョコ停していたことがわかったというのだ。しかし、総時間に関する数字がないため、ここを削減する活動がきちんとできていないという状況だったというのだ。
一方で、多大な電力を消費するコンプレッサーの利用状況を見てみると、本来停止していてよい、夜間や休日もコンプレッサーが動いているというケースがあり、エア漏れのため、年間で1億円の電気代のうち500万円(全体の5%)が無駄に使われていたというのだ。こういった無駄を省かない一方で、この企業では生産性向上の活動を激しくやっているのだ。
こういった、全体の可視化や無駄の発見にスマートファクトリーは役立っているのだ。
個別データによるマネージメント
マネージメントは統計データのみに基づいて、改善について議論する傾向がある。しかし、本当は個別のデータにも目を向けるべきだと清氏は述べる。
なぜなら、例えば「不良率x%」という大雑把な情報だけでは手が打てないからだ。不良率の原因が、特定の機械なのか、部品の特定ロットなのか、という原因自体が明確でないまま、報告だけされるケースが多いからなのだという。
たとえば、レポート上で「25%の不良率」といわれると「4個に1個の不良」ということしかわからない。そういう時は、個別のデータを具体的に見ると規則性があることがわかる場合があるということだ。スマートファクトリーでは、「不良発生時刻」「不良が発生したのが特定の設備なのか」といった情報を、時系列でドリルダウンすることができるので、こういった規則性が見られるデータの可視化が可能となるということだ。
マニュアル作成などの間接業務時間(コスト)の削減
間接業務の時間コストにも目を向けてみよう。生産現場では帳票作成が問題になっている。その一方で、膨大な帳票をつくったからといって役に立つわけではない。
工場全体で作成している帳票は1,000種類以上にも上ると、このことだけで製品原価の中の人件費割合は多くなる。一方で、この膨大な資料を作成するのに、たった数10のオリジナルデータを加工していうケースも多いというのだ。
ここを共有するだけで、無駄な関節業務時間は削減するのだという。
キャッシュフローによる改善評価
また、スマートファクトリーはROAの改善にも寄与する。
工場のラインで、従来30秒かかっていたのを20秒にするという改善計画をよく聞く。しかし、あるラインを10秒短縮したとしても、中間在庫におかれている時間は実は10秒以上増えているというケースもあるというのだ。これでは、短縮した意味がない。
そこで、部分的な改善より、改善効果のトータルを考えて自社の利益を評価すべきだという。
その利益指標は、以下の指標を使うとよいと述べた。
Jコスト= コスト x 期間
とする。この「Jコスト」という指標を使うことで、現場改善でやったことが、ROAの改善に直結することができるのだ。
Jコストをはじき出すうえで、工場にセンサーを設置することで、「何時何分に、なにが、どの工程を通過したか」ということが取得できる。つまり、製造工程のどこに、どんな時間をかけている時間を可視化することができ、かつそれがROA改善にどう影響するかがわかるというのだ。
管理モデルの自動化
改善活動のなかで、PDCAをまわすという話がでることは多い。一方で、課題を発見すると、ドキュメントに落すことで満足してしまうことも多い。そこで、課題の解決策をすぐにシステムに組み込むようにするのだ。その結果、改善の結果をすぐ見ることができるので、PDCAをどんどんまわすことができ、データの相関を見ることで、いろんな管理モデルも構築できるということだ。
これも、人間でやるのは不可能で、システムがやることが重要なのだという。
スマートファクトリー導入事例
スマートファクトリーがつくる、改善のための5つのアイデアは、これまで見てきたとおりだが、実際にこのシステムを自動車部品の工場にいれたところ、導入後9ヶ月で生産性が13%向上したということだ。システムによって様々なデータが可視化できたことで、生産性の向上に繋がったからだ。
さらに、この部品工場では、この改善活動を行ったことで、欧米のメーカーとの取引が増えたのだ。なぜなら、欧米メーカーは日本の企業と付き合うと、何を聞いても応対時間がかかる、この時間のロスが、実は発注機会も失っていたのだ。しかし、データがシステムに格納されたことで、回答までの時間のロスもなくなり、信頼関係が構築できてきたということだ。
この例でみると、スマートファクトリーによるメリットはかなり大きいといえる。
生産管理とIoT
一般的に、様々なデータが取得できていないにもかかわらず、データありきだけでモノをみようとしがちだ。しかし、データを眺めていても解決しない場合は、前提条件自体も見直すことが重要だ。たとえ、システムを導入して、改善項目がみれたとしても、他人事だとおもってしまうと、結局改善はされない。
また、データの分析と形式を他社に依頼するというのはよくない。分析こそ自社で行い、自分たちのノウハウとしていくことが重要だという。
基幹システムと連繋をしたり、取得したデータについて、部門を超えた業務連繋への活用で効率化ができるのだと述べた。
※エイムネクストでは、SMART FACTORY LABというSmart Factoryのデモを2時間くらいで見ることができるということだ。
【関連リンク】
無料メルマガ会員に登録しませんか?
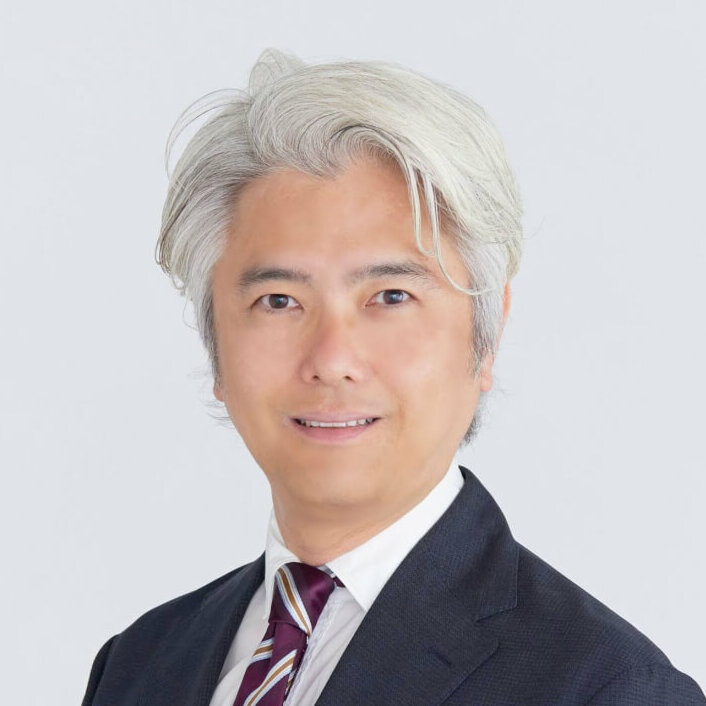
IoTNEWS代表
1973年生まれ。株式会社アールジーン代表取締役。
フジテレビ Live News α コメンテーター。J-WAVE TOKYO MORNING RADIO 記事解説。など。
大阪大学でニューロコンピューティングを学び、アクセンチュアなどのグローバルコンサルティングファームより現職。
著書に、「2時間でわかる図解IoTビジネス入門(あさ出版)」「顧客ともっとつながる(日経BP)」、YouTubeチャンネルに「小泉耕二の未来大学」がある。