2020年7月16日、ウイングアーク1st株式会社のウェビナー「生産デジタルツインの現実解 ~目指す姿とそのアプローチ~」が開催された。
本記事は、同ウェビナーでのシーメンス株式会社の泉佑樹氏の講演内容について紹介する。
シーメンスは全ての事業においてデジタル化を進めていて、雇用を維持しつつ生産性を14倍向上したという。このセッションでは、その秘訣である「Closed-Loopのデジタルツイン」について解説を行った。
今、日本の製造業で起きてること
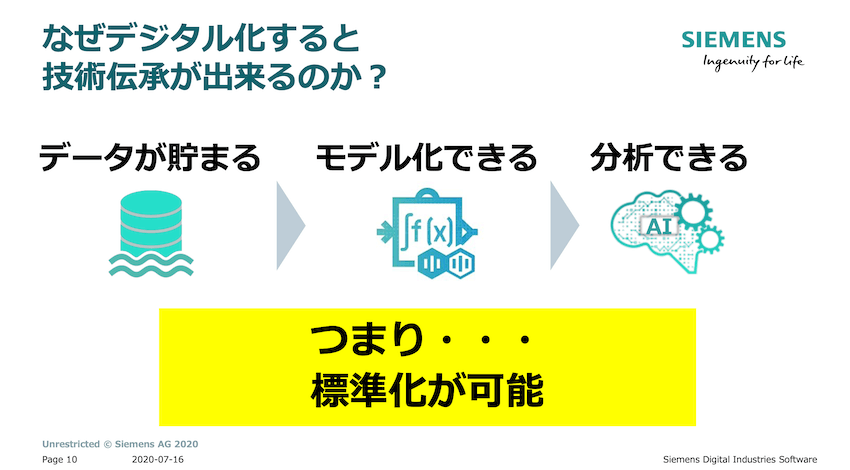
今、日本の製造業では大きく、
- 人手不足
- 高齢化
- 技術伝承ができていない
という3つの課題が起きているという。
製造業の現場では、人手不足を解決するためにファクトリーオートメーションやロボットオートメーションなどの自動化を行っている。高齢化については、雇用を延長して解決しようとしている。これらは、すでに取り組んでいる企業が多い。
しかし、技術伝承を本質的に解決するのは非常に難しいとした。シーメンスでは、デジタル化によってこの課題を解決している。工場のラインや設備をすべてデジタル上に再現するという取り組みだ。
デジタル化するとデータを貯めることができる。データが貯められればデジタル上にモデル化できる。モデル化できればAIで分析することができるようになる。つまり、属人化していた作業を標準化することが可能となるのだ。
デジタル化の方向性とデジタルツイン
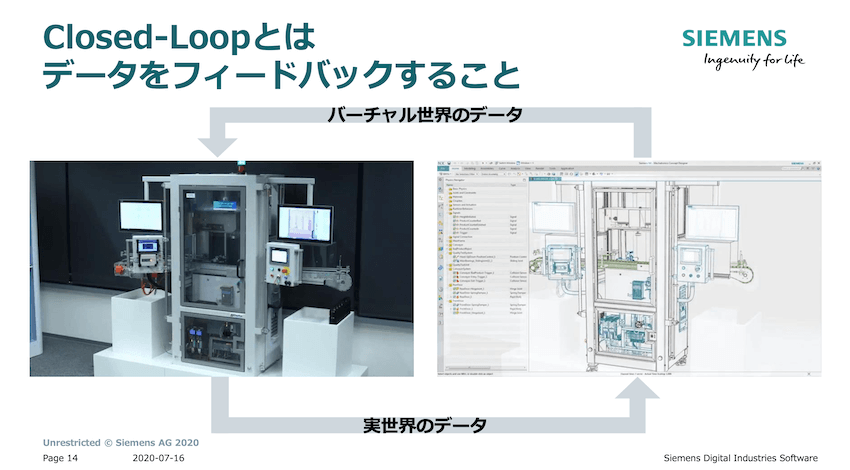
デジタル化は、接続、診断、デジタルツイン、AIの活用という順番で、時間がかかるが結果も大きくなっていくとした。
しかし実際は、接続だけでも大変だという。古い生産機械が存在していたり、生産設備は生産をすることを第一にしていたりするため、そこからデータを吸い出すということをどうやって行うのかが課題となる。更に、その取得したデータの診断をどうするのかを検討する必要がある。
接続と診断ができるようになって、ようやくデジタルツインができ、モデル化できる。これが可能になったところでAIの活用が実現し、標準化ができるようになるのだ。
今回のセッションではデジタルツインについて紹介するとした。接続や診断に関してシーメンスは協業によって課題解決をしているという。
デジタルツインを実現するということは、デジタル上の双子をつくるということだ。現実世界の機械と同じものをデジタル空間上で再現するのだ。
では、このセッションのテーマである「Closed-Loop」とは何か。これは現実世界とデジタル空間が互いに連携し、データをフィードバックしループするということだ。Closed-Loopのデジタルツインを構築することで、シミューレーション精度の向上を行なったり、現実世界の機械には設置されていないセンサーをデジタル空間上で検討するようなバーチャルセンサーを実現することができたりするのだ。
デジタルツインの第一歩
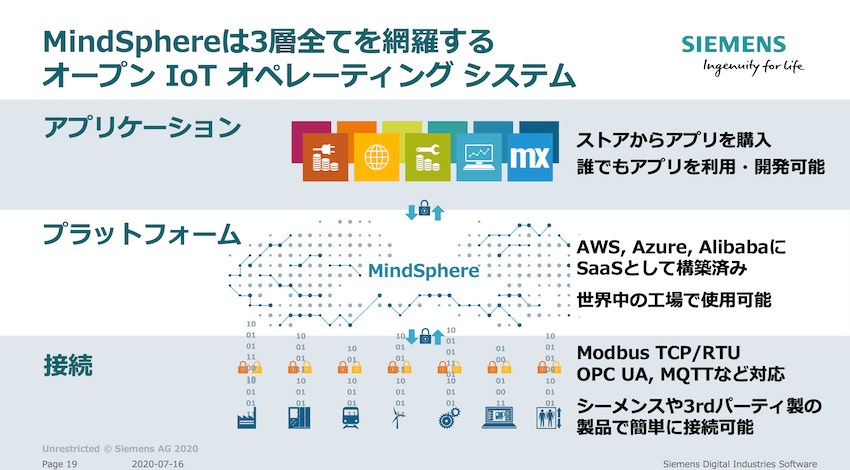
しかし、実際にラズベリーパイに温度センサーを搭載し、温度を取得したらそのデータをクラウドにアップロードして可視化するという作業を行おうとした時、30分で設定完了できるという時代がきているのだ。
実際に工場のデータを可視化するときには、クラウドベースの産業用IoTを使うことを推奨している。
- 目的が絞られているのですぐに効果がだせる。
- 環境構築から実施までトータルコストを安く抑えられる。
- 設備に接続する手段が豊富だ。
ということがその理由だ。
産業IoTは、接続、プラットフォーム、アプリケーションという3つの層でできている。
アプリケーションの層では、可視化、機械学習で異常検知、予兆保全などができる。プラットフォーム層では、AWS、Microsoft Azure、Alibaba Cloudなどの様々なプラットフォームの中から、どんなプラットフォームを使うかを検討する必要がある。接続の部分では、現場の機器をどのように接続するかが重要になる。通信プロトコルとして、OPC UAやModbus、MQTTなどの中から検討する必要がある。
シーメンスのMindSphereでは、これら3層を全て網羅している。アプリケーション層では、ストアからアプリをインストールしたり、誰でもアプリを利用したり、開発したりすることができる。プラットフォーム層では、AWS、Azure、Alibabaといった3社に対して対応している。このプラットフォームにサービスを提供する、つまり、SaaSとして提供することができる。中国に工場があったり、中国でサービスをやっていたりする企業では、Alibaba Cloudを使うことで、グレートファイアウォールの影響も受けない。
接続に関しては、Modbus、TCP/RTU、OPC UA、MQTTなど様々なプロトコル、サードパーティ製の製品、Node-REDなどにも対応している。
IaaSでIoT環境を構築する場合とMindSphereを使う場合を比較した時、MindSphereの方が専門的なITスキルが不要なことが大きい。初期投資や運用費に関してコスト削減も実現できる。
クラウドへの接続と可視化に関しては月額4万円で実現できる。その上でBIアプリをつかったり、データ領域の拡張などにも柔軟に対応可能ということだ。
既に準備されたアプリとしてはすでに1000以上のものが提供されていて、汎用的なものから特別なものまで様々な種類があり、ウイングアーク1stが提供しているMotionBoardもMindSphereに対応している。
MindSphereを使用した事例は多く存在しているが、代表的なものとしてフォルクスワーゲンの例がある。122の工場とMindSphereを接続した。大手企業でも、環境構築はシーメンスに任せ、自社の強みである自動車の開発や製造に集中するということをやっている例だ。
また、ドバイ万博のスマートシティもMindSphereを使用した事例である。130以上の建物を接続し、スマートシティ化を行った。スマートシティアプリでデータ管理を行い、満足度向上、エネルギー効率化などに活用されている。
Closed-Loopのデジタルツイン
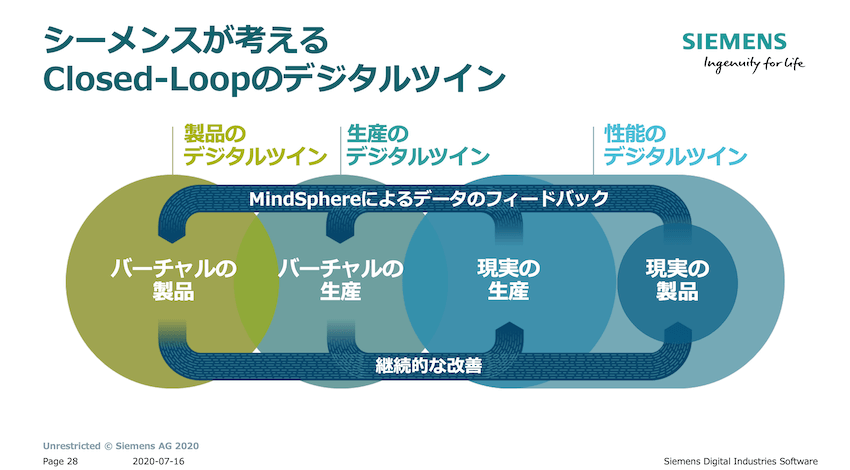
シーメンスでは3つのデジタルツインを考えているという。
1つ目は、製品のデジタルツインである。これは、製品の開発や設計の段階において、CAEやCFDといったシミュレーションモデルと実験データを使って製品リリースまでの時間を短縮
することに活用できる。
2つ目は、生産のデジタルツインである。これは、工場のデジタルツインとIoTデータでClosed-Loopを行うことでで生産性改善に活用できる。
3つ目は、性能のデジタルツインである。これは、市場に出回っている製品からの使用状況などのデータを活用することで、次に販売する新製品の品質改善を行うものである。
この3つのデジタルツインがそれぞれClosed-Loopを行うだけでなく、全体が密接に関係することが重要である。
生産におけるClosed-Loopのデジタルツインがもたらす嬉しさは3つあるとした。
1つ目は、シミュレーション制度の向上だ。MindSphereで取得しているリアルタイムデータを使用して、シミュレーション精度を向上することができる。実績値をもとに信頼できるシミュレーションモデルを作成できるので、机上で検討を行えるようになる。
2つ目は、工場ライン停止時の再現だ。ラインが止まった時、現実のラインで再現することは難しい。生産も止めないといけないため生産効率も下がってしまうし、そもそもラインを使っても再現できるかわからない。これもMindSphereで取得しているライン停止時のデータを使用することで、ラインが停止した時の状況をシミュレーション上で再現することができるのだ。改善活動に活用することができる。
3つ目は、What if 解析である。新しい製造条件やテストシナリオを確認できる。ラインのレイアウトなどもデジタル上で検証したり、効果についても現実世界の情報を使うことで検証することができるのだ。工場ラインの最適化ができる。
最後に泉氏は、「生産性向上の秘訣は工場のデジタル化だ」とした。Closed-Loopのデジタルツインの実現を念頭に置きながら、まずはデータを取得しクラウドに上げて可視化することから始めてみてはどうだろうかと語った。
参考:このイベントの他の記事は次のリンクから見ることができます。
ウイングアーク1st株式会社のウェビナー「アフターコロナに挑む製造業。デジタルの活用で、変化に強く儲かる工場を考える2days」
無料メルマガ会員に登録しませんか?
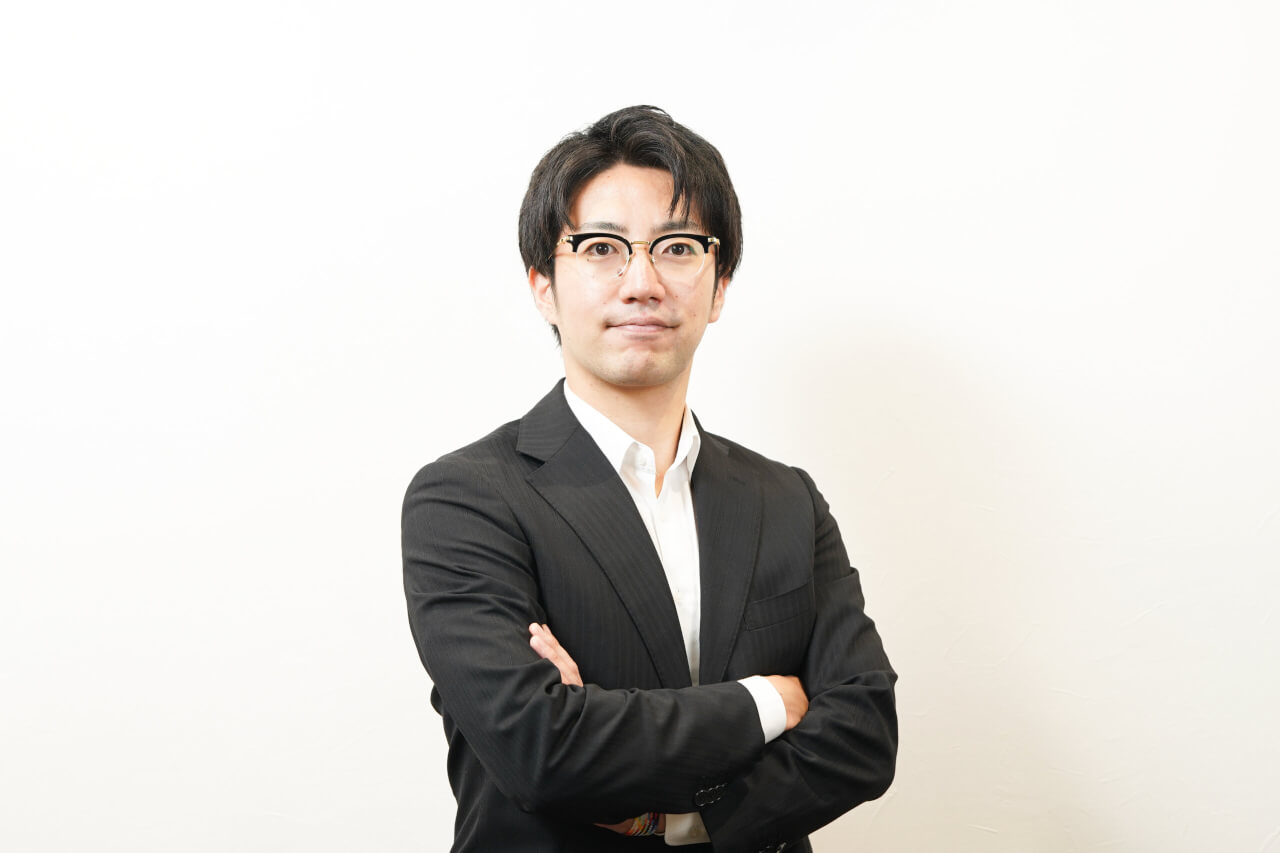
大学卒業後、メーカーに勤務。生産技術職として新規ラインの立ち上げや、工場内のカイゼン業務に携わる。2019年7月に入社し、製造業を中心としたIoTの可能性について探求中。