FAプロダクツ社は、FAとIT両方のプロフェッショナルが集結し、Smart Factory実現に向けたシステムコンサル、機器の販売、ロボットエンジニアリングを主軸に事業を展開している企業だ。
同社は、製造現場に関わるシステムは上流から下流まで全てワンストップに対応可能だということで、株式会社 FAプロダクツ 貴田 義和氏に話を伺った。
得意分野は、ロボット技術と画像技術
-御社について教えてください。
創業したのが2011年の8月で、従業員数は役員も含めて20名です。われわれは、モノづくりをしている製造業の製造工場をスマートにするために、必要なことを推進していくことを事業の根幹に置います。
スマートファクトリーを実現していく上で、必要なことは大きく2つあります。1つは、設備をより自動化していき、省人化に繋げていく領域です。省人化というと、人を減らすイメージがあるかもしれませんが、活人化です。人間が、より付加価値の高い仕事に従事していくという意味合いになると思います。つまり、ロボット化が1つ大きなファクターになっています。
ロボット、センサー、アクチュエータは、よくテレビに出てくるような製造設備の部分ですが、創業当初は「何でも作ります」ということからスタートしたのです。
もともとキーエンス出身の人間が多く、製造設備に詳しい人間が揃っていたので「何でも作ります」という形で事業はスタートしたものの、より得意ゾーンに特化をしていきました。それが、ロボット技術と、画像技術です。
ロボット化に関しては、20年以上前から多関節のロボットが世に出始めて、自動車業界を中心に導入が進んでいったわけなのですが、なかなかSlerが追いつかないという部分がありました。
例えば、「生産ラインを4人で製造しているが、雇用が難しくなってきたので、1年後には2人で製造できる製造ラインにして欲しい。提案して」と言われるのですが、これが非常に難しいのです。
まず、業務分析して、ロボットをセレクトして、ロボットのレイアウトを考えて、実際にどれぐらいのタクトタイムでモノが作れるのかをシミュレーションして、概算どれぐらいコストがかかるかということと、どのくらいスケジュールがかかるかということを考えます。しかし、それをするだけで2週間かかります。
売れるかどうかもわからない案件で2週間の工数をかけて、その構想を作るかというと、これはなかなか難しい。ですので、当時はけっこう「ロボットなんて」と皆さん避け気味だったのです。
大手の自動車メーカーだけは、生産技術がしっかりしているので「これで作ってくれ」とバシッと仕様書が出てくる状況でした。
しかし例えば、食品業界の包装工程などは、パートタイマーの方を中心に生産をしています。大手自動車メーカーと異なり、専任のエンジニアがおらず、いままでロボットを導入した実績がないので、要件定義がなかなかできません。
実は私たちの活路はそこにあります。
今まで順調に業績を伸ばしてこられたのは、ロボットと画像の領域で、他がやらないことを積極的にやってきたからです。そしたら、結果的に世の中がロボット化へ進みだし、補助金もたくさん付き始めました。
IoTを体現できている工場は、まだ日本にない
もう1つのファクターとして、IoTシステムの導入があります。誤解を恐れずに話をすると、IoTという分野まで踏み込んで、体現できて効果が出ている会社は日本ではほぼありません。実際はIoT化するための元データを現場から取ってくるために、四苦八苦しているのが多くの工場においての今の状態です。
そのような中で、データの収集、取ってきたデータをデータベース化する、モニタリングする、分析できる状態にする、こういったところは、われわれが得意ゾーンとしていたところです。現場の設備のデータを取って、進捗確認をしたいという話は、実は20年以上前からあるのです。
しかし、あまり進んでなかった理由はたった1つ、製造業の生産技術の方たちがITに対して苦手意識があったからです。
データを取ってくるところは、設備の知見がありますが、取ってきたデータをデータベースに取り揃えて、いつでも検索ができるようにするという技術はIT側の知見です。
当時製造業の生産技術の方たちは、IT技術は積極的に活用せず「なんとか機器だけでやりたい」とおっしゃって苦労していました。そこがITを知る私たちの出番でもあり、過去から得意としてきた歴史があります。狙っていたわけではないのですが、Industry4.0と言われ始めてから、ちょうどうまい具合にはまってきたというのが実情です。現在はうまい具合にロボットとIoTシステムというところに特化することで、事業が展開できています。
われわれの強みは、FA業界とIT業界の両方の知見を持っている人間たちが揃っているということです。両側揃っている会社はなかなかありません。
また、私たちは営業活動がすごく得意です。売り方自体も、新しくしていきたいと思っていますので、この売り方を製造業に広めたいという想いもあります。日本の製造業はすごくいいモノを作っていますが、プロモーションが苦手なのです。
日本を含めた世界に情報を発信して、うまく売っていくことを私たちは、実践でやっていきたいという想いがあります。例えば、マルケトと呼ばれるマーケティングオートメーションのプラットフォームを導入し、展示会出展を続けることで、製造業の技術者に頂いた意見や要望、市場ニーズの情報を管理しています。
ホームページやメール配信など、積極的に情報発信を行い「市場ニーズはどこにあるか」を統計的に分析し、サービス開発や提案活動に活用しています。そのような新しいマーケティングや営業の仕組みを社内で取り入れているところも、われわれの強みになっています。
また、パートナー協力も積極的に行っており、特にアドバンテック社、ISID社、シーメンス社、ルネサス社などは特に深く連携をしています。いずれも素晴らしい製品・サービスを持っている会社ですが、いずれもソリューションとして提案しないと売れないという製品特性があり、そのような製品・サービスを持っている企業が私たちにパートナー要請をしていただくケースが多いです。
中小企業向けパッケージの提供をスタート
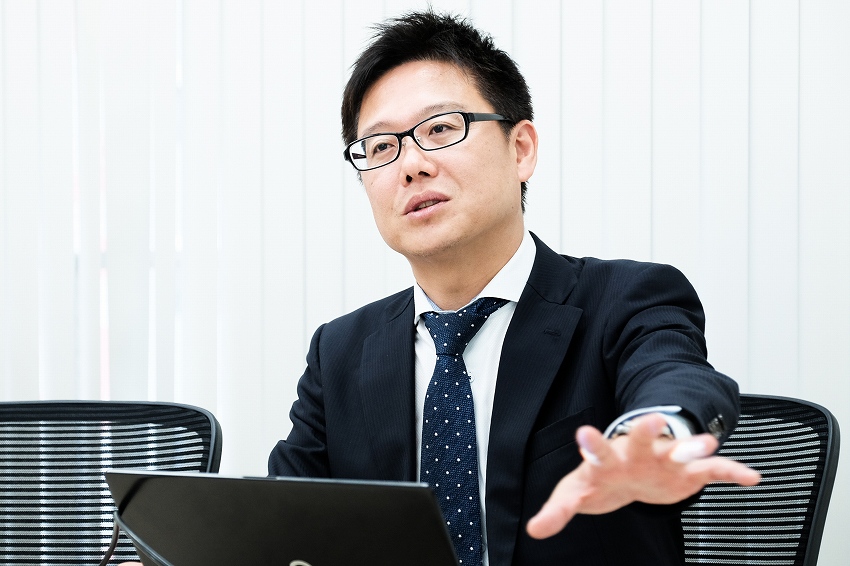
ソリューションサービスについては、ほぼお客さまのオーダーメイドです。
例えば、生産オペレーション管理、品質の管理、在庫の最適化、予兆保全。これを総合的に網羅するような大規模システムを入れたい、データを活用してシミュレーターを導入したい、ある工程にロボットを導入して自動化したいなど、要件が決まっていない案件です。
現在は、さまざまな大手企業で実績を頂いているのですが、中小企業がもっと簡単にこの仕組みを入れられるものを作らないといけないと思っています。
大手自動車メーカーは当然取り組んでいますが、サプライヤーになると途端に取り組みが鈍るのが実情です。
システム導入をしたからといって、いきなり生産量が倍になるわけではないので、予算の問題も出てきます。そうなると、安く簡単に知見がなくてもできるパッケージが必要となっていきます。
そこで、私たちが経験した多くの実績を活かして最大公約数をまとめたパッケージを作っています。設備の稼働分析というパッケージや、生産状況をモニターするパッケージ、予知保全のパッケージなど、非常に安価に提供しております。
過去は自動車業界がメインでしたが、この1年半ぐらいは、電子デバイス業界、家電業界はもちろん三品と呼ばれる食品、薬品、化粧品業界のお客様が増えてきました。今まで取り組んでこなかったけれど、ロボット化に取り組みたいというお客さまが多いです。
技術者の価値を上げたい
われわれが目指すものは、日本の技術者の価値をもっと上げることです。日本は製造大国ですが、大学の理系就職ランキング上位に製造業が登場しないことが問題だと思っています。人気があるのは、大手自動車メーカーの開発部門ぐらいです。
鴻海(ホンハイ)の社長は「自分たちの強みは、台湾で管理し、中国で製造し、アメリカとヨーロッパにモノを売り、製造設備は日本製を使っているところだ」と言っています。
このように、日本の生産技術は1位を走っているにも関わらず、国内では人気がない職業になってしまっています。
もう1つは、今、深刻になっている人材不足です。製造ラインで働いているオペレーターの方たちがもっと働きやすく、スマートにかっこよく、綺麗であまり体の負荷がかからなくて、付加価値の高い仕事ができるようにならないと、全部ITの会社に人材が流れてしまうと思っています。
FA プロダクツ事例
-事例を教えていただけますか?
バラ積みピッキングと言われる技術があります。
まだロボットには頭脳がないので、どこどこの座標にモノを取りにいきなさい、と指示をしなければいけません。しかし、それだとぐちゃぐちゃに積んでしまったり、崩れたりすることが起こっていました。
でも最近は、非常に技術が発達し、カメラとアルゴリズムとロボットとの連携で、うまくモノを取りにいくことが可能になり、コストも下がってきて現場での導入実績も増えてきました。
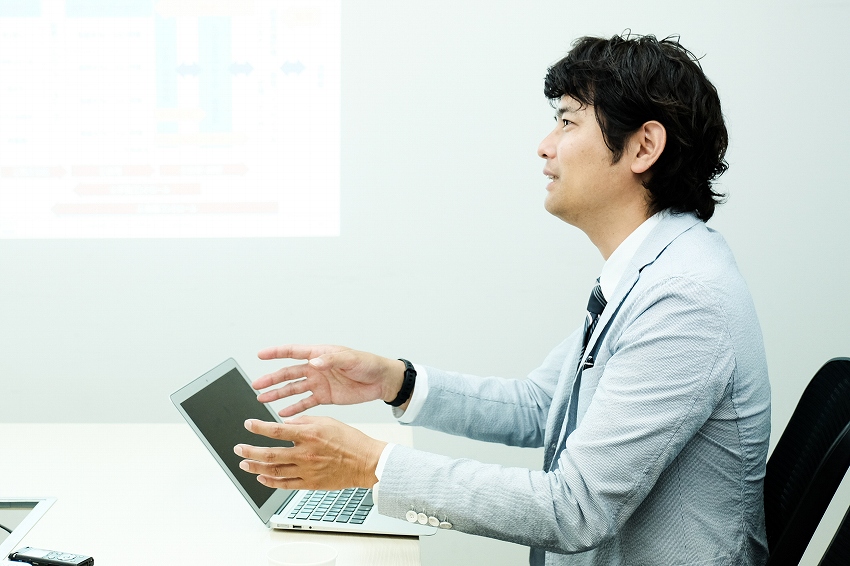
-2年前にディープラーニングや、画像解析の技術が一気に花が開いたときに、展示会ではまだコンセプチュアルな状態でした。
おっしゃる通りですね。例えば、ロボット専業メーカーのカメラの組み合わせでやると、できる用途が非常に限られます。
しかし、私たちは、3次元ビジョンやロボットビジョンといった高精度3次元計測技術をベースとしたソリューションを提供している三次元メディア社とパートナーとして導入を進めさせていただいています。
-導入すると言っても、ただ入れればいいというものでもないでしょうから、このラインのこの場所にロボットを置いてなど、流れてくる製品に対してそのロボットがどのように活動すれば良いか、ということまで含めて、要件定義されるのでしょうか?
おっしゃる通りです。この要件定義がわれわれのノウハウになります。次は、IoTのスマートシステムをご紹介します。
データを収集してモニタリングできる状態にして、分析して、活用するとはよく言われる話なのですが「何をやるの?」というのが、実はほとんどこの4つに集約されています。生産・オペレーション管理、品質管理、在庫管理、保全管理、これを効率化させたいと思っています。
こういったものを分析して、最終的にはAIを使ったり、シミュレーターを使ったりして、その分析結果を経営層にフィードバックし、より効率の良い販売、物流、生産を確立していくことになります。
もう少し具体的な話をしますと、ステップとしては、見える化、活用、分析、解析、手動、自動と流れていくのですが、現状どの企業も、フェーズ2の「活用」ぐらいまでで四苦八苦しているという状態です。
-見える化の話が大半ですよね。
そうなのです。なぜここで詰まるかというと、理由は2つあります。1つは、ここに1番お金がかかるという単純な話です。
この手の話は、生産量がいきなり倍になるわけではありませんし、コストが半分になるわけではありません。しかし、まずは何に効果があるのかを探し出すためにデータを取るという話では、予算が多く付かないのです。
そこに多くの方が四苦八苦していて「あまり予算がないけど、上からはIoTで効果を出せと言われていて、どうしたらいいかわからないから、助けてよ」というのが大半です。そこで、われわれは汎用的でローコストなパッケージサービスを提案しています。
製造現場の人は、見える化して、通り一遍の数値だけで判断されたくない
-いきなりゴールを予知保全だというと、よくわからないと言われるらしいのですが(笑)初めに活動状況、稼働状況のチェックを自動化しませんか?と提案すると、そこからだんだん深堀りしたくなると聞きます。
その通りです。私たちの営業戦略がそれです。いきなり分析して、こういうことをして、こういうKPIを見ると「経営者が喜びますよ」と伝えても、あまり意味がありません。
普段、経験に裏付けされた鋭いカン・コツと絶妙なバランスで製造しているわけですが、それが全部データとして見える化されてしまうとしたら、製造現場の人は嫌なのです。
-嫌なのですね。
そう、そもそも嫌なのです。自分たちのさじ加減がいろいろあるわけです。なぜこれができないんだ?あれができないんだ?と言われても、いろいろあるのですよという話です(笑)
製造現場は、本当にいろいろあるのです。働かない人がいたり、嘘の報告を書く人がいたり、材料費と原価との問題があるので、ちょっと上には隠してなんとか帳尻合わせをしてみたり、特急で作らなきゃいけないものを生産順序の中に割り込ませなきゃいけなかったり。
さまざまなことが起きている中で、通り一遍の設備の稼働率だけ見られて、その設備が止まって、止まる要因分析なんかをされた日には内心「うるせーよ、お前たちは黙ってろ!」という話です、皆さんさすがに声には出しませんが(笑)
職人気質なので、それを突破するのが先程の「稼働状況のチェックの自動化」なのです。
帳票をつけるのは大変です。設備が止まったらちゃんとチェックし、何故止まったか、何時から何分まで止まったか、復旧に何分かかって、誰がそれを対応したか、部品は何を使ったか、それを紙に書いて、1日分をラインリーダーが集めて Excelに打ちます。
各ライン分が生産管理に上がってきて、それを生産管理部門が 1日かけて集計して、2日目に初めて帳票が出てくるのですが、これは効率悪いですよね。しかも、大変です。
今、私たちはある現場にだいぶ入り込んでいますが、現場に帳票レスという言葉を言っただけで「それはいいね」とおっしゃいます。
そうすると、その帳票を見て、「目標の生産数に対して現状どうなっているか見たい」とか「生産数が低い場合の要因を見たい」と広がっていきます。
今は、製造業取り巻く状況が変化していて、工場や、基幹システムの会計側、営業側などが、しっかりデータで結び付いていかないと、これ以上日本の製造業は世界と戦っていけません。品質ではまだトップを走っているとも言われますが、コストやブランド力の面では優位性が揺らいでいます。今後は、より効率化を図り、しっかり生産をマネジメントしていくことが重要です。
そもそも経営者は、全体を最適化するために IoT化に取り組みます。しかし彼らは現場がわかりませんので、生産ラインを可視化し、各システムと連動させることから行う必要があることに気が付いていないケースもあります。
計画に従った生産、稼働状況、コストなどの見える化から始め、次いで需給バランスを鑑みて販売機会を逃さない生産、合理化、省力化に繋げていきます。
もうひとつ実例をお話します。
加工機、工作機械成形機などは、汎用PLC(プログラマブルコントローラ)が入っておらず、ブラックボックス化された専用コントローラで制御されているケースが多くあります。そのためデータを外部に出力しにくいのですが、あるお客様は、なんとかそのデータ取り出して活用したいとのことでした。さらに、作業者の手入力情報である、生産品目、生産数、時間、設備条件、設備の実績データ、環境データも取りたいと。
実はこのお客様だけではなく、10社の相談があったら、9社がこのような内容です。
取ってきたデータは、基本的にはデータベースに入れるか、CSVファイルとして保存しますが、単位時間当たりの出来高や、稼働率、設備データなどをグラフ化したいという要望もあります。
最終的に製造部門としては、生産性の向上や、稼働率のアップに繋げたい。品質部門だったら、品質の安定化に繋げたい。トレーサビリティデータを残したい。保全部門だったら、予防保全から予知保全に変えていきたい。設備の停止時間を削減したい。生産技術部門は、このデータを基に新規ラインを設計するときのデータベースにしたいというオーダーでした。
まずは、この「見える化」からスタートするという話です。これをラインの追加拡張時に順次増やしていくということを実例としてやりたいと思っています。
稼働率が向上すれば、設備の生産性が大きく向上するは当たり前の話です。見える化、ボトルネックの分析が発端となり、改善ポイントの発見や生産性の向上につながり、スループットが上がって設備の利益改善を実現します。
見える化の問題
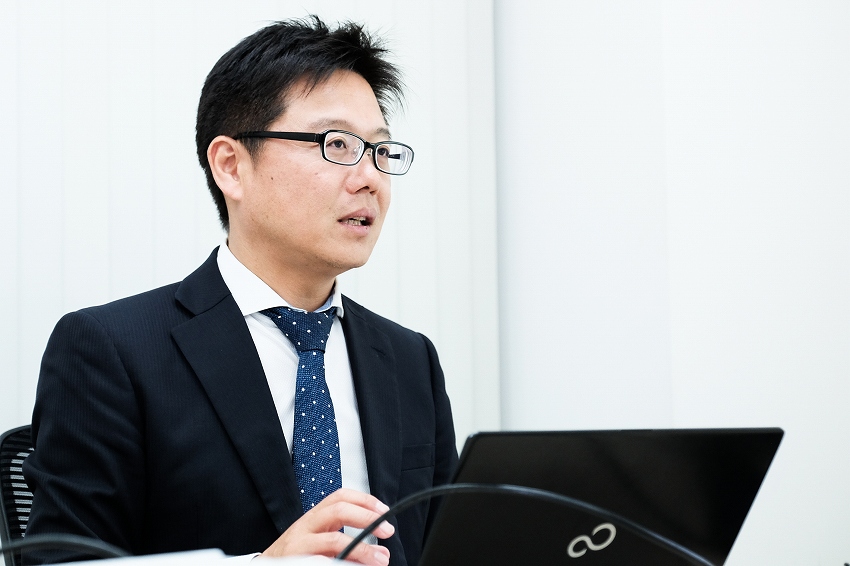
ここまでの見える化に関しては、最近は簡単に導入できるパッケージが出始めてきましたが、ここで今大きな問題が起きています。
「見える化」自体には多くのコストはかけられません。そのため、まずはデータを取るのを優先し、コストがかかるデータベース構築は後回しとなります。しかし、ここに一度綱引きが起きているのです。
データベース構築をせずに行うため、CSVで簡易的にデータを保存する「安いパッケージがあります」と、さまざまな会社がモニタリングパッケージを出しています。
これが実は大きな落とし穴で、そのデータを使って次はグラフ化や分析がしたくなるのです。そうなったときに、「CSVファイルからどうやって、求めるグラフ化をするのですか? 」という話になるのです。
1日1ファイルできていて、それが1000ファイルあるものを、1つ1つ開けて、エクセルで中身をつなぎ合わせれば、グラフ化はできます。しかし、手作業でそれを行うのは現実的ではありません。最近はBIツールでいいものが出ているのですが、データの量が多くなってくると難しくなります。
そうすると、結局データベース構築の話になります。そこでどういうことが起きるかというと、データベースとそのモニタリングシステムのインターフェースを開発しなければいけなくなります。それに対応しているものしか使えないので、今まで入れたものをそっくり入れ替えないといけなくなってしまいます。
これが、一番ミスしている会社が多い実例です。せめて将来的に個々のデータ(レコード)を後で紐づけできるように、データベース構築を見据えたデータ収集をしておけば、CSVファイルでの取得でも後で困らないのですが、経験が無いとなかなかこれが難しい。
-続けられなくなるのですね。
はい、続けられなくなるのです。「見える化まではできた、さぁその見える化を使って、次にどんな分析して、どんな効果に繋げるのか。第2ステップ頑張れよ」と言われた瞬間に止まってしまうことになります。
一歩進むと、詳細分析がしたくなります。例えば、「停止」の要因は計画停止なのか、故障なのか、段取り待ちなのか、設備立ち上がり待ちなのか、チョコ停なのかなどです。
こういったものから時間の稼働率、性能の稼働率を割り出していき、ボトルネックを見つけて、1つ1つ改善していく。そうすると、最終的にはデータベースが必要になってきます。
だから私たちは「必ず必要になるので、最初からデータベースを入れるか、考慮したシステムにしましょう」という提案をします。そうすると、価格で負けるのです。
そこで、スモールスタートできるパッケージ提案をスタートしました。何から始めたらいいのかわからないという方のために、私たちで見るべき項目を挙げ、ひな形の画面も作りました。
コストも抑えました。設備を極力改造したくないというニーズにも対応できます。そして、段階的な導入も可能です。これが一番重要で、最終的には顧客が望むデータベースにノンプログラムで直結できる各種インターフェースを最初から持たせています。
私たちがご提供しているのは、基本の見える化コースと、見せる化コースという2つのパッケージがあります。
パッケージ仕様は汎用的な要望を網羅しています。データ収集、帳票の自動化、画面サンプル、帳票のサンプル、手順書をパッケージにして提供しているため、すぐに導入でき、お客様自身でカスタマイズが簡単に行えます。最小構成で50万円から提供可能です。
「モデルラインのここだけやりたい」という要望から、1ライン全体、複数ラインヘの展開と順を追っての展開が可能で、必要なタイミングでデータベース構築にも対応します。
各社PLCはもちろん、多ようなプロトコルに対応する機器を中心に構成しており、必要に応じてSCADAソフトと組み合わせて活用頂く、汎用的なパッケージになります。
-去年ぐらいまではこのようなパッケージはなかったのですが、今年はたくさん出てきましたね。
確かに各社、自社製品を中心に「見える化」「IoT化」というキーワードでパッケージを提供しはじめています。
当社は系列やメーカーのしがらみがないため、オープンな規格・製品を中心にパッケージを構成しているため、極めて汎用性が高いのが一番の強みです。さらにグローバルに展開しているメーカーと協業していますので、対応機器の豊富さや、OPC UAやMQTTなど、海外では当たり前になっている標準規格を取り入れていることも含め、10年・20年先を見据えたシステムをスモールスタートするためには最適だと自負しています。
-CC-Linkなどフィールドネットワークにはどのように対応するのですか?
CC-Linkに限らず、フィールドネットワークがそこにあるという事は、PLCやPCなどコントローラが必ず存在します。多くのコントローラに対応していますので、ほとんどの場合対応可能です。組み合わせは無限にありますが、あまり問題になることはありませんし、必要な情報は限られていますので、情報が取れないというケースはあまりありません。
-主には、稼働状況を取ってくるということなのですね。
そうです。稼働状況を見える化する事で、第一ステップはほぼ解決します。さらにときどき頂く要望は在庫管理です。工程内在庫の状況が見たい、品質の検査結果の情報を紐づけたいというニーズも次に出てきますが、弊社パッケージシステムはそれらニーズに対応できる様、順次拡張できる仕組みにしています。
そろそろクラウドを使おう
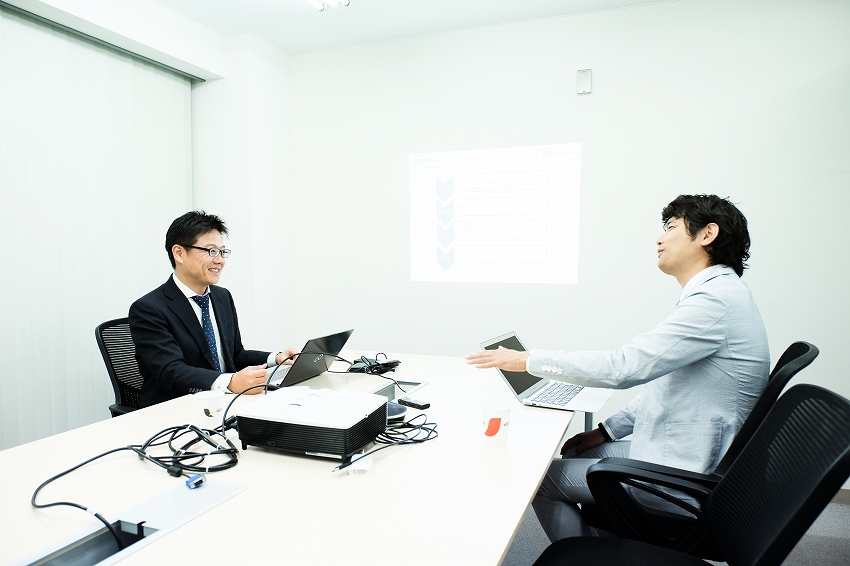
そして、「工場見える化パッケージ」を作りました。拡張版の「見せる化パッケージ」ですと、今度はデータベースを構築し、過去データの検索、工程間情報の連結、上位システムとの連携などさらなる顧客ニーズに対応が可能です。現状はオンプレミス(自社運用)のデータベースで構築する要望が多いですが、そろそろクラウドに移行するタイミングだと考えています。限られたコストの中で、オンプレミスのデータベースを立てていたら、1つもいいことありません。
スピードの問題が解決できるのであれば、AzureやAWSなどクラウドサービスを使うといいと思います。セキュリティを気にする顧客もいらっしゃいますが、現在では銀行の基幹システムがクラウド化されている時代です。むしろ外部攻撃など、セキュリティ対策をクラウドサービス事業者に任せられるので、オンプレのリスクの方が高いとも言えます。
-ほとんどAzureやAWSで解決しますよね。
あとはその検索性や機能の問題だけなのですが、やはりクラウド化に取り組む製造業の企業は多くはありません。
-なぜクラウド化を拒むのでしょうか。
うーん、文化ですね。まだ設備の稼働や在庫を見たいというフェーズなので、取ってくるデータの数がそれほど多くなく、まだPCをサーバーとして運用できるケースが多いということもあります。
1台の設備で取ってくるデータは、異常コードや、いくつかの信号のフラグを取ってくるぐらいなので、バッチで送ればいいのです。オンプレで処理しても十分いいでしょう。
ただこれから先、品質に関わるようなデータ収集が主流になって、予知保全が主流になってくると、リアルタイムのデータをずっと取り続けなきゃいけないという話になってきます。
センサーのデータを、例えば500msごとに収集して傾向値を見つけるという話になってきた瞬間にもうパンクです。そうなると、データ量や処理能力を柔軟に運用できるクラウドを使うことになるわけですから、そろそろやろうよという準備をしています。
-そこに進もうとすると、エッジ側でそれを処理する産業用PCが必要でしょうか。
そうですね。産業用のPCもコストを含めて入手が容易になってきました。特に、世界シェア1位のアドバンテック社の製品は、FA現場で使いやすいようにDINレールに取り付けできて、拡張ユニットも容易に増設できるなど、見た目や使い勝手がPLCと同じものもあります。
生産現場での運用を想定していますので、小型で、耐久性、耐熱性が非常に高いです。今はマルチコアのCPUを使い、Windowsなどの汎用OSと制御用のリアルタイムOSを分けて制御することが当たり前になりましたので、信頼性を疑う必要はありません。
設備のメイン制御をPCが担うことも欧米では主流ですが、日本ではPLC文化が強く残り、メーカーの力も強いため、まだまだ移行には時間がかかりそうです。しかし日本でも現場から収集したデータをバッファしたり、モニタリング画面を作って、そのデータを例えばクラウドに上げたりという用途では生産現場でのPCの活用もこなれてきています。
ただ気になるのは、クラウドのプラットフォームを提供している会社が、もともとFAを知らないところです。現場を知らないまま、技術ありきで開発に取り組んでいるので、どこかで本当にFAの詳しいところと組まないと導入がどんどん遅くなっていくと危惧しています。
-それこそ基本パッケージはないですよね。平たいデータベースと処理能力がすごくいいサーバーはあります(笑)
製造工場が見たい内容や、分析したい内容の演算方法など様々あるのですが、その知見がいる人が開発しないと、使ってみたけど使えないという話になってしまいます。そこはマイクロソフト社が一番近いところに今いるので、僭越ながら頑張っていただきたいと思います。
-基本パッケージは、どのくらい導入されているのでしょうか。
正式にはこの春から売り始めているので、今はまだ数社で、自動車業界が多いです。われわれの提案先の中心は、一次・二次サプライヤーで、売上規模で見ると100億~1千億ぐらいの企業です。
-製造業は、動き始めてからの瞬発力がすごいですよね。
早いです。ある会社の事例なのですが、加工工程の情報と電力量をモニターして、稼働監視のデータをデータベースに溜めて、稼働分析をしたいということでした。いったんは、モデルになっている加工工程はOPCサーバーを使うことで、ある程度データを取ってくることができます。
ただOPCサーバーの設定だったり、プログラミングだったり、都度加工工程を制御しているPLCのラダープログラムの中身を分析しないとできないので、すごく立ち上げに時間がかかります。これをなんとかしたいという話になりました。
また、あるお客様がファナックのMT-LINKiを採用したいので、君たちのシステムにMT-LINKiでデータを取って入れたいということがありました。しかし実はこれ「i」と書いてある通り、iシリーズと呼ばれる加工機しか取れないのです。今現場に460の設備があるけど、何一つiシリーズがないので、これはできないなという話になっています。
今度アドバンテック社がWeb AccessCNCというのを出して、工作機械のデータが取れるようになります。これもまだファナックのiシリーズと、一部三菱の工作機械とハイデンハインの工作機械などに対応していて、これからオークマにも対応し、どんどん広げていく予定です。
それでもデータが取れないものは、もうI/O(接点入出力)で取ってくるしかない。そうなると「Raspberry Piでも置いて、入力して、パソコンの画面にちょっとVBいじれる人が画面作ってあげたら、安くできるんじゃない?」とお客様はおっしゃっていました。
今はいいですよ、でもRaspberry Piは産業用ではないので、すぐ壊れる可能性があります。ですから私たちは、「もうちょっといいものを使いましょうよ、画面もタッチパネルにしたらいいかもしれませんよ」というご提案をしています。
私たちは、現場が使いやすいパッケージや、プラットフォームを作っていきたいと思っています。
-その感触としては、今年からできるようになってきたのでしょうか? 去年からできていたのでしょうか?特に、既存設備に対するデータの収集は簡単ではなかった気がします。
そういう意味で言うと、あまり変わっていません。結局PLCが付いていればデータは取れるのです。工作機械も新しければ取ることができます。要は、最近の工作機械はデータを出そうという気はありますが、それ以外の機器(古い工作機械、PLCが入っていない装置)からのデータ取集が大変なのです。
加工ラインの稼働分析をしたいというニーズが高いのですが、古い設備が多いので、信号が取りづらいわけです。積層信号灯からデータ取得するシステムも普及してきていますが、そこから収集できるデータは限られています。今年も去年も、「取れないものをどう取ってくるか」、皆さんそこに苦しんで悩んでいるのですが、まだ解が出ていません。
-電極をパチンと挟んで、信号線に流れる電流値を見ながらデータをデジタル化することやっている人たちがいて、すごくアナログだけど、すごくいいなと思っています。
確かに、それはすごくいいのですが、そこから先の取得したデータの処理が重要だと考えています。
-御社みたいな会社がまとめていくといいですよね。
ありがとうございます。そういう企業が、どんどん出てきて、それぞれさまざまな部品が自己主張してくれるような形になってくればくるほど、もっと進んでいくと思います。ただまだ、少し出始めてきたかなという感じです。
信号線からの信号取得をどうしてもやりたいというお客様がいると、私たちでボックスを作って、無線機付けて、I/Oを拾ってきて、中を分析して取ってくるということをやります。
組立系のラインは全部PLCが付いているので、三菱でもオムロンでもキーエンスでも、どこのPLCが付いていようが、簡単にデータは収集できるので、そういう意味では楽です。それは去年も今年も同じです。
私たちがご提供しているような、パッケージ商品の数が増えてきましたが、その次の展開までしっかり考慮し、慎重に選定してほしいと思っています。
可視化だけできても、効果は薄い
-結局、なぜデータを取らなければいけないのか、なぜクラウドに繋がなければいけないのか、その「なぜ」の部分があまりわかっていないまま、可視化しなければいけない、止めちゃいけないという、そんな話が先行しすぎていると感じています。
可視化だけできても効果は薄いです。可視化ができれば、データが取れているということです。そのデータは後で誰かが料理してくれるだろう、という感覚で現場は導入しようとしています。動くのは、情報システムと生産技術です。
情報システムは現場がわからないので「どんな形式の、どんなデータを上げてもらえるの?」と言うし。生産技術は情報システムがわからないので「CSVで良ければ、置いとくか」と。
この2つの部署は、昔からすごく仲が悪い場合が多く、話が前に進みません。「じゃあ、もうあいつら放っておいて、いったんデータまで取っておいて、データは取ったからって言える状態にしておこう」という話になりがちです。
何にも話が噛み合わないです。そうなったらどういうことが起きるかというと、大義名分がないので、予算がつきません。
そうすると、保全費の余りや、生産技術費の余りなどで、やる気のある人がなんとか予算を取ってきて「300万でちょっと1ライン見てみたい」という無理難題が始まるのです。
そうなると、安いパッケージを持っているSCADAソフトが選ばれますが、入れたはいいけど、ライン展開しようとしたときに結局またイチから選び直すことが起きているというのが現状です。
-失敗例も積みあがってくると、成功例を持った提案が勝つようになってくるので、今は出入り業者が強くなるのは仕方がないかもしれません。
そうですね。この業界が、IT業界とは決定的に違うのが、失敗例や成功例が共有されないので、いつになっても皆が同じ失敗をどの会社も繰り返すところです。
-ちょっと偉そうですが、われわれがその役目をしたいなと思っています。本来見えなきゃいけなかったことが、別に隠したかったわけでもなく、単に公になる場がなかっただけだと思うのですが、やっとこのIoTという言葉によって、皆さんが公にしたくなってきたというか、知る場ができてきたのだと思っています。
私たちは、年1回開催している大規模セミナー「スマートファクトリー・セミナー」を9月に実施しています。今年で3回目ですが、一昨年と去年の反響の違いがすごかったです。一昨年は集客に苦労しましたが、去年はメール配信だけでほとんど集客せずに席が埋まりましたので、今年はもっと増えると思います。
参加頂いた方は導入の際、何に苦労して、導入してどんな効果があって、終わったあと何に苦労しているか、という事例を知りたがっています。
-見える化をして、予知保全、予兆保全まで具体的に語れる人たちって案外いらっしゃらないので、聞きたいですね。
予知保全の機能を1つ1つの設備に全部に入れるために「現場のPLCを全部無くし、全部PCに置き換える」という会社もあります。
-でも、生産設備メーカーが予知保全のパッケージを入れて、データをオープン化して、会員登録をしている人が見ることができるといいなと思っています。その時のデータフォーマットがある程度決まってないと、情報収集したときに、工場のライン側が困るのではないかと思っています。
そもそも、予知保全が必要で故障検出が必要な機器はけっこう限られるので、何でもかんでも予知保全する必要はありません。しかし、内部のデータを決まった形式で簡単に吐き出す機能を付けてあげたらいいですよね。装置メーカー主導でPC制御を進めるといいのかもしれません。
-例えば、パソコンのPCIスロットのような場所にカチャッと挿せる製品があればいいなと思っているのですが。
そういう製品は、本当に決められた動きしかない機器はやりやすいのですが、普通の自動機ですとそう簡単にはいきません。PCは、簡単にスロットを挿してラダープログラムを組んで同じように動かすソフトウェアを載せるためには少し難しいのです。だから簡単な製品はPLC文化が発達している日本が作るべきで、そうするともっと簡単なIoTが進んでいきます。
-まずPCベースにならないと、せっかく拡張性があるOSを積んでもあまり意味がないそうです。普通に考えたら、OSの上に乗せられたらフリークエンシーの高い産業機器もコントロールができなさそうな感じがするので、OSがボトルネックになっている気がします。いわゆるWindows OS の汎用PCを使えば、産業用のPLCに代わるような技術提供ができるものができるのかなと。
ベッコフ社、ロックウェル社、シーメンス社も良い製品を作っているのですが、日本ではPC制御自体が全然普及しません。Windowsなど汎用OSは安定性やリアルタイム性で生産設備の制御には適しませんが、データ処理などの汎用性が高く、活用しない手はありません。
また、高速処理と安定稼働を両立したCodesysなどのリアルタイムOSの認知も進んでいないのが現状です。プログラミング手法の標準化も進み、ラダープログラムでも記述できることもあまり知られていません。マルチコアCPUが普及している現在は、WindowsとリアルタイムOSを1台の産業用PCで並行して活用することも容易です。標準機を持っている装置メーカーはコントローラのPC化に対する取り組みが進んでいます。
-そうなりますよね。マーケット的に専用機作っている人たちがやりづらいですよね。
最近のロボットを使うシステム案件は画像処理システムを搭載するケースが多いです。画像処理システムとPLCとロボットコントローラの間をハブで繋いで、制御するためのPCを入れます。これは非常に無駄だなと思いますので、そろそろPC制御に変わっていくのではないかと思っています。
-水が上から下に流れるような世界があるのかなと思うのですが、今は結局やらざるを得なくなってきて「その箱が3つもあるのは、ナンセンスじゃない?」と誰かが言い出したときに、はたと気づくのかもしれません。
そうですね、だから特に食品系の包装機メーカーなどは、その取り組みが早かったです。タッチパネルを付けて、PLCを付けて、PC置いて、画像を置いていたのですが、パネル付きのパソコンで良い話です。
特定用途の標準マシンは装置メーカーさんが強いので、「私たちの仕様です。この仕様からずれると金額が高くなります」となります。自動車業界だと、専用機か1品ものが多いのでなかなかそれがやりづらいというのがあるかもしれないですね。
かつては世界に名を響かせた「Made in Japan」ですが、今人気がある職業は金融、商社、ITなどで製造業は下降気味です。とはいえ、日本のGDPの三割を占めるのはいまでも製造業であることには変わりありません。製造業で働くことの付加価値を高め、給与を上げ、働きたい業種ナンバーワンにしたい。
そのために必要なモノづくりを「Smart」にし、Smart Factoryという新しいことにチャレンジしたいエンジニアや企業の第1歩を後押ししたいです。その1歩を束ねることで日本の製造用に大きな変化をおこして未来を創ることが我々のミッションだと考えています。
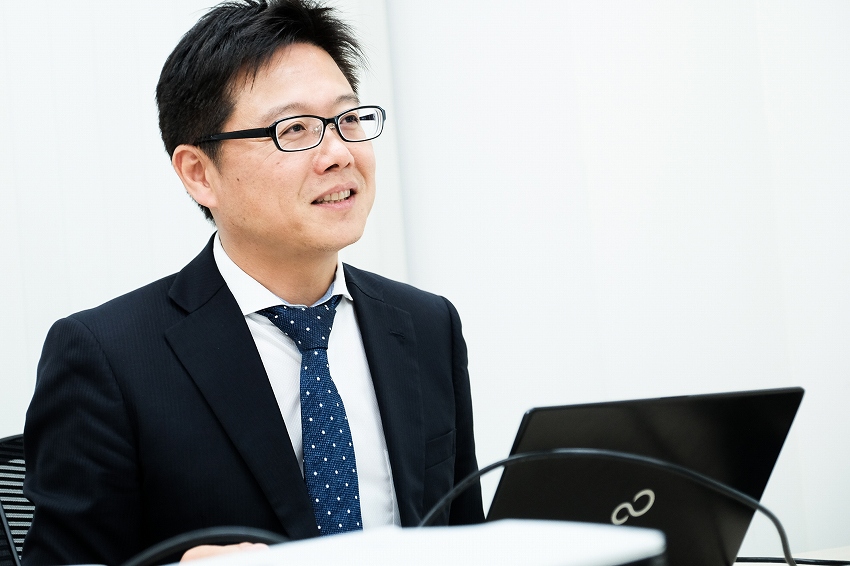
-本日はありがとうございました。
【関連リンク】
・FAプロダクツ
無料メルマガ会員に登録しませんか?
IoTに関する様々な情報を取材し、皆様にお届けいたします。