製造業におけるIoT/AI、スマートファクトリーを考えたとき、デバイスの設置やクラウドサービスの利用法などの情報から「とりあえずPoCをやる」という流れが一定ある。
しかし、本質的な製造業における改善事項が理解されていない状態でのPoCは技術検証にしかならない。そこで、製造業における様々な品質向上や生産性向上のキーワードの中でも、製造工程に注目し、その生産性(労働生産性・設備生産性・原材料生産性)を向上させるためのポイントについて解説する。
目次
「ムダ」を省き、労働生産性を向上する
労働生産性とは「ある一定期間に、作業者1人がどれだけ付加価値のあるモノをつくれるのか」を示す指標である。労働生産性を向上させるためには、製造過程に生じる「ムダ」「ムリ」「ムラ」を省き、作業者の作業能率を上げる事が必要だ。
「ムダ」とは、ものづくりに本来必要のない作業を行っている状態を指す。ムダが増えれば、サイクルタイム(作業時間)における正味作業(付加価値を生む時間)の比率が下がる。トヨタ生産方式によると、代表的なムダには、以下の7点がある。
つくり過ぎのムダ
必要量以上にモノを作ることで、タクト設定や管理の甘さから生まれる。作りすぎていると作業者が忙しくなるため、「手待ちのムダ」が隠れてしまうことがある。また、作りすぎのムダが発生することで、「在庫のムダ」「動作のムダ」「運搬のムダ」も発生する。
また、昨今海外への供給が多くなってきていて、リードタイムが長くなることがあり、その際に作りすぎのムダも発生しやすくなってきている。
加工のムダ
「機械加工」「溶接」「仕上げ」「検査」などの工程で、標準が決まっていないことによる、必要以上の仕上げや検査を行うこと。従来のやり方を見直し、本当に必要な作業を見つけ出すことで改善される。
運搬のムダ
「モノの移動」「仮置き」「積み替え」などが必要以上に行われていること。モノの流れを決め、工程のバランスを最適化することで改善される。
また、運搬ルートが最適なのかどうかをシミュレーションすることも運搬のムダを省くのには有効だ。
そもそも工場のスペースが狭いことや、金型などの治具工具の置き場が場所を取りすぎていることを理由に、遠い資材置き場からモノを運搬する必要があるのが原因となることが多い。
在庫のムダ
「材料」「部品」「仕掛品」「完成品」の在庫が必要以上に滞留していたり、逆に必要な在庫が準備できていないため製造できない状態になること。在庫の状態を論理的に説明できるようにすることで改善される。
在庫は、生産リードタイムの観点から、仕入れ先に在庫リスクを転嫁しているような受発注関係の場合に、必要以上の量をもつ必要が出てくることがある。
動作のムダ
「探す」「しゃがむ」「持ち替える」「調べる」など人の動きの中で付加価値を生んでいない動きのこと。作業を標準化し誰でも同じ動きができるようになっていない場合や、訓練不足の場合に起きる。作業者の動作を観察し、動作にムダがないかを確認することで改善される。
手待ちのムダ
やることがなくなり、作業者が暇になること。標準作業を明確にして、手待ちを顕在化しなければ、作業者の作業スピード調整により、手待ちが起きていることに気づかない状態となる。
不良のムダ
不良品を廃棄したり、手直し、作り直しを行うことで発生するムダ。標準化を遵守させることや、品質管理を徹底することで改善される。工程単位で完結した品質管理を行うことも重要。
生産性向上の指標となる、「標準作業」とは
すべてのムダは、きちんと定義された「標準作業」との差分でうまれてくるものだ。この、標準作業とよばれるものは、どう定義づければよいだろうか。
標準作業とは、ヒト、モノ、設備を品質よく、ムダなく、早く、安全につくることだという。「標準の無いところに改善はない」といわれるように、改善を行う際の指標となる。
「タクトタイム(製品や部品を何秒で作らなければならないか)」「作業順序(最も効率的に作業を行うことができる順序、誰でもできないといけない)」「標準手持ち(同じ手順で繰り返し作業ができる最小限の手持ちのこと)」から構成される。
※タクトタイム=稼働時間/必要数量
「設備生産性」の向上
設備生産性を上げるためには、設備が止まっている時間を減らし、可動率(べきどうりつ:=実際に設備が動いた時間/設備を動かす計画上の時間)を上げる必要がある。
可動率(べきどうりつ)=生産実績数x基準サイクルタイム/総運転時間
[注意] 可動率と稼働率は異なる指標だ。可動率は上記の通りだが、稼働率は1日の生産能力が100個だとした場合、注文が150個来た時に、稼働率は150%となる。つまり、稼働率は注文の状況によって変動する指標だが、可動率は注文の状況とは関係ない。可動率は、本来100%であるべきなのだが、チョコ停やドカ停によって、可動率は落ちていく。
設備の停止要因は、「設備故障(チョコ停やドカ停)」「段取り替え時間・切り替え時間」「設備メンテナンス時間」「清掃時間」があげられる。
故障による停止を防ぐためには、早期に設備の異常を検知して故障を直すか、そもそも故障を起こさないように予防保全(故障しそうな箇所を未然に見つけて修理する)を行う必要がある。
また、「段取り替え」に関しては、生産する製品の変更に伴う、刃物交換・金型交換といった設備の切り替え作業を指す。段取り替えには、設備を完全に止めずに切り替え作業を行う「外段取り」と、設備を一旦停止して作業する「内段取り」がある。設備の停止時間を減らすには、内段取りをできるだけ外段取りにしていく工夫が必要になる。
設備生産性の指標「設備総合効率(overall equipment effectiveness, OEE)」
また、設備生産性に関して、可動率のほかに、「設備総合効率」という指標が使われることがある。これは、以下の式であらわされる。
設備総合効率=時間稼働率x性能稼働率x良品率
※時間稼働率=(負荷時間-停止時間)/ 負荷時間
※性能稼働率=(基準サイクルタイムx加工数量)/ 稼働時間
※良品率=(加工数量-不良品数量)/ 加工数量
「設備7大ロス」と呼ばれるものがあるが、以下の7つだ。
- 故障
- 段取り・調整
- 刃具交換
- 立上がり
- 空転・チョコ停
- 速度低下
- 不良・手直し
負荷時間に対して、「故障」「段取り・調整」「刃具交換」「立ち上がり」「空転・チョコ停」は、「稼働時間」を減らす「停止ロス」の原因となる。
また、「速度低下」は、「賞味稼働時間」を減らす「性能ロス」となり、「不要・手直し」は、「価値稼働率」を減らす「品質ロス」の原因となる。
「原材料生産性(歩留率)」の向上
最後の、原材料生産性は、歩留率(=生産高/材料の使用量)で計算される。歩留率を上げるためには、材料のロスを抑えつつ、製品をなるべく多く作ることが必要だ。製造段階で材料のロスを無くすポイントとしては2点あり、「不良品を作らないこと」「付加価値を生まない製造」を極力減らす事がある。
2点目の付加価値を生まない製造に関しては、「成形条件を調整するために行う試作」などがある。
また、プレス工程や樹脂成型工程のように、金型交換のための段取り替えが発生する工程では、段取り替えが頻繁に起きないよう、ある程度まとめてロット生産を行うのが通常だが、実際には段取り替えを行うたびに、歩留まり率が落ちてしまうケースがある。これは、昨今の人材不足・匠の技術の伝承の問題から、段取り替え時の最適な生産体制が作れないことに起因する。
無料メルマガ会員に登録しませんか?
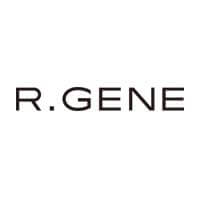
「DXトレンド解説」と「DX実践講座」は、IoTNEWSの運営母体となる株式会社アールジーンのコンサルタントが、これまでの経験と知見をお伝えするコーナーです。
「体系的に勉強会を開いてほしい」「企画のアドバイスが欲しい」「コンサルティングをしてほしい」などのご要望は、問い合わせフォームよりご連絡ください。