2020年7月16日、ウイングアーク1st株式会社のウェビナー「生産デジタルツインの現実解 ~目指す姿とそのアプローチ~」が開催された。
本記事は、同ウェビナーでの株式会社マクニカの阿部幸太氏の講演内容について紹介する。
マクニカはこれまで、製造業におけるDXやAIの活用の支援など、250件程度の現場を担当してきている。その中でわかってきている、陥りがちなトラブルやそのトラブルを乗り切った顧客の共通点の解説を行った。
テーマ・スコープ設定の肝
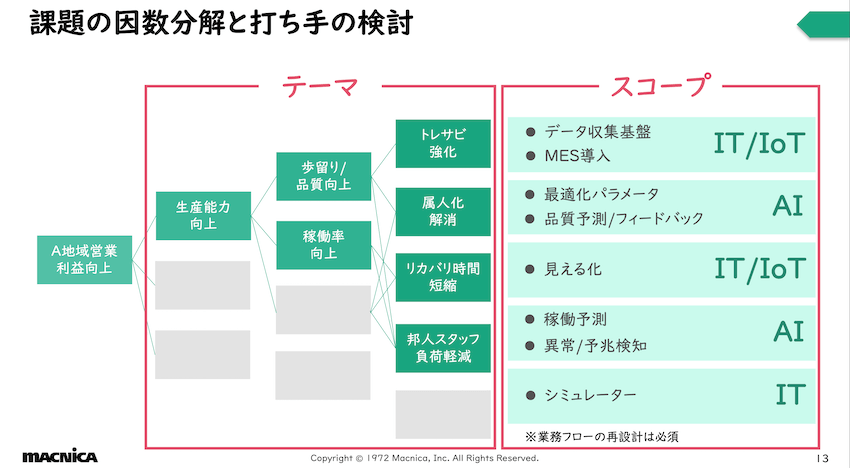
デジタルデータを活用し課題解決を行おうと考える場合において、まず課題の整理をして、ブレイクダウンを行い、テーマを決めて、テクノロジーを当てる、こういった流れになることがほとんどだろう。
テーマに関しては、今の業務をどうデジタルデータで解決するかということなので、顧客企業のリーダーがキーパーソンになる。なぜなら、実際にその業務に従事しており、その業務に関する知識が豊富だからだ。しかし、スコープを設定するという部分が難しいと感じているという。テーマ設定とテクノロジーの紐付けが難しいからだ。
スコープ検討の初期段階において、複数技術領域のスペシャリストのインボルブが手戻りを最小限にする上で重要だ。AIを使おうと考えたとき、物性や生産設備がわからないとどうやってAIを活用するかがわからないし、実際に運用をする場合には、金額はいくらでどういうシステムであれば運用できるのかといったようなITの知識も必要になる。
プロジェクトの初期段階の検討では、データエンジニアやITエンジニアなど、多くの領域のメンバーで顧客とディスカッションを行いながらテーマ検討をしている。プロジェクトを進める上で、社内に足りない専門知識をうまく社外のメンバーを活用しながらチーム編成を行うことが重要である。
分かっていても陥るデータの重要性
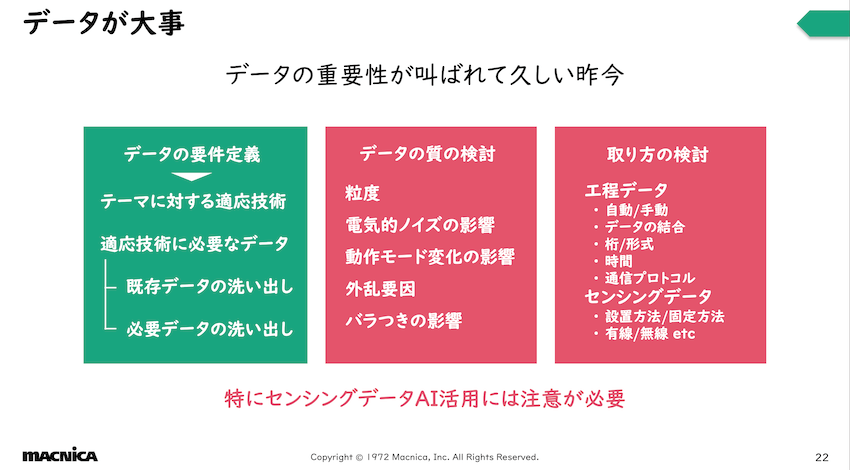
デジタルデータの活用は1番最初が難しい。データがあればデータを見て議論ができるが、データがないと、何をどうしたらどんな効果が出るかがわからないというところから始めなければならないので、話が進まないケースが多い。
データが大事ということは散々語られてきているため、意識が高い企業も多く、データの要件定義を初めにやることはもはや常識になってきている。しかし、必要なデータは何なのか?足りないデータは何なのか?ということを議論していても、結局データ起因で手戻りが発生してしまうことがある。
なぜなら、データは項目を検討するだけでは足りず、質を検討することが重要だからだ。
PoCであれば問題ないかもしれないが、運用することを考えたときに、ローコスト・ローパワーでデータが取得できなければならない。ある程度初期段階で、後々の分析までを見越してデータの質や取得方法を検討していなければ、後からデータが足りなくなってしまい、手戻りが発生してしまう。
1つの例として、センシングデータに振動データを使う場合を考える。
振動を取得する対象の設備が、何を削るための設備なのか、どうやって削るのかといった粒度が足りなかったり、センサーの精度を変えたことで無線通信でデータが送れなくなってしまったりといったようなことが起きると手戻りがとても多くなってしまう。
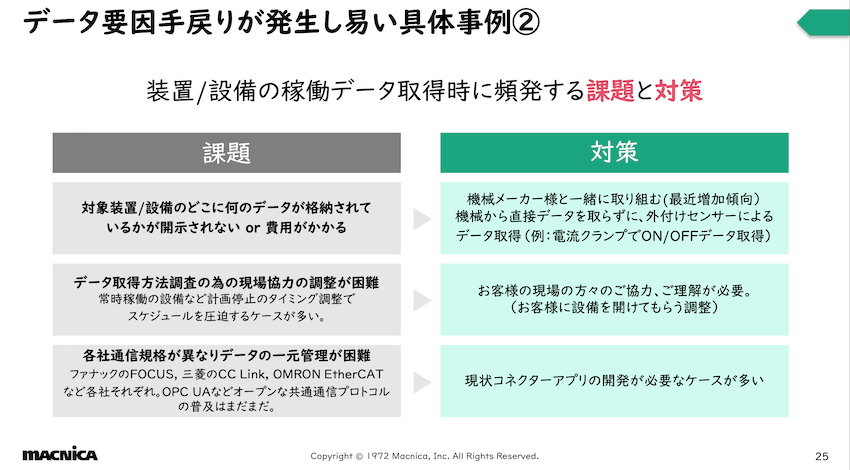
他にも、設備を見える化しようとなったとき、対象の設備ひとつひとつに、何のデータがどこに格納されているかが開示されていなかったり、そのデータを取得するためにメーカーと交渉が必要だったりすると、データを集めるところに時間とお金がかかってしまい、データを使った効果を見る時間が減ってしまいプロジェクトがストップしてしまうケースが非常に多いという。こうした課題は、プロジェクトを機器メーカーと共同で取り組むことで徐々に改善されてきているが、まだまだ課題は多いそうだ。
データ取得方法の調査のための現場の協力が困難な場合もある。新しいデジタルデータを活用したテクノロジーのプロジェクトの場合、主体となるのは現場と少し離れたR&D部門だったり研究開発部門だったりするケースが多い。実際にこのデータが欲しい、このデータを取ろうとなったとしても、生産現場と、設備をいつ止めるのかといったような調整が必要になり、生産スケジュールへのインパクトも大きいことが想定される。
さらに、機器メーカーごとに通信プロトコルが異なる場合があって、接続を行い、クラウドにデータを上げるということは難しいという。BCPの観点からも、同じメーカーで生産設備を揃えている場合は少ないため、OPC-UAのSDKがあっても、コネクタのアプリ開発をしなければいけないケースが多い。
データの手戻りが発生しやすい事例の1つとして、混ぜる、練る工程がある。こうした工程は、プラスチックや小麦粉、化粧品などの工場に存在しているが、品質改善の時に多変量でデータを見ないといけないので、正規化が大変になる。
温度や回転数、湿度、水分量といったパラメータをシステム的に取るのはあらかじめ考えられているのだが、工程間の時間が実は品質に影響を与える場合が多いことがあとからわかり、システム的に手戻りが発生してしまったということもある。
最大の難関は現場の反対
デジタルデータを活用するソリューションを導入するにあたり、最大の難関は現場の反対だという。デジタルデータのプロジェクトが実際にスタートし、PoCまでうまくいった後に、運用時に現場の反対にあるというケースがよく起きてしまう。
実際にシステムを使う現場の方から、忙しい、AI/IoTがよくわからないのでやりたくないといった使えない理由が出てきたり、現場が納得するシステムではないと入れられないということが起きたりする。
この課題を解決するために、プロジェクトをスタートする時点で実際に使う人も最初からインボルブするようにしている。導入のタイミングになってから説明を行うよりも、プロジェクトの初めから入ってもらいプロセスを共有することが重要だ。
実は厄介なヒューマンインタフェース
ヒューマンインタフェースは、スケジュールの延伸と費用増加のきっかけになりやすい。アウトプットされる画面が出て始めて、あれを見たい、これを見たい、とフィードバックが来るようになる。
しかし、その要望を限られた予算や時間の中ですべて叶えていくということは現実的ではない。画面の試作を見てもらっている時点で、システム運用開始の日程も費用も決まっている場合がほとんどだ。
本質的に大事なのは、誰がいつどう使うかのイメージをクリアにしておくことが重要なのだ。ここでは、現場の意見を聞きすぎないことも重要になる。
日本で作成したシステムを、海外など新しい現場で使いたいというケースも多い。業務のエキスパートからは、これを見たい、あれも見たいということを言われることが多いが、そういう人は案外システムが必要がない人である。海外工場で働く人やノウハウがない人が、見たいこと、見なければならないことを明確にして、システムを作ることが重要だ。慣れの部分もあるため、ある程度使用してからアップロードしていくことが必要になる。
では、どうやってデジタル化を始めるのか?
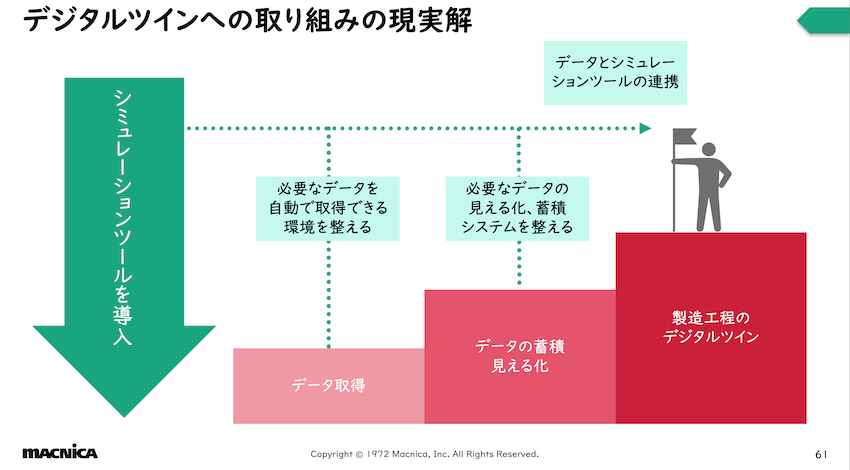
デジタル化を始める時、課題をブレイクダウンしてやることを決めていく。この時、見える化やシミュレーターから始める場合が多い。しかし、何をいつ、どんな予算でやるかが明確にならないと、プロジェクトを始められない。
マクニカでは、検討の時間がなかなか取れない方のために、月額費用を固定で見える化を進めるようなサービスもやっているということだ。
さらにマクニカでは、最初のスコープとして生産シミュレーションから始めてみることをおすすめしている。シミュレーションは、簡単にできないものである。ただ、何のデータがないのか、どんなデータがあるとシミュレーションできるかということが明確になるので、デジタル活用という壮大な話をする中で、ある種コンパスのような役割を果たすことが多い。
阿部氏は最後に、「業務プロセスや考え方そのものを変革するのがDXだと考えている。大きな変換点に貢献していきたいと考えている。」と語り講演を締めくくった。
参考:このイベントの他の記事は次のリンクから見ることができます。
ウイングアーク1st株式会社のウェビナー「アフターコロナに挑む製造業。デジタルの活用で、変化に強く儲かる工場を考える2days」
無料メルマガ会員に登録しませんか?
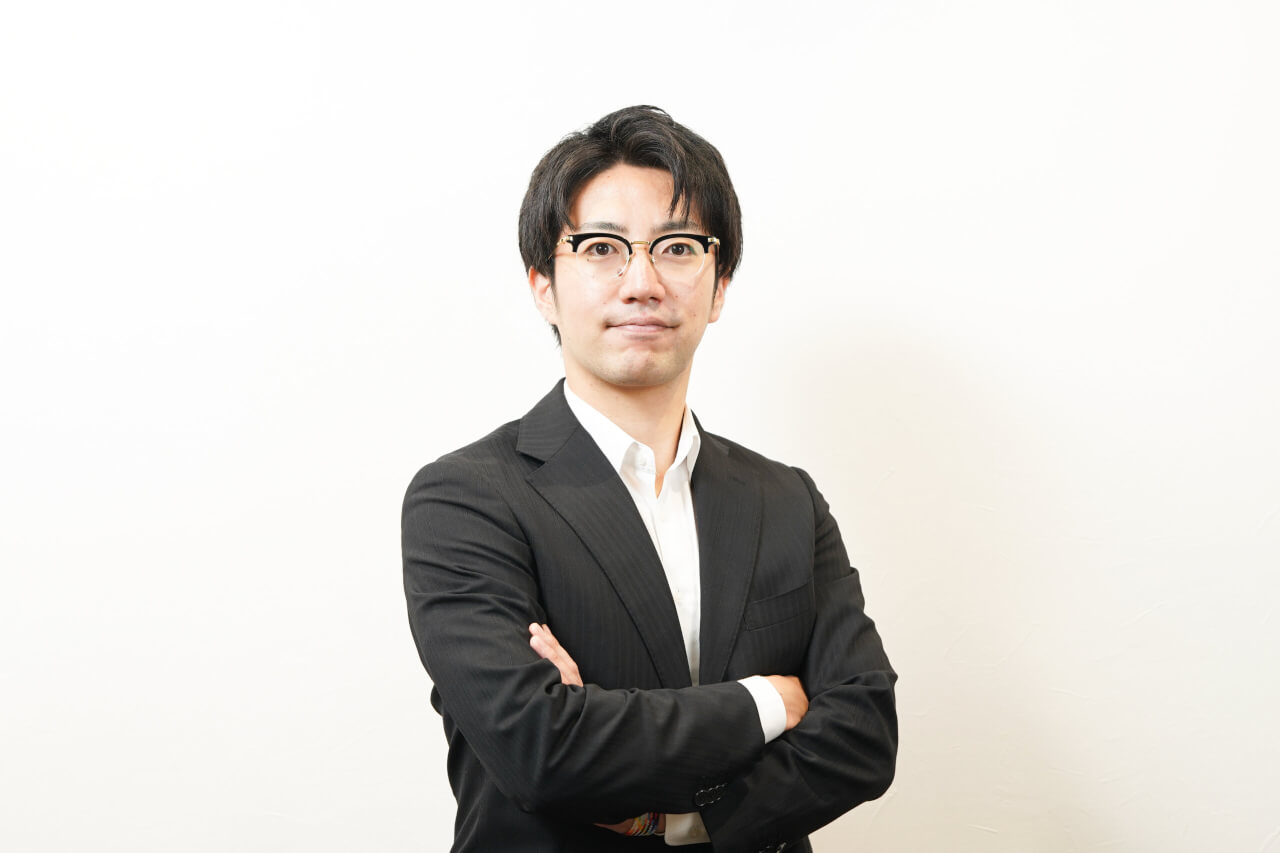
大学卒業後、メーカーに勤務。生産技術職として新規ラインの立ち上げや、工場内のカイゼン業務に携わる。2019年7月に入社し、製造業を中心としたIoTの可能性について探求中。