工場の中では、様々な機械や設備が稼働することでモノを製造しています。
こうした機械や設備は、当然故障することもあるため、異常があった際に直したり、定期的なスケジュールで点検を行ったりという保全活動が行われています。
しかし、こうした保全活動には、コスト面や効率面での課題があります。
そこで、機械が故障する以前の微細な予兆を捉えて、最適な対策を講じる「予知保全」が注目を集めています。
本稿では、予知保全とは何かといった概要から、予知保全が注目されている背景に加え、得られるメリットや導入プロセス、事例までを解説します。
予知保全とは
予知保全とは、機械や設備の状態を、センサーなどを用いてリアルタイムで監視・分析し、故障や異常が発生する時期を「予知」することで、最適なタイミングでメンテナンスを実施するという保全の考え方、およびそのための活動全般を指します。
普段止まることなく稼働している工場の生産設備が突然停止してしまったり、社会を支えるインフラ設備が予期せずダウンしたりすることは、企業にとっても社会にとっても大きな損失につながります。
予知保全は、こうした突発的な故障やそれに伴うダウンタイムを防ぎ、設備を可能な限り安定的に稼働させ続けることを最大の目的としています。
重要なのは、「予知」という言葉が示す通り、データに基づいて将来の状態を予測する点です。
予測を行うため、機器に取り付けられたセンサーから得られる「振動」「温度」「音響」「圧力」「電流値」「摩耗度」などの稼働データを継続的に収集・分析します。
そして、そのデータの中に現れる「いつもと違うわずかな兆候」や「過去の故障事例と類似したパターン」などを捉え、「いつ頃、どの箇所が、どのような問題を起こしそうか」を統計的・科学的に予測しようと試みるのです。
この「予知」の結果に基づき、「そろそろメンテナンスが必要だ」と判断された最適なタイミングで、部品交換や修理、調整といった保全作業の計画を立て、実行します。
これにより、故障による緊急停止を回避しつつ、まだ十分に使える部品を交換してしまうといった無駄も省くことを目指すのが予知保全です。
従来の保全手法との違い
では、従来の保全手法と予知保全は、どう違うのでしょうか。
ここでは、これまで一般的だった保全手法として、「事後保全」と「予防保全」の2つとの違いを紹介します。
事後保全
事後保全は、「故障が発生した後で対応する」という考え方に基づく、最もシンプルな保全手法です。
機器や設備が実際に機能を停止したり、明らかな異常を示したりしてから、修理や部品交換を行います。
事後保全の場合、故障が発生するまでは、基本的に保全コストがかかりません。日常的な点検作業なども最小限で済みます。
しかし、故障の発生時期や規模を予測できないため、突然生産ラインが停止することによるダウンタイムが避けられず、生産計画の遅延や納期への影響、機会損失が発生します。
また、故障の仕方によっては、他の部品への二次的なダメージや、場合によっては安全上のリスクにも繋がりかねません。
さらに、保全業務が緊急対応となるため、部品の調達や作業員の確保が困難になったり、コストが割高になったりする傾向があります。
予防保全
予防保全は、事後保全の持つ「予測不能なダウンタイム」という大きなリスクを軽減するために広く採用されている手法です。
これは、故障が発生する前に、あらかじめ計画された基準に基づいてメンテナンスを行うというものです。
一般的には、時間基準保全や回数基準保全のいずれか、または組み合わせで行われます。
時間基準保全は、「半年ごと」「1000時間稼働ごと」のように、一定の期間や稼働時間を目安に、定期的に部品交換や点検、給油などを行うものです。
一方回数基準保全は、「1万回の動作ごと」のように、稼働回数に基づいてメンテナンスを行います。
予防保全は、事後保全と比較して、突発的な故障の発生確率を低減できるというメリットがあります。
メンテナンス作業を事前に計画できるため、部品や人員の手配がしやすく、ダウンタイムも計画的に管理できます。
しかし、機器の実際の劣化状態や健康状態に関わらず、定められたスケジュールや回数に基づいて一律にメンテナンスを行うため、まだ十分に機能する部品を交換してしまう「過剰保全」が発生しやすく、部品コストや作業工数に無駄が生じる可能性があります。
さらに、使用環境や負荷の変動などにより、想定よりも早く劣化が進行した場合、計画されたメンテナンス時期より前に故障が発生してしまうリスクも残ります。
これに対し、予知保全では、本当にメンテナンスが必要なタイミングで、必要な箇所に対してのみ介入することを目指します。これにより、保全活動全体の効率と効果を最大化しようとする、スマートなアプローチだといえます。
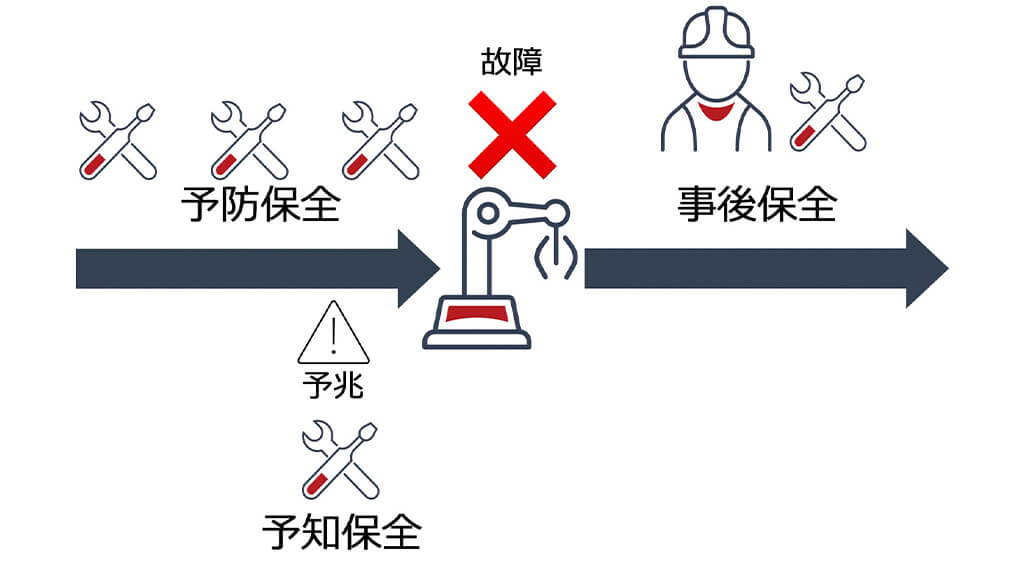
なぜ今、予知保全が注目されるのか
予知保全では、データに基づいて故障や異常が発生する時期を「予知」しますが、どのようにして状態データを取得したり、故障時期を予測したりするのでしょうか。
ここで重要になるのが、IoTやAIといったテクノロジーです。
予知保全の考え方自体は、以前から存在しており、特定の重要な設備の運転記録や定期的な検査結果などを分析し、経験則や物理モデルに基づいて設備の劣化傾向を把握したり、異常の兆候を捉えようとしたりする努力がなされてきました。
しかし、かつては、コストや技術的なハードルが高く、一部の限られた用途でしか実現できないのが実情でした。
こうした中、IoTを中心とした関連デジタル技術が進化し、普及してきたことで、予知保全が幅広い分野で注目を集めています。
具体的に、どのような技術が予知保全の実現を後押ししているのか、主要な要素を見ていきましょう。
センサー技術の進化と低価格化
センサーは、機器の状態を詳細に把握するための「感覚器」となります。
昨今、センサーの小型化・高性能化に加え、低価格化が進みました。
また、温度、振動(加速度)、音響(異音)、圧力、湿度、電流・電圧、潤滑油中の摩耗粒子、赤外線サーモグラフィによる熱分布、カメラによる画像認識など、多種多様な物理量や状態を計測できるセンサーが登場しています。
これにより、監視したい機器の重要な箇所に、複数のセンサーを比較的安価に、かつ省スペースで設置することが可能になりました。
通信技術の進化
センサーが取得したデータは、効率的に収集され、分析システムへと送信する通信が不可欠です。
しかし、「通信」と一言に言っても、どんな状況にも完璧に対応できる万能な通信技術というものは存在しません。
センサーを設置する環境やかけられるコストに加え、「どれくらいの距離を通信させたいのか」「どれくらいの量のデータを、どれくらいの速さで送る必要があるか」「消費電力はどれくらいか」「通信が途切れたり、データが欠損したりするリスクはどれくらい許容できるか」などを考慮して、適切な通信技術を選ぶ必要があります。
こうした検討項目に応えるべく、Wi-FiやBluetoothのような近距離無線、LPWA(LoRaWAN、Sigfox、NB-IoTなど)と呼ばれる省電力広域無線、高速・大容量通信が可能なセルラー通信など、多様な通信技術が登場しています。
また、データを送る前に、現場に近い場所(エッジ)で、ある程度のデータ処理を行う「エッジコンピューティング」も活用され始めており、こうした技術も組み合わせながら最適な通信を選択することができるようになりました。
クラウド技術の発展
無数のセンサーから常時生成され続ける膨大な量の時系列データを、安全かつ効率的に蓄積・管理し、高速に処理するための基盤として、クラウドコンピューティングの利用が一般的になりました。
クラウド環境は、必要に応じて計算資源やストレージ容量を柔軟に拡張できるため、大規模な予知保全システムの構築・運用に伴う初期投資や管理の手間を低減させました。
AI技術の成熟
収集・蓄積されたデータを分析し、予知保全の核となる「予測」の精度を向上させたのが、AI技術です。
クラウド上に集められた膨大な過去の稼働データやリアルタイムデータをAIアルゴリズムが学習・分析することで、人間の五感や経験則だけでは捉えきれない、故障につながる可能性のある微細な異常の兆候を高精度で検知します。
正常な稼働パターンから逸脱する異常な動きを早期に発見したり、機器の劣化がどのように進行していくかをモデル化し、故障発生までの残り有効寿命を具体的に予測したりすることも可能になってきています。
このように、「高機能・低価格なセンサー」「データを繋ぐ通信ネットワーク」「データを蓄積・処理するクラウド」「データを分析し予測するAI/機械学習」といった個々の要素技術が成熟し、それらが相互に連携して一つのソリューションとして機能するようになったこと。これが、予知保全が実用的な技術として広く普及する段階に入った最大の理由と言えるでしょう。
加えて、世界的な潮流であるDXや、製造業におけるインダストリー4.0(第4次産業革命)の推進といった大きな流れの中で、データ活用による生産性向上、コスト最適化、新たな価値創造の重要性が叫ばれていることも、予知保全への関心を強く後押しする要因となっています。
予知保全の仕組み(プロセス)
では、実際に予知保全はどのような手順で進められるのでしょうか。
これは、一度きりの作業ではなく、継続的に行われる一連のプロセスとして捉えることができます。
ここでは、予知保全を実現するためのステップの一例を紹介します。
データ収集
まずは、機器や設備の状態を示すデータを取得する必要があります。
そこで、監視対象となる機器の、故障や劣化の兆候が現れやすい箇所に、適切なセンサーを取り付けます。
故障や劣化の兆候が現れやすい箇所の例としては、モーターの軸受、配管の接続部、歯車などが挙げられるでしょう。
センサーが取得する項目としては、温度、振動(加速度)、音響(超音波)、圧力、流量、電流・電圧、潤滑油の成分や摩耗粉、赤外線画像、稼働音、外観画像などです。
こうした状態データを、センサーが機器の稼働中にリアルタイム、または定められた短い間隔で継続的に計測します。
また、機器や設備を制御するシステムからデータを収集する場合や、多数のセンサーが元々組み込まれており、ネットワーク接続機能を標準で備えている機械から直接データを収集する場合もあります。
データ送信・蓄積
収集された生データ(処理されていないデータ)は、分析のために集約される必要があります。
収集されたデータは、必要に応じてIoTゲートウェイなどを介し、Wi-Fi、LPWA、有線LAN、モバイル回線といったネットワークを通じて、データが蓄積されるクラウドサーバーや社内サーバーへ送信されます。
送られてきたデータは、分析しやすいように形式を整えたり、ノイズを除去したりする前処理(データクレンジング)が施された後、データベースやデータレイクといったデータを蓄積するシステムに時系列データとして蓄積されていきます。
データ分析・状態監視
蓄積された膨大なデータから、機器の状態を評価し、異常の兆候を捉えます。
そのためにまず、機器が正常に稼働している状態のデータパターン(ベースライン)を定義します。
そして、リアルタイムで収集されるデータを常にベースラインと比較し、統計的な閾値からの逸脱や、通常とは異なる異常なパターンが発生していないかを監視します。ここでは、統計的手法や機械学習のアルゴリズムが活用されます。
故障予測
さらに、単に「異常がある」と検知するだけでなく、その異常が将来どのような問題を引き起こすのか、いつ頃起こるのかを予測します。
これを予測するために、異常の進行度合いや変化のパターンを分析し、機器の劣化がどの程度のスピードで進んでいるかを評価します。
具体的には、回帰モデルなどの機械学習モデルを活用し、蓄積されたデータと劣化トレンド、過去の故障事例などから、機器や部品が故障に至るまでの残り時間を推定します。
保全計画・実行
予測結果を適切なタイミングで得て、それを元に具体的なメンテナンス活動へと繋げます。
具体的には、故障の危険性が高まったり、残存寿命が一定値を下回ったりした場合、システムが保全担当者や管理者に自動でアラート通知を送ります。
そして、通知された対象機器、問題箇所、予測される故障時期、推奨される対策などの情報に基づき、部品の手配、作業員のスケジュール調整、生産計画とのすり合わせなどを行い、最も効率的かつ効果的なタイミングで点検、部品交換、修理、調整などのメンテナンス作業を計画し、実行します。
フィードバックと改善
フィードバックと改善も、予知保全の精度を継続的に高めていくために重要なステップです。
実施したメンテナンスの内容や、その際に確認された機器の実際の状態を記録し、データとしてシステムにフィードバックします。
このフィードバックデータを用いて、AIの予測モデルを再学習させ、チューニングを行います。これにより、予測精度が徐々に向上していきます。
予知保全は、このデータ収集からフィードバックまでのサイクルを継続的に回していくことで、精度が向上していきます。データが蓄積され、AIモデルが学習を重ねるほど、より賢くなり、より高精度で効率的なメンテナンス体制の構築を目指します。
予知保全導入のメリット
では次に、データに基づいた予知保全を実施することで得られるメリットについて紹介します。
稼働率向上
稼働率の向上が、予知保全導入における最も直接的かつ大きなメリットと言えるでしょう。
故障の兆候を事前に検知し、致命的な故障が発生する前に計画的にメンテナンスを行うことで、生産ラインやサービスの予期せぬ停止を低減することができます。
これにより、生産機会の損失を防ぎ、設備の稼働率を最大化することができるほか、納期遵守率の向上にも繋がります。
メンテナンスコスト全体の最適化
予知保全は、メンテナンスに関わる様々なコストを削減し、最適化します。
例えば、従来の時間基準保全などの予防保全では避けられなかった、まだ十分に使える部品を定期交換してしまう「過剰保全」をなくすことで、部品代や交換作業にかかる人件費の無駄を省けます。
また、予知保全が行えれば、突発的な故障発生後の緊急対応にかかりがちな「部品の緊急手配費用」「作業員の時間外手当」「二次的な破損の修理費用」などを削減することができます。
さらに、問題箇所とタイミングを特定してメンテナンスを行うことで、調査や診断にかかる時間を短縮でき、人件費を削減できるでしょう。
加えて、機器の状態を継続的に監視し、異常の初期段階で適切な処置を施すことで、過度な負荷がかかった状態での運転や、致命的な故障によるダメージを回避できます。
これにより、設備が本来持つ性能を長期間維持し、結果としてその寿命を最大限に延ばす効果が期待できます。設備投資のサイクルを長期化させることで、結果的にコスト削減にも繋がります。
安全性の向上とリスク低減
設備の予期せぬ故障は、生産停止だけでなく、作業員の安全を脅かす重大な事故につながる危険性もはらんでいます。
特に、プラント設備や大型機械、インフラ設備などにおいては、故障が甚大な被害を引き起こす可能性や、保全作業が危険な工程を含んでいるケースもあります。
予知保全によって故障リスクを管理することは、労働災害や環境汚染などのリスクを低減し、より安全な操業・運用を支援します。
生産性および製品品質の安定・向上
設備が常に安定した最適な状態で稼働することは、一定の生産量を維持し、生産性を向上させる基盤となります。
また、設備の微妙なコンディションの変化が製品の寸法精度や特性のばらつきに繋がることもありますが、予知保全によって常に良好な状態を保つことで、製品品質の安定化や不良率の低減にも貢献します。
保全業務の効率化と人員配置の最適化
「いつ壊れるか分からない」という状況下での場当たり的な対応から脱却し、メンテナンス作業を計画的に行えるようになるため、保全担当者の業務負荷を平準化し、効率を高めることができます。
これにより、緊急対応のための待機時間を削減し、より計画的で付加価値の高い業務にリソースを振り分けることが可能になります。
これらのメリットは、単にコスト削減や業務効率化といった側面だけでなく、企業の信頼性向上、競争力強化、そして持続可能な事業運営に寄与する要素となるでしょう。
予知保全の導入における課題と考慮点
多くのメリットを持つ予知保全ですが、その導入と運用を成功させるためには、事前に認識し、対策を検討すべきいくつかの課題や注意点があります。
投資コストと費用対効果
予知保全システムの構築には、センサーの購入や設置費用、データを送受信するためのネットワークインフラの構築費用、データを蓄積・分析するためのクラウドプラットフォーム利用料やソフトウェアライセンス費用、そしてこれらを統合・設定するためのシステムインテグレーション費用などの、投資コストがかかります。
そのため、導入によって得られる効果を事前に試算し、費用対効果を慎重に見極める必要があります。
どの程度の効果が見込めるか不確実な場合は、影響の大きい重要設備に対象を絞って小規模に始めるPoC(実証実験)からはじめるなど、段階的なアプローチをとるケースもあります。
専門知識・スキルの確保
効果的な予知保全システムを構築・運用するには、多様な分野における専門知識が求められます。
具体的には、「対象設備とその故障メカニズムに関するドメイン知識」「適切なセンサーを選定・設置する計装技術」「データを収集・管理するIoT/ITインフラ技術」「データを分析し予測モデルを構築・運用するデータサイエンスのスキル」などです。
これらのスキルセットを全て自社で賄うのが難しい場合も多く、社内人材の育成と並行して、外部の専門ベンダーやコンサルティング企業の知見を活用するという選択肢もあります。
対象設備と収集データの適切な選定
「どの設備」の「どのデータ」を監視するかが、予知保全の成否を分ける重要なポイントです。
全ての設備にセンサーを取り付けてデータを収集するのは現実的ではなく、コスト効率も悪くなります。
故障時の影響度が高い設備や、過去の故障実績が多い設備などを優先的に対象とすべきでしょう。
また、その設備がどのような壊れ方をするかを分析し、その兆候を最もよく捉えることができるよう、センサーの種類や設置場所、計測頻度などを慎重に選定する必要があります。
データ品質と量の確保
AIおよび機械学習モデルの予測精度は、学習に使用するデータの質と量に大きく依存します。
不正確なデータやノイズが多いデータでは、誤った予測をしてしまう可能性があります。
また、特に故障データのような稀な事象を予測する場合、十分な量の学習データを確保することが難しい場合があります。
データの精度を担保する仕組みや、データ量が少ない場合に有効な分析手法の活用も検討が必要です。
データセキュリティとプライバシーへの配慮
設備の稼働データは、企業の生産活動に関わる機密情報とも言えます。
これらのデータをネットワーク経由で収集、送信、蓄積、分析する過程においては、不正アクセスや情報漏洩を防ぐための堅牢なセキュリティ対策が不可欠です。
データの暗号化やアクセス権限の適切な管理、ファイアウォールの設置、使用するクラウドサービスのセキュリティ基準の確認など、多層的な対策が求められます。
個人情報に該当するデータが含まれる場合は、プライバシー保護に関する法規制への準拠も必要となります。
既存システムとの連携・統合の複雑性
予知保全システムから得られた予測結果やアラートは、CMMS(コンピュータ化保全管理システム)やERP(統合基幹業務システム)、MES(製造実行システム)などの既存の業務システムと連携させることで、具体的な保全アクションに繋げることができます。
しかし、異なるシステム間でデータをスムーズに連携させるためには、インターフェースの開発やデータ形式の統一など、技術的な調整やインテグレーション作業が必要となり、これが複雑な課題となる場合があります。
これらの課題や考慮点を事前に十分に理解し、自社の状況や目的に合わせた実現可能な計画を立てることが、予知保全導入プロジェクトを成功に導くための鍵となります。
予知保全の導入事例
このように、予知保全を実現するには様々な項目を考慮する必要があり、体制を整えるのは大変なプロセスであるといえます。
そこで今回紹介するのは、センサーを活用して取得した設備の時系列データを、予知保全だけでなく様々な用途に活用した部品メーカーの事例です。
この部品メーカーの現場作業は、交代制での勤務であったため、これまで、設備の稼働状況や温度などのデータを担当者が手書きで記録し、データの分析を行っていました。
しかし、上長への報告や勤務交代時に行われる報告に決まったルールはなく、個々人の感覚によるやりとりが行われていました。
そこで、設備や作業内容に関する情報を正確に伝達することを目的に、設備に空気・温度・ガスといったセンサーを取り付けることによる、24時間の自動監視を実施しました。
取得したデータは、パソコン上のダッシュボードに時系列で表示し、トラブル時にはアラームで通知する仕組みを取り入れました。
こうしてデータを蓄積し、時系列で情報を見ることができるようになったことで、設備の特定の部分や部品の劣化などが読み取れるようになり、予知保全にも活用されるようになったそうです。
また、社員教育をする際にも、数値化された指標をもとにコミュニケーションをとることができるようになりました。
さらに、出荷後の品質に問題があった場合、データを遡って調べることで原因を追求することができ、予防処置を取ることも可能になりました。
このように、設備の時系列データを予知保全を含めた様々な目的に活用することで、費用対効果を高めている事例です。
無料メルマガ会員に登録しませんか?
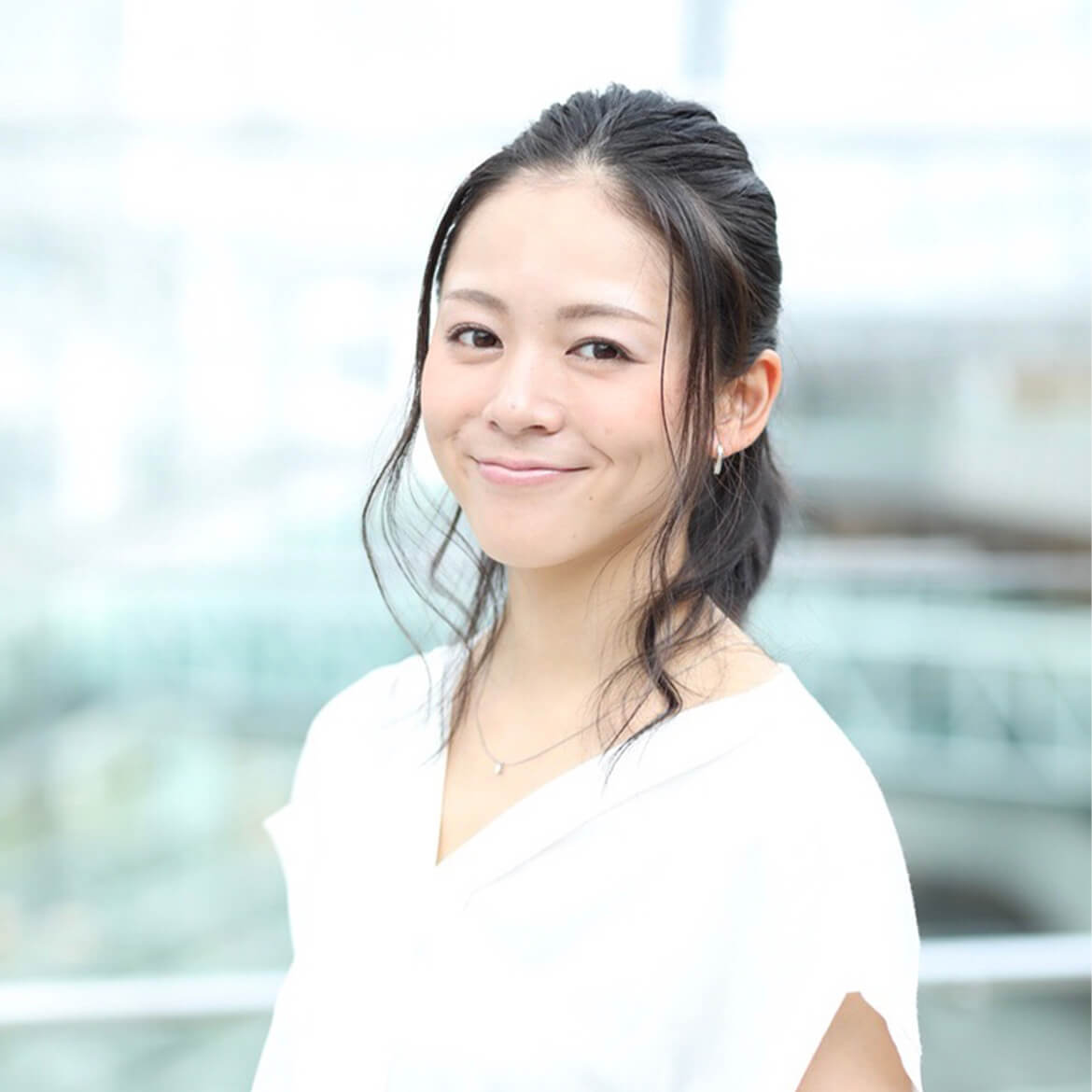
現在、デジタルをビジネスに取り込むことで生まれる価値について研究中。IoTに関する様々な情報を取材し、皆様にお届けいたします。