「スマートファクトリーというと、いろんなことを言う人が多くいて、私はこのIoTNEWSをはじめた当初「分かりづらい」と感じたものだ。
というのも、当時から(今もだけど)グローバル企業も、零細企業も、部品メーカーも、完成品メーカーも、産業機械メーカーも、工場で完成品を組み立ててる企業も、なにもかも一緒に語られていた。
その上、産業用ネットワークや、セキュリティの話題もあり、挙げ句の果てに、インダストリー4.0がどうだ、ドイツが進んでいるとか、中国に負けているとか、本当にいろんなことをいう人がいて、一体何を根拠に、どのレイヤーについて、そういう議論を展開しているのだ?と思うことがとても多かった。
そこで、今回以降、何回かに分けて、スマートファクトリーの基本について、これらのことを随分長い時間をかけて、縦に横にと整理した。
皆さんも私と同じ思いをしなくてよいように、整理した内容をわかりやすく解説していきたい。
これを読めば、スマートファクトリーの基本と、何が課題か、対応のポイント、がわかるはずだ。
目次
この続きの内容と目次
- 工場のIoTがスマートファクトリーなのか?
- 「つながる工場」とはどういう工場なのか
- つながる工場では、すべての産業機械がネットに接続する必要があるのか
- ライン全体の死活監視と3つの効果
- AIも活用される、最新の工場向けソリューション1
- AIも活用される、最新の工場向けソリューション2
工場のIoTがスマートファクトリーなのか?
スマートファクトリーというと、「工場のIoT」のイメージを持つ人が多い。また、その一方で、「サプライチェーン全体の最適化」を指す人もいる。
実は、これは解釈の問題なので、どれが正解ということではないのだが、幾つかのレイヤーに分かれる、ということはまず最低限知っておくべきだ。
工場の中には、「ライン」と「ラインを構成される産業機械」がある
なぜ、こんな当たり前のことを言うかというと、ラインの最適化、生産性の向上といった工場全体の話と、後述する、産業機械の予知保全や、マスカスタマイゼーションの実現などのテーマがごっちゃになって議論されているからだ。
そこで、今回は「工場のIoT」について、しかも、「ライン」にフォーカスして解説する。
まず、「ライン」というのはイメージがつきやすいと思うが、原材料を入れると、何らかの完成品が出てくるという一つの流れのことだ。
そして、ラインを構成するものが様々な「産業機械」で、例えばベルトコンベアーや、ロボット、品質検査器など様々な機械がある。
また、ラインには途中で人が作業をする場合もあって、一言でラインといった時、人と機械の両方が作業をしているケースも多い。
最近では、「ロボットが人と協働する」という話題がでることがあるが、ロボットというと当然鉄の塊なので、すごい力で動くロボットが人にぶつかると危ないから、通常は人とロボットは近くにいない。一方で、「協働するロボット」の場合、人とロボットが近くにいて、例えば人が作業してできた成果物をロボットが次のベルトコンベアーに流す、といったようなことを実現するのだ。
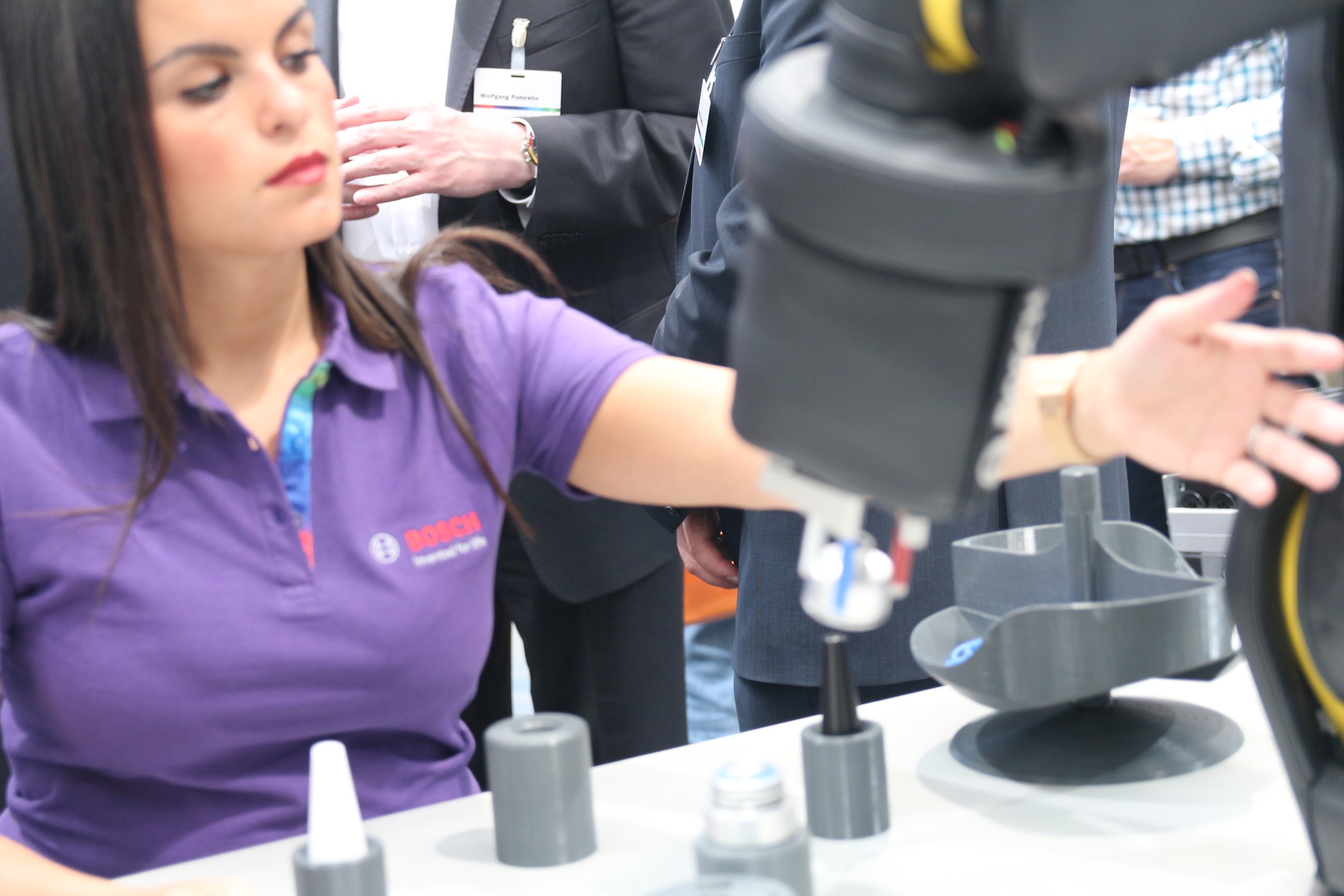
ここまでで、このロボットや産業機械と呼ばれるモノ、そして、産業機械をつなぐネットワーク、ゲートウェイ機器などが工場のIoTにおける最小単位だと、まず理解してほしい。
「つながる工場」とはどういう工場なのか
ラインに配置された、産業機械はコントローラーと呼ばれる産業用の小型のコンピュータから指示をうけて動くのだが、産業機械とコントローラーをつなぐネットワークの決まりごとがそれぞれ違っている場合があるため、「つなぐ」と言っても実際は簡単に繋がらない。
もう一点、最近作られたの産業機械はともかく、旧式の産業機械ではそもそも「ネットワークに繋げる」という発想がなかったため、データを取得したり指示を受け取るような口が準備されていない場合が多い。
しかし、設備は高額で、大抵の場合複数年かけて減価償却されるというタイプのものなので、簡単に新しいものに取り替えるということができず、ラインを構成する産業機械のすべてから機械の状態を取得するということは、簡単ではなかった。
皆さんは、はじめに「つながる工場」と聞いた時、どう思っただろうか。おそらく多くの人は、「すべての産業機械がネットワークにつながることで、何かいいことがある」ような工場、と想像したのではないか。
実際、みなさんのご想像の通り、本来「つながる工場」は、すべての産業機械から産業機械の情報を取得するべきだと私も思う。
つながる工場では、すべての産業機械がネットに接続する必要があるのか
しかしここで、一旦このボトムアップ的な考え方から脱して、トップダウンに見てみよう。
そもそも、工場のIoT化を考える際に起こる疑問としては、「つながる工場とは、工場の産業機械からデータを取ることが目的なのだろうか?」という疑問だ。
もちろん、データを取得するのは、「何か」をやるための手段にすぎない。では、その「何か」とは何なのか。
結論を言うと、工場のIoT化の目的は、「コスト削減(生産性改善)」と「機会創出(ビジネスの拡大)」の2つなのだ。
ライン全体の死活監視と3つの効果
まずは、ネットワーク対応されていないような割と古い産業機械で構成されているような工場のラインをイメージしてほしい。
工場のラインには、たいてい信号灯がついている。この信号灯自体は、赤、青、黄色で状態がわかるようになっていて、例えば赤くなっているとラインが止まっているということを表すのだ。
これがあることで、何ラインもある工場でも、それぞれのラインがどういう状態であるかを目視することができる。
最近よくあるのが、この信号灯の色を光センサーで感知して、ランプの色の情報を無線で飛ばし、コンピュータで情報を集約するタイプのものだ。
その上で、「アンドン」に表示したり、「モニター」に表示したりするのだ。これをすることで、「どこのラインがどの時間からどの時間で停止していたか」がわかる。
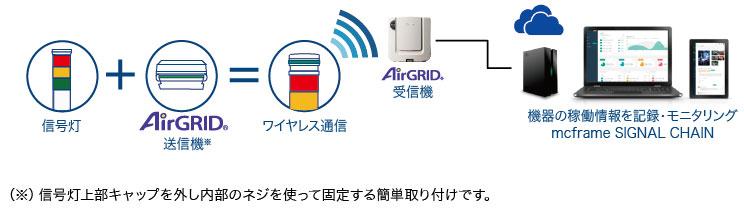
これでどういうの成果がでるというのだろう。
稼動状態が「可視化」できるという回答では、「見てどうするの?」という疑問が湧くだけだ。
効果1:厳密な稼動監視により、問題解決が緻密になる
これまでも、業務日報をつけていた工場は大半で、ラインが停止するということは大きな問題なので、当然記録もとっていた。
しかし、このやり方は決して厳密ではなかった。
というケースが多い。
そもそも、例えば10ラインを管理しているラインマネージャーがいたとして、毎時同じ時刻にそれぞれのラインで生産した個数を計測し、同時に記録することができるのだろうか?分身の術でも使って、同時に計測しないとそんなことはわからない。
それに加えて、障害発生時も、同じだ。工場のいたるところで起きる障害の発生時刻と完了時刻をきちんと記録できるとはとても思えない。
つまり、このアプローチでは、
といったことが起きてしまうのだ。そして、完成品を店舗で手に取っている人には全く理解できないことだと思うが、実は、これはどの工場でも日常的に起きている。
また、ライン自体に問題がなかったとしても、別のところで問題が起きるケースはある。
面白い例だと、生産能力が他工場よりも著しく低いとみられていた工場があったため、ラインの死活監視をしてみたところ、それほど問題がなかったという。
そこで、原因を追求したところ、工場が資材を発注しているにもかかわらず、届いていない場合が多く、生産そのものができていなかった、ということが分かったという例もあるくらいだ。
実は、こう言ったことも、監視をしてみないとラインマネージャーが魔女狩りにあうのだ。
つまり、工場の生産性改善をやってきたと言っている多くの工場では、「一つの製品ができるまでに要する時間」も正確に計測できていない場合は多いし、その結果、「単位時間当たりの生産量」も正確に測定できていない場合が多く、「問題発生時の停止時間」も、「対応に要した時間」も正確には記録されていないということが起きているのだ。
かの有名な「トヨタ生産方式」でも、担当者がラインの横でストップウォッチをもって、生産にかかる時間を測っているという。すごい速度で自動化された産業機会が動く現場で、これで正確に測れているとはとても思えない。(トヨタの工場というはなしではなく、まだネットワーク化されていないような産業機器を使い続けているような工場の生産性改善としての話なので誤解しないでほしい)
つまり、まずはラインの死活監視と、生産時間を可視化をするというのが、工場の生産性改善の第一歩となると言えるのだ。
これがわかることで、問題箇所が掘り下げて議論できるため、解決すべき課題を見出すことができる。
効果2:改善効果がすぐわかるため改善モチベーションが向上
死活監視により、課題が明確になる。その後はこれまでもやってきた、いわゆる改善をするのだが、それでめでたく課題が解決できたとしよう。
誰しも課題を解決した以上、「解決できた」という実感を持ちたいものだ。
しかし、根拠がある解決策ばかりでなく、「とにかくやってみよう」という解決策も多い中、実際に改善したのかどうかについて、ビフォア・アフターを計測していないとわかるよしもない。
この、ラインの稼動状況をモニタリングするということで、結果、改善されたことによるメリットも計測しやすくなるため、改善へのモチベーションもあがるというのだ。
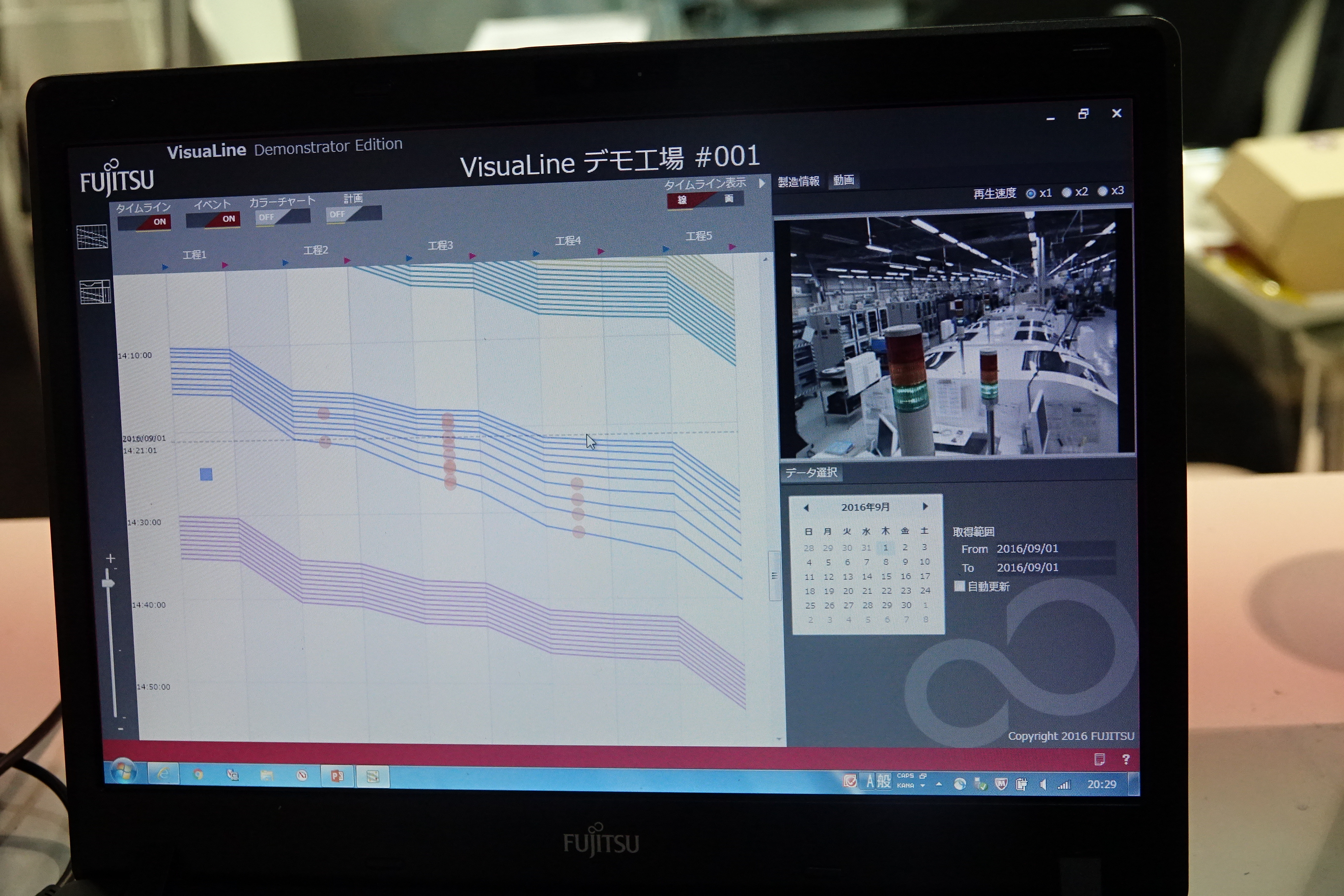
効果3:現場の生産性向上によって、無駄な投資が不要に
ラインの生産性を向上することで、ライン増強を検討していた工場でも、既存のラインでまかなえる可能性がある。
実際に、IoTによって、生産性を69%改善した企業では、これまで6ラインあった工場で2ライン増強しようとしていた投資をやめたのだという。
また、労働生産性にも寄与していて、これまでは、目標生産数に対して、「人」が無理やり結果を出そうとしていたため、残業や土日出勤も当たり前だったという。
しかし、明確な指標に従って生産性を改善した結果、残業も減り、土日出勤もなくなったというではないか。
その結果、この企業では、労務費が10,000,000円単位で削減できたという。
これは、それほど大きくない工場の例だが、実際に取り付けられているセンサー類は月額数万円から始められるもので、固定資産となる高額なラインの増強も、固定費として計上される人件費も削減するばかりか、時間の空いた人が他のサービス(この企業の場合、コンサルティングサービス)へと振り分けられあらたな事業を生み出しているのだというではないか。
現実に立ちふさがる問題と解決策
先ほど触れたとおり、実際にはすべての産業機械が新しいわけではない。古い産業機械が現役で動いているケースが大半だろう。
そういった産業機械を使って、ラインに材料が流れ込んできてから、完成するまでの時間をどうやって正確に測れば良いのだろう。
産業機械が信号灯と連携していて、製造中だけ信号灯が緑に光るという工場であれば、信号灯を先ほど説明したやり方で繋げば良い。
しかし、そういうことができない機械の場合はどうすれば良いのだろう。
これは産業機械ごとに稼動状態を何らかの形で検知するしかないのだ。
例えば、稼動中にランプがつくのであれば、ランプの電極にセンサーをつけて、電流が走ったらそれを検知する、といったやり方もある。
こうやって、本来計測したいこと(ラインの稼動状態)から、なにのデータを取るべきなのかを明確にして、取得していくことで本当に必要な情報が取得できるのだ。
多くのサプライヤーが、高価なマルチセンサーを売りつけようとしてくるかもしれないが、マルチセンサーを付けたからといって、そのセンサーが取得する情報が必ずしも必要な情報であるとは限らないことに注意してほしい。
AIも活用される、最新の工場向けソリューション1
AIというと話しが発散するので、「画像認識技術を使った」と言い換える。
GoogleやFacebookが写真をみて、この人が誰、というのを言ってくるのと同じ仕組みだ。
この、画像認識技術を使った品質検査をやろうとしている企業がある。
例えばプラスティックのバルブを作っている企業だ。プラスティックバルブは、製造の過程で傷がつくことがある。
品質検査の段階でこの傷は取り除かないといけないような製品なので、最終的に人が時間をかけて傷がないかをチェックしていたというのだ。
しかし、このチェック、相当な熟練が必要で、当然時間をかければ誰でもできることなのだが、時間をかけてはいられない。
そこで、カメラで製品を撮り、傷がないかをAIがチェックするというのだ。
AIは画像認識の技術を使うために、多くの学習データが必要になる。
そこで、傷のついた製品や汚れている製品などをサンプルデータとしてたくさん準備し、AIを鍛えるのだ。
こうして完成された学習モデルをつかって品質検査を始めているのだという。
かなりの精度で傷を見つけてくれるから、一応人もチェックするが、相当な時間の短縮と習熟度に依存しない品質検査が実現できるのだという。
しかし、このやり方にも課題があって、カメラは何個準備して、どの方向から撮れば問題が起きないのか?ということだ。
品質検査をしているのに、それ自体のクオリティが低いのは本末転倒なことはおわかりだろう。
こう考えると、まだまだこのサービスにも改善の余地があるとともに、今からやれば特定目的の品質検査には使えるサービスが作れる可能性があることもわかるだろう。
AIも活用される、最新の工場向けソリューション2
もう一つ、紹介したいのが、生産技術そのものをAIに覚えさせるというやり方だ。
何回か後に説明するが、インダストリー4.0の流れから設計と製造をつなげようという動きがある。
というのも、設計差と製造担当の間に大きな壁があり、新商品の開発をするというと、設計内容を製造担当に説明する。製造担当は持ち帰り、既存のラインで生産できるのかを確認、実際に試してみる。問題があれば設計者にフィードバックし、必要な産業機械を購入する申請を行う。これを何度か繰り返し、ラインを完成させる。ということをやっていくのだ。
しかし、最近は生産機械についても仕様がデジタル化されているので、産業機械の設計情報をデジタルデータとして格納し、デジタル空間上に展開することで、擬似ラインをデジタル上に作ることができる。
そこに、設計データを流し込めば、既存のラインで生産可能かどうかがある程度判断できるというのだ。
この考え方を、さらに発展させると、実際にラインを動かしてみると思ったように生産できない場合がある。今までのやり方だと、これを職人技でチューニグするという流れになるのだが、このソリューションでは産業機械のコントローラーにAIを搭載して学習させていくのだ。
こうやって製造物を計測し、仕様通りになっているかどうかもデジタル的に判断し、その結果を産業機械のコントローラーにフィードバックする。
産業機械は何通りものサンプルを作りながら、一番最適な動きを見出すというのだ。
これが、通常人では思いつかないような手順や動きをするというから興味深い。
こうやって、AIを活用して工場のラインを最適化していくということも実際に起きているのだ。
工場のIoTはこれで全てか?
実は、まだ語り尽くせていないことがたくさんある。
工場のIoTだけを語るとしても、ラインを構成する個別の産業機械のIoTの話しがあるからだ。
他にも、ラインとしての改善した結果、生産効率が上がったとして、それを営業してもっと使ってもらわなければならない。製造した製品を物流網を使って運ぶということも考えるべきだろう。
冒頭に述べた通り、スマートファクトリーの範囲は広く捉えるとサプライチェーンの話になっていく。そこで、次回は、ラインを構成する産業機械の話をしていきたい。
この記事に関するご意見、質問などは以下からどうぞ
エラー: コンタクトフォームが見つかりません。
無料メルマガ会員に登録しませんか?
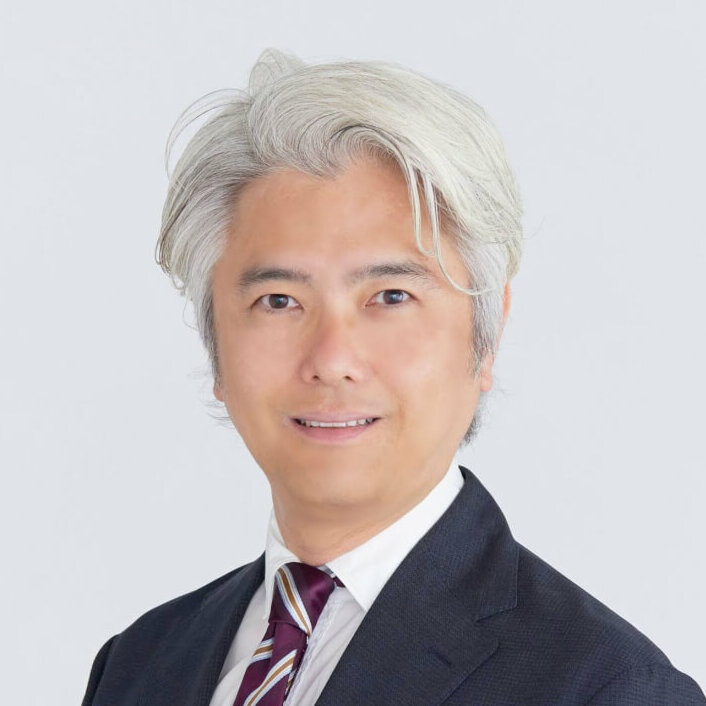
IoTNEWS代表
1973年生まれ。株式会社アールジーン代表取締役。
フジテレビ Live News α コメンテーター。J-WAVE TOKYO MORNING RADIO 記事解説。など。
大阪大学でニューロコンピューティングを学び、アクセンチュアなどのグローバルコンサルティングファームより現職。
著書に、「2時間でわかる図解IoTビジネス入門(あさ出版)」「顧客ともっとつながる(日経BP)」、YouTubeチャンネルに「小泉耕二の未来大学」がある。