DIC株式会社(以下、DIC)と株式会社日立製作所(以下、日立)は、2021年3月より、DICの国内3工場で製造される樹脂製品を対象に、「理論モデル×現場データ×AI解析」による反応予測モデルの探索と精度検証を行った。
従来、プラント内の反応や蒸留といった操作においては、文献を基に各操作の理想状態をモデル化した理論モデル(文献値)を用いたシミュレーションにより、品質値(粘度など)の各種パラメータの挙動が推定されてきた。
一方で、製造現場におけるセンサーデータや分析データといったパラメータは、その動特性が、装置サイズ・設備構成により大きく影響を受けることから、シミュレーション結果(理想状態)と現場データに乖離が発生する。
そのため、プラントの設計時にその乖離を想定しておき、現場では熟練者が感覚的に調整することが一般的だ。また、少量多品種のバッチ生産では、同一製品におけるデータ数が少なく、共通する特徴や関連性の探索や普遍的なルールを導き出すアプローチには限界があった。
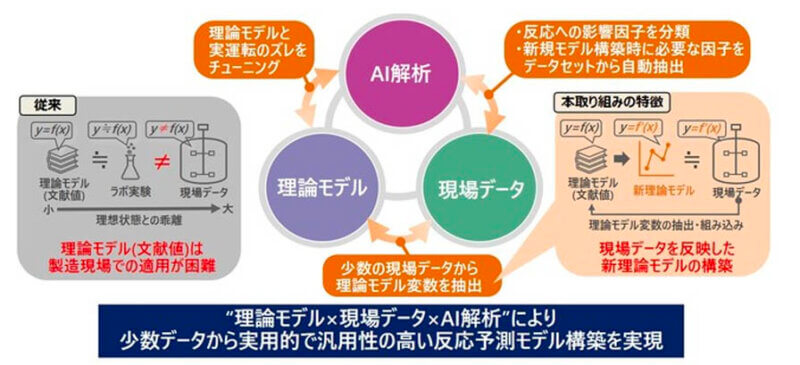
そこで本日、DICと日立は、IoTデータの利活用とデジタルツイン技術により、樹脂製品の製造におけるバリューチェーン全体の最適化を図るため、本格的に協創を開始することを発表した。
今回発表された協創では、少数の現場の実運転データ(DCSデータ、原料データ、サンプリングの分析結果など)から、文献上の反応理論式に用いる変数を作成し、その変数を用いた新理論モデルを構築することで乖離を抑えた。
そして、この新理論モデルと現場データを用いたAI解析により、品質値に影響を与える因子を分類し、高精度の反応予測モデルの構築を実現した。この結果、熟練者の経験則から感覚的に認識していた反応影響因子を、反応理論や装置などに明確に細分化し反応状態と紐づけて管理することで、反応性や装置の違いを考慮した高精度なシミュレーションが可能となった。
また、構築した反応予測モデルは新理論モデルを活用しているため、少数データから構築可能かつ、反応機構が類似する品種への転用が容易だ。
さらに、AI解析によりさまざまな品種のモデル構築に対応できる汎用的なデータセットを確立することで、新規モデル構築時に必要な因子をデータセットから網羅的に検索し、容易に抽出することが可能となった。
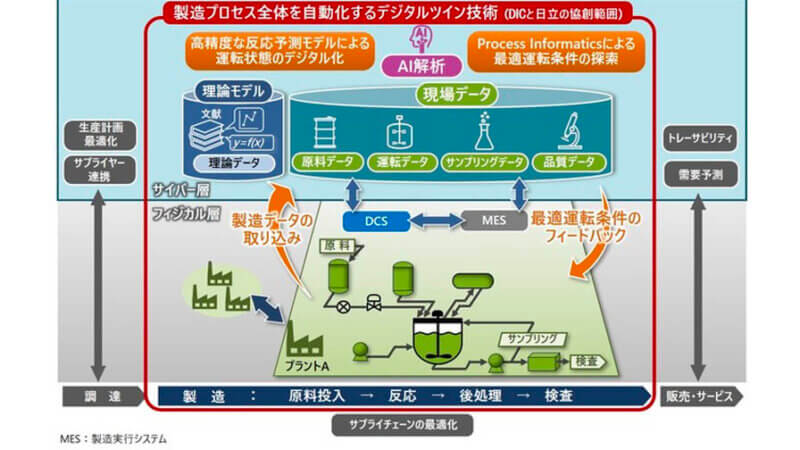
今後は、2022年中に反応予測モデルに基づいた最適運転条件の探索に関してプロトタイプによる検証、およびシステム化を行う。
その後、DICのプラントにおける最適運転条件のフィードバックの実施・検証を経て、2024年にプロセス全体を自動化するデジタル技術の実用化を開始するとともに、国内外の複数拠点へ展開していく予定だ。
無料メルマガ会員に登録しませんか?
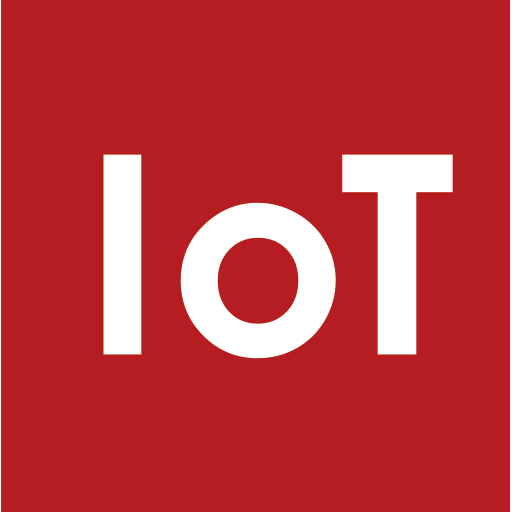
IoTに関する様々な情報を取材し、皆様にお届けいたします。