切削の現場に見る、デジタルを活用した競争力の強化策
福本: 予知保全ではないですが、デジタルを活用した製造という意味では、工具の磨耗により発生する「削る側」のズレにあわせて「削られる側」をずらして、摩耗した工具でも正確な位置を削ることができる、というコアコンセプト・テクノロジーの事例をみたことがあります。こういうアプローチは消耗品も長く使える良い事例だなと思いました。
田口: その事例は、切削の現場において、補正の作業が難しいということを解決した事例になります。
このヒトでないとできない、ということが多いのでどうにかしたいわけですが、切削結果の定量化は画像センサや振動センサを使えば可能です。それで実際とのズレを見て、温度や振動なども合わせて結果との因果関係をAIでなんとかするのです。
どれくらい時間がたつと、どれくらいズレるのか、ということについてはこのAIでわかるので、あとは、切削時に機械をどれだけずらせば良いかがわかります。これを導入することで、アルバイトでも作業ができるようになるのです。
結果的に、競争力が高くなるのです。
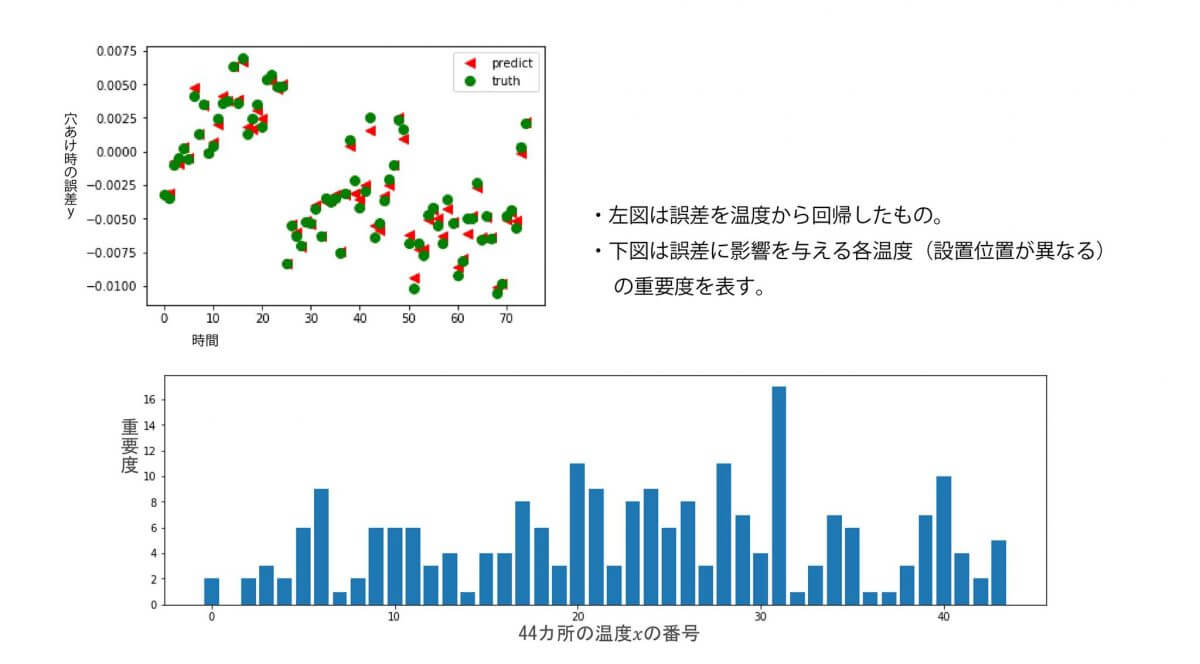
44カ所の熱電対温度センサーの値𝑥と穴あけ加工機の誤差𝑦との関係を算出した。
機械学習(回帰と重要度の算出)を活用している。
提供:コアコンセプト・テクノロジー
小泉: そもそも、温度と因果関係があるというのはどうやって導き出したのですか。
田口: いろんなお客様と付き合うことで、切削における微妙なズレはだいたい温度に依存しているということがわかってきました。
それで、温度と結果との依存関係を見るということになります。詳細は省きますが、弊社では結果として勾配ブースティング法を使うとよいということがわかってきています。
ディープラーニングが流行していますが、最初は古典的な解析方法でアプローチする事も多いです。そのうえで良好な結果が出ない場合などに機械学習、ディープラーニングに移行していきます。
小泉: 数理式の選択は経験がいるのでしょうか。
田口: 時系列であればRNN(リカレント・ニューラルネットワーク)、画像処理であれば、コンボリューション・ニューラルネットワークと、AIの実装方法の選択において、決まってきているものがあります。しかし、こういう決まっていないことについては、経験が積み重なる必要があるのです。
小泉: いろんなことを試しているからわかることであって、経験のある領域だからわかるということですね。
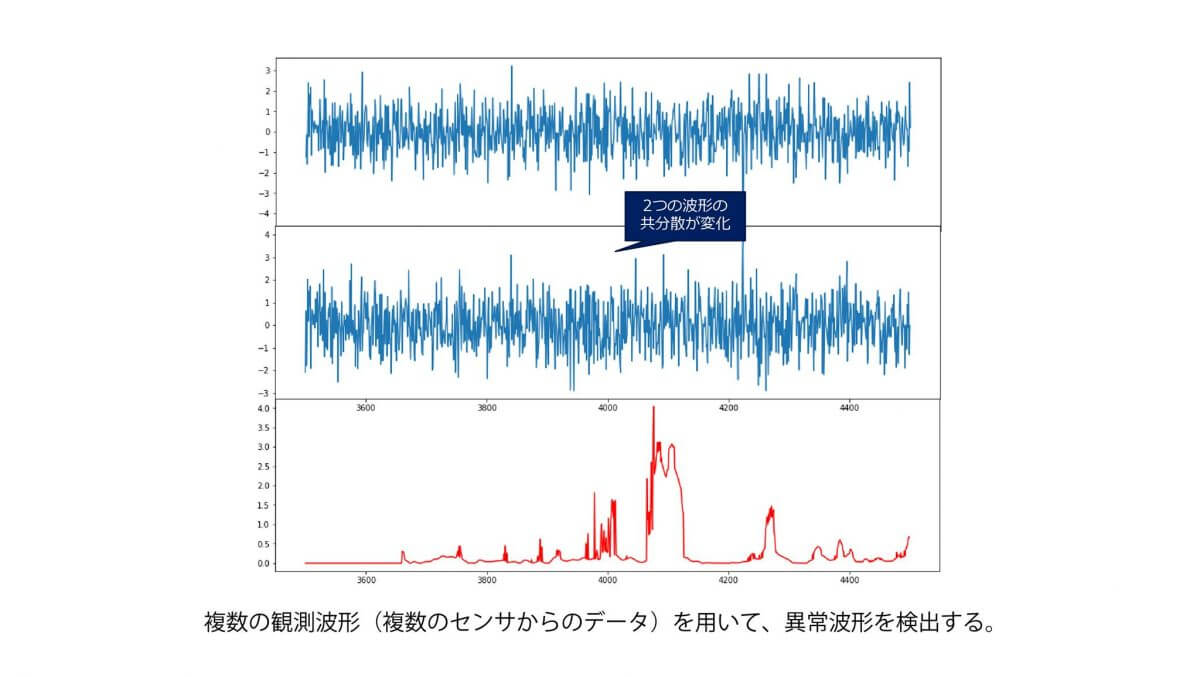
密度比推定(異常検知)の事例
提供:コアコンセプト・テクノロジー
福本: 現場の人は、経験的に「こういうときに、こうすればよい」というノウハウを持っていることが多いです。そこを教えてもらうことで、闇雲に、色々な相関確認を行う必要もなくなります。
例えば、溶解金属から成形をした時に、巣が入る時があります。金型の温度や素材に対する不純物の含有量によって巣の入りやすさが変わったりします。これが経験的にわかっていれば、取得データやAIの活用範囲を予め絞り込むことができるのですが、知らないと闇雲にやることになります。
田口: 我々も熟練工の話が聞けるなら聞いて対応しています。例えば、故障する時に音が出るというのであれば、マイクを置いて音をとり、スペクトグラムを作ってみる、といったようにヒントとして使う場合もあります。
射出成形でも、温度が上がらないと剥がれにくいという話があります。そこで、イジェクターピン(型からの取り外しに使うピン)にどれくらいの応力がかかっているかをセンシングする、ということもやっています。
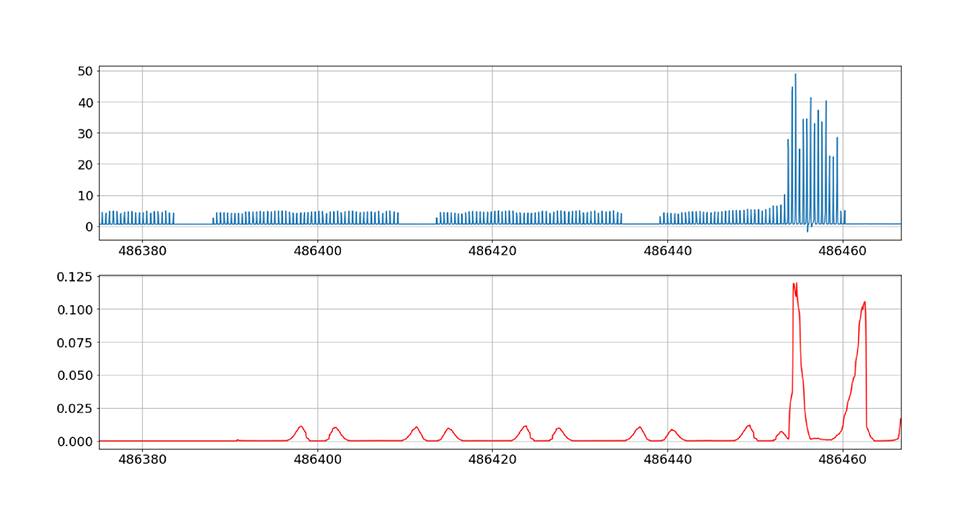
観測波形が大きく変化するとき、異常度も大きな値をとっている。
機械学習(波形の差異を検知する)
提供:コアコンセプト・テクノロジー
小泉: つまり、初めはうちの「IoTどうにかしてよ」と言われる。でも細かなニーズはないので、「大雑把にアイデアをだす」。それをやったことがあることであれば話が通りやすいが、なければ説明をするけど、説明をしてもわからない場合もある。そして、うまくいくとOKというプロジェクトの進め方になるわけですね。
次ページ「大企業の工場と中小工場に差はあるのか」
無料メルマガ会員に登録しませんか?
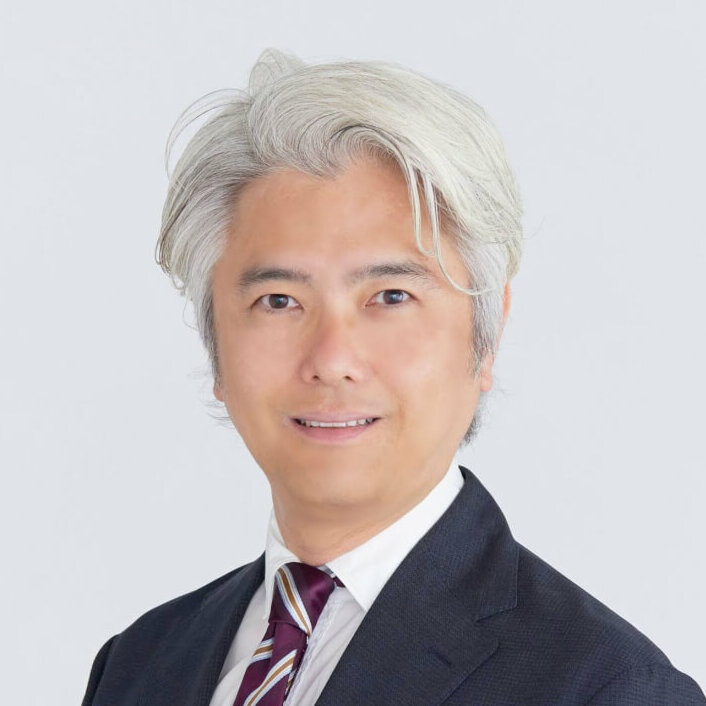
IoTNEWS代表
1973年生まれ。株式会社アールジーン代表取締役。
フジテレビ Live News α コメンテーター。J-WAVE TOKYO MORNING RADIO 記事解説。など。
大阪大学でニューロコンピューティングを学び、アクセンチュアなどのグローバルコンサルティングファームより現職。
著書に、「2時間でわかる図解IoTビジネス入門(あさ出版)」「顧客ともっとつながる(日経BP)」、YouTubeチャンネルに「小泉耕二の未来大学」がある。