多くの中小工場では、手作業により一品モノが作られていて、いわゆる生産ラインのようなものはない。
そんな工場におけるDXを考えるとき、「手作業が多い中で、デジタル技術をどういうふうに導入したらよいのかわからない」、あるいは、「デジタル技術は自社に関係がない」と考える経営者も多い。
実際、今回取材した「DX工場」がある広島県の調査によると、広島県内製造業のうち、従業員数が100人以上の企業はわずか4%だという。そして、8割の企業がDXというキーワードを認識しておらず、認識していても、実際にデジタル活用をしている企業は25%なのだという。
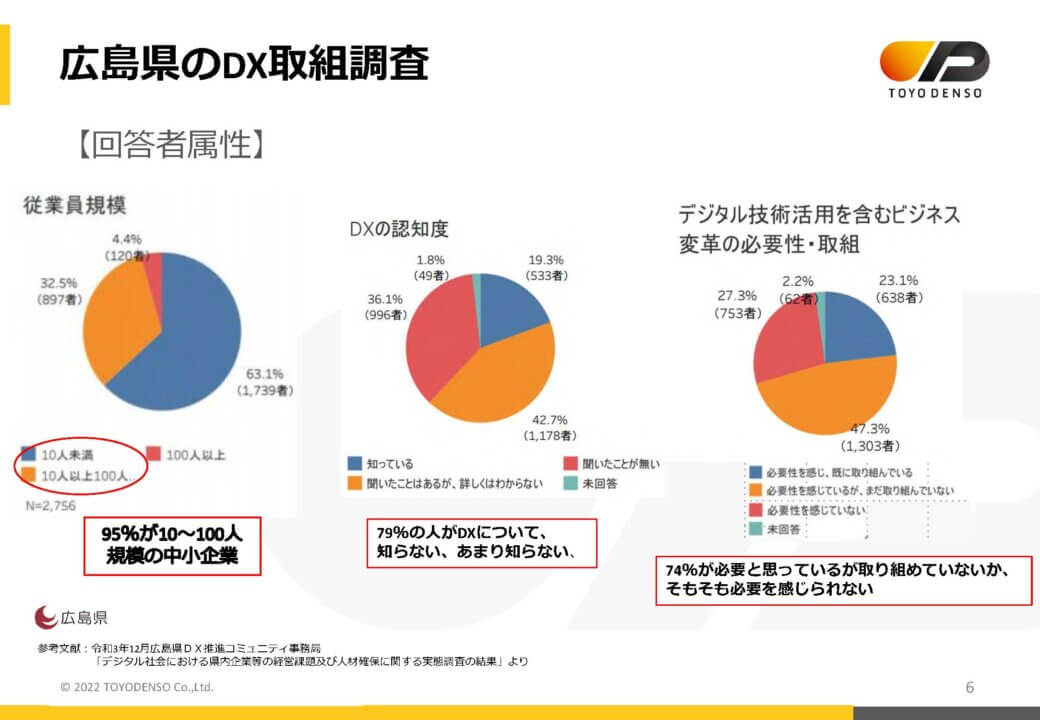
つまり、大半の中小製造業がDXを認識していないか、していてもデジタルを活用していないことになる。
こんな環境下で、広島にある、制御盤のメーカーである東洋電装は、この度、可部(広島市安佐北区)に「DX工場」をオープンした。
東洋電装の代表取締役 桑原弘明氏(トップ画)は、「中小工場では、エンジニアが最高の仕事ができる場所出ないといけない」という。そのためにDXは必要と考えていて、今回のDX工場を、中小製造業におけるDXの推進拠点と位置付け、製品やサービス、業務のテストフィールドとして活用したいと考えているのだ。
「自社が事例を公開することで中小製造業におけるDXのロールモデルとなり、本来得意とするきめ細やかさやすり合わせ、改善精神といった能力が最大限発揮される場を作りたい、一緒にDX推進をしたいと考えるパートナー企業とも行動を共にしたい」と述べた。
東洋電装の考える中小製造業のDXとは
製造業においては、エンジニアの技術習得が必須なわけだが、東洋電装は現状、誰でもできる仕事も、高度な技術を有するエンジニアにしかできない仕事も、同じエンジニアがやっているという実態がある。
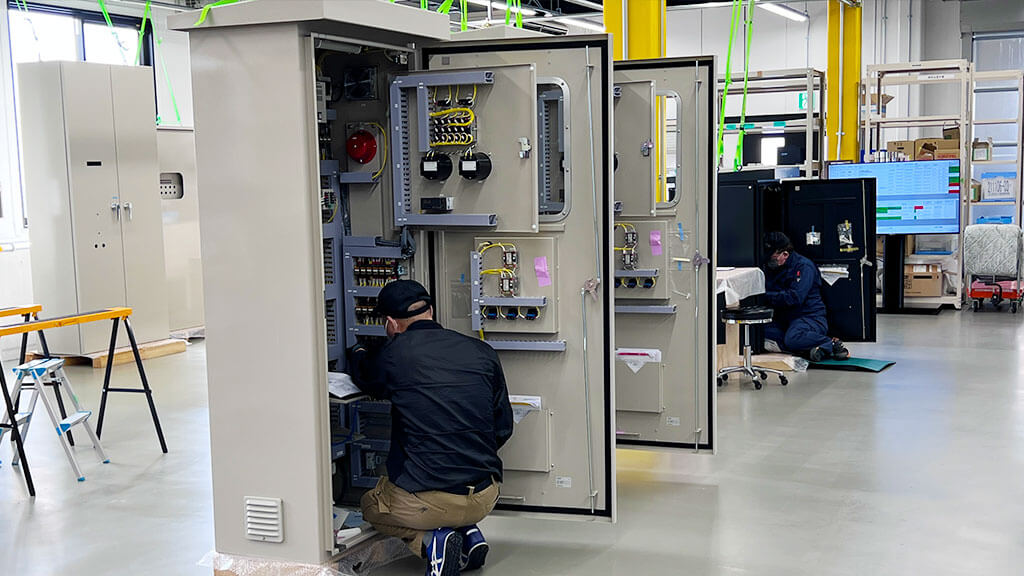
また、設計図面や製造ノウハウを共有する資料などはすべて紙ベース、製造時は高度な技術を有するエンジニアが現場で工夫を凝らして、図面にないものを付け加えながら良品を作っているという状況だ。
そこで、ある程度の技術力があればできる仕事と、高度な技術を有するエンジニアでしかできない仕事を区別し、「誰でもできる仕事は段階的にロボットなど自動化技術を活用し、なるべく人でないとできない仕事だけを人が行う生産ができないか」と考えたのだ。
しかし、一品一様のものづくりを行う現場では、大量生産の効率性をもって製造するのは困難だ。
そこで、東洋電装は、広島工業大学 情報学部 情報工学科 濱崎俊彦教授と共に、「少量品の連続的生産技術」と「安定的な価値創造」を、制御盤の製造においてどう実現するか、つまり、中小工場における「マスカスタマイゼーション」をどう実現するかについて、実証する目的でDX工場を設立したのだという。
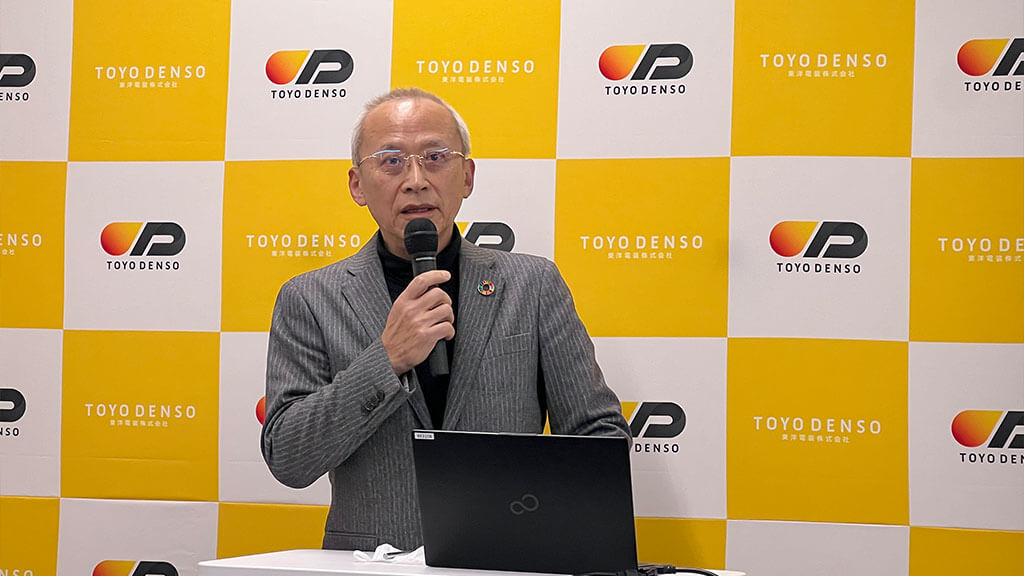
東洋電装は、制御盤の製造以外にも、通信やITサービスなど、多岐にわたっているので、詳しくは以前の取材記事を参照してほしい。
製造現場のデジタル化とマスカスタマイゼーション
中小製造業のDXに向けたアプローチ
まず、マスカスタマイゼーションを実現するために行ったことは、バリューチェーンの整理だ。
「営業」「設計」「購買」「製造」「検査」という、製造業における各プロセスについて、「何を用いるのか?(何が必要なのか?)」「誰が関わるのか?」「どう実現するのか?」「どう達成するのか?」ということを整理していく。
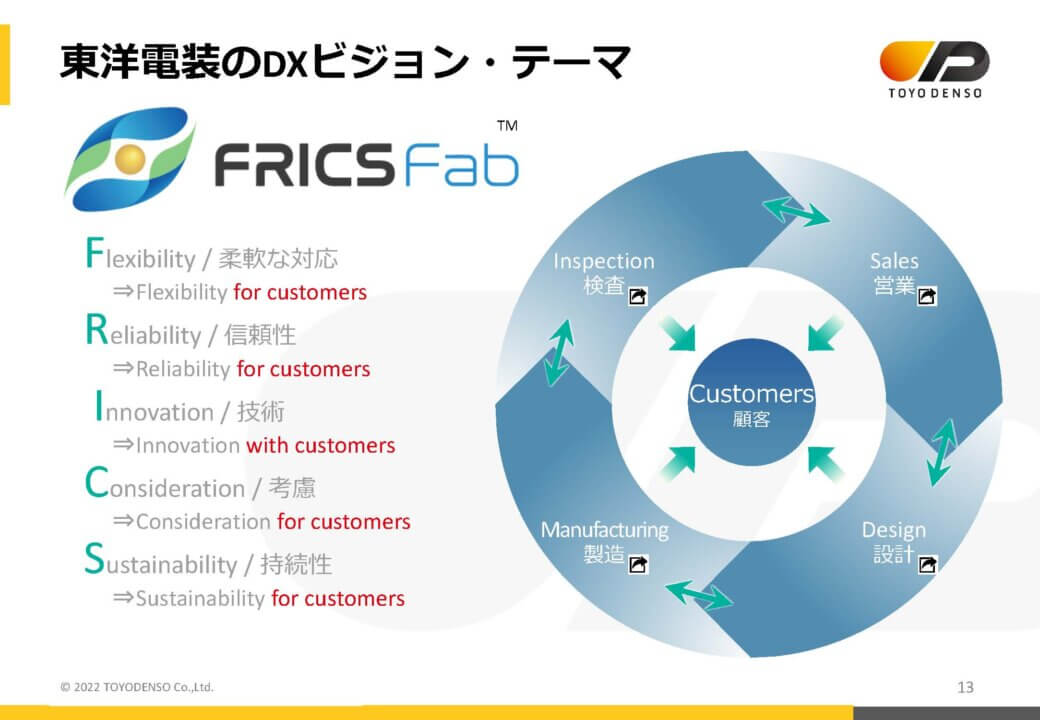
そして、それぞれのプロセスにおいて、デジタルでできることを緻密に検討し、具体的なデジタル技術を導入していくという考え方だ。
例えば、「製造」のプロセスについて、東洋電装の制御盤の製造においては、「加工」、「組み立て」、「配線」という3つの作業からなる。
このそれぞれの作業について、工場内のカメラで作業者の動きを録画したり、生産管理システムなどを活用して、作業状況を取得したりする。
そして、課題を発見し、業務を効率化していくというアプローチだ。
東洋電装の生産現場で行われたデジタル化
東洋電装では、まず、生産管理システムが導入されたことで、発注情報や設計データなどが一箇所で管理されるようになり、作業進捗も管理できるようになったのだという。そして、作業上必要な手順書などもすべて電子化された。その結果、工場の中のPCで作業者は必要な情報をすべて閲覧することができるようになったのだ。
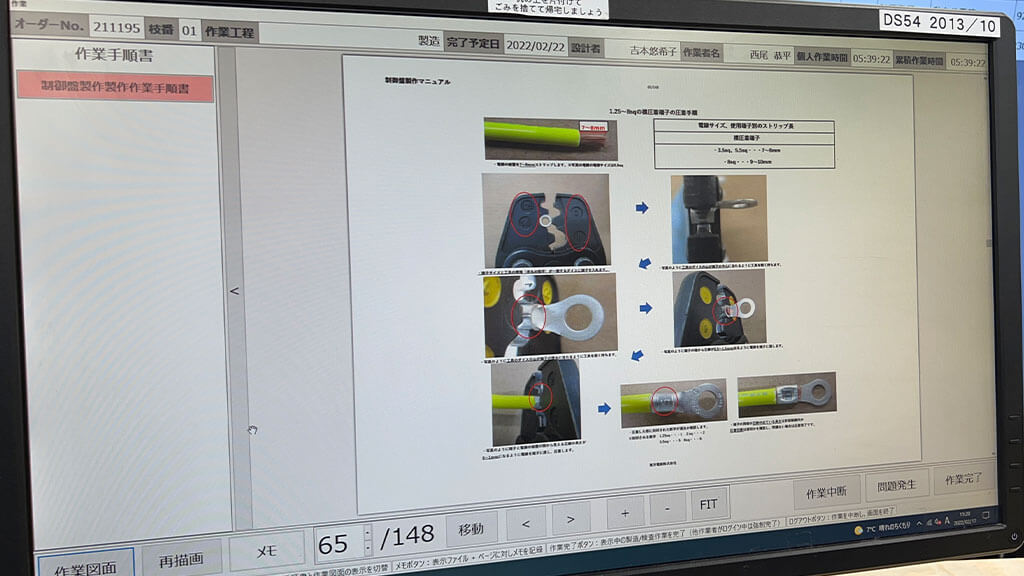
これまでは、すべて紙で設計データが配られ、それを見ながらキングファイルにある手順書を調べ作業をする。作業時間も曖昧に記録していたわけだが、そういったアナログ作業をすべてデジタルに切り替えたのだ。
実際、工場の中には、ほとんど紙類がなく、例えば図面の変更や課題の記録などについても、タブレットが使われていて、そこに直接記入することで、情報の共有もスムーズになっている。
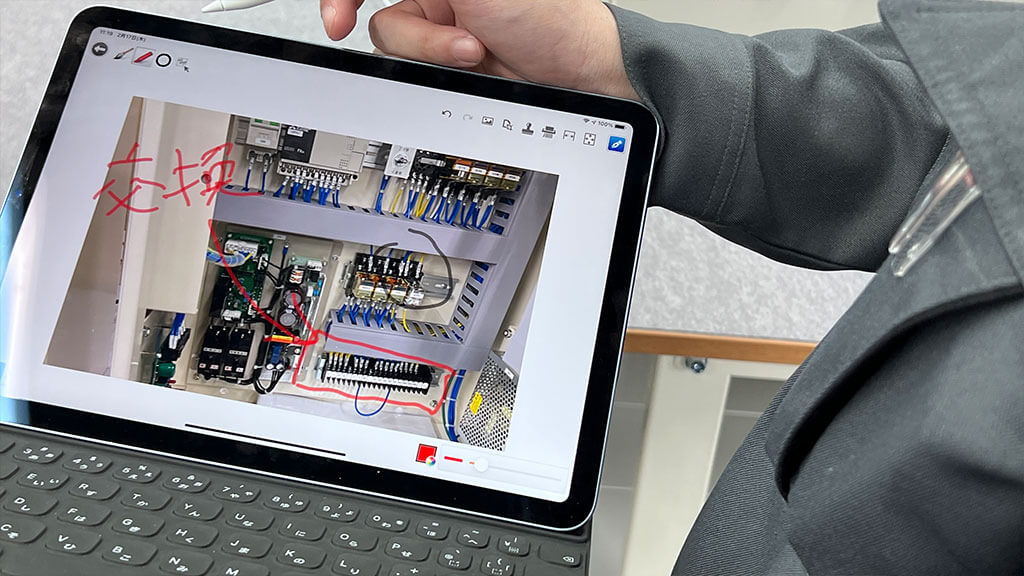
作業の記録に関して、現場のエンジニアにとっては手間が増えるだ。そこで、「現場の抵抗はなかったのか」質問したところ、「初め嫌がるエンジニアもいたが、必要性を理解してもらうことで現在では使いこなしている」ということだった。
実際、作業をしているエンジニアを見ていても、作業場にタブレットを持ち込んで、図面を見ながら作業をしていて、すでに習慣となっていることが見てとれた。
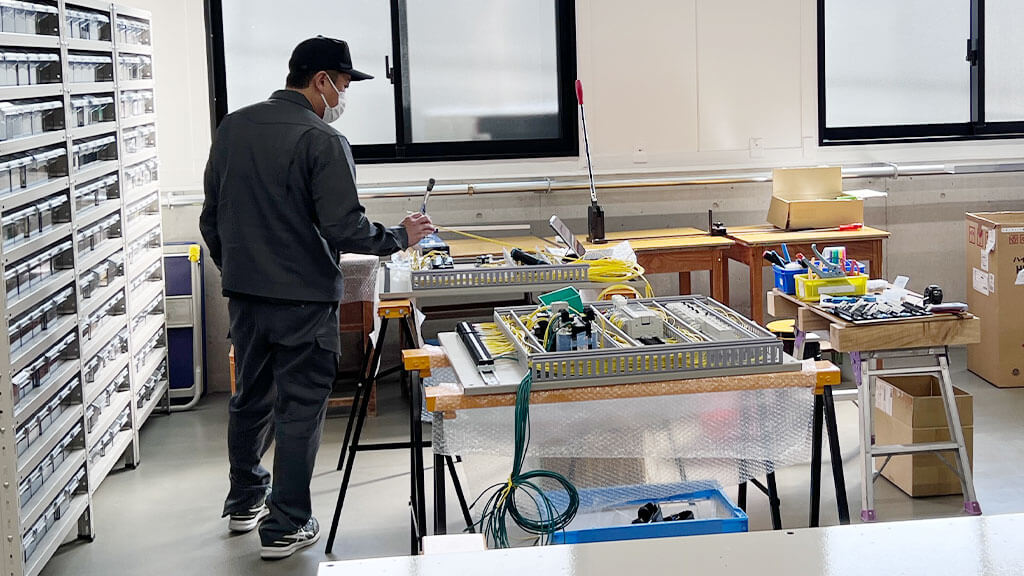
デジタル化によるデータが実現する生産性改善(DX)
このように、手を動かす作業「以外」の部分をデジタル化し、作業状況も記録できるようになると、製品ごとの作業進捗が把握できるようになり、想定していたよりも時間がかかっている作業が何なのか、ということも把握できるようになる。
そして、時間のかかっている作業を特定したら、その作業を行なっていた時間帯について、録画していた作業映像と照らし合わせて、課題を発見するのだという。
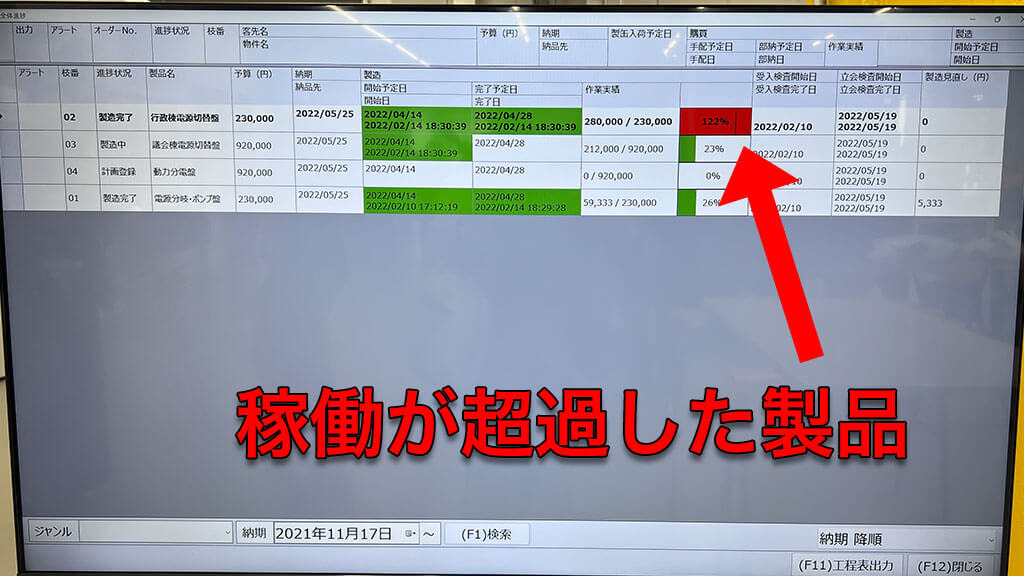
具体的には画像分析のソフトが導入されていて、「作業者の動線」や「作業手順」、「設備の見直し」などを行うのだという。
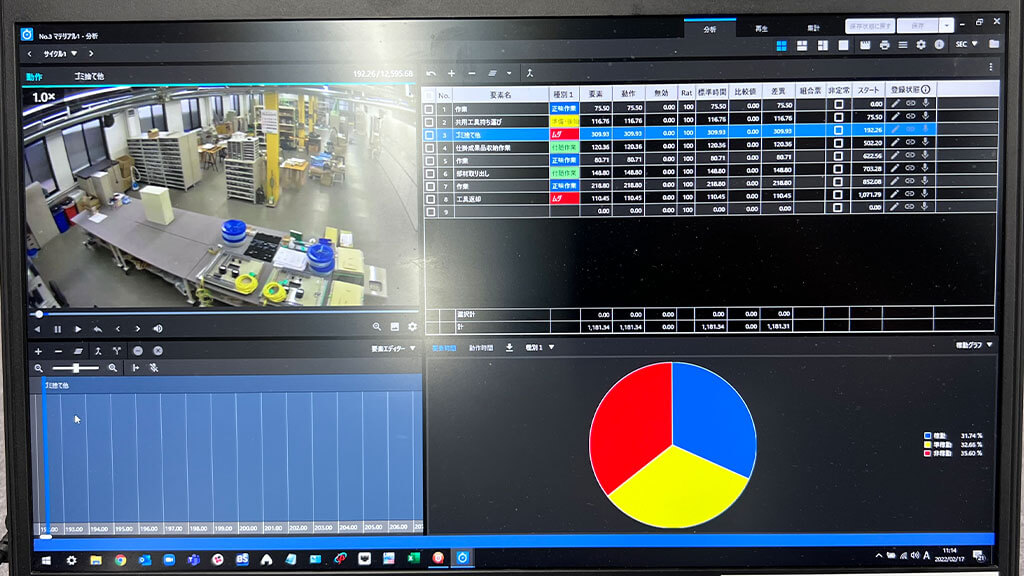
その結果、同様の製品を作る際、35.6%の無駄なコストが削減されたという事例も登場している。
動線解析の例として、工具を格納する場所やゴミ箱が設置された場所が以前は一箇所で、作業ごとに工具を探しに行ったり、ゴミを捨てに行っている時間が無駄であることがわかり、工具をエンジニア個人に配布したり、ゴミ箱を増やすなどすることで、作業効率を上げることに成功したという事例が紹介された。
こういった改善は、この作業者だけを見ると良さそうだが、工具の管理がバラバラになるのではないかという新たな懸念がでる。
そこで、工具にICタグを付け、管理しているというのだ。
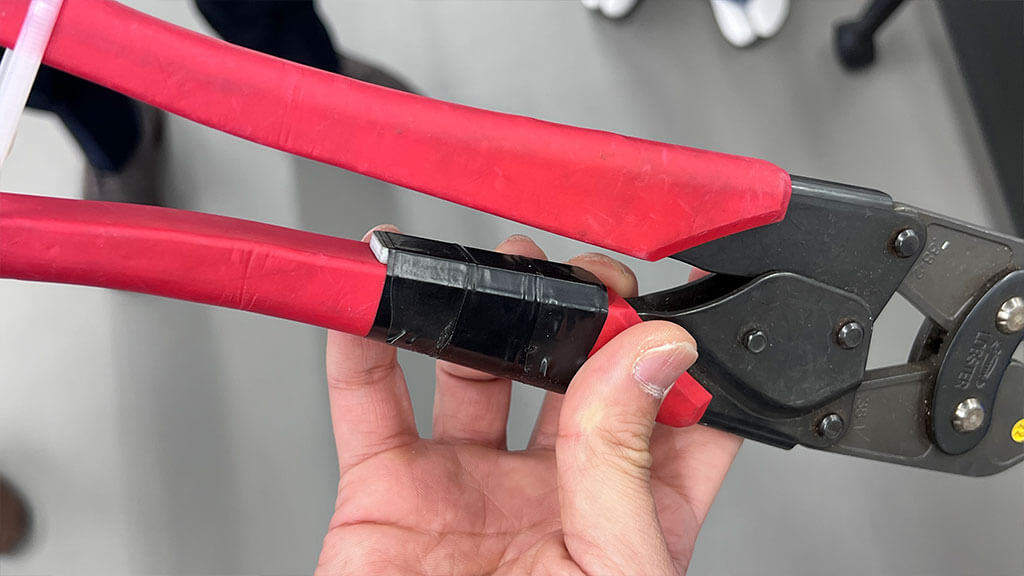
ICタグがついていることで、リーダーを使って、工具入れにある工具の数を瞬時に数えることができるので、工具が元の場所に戻っているという確認ができるように工夫がされていた。
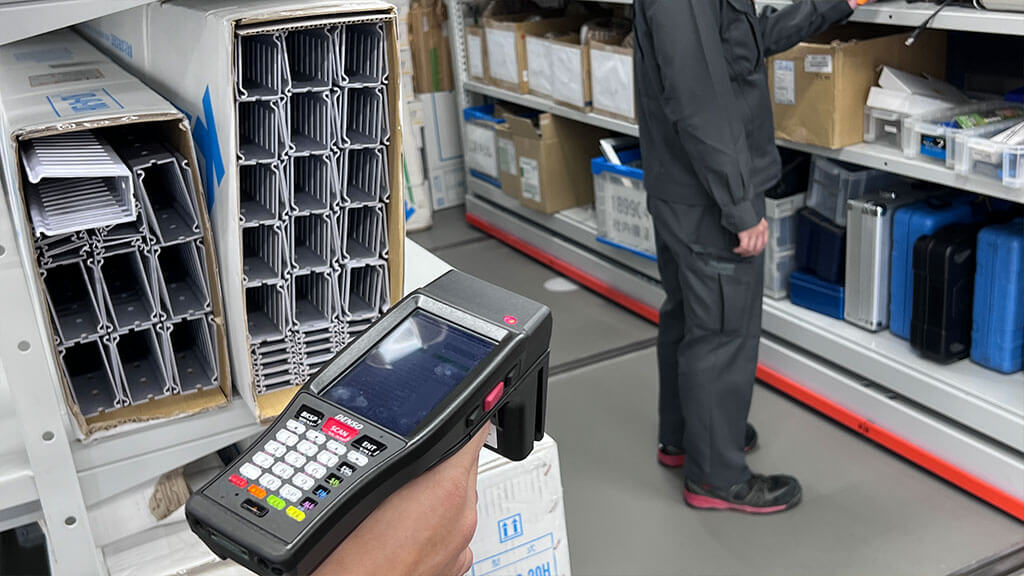
さらに、作業をしていて、あるエンジニアや設計担当などに質問をしたいといった、人の所在が知りたいというケースがある。
そういった場合に対応するため、出退勤システムが工場の入り口に配置されていて、今だれが出勤していて、会議室などどこかにいるのか、在宅勤務をしているのか、など、一目でステータスが分かるようになっているため、人を探す時間の無駄も省かれている。
現在のDXの到達点と今後
東洋電装の制御盤事業部長 越智稔氏は、「こうやって改善がすすんだ結果、その数値を社員内で共有することで、意識改善がおき、デジタル技術による社内改革が起きている。」という。
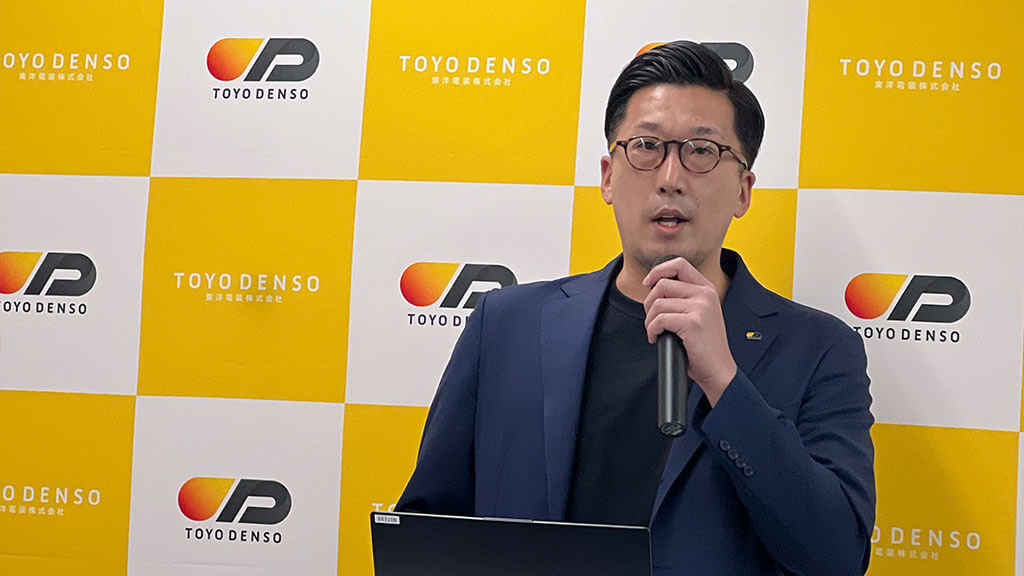
現状は、デジタル活用を推進し、無駄をなくすということが実現できている状況だが、なぜ、いきなりロボットなどの導入を考え、さらなる効率化を目指さなかったのだろう。
これに関して越智氏は、「いきなりロボットを導入するのは、資金力の問題もあるし、システム設計も必要になるというということもあり、社内のリソースを確保できないから」なのだという。
多くの中小工場に置いて、同じ悩みがあることを考えると、現実的な考え方で、参考にしやすいのではないだろうか。
最後に桑原氏は、「DXによって日本の特徴をより際立たせて、世界とたたかえる製造業を作っていきたい。」と述べた。
今回、DX工場を取材して、中小工場にとって、かなり現実的な取り組みだと感じた。全てを真似することができなくても、部分的に取り込むことで、生産性改善や技術伝承の問題にアプローチすることができそうだ。
このDX工場は、希望する方は見学も可能で、3月以降広島県と共同でセミナーも実施していくということだ。
無料メルマガ会員に登録しませんか?
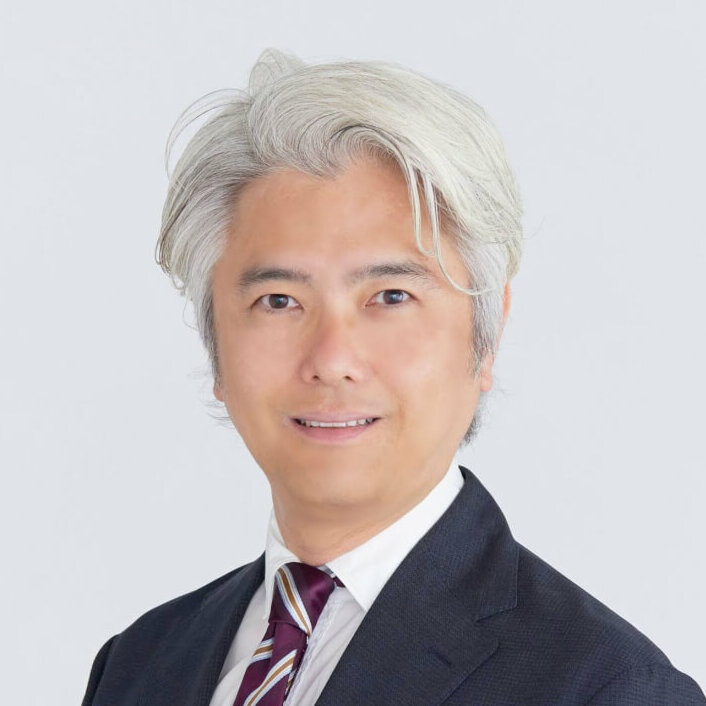
IoTNEWS代表
1973年生まれ。株式会社アールジーン代表取締役。
フジテレビ Live News α コメンテーター。J-WAVE TOKYO MORNING RADIO 記事解説。など。
大阪大学でニューロコンピューティングを学び、アクセンチュアなどのグローバルコンサルティングファームより現職。
著書に、「2時間でわかる図解IoTビジネス入門(あさ出版)」「顧客ともっとつながる(日経BP)」、YouTubeチャンネルに「小泉耕二の未来大学」がある。