ダイナミック・ケイパビリティ強化のカギは、「設計力」にある
小泉: 後半の設計力強化戦略(本文p.73~)は、今回の白書の見どころの一つだと感じました。これは、製造業のデジタル活用の文脈において、あまり議論されてこなかったことですよね。
中野: まさに、今回の白書の重要なテーマです。ものづくり白書では、これまでは製造現場におけるIoTの活用などを重視していました。日本の製造業の競争力の強みは「現場力」、「匠の技」にあります。労働人口が減少に向かう中、その部分をデジタル化によって維持、強化していこうということを、経済産業省ではここ5年ほどうったえてきました。もちろん、製造現場が大事であることはいうまでもありません。しかし、今回ヒアリングを行った結果、この数年で日本の製造業の「設計力」が弱っているという声を多く聞きました。事実、近年、設計力が上がっていないという傾向が各種アンケート調査からも見られたのです(本文p.74~)。
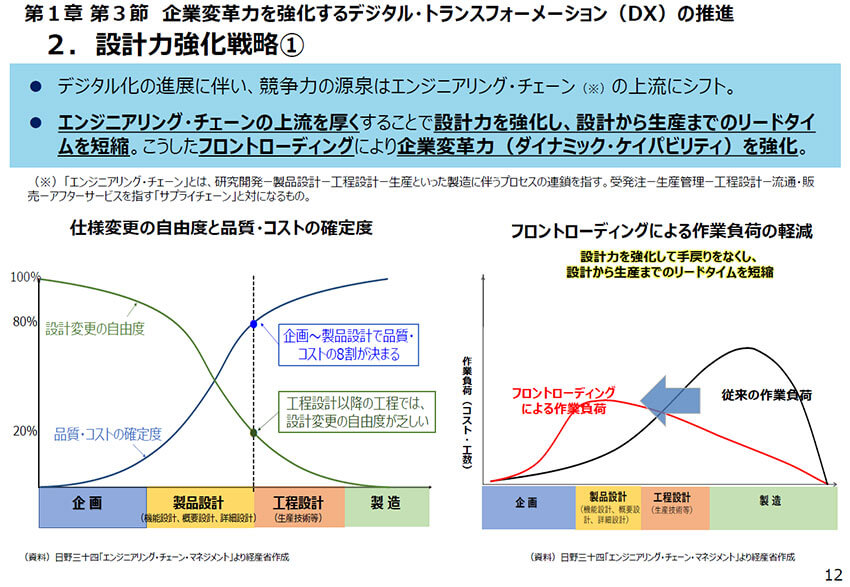
中野: 製造業では、製品の品質とコストの8割は、設計段階で決まると言われます。開発が進むにしたがって、仕様変更の自由度が低下していくからです。そのため、できるだけ開発の初期段階であるエンジニアリングチェーンに資源を集中的に投入する「フロントローディング」が有効です(上の図)。しかし、そのためには設計力が強くなければなりません。
具体的にいえば、設計段階でデジタル・ツールなどを使ってシミュレーションができれば、試作を行う必要がなくなります。すると、設計の作業負荷が下がり、しかもリードタイムを短縮できるようになります。これまで数か月かけて作っていたものが数週間、数日でつくれるということは、先ほどのダイナミック・ケイパビリティの議論に戻れば、「変化に素早く対応できる」(反射神経が高い)ということになります。製造現場の力が重要であることはわかっています。しかし、これまではその部分ばかりを重視してきたために、設計力が弱っている、設計のデジタル化が遅れている、という現状を看過してしまっていたという反省があります。
しかし、よく考えてみれば、製造現場のデータをIoTで収集できれば、その知見を設計にフィードバックできます。したがって、製造現場のデジタル化というのも、結局のところ設計力に効いてくるということになります。言い換えれば、設計力を強化して、フロントローディングを進めるためには、データの活用や設計のデジタル化(3Dデータでの設計)によって、設計―製造―サービスといったプロセス全体の連携を進めていくことが重要になるのです。
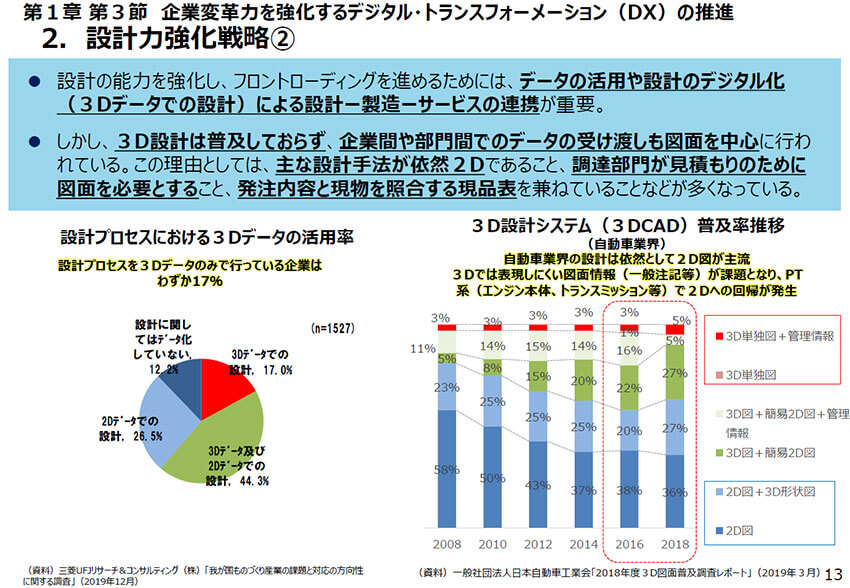
ところが、現状はなかなか厳しいです。アンケート調査を行ったところ、設計プロセスを3Dデータのみで行っている企業はわずか17%しかいないことが判明したのです(上の図・左)。また、自動車業界では、3DCADの普及率は低迷し、むしろ2Dへの回帰が進んでいることもわかりました(上の図・右)。企業にヒアリングしてみると、3Dで設計したデータをわざわざ2Dデータ・図面に変換して渡し、受け取った方がまたその2Dデータ・図面を再び3Dデータに変換するといったこみいった現状があることもわかってきました。実際にアンケート調査からは、そうした傾向が出ています(本文p.92)。欧米のデータはないので比較はできませんが、日本で欧米と取引している企業では3Dデータで設計データのやりとりをすることは当たり前ということですから、日本は相当遅れているのだろうと推測しています。
(後編へ続く)
無料メルマガ会員に登録しませんか?
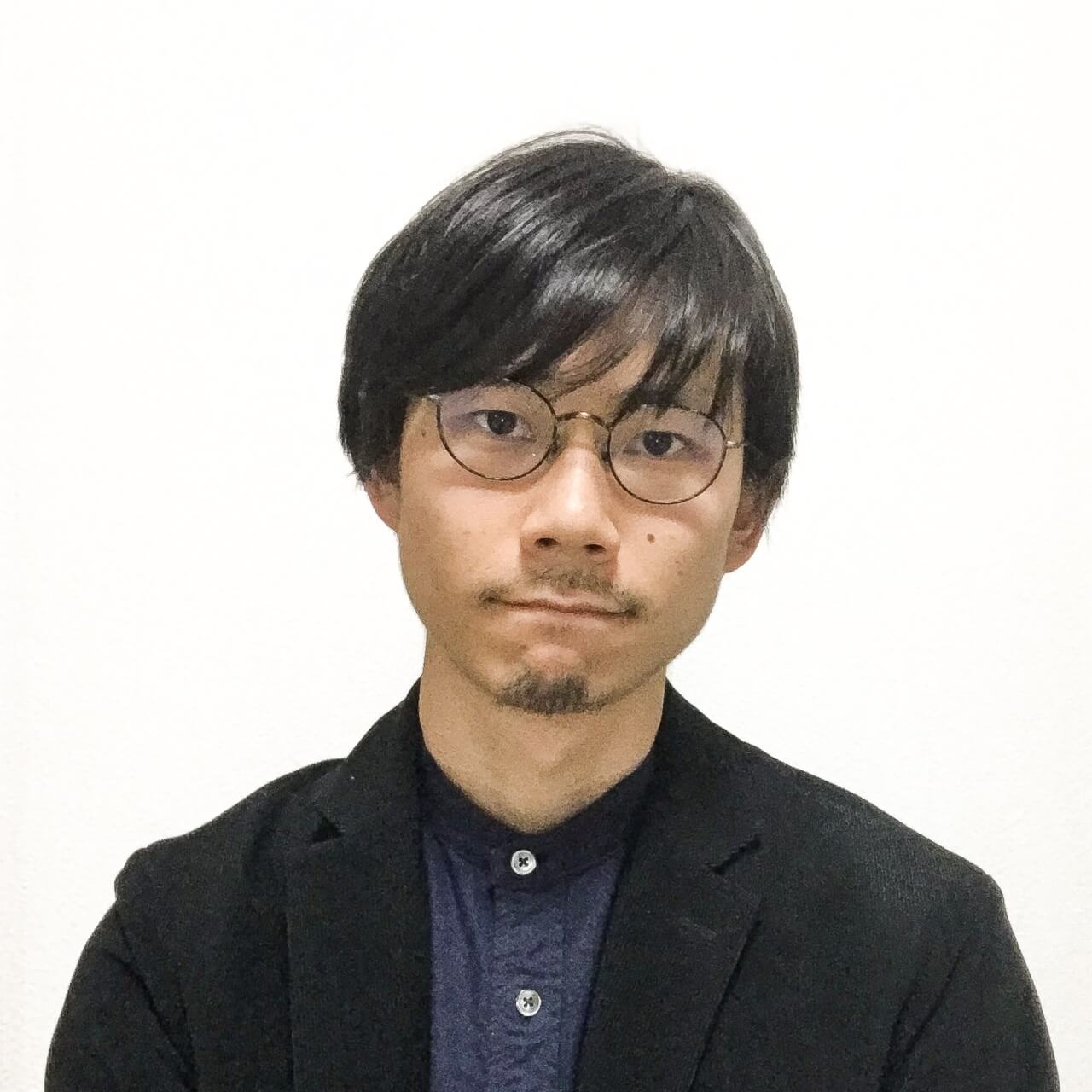
技術・科学系ライター。修士(応用化学)。石油メーカー勤務を経て、2017年よりライターとして活動。科学雑誌などにも寄稿している。