PoC事例3:ダッシュボード化・KPIマネジメント
樋口:3つ目のPoC事例は、ダッシュボード化・KPIマネジメントです。
稼働データを全て集約、整理クレンジング、紐づけ、関連付けを通じて、より工場の状態、パフォーマンスがリアルタイムで見れるようにするという取り組みになります。
この取り組みでは、いきなりセンサーデバイスをつけてデータを収集するのではなく、まずは関係各社へヒアリングを行いました。
どんな項目で収集するのか、どんな細かさで収集するのか、その結果何を評価するか、指標が悪化した時のアクションはどうするか、OEEを取得したあと、「で、どうするの?」を考えそれぞれの管理スタイルに合わせてソリューションを考える必要があります。
古いプラントほど、工程の設備機器の世代やデジタル化の難易度がばらばら、言語が不統一という状態にあり、いろんな種類の情報データを全て取得しようとするとシステム構成が複雑になってしまい、費用がかかり難易度が高くなります。
マネジメントそのもののスタイルさえ不確実性で変わっていくかもしれない中で、どんなことが出来るといいのか、それを達成するためにはどんな道具が必要かを決めていく必要がある、個性の出る分野だと考えています。まずはどんな管理がしたいかに重点を置いて掘り下げることにしています。
小泉:下からデータをとろうとすると、産業機械一つ一つがデータを取れるようになっているのかが気にかかってしまいますが、先にやりたいこと・取りたいデータを元に仮説を立てていけば、どの機械からどんなデータをとればわかるのかにたどり着ける。上から見たほうが実は解決しやすいことは多いのですね。
OEEというと工場全体が見えなければならないという印象があり、ここで大きな話をしようとしすぎてしまうと実態のデータが取りづらいということが起きます。目的、仮説から取得したいデータまで掘り下げていくことによって、ダッシュボードの価値が見えてきますね。
樋口:職位や立場、抱えているミッションによって見たいデータ、デザインは変化します。そういったことに対応できるものを備えた上で、どんなデータが見たいのかをそれぞれにヒアリングしていく必要があります。
PoCの現在の到達点としては、立ち上げ中の最新鋭の工場でごく一部のプロセスにおいてリアルタイムでPCやタブレットで稼働状況、パフォーマンス評価、さらに承認プロセスまで確認ができるようになっています。ここまで来てやっとM3.0(「工場全体」の自動化・データの解析や活用)レベルで進んでいる姿になってくると思います。
スマートファクトリー化は関係者間で共通理解を得るところから進む
小泉:ちなみに、このPoCの予算の取り方はどう行っているのでしょうか。
樋口:小さなスケールのPoCであればスマートファクトリー部の自前の予算でできます。実装レベルの技術を入れるにあたっては、それぞれ関連企業が投資を行うかどうかを判断する必要があります。
小泉:製造業は組織の部署間の壁があると思います。横串でビジネスプロセスを見るのは難しいですよね。
樋口:一筋縄ではいかない状態になっています。なので、スモールサクセスを小さな領域でいいので見せられる状態にして、それをアピールの材料として、その前後関係者の理解を得ていくことを地道にやっていく必要があります。また、データを並べてみて、可視化をし、どういうデータが取れるということを見せることによってコミュニケーションが取れるようになっていきます。そしてそれがフックになり、現場の方からもっとこうした方がいいと意見が出てくる、開発が加速していきます。
小泉:まずは作ってみることが大事なんですね。つなぐというと、OEEとつなぐ経営システム、ERPなどもあると思いますが、そういったものと現場のシステムとをつなぐ取り組みはされているのでしょうか。
樋口:ERPで原価計算を回すなど、ERPとコスト管理と製造部門との繋がりは強いと考えています。一方で、工場の出口のところで、デジタルで繋がっていない、分断されているところといえばSEMです。デリバリー関連はまだ隔たりがあると感じており、これからテコ入れをしていく段階です。
小泉:サプライチェーンのつなぎかたについての取り組みはどういった状況なのでしょうか。
樋口:需要予測と在庫補充計画、生産計画を行う際に手作業が発生しており、主に日割りの生産計画を行うところで工場の人が手で割り振っているというのが現状です。
こういった作業は技能差が出てしまいがちです。ベテランと新人で、習熟度合いで差が出ることはストレスとなるため、ストレスは取り除いていきたい。そこをどう洗練させられるか考えています。
小泉:工場全体を一つの箱と捉えた時に、前後を含めてどういった原価の状態になっているのかを見ることは、天候だったり、トレンドだったりに左右されるため、自動化が難しいのではないかと言われていますが、現場のデータが取れることで改善されるのでしょうか。
樋口:欠品をさせずに在庫水準を低く保とうとする、CCC(※1)をどれだけ短くできるかというところにフォーカスがいってしまうと、難しさだけになってしまいます。しかし、これが生産計画の立て方によって工場の生産コストはこう変動する、それは有効稼働率が生産計画変更によってこれだけ変動する、ということがすぐに確認できるようになれば、コスト最適で、かつ在庫もそんなに増えない生産計画思考でいこうという議論を同じデータを眺めながらいろんな部門の人を交えて行い、共通理解を作れるというだけで、レベルアップになるのではないかと思います。
小泉:まさにスマートファクトリーですね。工場の状態がわかっているから、周辺のプレイヤーと折り合いをつけることが出来る。新設工場であれば、状態も取りやすいでしょうし、システム間連携、既存の外側にあるシステムとの連携、PLMとの連携もやりやすいのではないでしょうか。
樋口:現時点で月次で回している原価管理の管理サイクルを週次や日次でやるところまで管理サイクルを縮めていくのはまだまだ難しいです。
小泉:壁は高いですが、越えたら効果がありそうですね。
今までのように大量に作ればいいという考えは変わってきている状態にあって、なるべく、状態管理をしていきたい、細かく無駄をなくしていきたいと考えている人は多いと思います。そこはこれから先の課題になっていくのかもしれないですね。
樋口:はい、サプライチェーンマネジメント、またその先のS&OP(※2)を遅まきながらでも考えておくと、不確実性への対応力の武器になるのではと考えています。
※1 CCC(Cash Conversion Cycle):企業が原材料や商品仕入などへ現金を投入してから現金化されるまでの日数で、資金効率を見るための指標。
※2 S&OP(Sales and Operations Planning):経営層と生産や販売、在庫などの業務部門が情報を共有、意思決定速度を高めることでサプライチェーン全体を最適化していく手法。
無料メルマガ会員に登録しませんか?
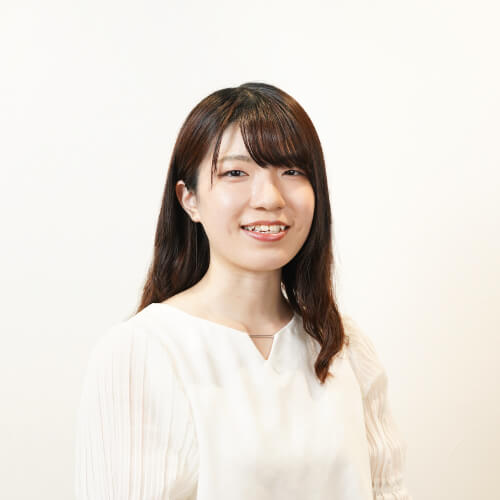
現在、デジタルをビジネスに取り込むことで生まれる価値について研究中。IoTに関する様々な情報を取材し、皆様にお届けいたします。