株式会社 FA プロダクツは、製造業向けに、既存設備の改造無しで稼働監視が実現できるセンサパッケージを発売。 信号横取りセンサ「ICS シリーズ」として販売を開始したということで、詳細をインタビューした。
- お話いただいた方
株式会社 FAプロダクツ 代表取締役社長 貴田 義和氏(トップ写真)
株式会社 FAプロダクツ Smart Factory 事業部 高見 守氏
- 聞き手
株式会社アールジーン 代表取締役/IoTNEWS 代表 小泉耕二
前回インタビュー
・スマートファクトリーで本当にやるべきこと -FAプロダクツ 貴田氏インタビュー
小泉: 2017年の夏ごろに一度インタビューをさせていただきましたね。近況について教えてください。
貴田: 去年発売した設備の稼働分析のパッケージは50万円ということもあり、おかげさまでかなりのお引き合いをいただきました。現在は、導入後のカスタマイズのニーズが出てきており、今またチューニングをしています。
さらに生産シミュレーターの導入は、ここ2年で一気に盛り上がってきています。生産ラインや物流ラインのシミュレーション技術は、10年以上前から日本に入ってきていますが、実はほとんど広がっていませんでした。世界では広まっているのに日本で広がらない理由は、日本人はものすごく優秀で、すり合わせ技術に長けているからです。
それが、この少子高齢化の世の中で人材不足になってきて、IoTで現場のデータが集まり始めてくると、さすがに標準化しなきゃいけないということで、シミュレーションソフトウェアが売れ始めてきました。スマートファクトリー化に向けた流れに、非常に手応えを感じています。
ロボット関連では、MUJIN、Life Roboticsなど、それぞれのパッケージ作りがほぼ完了いたしました。今春、弊社の一連のプラットフォームを「スマートファクトリーコンダクターLABO」というネーミングで、10メーカーほどのロボットの最新システムを並べたスマートファクトリーセンターを開設する予定です。
ロボットシステムと稼働状況や予知保全のシステムが連動して、スマートファクトリー関連の最新技術が見られるようになっている複合施設で、栃木県小山市に竣工します。結構大きいスペースで、1階がラボ、2階がセミナースペースになる予定です。
スモールスタートしよう
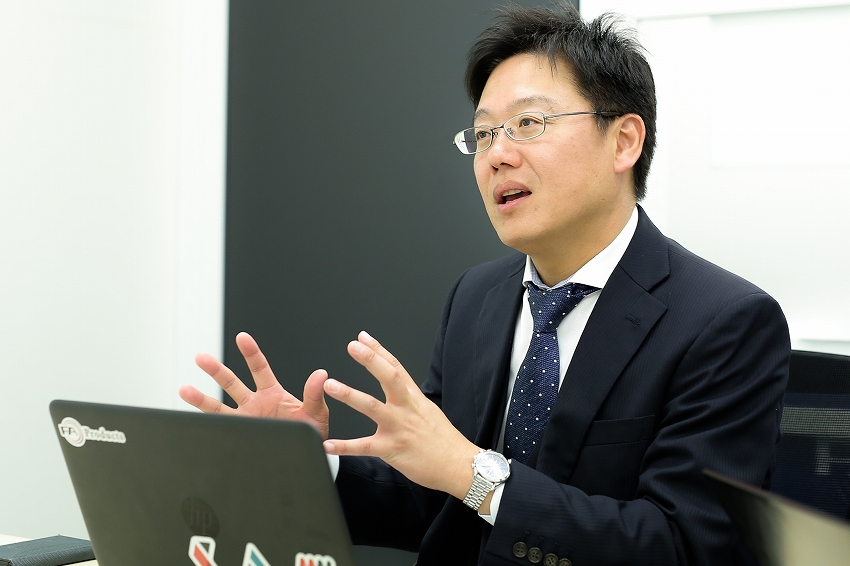
貴田: 弊社からのご提案としては「スモールスタートしましょう」ということです。ただ、スモールスタートをするのに最適なシステムとして、弊社の設備稼働監視パッケージを売っていく中で、すべての設備に対応できるかというと、実はそうではないケースも最近出てきています。なぜかというと、老朽化している設備が多いからです。
その中でも、どういう設備が今でも現役で動き続けられているかというと、加工工程の装置で、特に成型機や工作機械、プレス機などです。
材料を溶かしたり、穴を開けたり、プレスをしたりという素材を成型するマシンの中身の構造は実は単純で、しっかりメンテナンスしていくと20年でも30年でも使えます。われわれの50万の稼働監視パッケージは、国内外含めて300種類以上のコントローラに対応していますので、PLCなどの通信できる機器があれば概ね対応できますが、20年・30年前の設備ではさすがに内部を動かしているコントローラからデータを取れないという現状があります。
加工ラインや成型ラインは人も介在するし、マシンの能力に生産の能力が左右されます。そういうところこそ、設備の稼働分析をすると大きな利益が残せます。こういったところにレトロフィットする機器を作ったのが、今回の製品になります。
「スマートファクトリーコンダクター」という一つのプラットフォームの中で、われわれのさまざまな製品をパッケージとして発売をしていきます。
製造業でIoT化、スマートファクトリー化をスモールスタートするというと、上記4つの管理のどれかを効率化するという話なのですが、どの企業も中央二つは難しくて、今あまり手が出ていません。パッとIoTを進めるのは、稼働分析か予知保全でないと難しいという中で、稼働分析は非常にニーズが高いです。
ほとんどのPLCメーカーで、ノンプログラムでゲートウェイにデータを引っ張ることができて、モニタリングできたりタッチパネルの機能がついていて色々入力できたり、データをOPC-UA規格で上げることできます。これで50万という安いパッケージです。
こういう新しいものを既存の設備に導入するときには、1.改造しない、2.仕事が楽にならないといけない、3.安くないといけない、4.入れた後にユーザサイドでカスタマイズできなければならない、というこの4つに対応したものじゃないと売れません。
信号横取りセンサ「ICS シリーズ」
貴田: 今回の新製品の紹介になりますが、先日、稼働分析パッケージのオプション品発売が決定いたしました。単なる稼働分析のパッケージのオプション扱いにするには、ちょっともったいないぐらいだと思っている製品、信号横取りセンサ「ICSシリーズ」についてご紹介します。
似ているのは電流センサやCTと呼ばれるものになるのですが、それとは少し仕様が違うものになります。今回発売した信号横取りセンサ「ICSシリーズ」は、製造設備の運転中ランプや起動スイッチなどの信号線からI/O信号を横取りしてくるイメージになります。
多くの機器はDC24Vなどの直流電源で動いていますが、そのタイプのセンサーは世の中になかなかありません。でも、これはパチッと挟み込むだけのものになっていて、改造工事等々は一切いらずに、配線のところに挟み込んでもらうだけです。
だから配線変更も切断もしない、機器の構成変更もない、設備を止める必要もありません。
一つの設定が大体7秒ほどです。一つの工作機械で取りたい点数は多くて10点くらいなので、10本分とすると単純計算で70秒ほどで配線が済んでしまうというのが一番のポイントです。
加工機、成型機、NC装置、プレス機、鋳造マシンがターゲットになります。中小企業になればなるほど古い設備を持っているので、この手のニーズは高いです。
高見: 既存の設備に手を加えた段階で、設備の補償の対象外になることもあるので、手を加えずに設置できるというのが重要なポイントでした。さらに、24時間連続操業している機械もあるので、稼働中でもつけることができるのもポイントです。他にも、対環境性能も非常に重視されているので、温度やノイズなど耐環境性を考慮し、FAの現場で使えるようなセンサを企画しました。
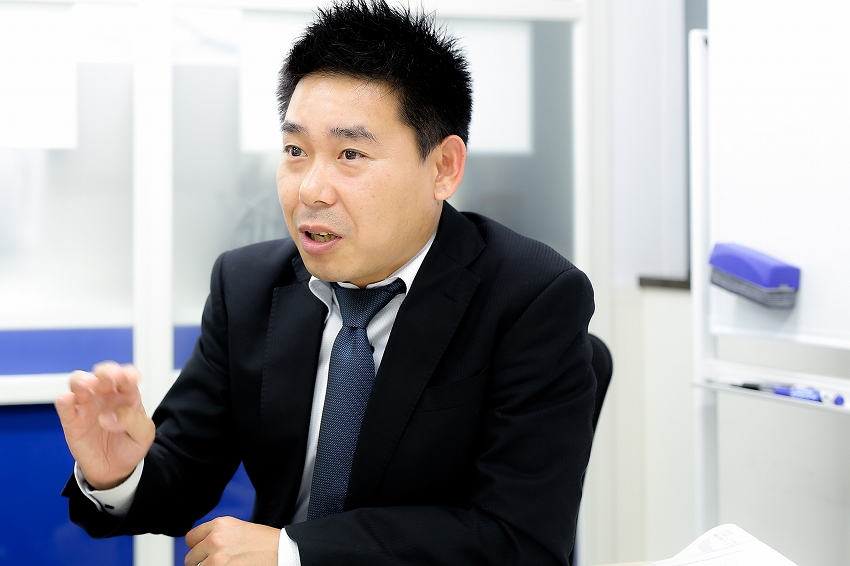
貴田: 組み合わせとしては、信号横取りセンサで信号線の電流値を検知して、中継ボックスによってON/OFFの接点出力に変換しています。今回、この中継ボックスも標準で作っているのでDC24Vだけ給電できれば汎用センサ感覚でこの信号横取りセンサを活用することができます。
今、この製品をヒアリング回ったら反響が大きいので、単体で販売してもニーズがあるのではと思っています。ですので、信号横取りセンサをオプション扱いではなく、ちゃんと製品としても扱ってプレス発表いたしました。
小泉: これは、なぜこの形にしたのでしょうか? つまむタイプの製品も見たことがあるのですが。
高見: つまむタイプだとどうしても隙間が出てしまうのですが、これだと金属で全周覆うことができます。そうすると外れにくく、ノイズ対策にもなります。周辺のノイズを逃がすというとちょっと語弊があるかもしれないのですが、取りたいのはあくまで信号線の信号なので、これ以外の信号をシャットアウトするようなカバーがわりです。
小泉: 電気のわからない人に説明を補足したいのですが。例えば、子供のころに理科の勉強で、電気に電池をつないで豆電球をつけた覚えはみんなあると思います。線の上に何かをセンシングするものをつけたら、中で電流が流れているというのが取れるイメージがいまいちつかないと思うのですが、センサだから取れるということなのでしょうか。
高見: それでいくと、確かにセンサでセンシングして検知しています。フレミングの左手の法則になってくるのですが、電気が流れると周りの磁場が変化します。このセンサはその変化をとらえています。ただしその変化が信号線に流れている直流電流の場合、非常に微弱なので、簡単にはセンシングできないのが実情でした。また、微弱な故に先程お話した生産現場に存在するノイズ対策が重要になります。
小泉: なるほど。磁場の変化をとらえているわけですね。電気自体が通っているわけではないのですね。生産現場のノイズ対策も考慮しているというのはすごく説得力があっていいなと思います。古い設備から信号を取るために、他の方法って世の中にはなかったのでしょうか?
貴田: 例えば、センサーやRaspberry Piなどを自前で用意して、配線を分岐させてI/Oに変換したり、光センサをランプにつけて取り込んだりということはやろうと思えば比較的簡単にできます。しかし、「それを現場に10点も20点も並べて、本当にできますか?」というと、環境的にアウトになってしまいます。もちろん弊社の信号横取りセンサは、FAの現場で使える信頼性と対環境性をそなえています。
小泉: 信号横取りセンサが売れ出すと、PoC時代が終わってきたなと感じます。
貴田: 実は、去年われわれが設備の稼働システムを見せていただいた、ある自動車メーカーの一次サプライヤーさんの、加工機のある事業所の話です。そこでは新規のライン300台分くらいに最新のファナックの加工機が入ってくるので、簡単にデータが取れるそうです。
しかし、今現場にある350台の工作機械に関しては一切データが取れないのでどうするか、という話になっていたのが、最初の取っ掛かりです。
われわれも今まではPCベースでOPCサーバーを活用し、間にPLCを入れるなどしながらソフトウェアを開発して進めていたのですが、もう少し簡単にできないかと考えていました。
その間にお客さまはRaspberry Piでやり始めてしまうのですが、なんか違うよねというところから企画がスタートしていて、皆さんに聞いて回ったら皆さん同じことで悩んでいたというところが発端です。
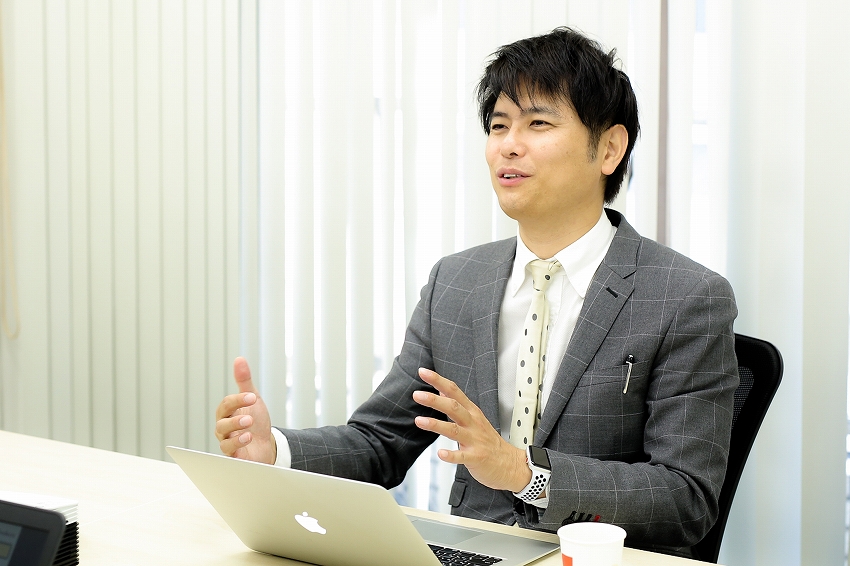
/IoTNEWS代表 小泉耕二
小泉: 導入するのはどのくらいの日数がかかるのでしょうか?
貴田: 基本的な稼働監視であれば1日かからないです。画面をカスタマイズしたいというお客さまもいるので、簡単に対応ができるようになっています。日本の生産技術とか、保全のお客さまは、PLCやタッチパネルのプログラムができる技術を持っています。この稼働監視パッケージに使われているタッチパネルは、デジタルや三菱電機といった日本の大手メーカー製産業用タッチパネルと同じ感覚で、お客さま自身でご自由にカスタマイズいただけます。
営業を一緒に回っているときに、お客さまにこれを見せると「ちょっとさ、画面の変更とか、現地での工事も全部見積もってよ」と言われるのですが、一つ一つ対応するのは弊社も難しいのです。
ただ、裏を返すとニーズが見えます。これは「産業用のタッチパネルですよ」と、ソフトウェアを見せて作画の方法を教えると、「なんだ、普段使っているタッチパネルと一緒じゃん」と。つまり、1年目の若手でもできますので、すぐにご購入・運用いただける状況です。中小企業向けのパッケージとして作ったのですが、8割大手で売れています。
大手企業では横断的な部署やプロジェクトチームができていて、最新のラインをモデルケースとしてトライをしているのですが、他の事業所にはその技術は全然行き渡っていません。しかし、ローカル側も今のままだったら人も採用できなくなってしまうし、設備をマックス動かせる稼働分析をしなかったら、この先やっていけないという危機感を持っています。
貴田: 現状の稼働分析の予算は、100万から200万円です。こういうもので設備の稼働データを取ると、実質の稼働率や効果がわかるようになります。そうすると、彼らはもっと積極的に現場のデータを取って、もっと本質的なところを見ようと思うはずで、そこに今後予算がつくはずなのです。
今、大阪の三次サプライヤーさんでは、1回100万円で8つの設備の見える化だけを実施して、ある程度うまくいくことが見えたるので、大阪のもう1つの工場と、フィリピンの工場を全部一元で結んで同じことをやりましょうという企画になっています。
小泉: 同じことで同じ軸で見ると、生産力が全然違うことがあるそうですね。
貴田: 全然違います。僕もいろいろ探ってみたら、売上げが20~30億規模の中小企業は自動車業界もまぁまぁ活況で、さらにiPhone周辺部品を作っているところは非常に忙しいようです。
先日、ある経営者に「今稼働率どれくらいですか?」と聞いたら、「何言ってんだよ、貴田ちゃん、100%に決まってんだろ」とおっしゃるのです。彼らは、入口と出口でしか見てなくて、工場全体として今受けきれないほどオーダーがあると稼働率が100%だと思っています。
おそらく実際に可視化してみると100%ではないはずです。あまり気にしてない会社だったら、実質稼働率は半分ということもあります。さらに、納期であおられているので「設備あと3台くらい買うか」とおっしゃってもいたのですが、生産性を上げた方がコストかかりません。
例えば、なぜ止まっているのかという理由だけを、タッチパネルで現場の方に押してもらいます。それを分析してみたら、例えば、驚くべき工程待ちと作業待ちがこれだけあった、ということがわかります。それを見ると「おいおい、投入順序どうなってるの?せめて投入順序変えるだけで、この生産の能力って20%くらい上げられるんじゃない?」という話ができます。
今、多くの工場は紙で記録を取っています。例えば、何時から何分まで止まっていて、止まっている要因は2番で、誰が復帰させて、復帰にかかる工数がこのくらいで、どうやって復帰させたか、などです。しかし、紙に書かせると皆さん嘘をつくらしいのです。
小泉: ラインを直すことを優先していると、きっと何時に止まったかよく覚えてないですよね。
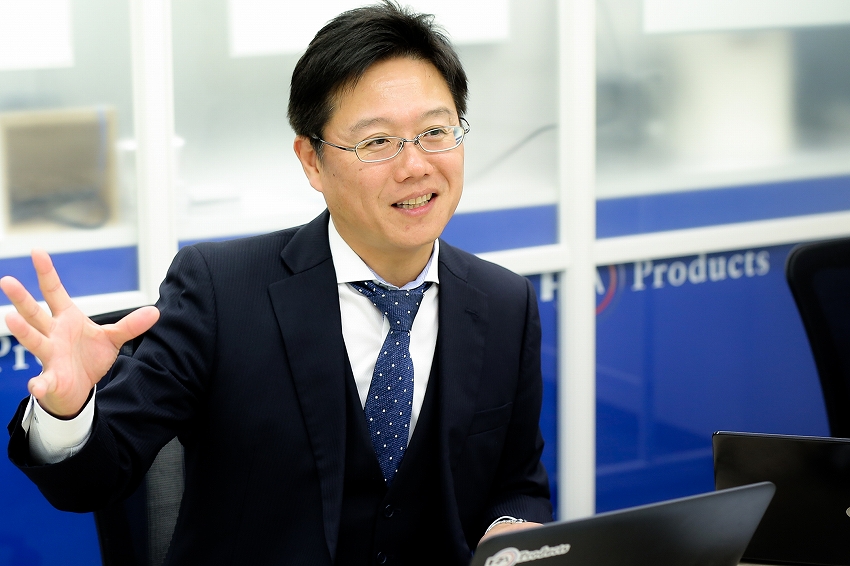
貴田: そうなのです。時間もめちゃくちゃだし、ほとんどがセンサー異常とコンベア異常で、自分たちが悪いとは書かないのです。すでに導入いただいているサプライヤーさんで確認したところ、コンベア異常は2件しかありませんでした。はじめは、設備をラインごとにラインの入口と出口で管理しようという話だったのですが、「一設備ごとの稼働状況を全部見なければ駄目だ」と変わって、予算が5千万つくことになりました。
「IoTって何から始めたらいいかわからない」、というお客さまは、ぜひ予知保全か設備の稼働分析からやってください」、ということです。いつまでも、「データ取って何に活用するの?」ってもういい加減やめない?と話しています。
中小のお客さまは、忙しくなってくると「お金はあるけど何もできない」とおっしゃいます。次に暇になってくると、お金がなくなってくるので投資をしません。つまり、どっちもできません。
「忙しくて現場なんか止められない」とおっしゃいますが、弊社のサービスは現場を止める必要はありません。信号横取りセンサが日本のスマートファクトリー化を加速する一つの起爆剤になってくれたらいいなと思います。
こういうもので稼働率だったり、稼働データだったり、時間だったり、停止要因分析のデータだったりというのがそろって、どんどんそのデータが増えてくると、いろんなシミュレーションができるようになってくるので、確からしさみたいなものがもっともっと上がってくるはずです。
ここまでできれば、あとはもう少しデータベース化して、過去のデータを検索してみたり、過去のデータを並べ替えてみて、比較検討や分析ができるようになるといいわけじゃないですか。
そうなってくると、さすがに上位にはデータベースを入れなければいけませんので、クラウドのデータが必要です。われわれも次はそちらを見ているので、今度「FAクラウド」という、クラウド上のFA専門のデータベースを発表する予定です。
シリコンバレーのMODE社と共同開発していて、いくつか具体的に適用できそうな事例も出てきました。何も考えずに現場にあるデータベースに放り込んでしまうと、あとから取り出すのに非常に手間と時間がかかります。MODE社のデータベースは取り出しやすさの課題も含めて、生産現場で運用されているデータベースが抱えている課題が一気に解決できます。
小泉: MODE社のデータ分散方式は素晴らしいですよね。伝送のプロトコルもきちんと作りこまれているので、すごくいいと思います。本日はありがとうございました。
【関連リンク】
・スマートファクトリーで本当にやるべきこと -FAプロダクツ 貴田氏インタビュー
・シリコンバレー発、Google, Twitterで培った技術力で差別化するIoTプラットフォーム -MODE CEO 上田氏インタビュー
無料メルマガ会員に登録しませんか?
IoTに関する様々な情報を取材し、皆様にお届けいたします。