製造業では、メーカーが工場のデジタル化に取り組み、生産性改善を実現した事例が増えてきている。
その中心的な取り組みは、IoT/AIを活用した、稼働状況の可視化や産業機械の予知保全だ。ある自動車部品メーカーは、工作機械の扉にセンサーを設置。サイクルタイムを「可視化」することで、生産性を60%改善したという。
また、ある半導体メーカーでは、ドライポンプのモーターや軸受にセンサーをとりつけ、AIを活用することで「予知保全」を実現。年間約6,000万円かかっていた修繕費を1,200万円削減した。
成功事例は着実にでてきている。
その一方で、「検討しているけど今一つ踏み切れない」、「デジタル化でどんなメリットがあるのか具体的にわからない」、という企業もあるだろう。
そこで今回、製造業のデジタル化をテーマとして、全3回で解説をしていく。第1回では、昨今、デジタル化の主なテーマとなっている可視化と予知保全によって具体的にどのようなメリットが得られるのか、事例を交えながら解説する。
第2回では、可視化や予知保全のPoC(Proof of Concept:概念実証)を始める前に知っておきたいポイントを解説する。たとえば、PoCで失敗してしまった企業によくあるケースや、製品やソリューションを選ぶ際の判断のポイントなどをテーマとする。
第3回では、可視化と予知保全の次のステップについて解説する。可視化や予知保全は、メーカーにとってサプライチェーン全体の「製造」という一部分の取り組みである。一方で、インダストリー4.0で言われるような世界のデジタル化では、サプライチェーン全体に及ぶビジネスモデルの変化が起きている。これらのグローバルの動向をふまえ、企業がとるべき戦略について解説する。
「可視化」による生産性の改善
工場内にあるさまざまなデータを収集し、可視化することで、企業は生産性を改善することができる。具体的には、次の3つの方法がある。
- 設備の稼働状態や生産状況を把握
- ヒトや搬送機の動線を効率化
- 設備の故障を未然に防ぎ、稼働率を向上
以下、それぞれについて解説していく。
設備の稼働状態や生産状況を把握
可視化といって誰でもすぐにイメージできるのがこれだろう。
まず、設備の稼働状況のデータをリアルタイムで可視化することで、異常停止が起きた時に迅速な対応ができ、設備のダウンタイム(機械の異常停止時間)を短縮することができる。
つまり、「正常」「停止中」などの稼働状況や単位時間あたりの生産数量は、工場内のアンドン(モニター)や、スマートフォンなどを見ることで、常に確認することができるようになる。
もし、自分が担当するラインの設備が異常停止していた場合、それを見てすぐに駆けつけることが可能になる。
また、単位時間当たりの生産数を正確に測定できるため、同一工場内におけるライン間の生産性のギャップを明確にすることができる。
たとえば、AのラインよりもBのラインの生産数が著しく少ないことがわかれば、ラインを構成する産業機械や手作業など工程ごとの時間を計測していくことで、生産性を悪化させている要因(ボトルネック)を追究することができる。
自動車部品メーカーの旭鉄工株式会社は、工作機械のサイクルタイム(製品1個をつくるのにかかる時間)を可視化することで、生産性の悪いラインを発見。その要因を突き止めることで、生産性を改善した。
その工作機械は旧式であり、PLCやNCでサイクルタイムのデータを取ることが不可能だった。そのため、ストップウォッチを使ってサイクルタイムの計測を行っていたという。
このラインでは、ロボットアームが加工前の部品(ワーク)を工作機械の中へセットし、加工が終わったらその部品(ワーク)を取り出すという工程で、アームが部品を出し入れする際に、工作機械の扉が開く。
そこで、工作機械の扉が次に開くまでの時間を測定すれば、製品1個をつくるのにかかる時間(サイクルタイム)がわかるというのだ。つまり、このサイクルタイムは、扉の開閉部にセンサーを設置することで取得できる。
そして、各工作機械のサイクルタイムを横並びで比較した結果、あるラインだけサイクルタイムが著しく悪かったという。その要因を追究したところ、ロボットアームの動作や工作機械の扉の開き具合に問題があることがわかり、それらを見直すことで、サイクルタイムを短縮できたということだ。
こういった様々な取り組みの結果から、同社は生産性を従来の60%以上改善し、必要とされていたラインの増設についても実施を見送ることができたということだ。
では、工場間の生産性はどうだろう。例えば比較の結果、工場間の生産性が同じくらいであったにもかかわらず、片方の工場だけが生産性が著しく悪い場合などは、単に材料の調達がうまくいっていなかったということもあるくらいだ。
海外などの、工場が必ずしも目に届くところにあるわけではない場合には大きな意味が出てくるだろう。
他にも、据え置き型の産業機器だけでなく、工場内を移動する搬送車の稼働状況を可視化した事例もある。
クラウンなどを製造するトヨタ自動車の元町工場では、日立のソリューションを活用し、無人搬送車(AGV)にセンサーをとりつけ、稼働状況と位置を可視化した。
これにより、トヨタ元町工場では、無人搬送車が異常停止した時は現場スタッフが速やかに対応することが可能になり、停止した無人搬送車の復旧作業にかかる工数を50%削減したという。
ヒトや搬送機の動線を効率化
ヒトやフォークリフトなどの搬送機に位置センサーをつけることで、それらの動線を可視化し、無駄な動きをしている場合は改善することができる。
株式会社CECの動線管理ソリューション「RaFlow」を活用し、フォークリフトが回りこむ動線が数多くあることや、同一エリアに台数が集中する時間帯があることを発見したという。
それにより、レイアウト見直しを行うことができ、その結果フォークリフトの稼働台数が70台から60台に削減。また、総移動距離も4,600 mから2,300 mに削減できたということだ。
また、ヒトの動線データに設備の稼働状況のデータを組み合わせることで、ボトルネック分析に活かした事例もある。
たとえば、設備の稼働状況をチェックしていたところ、ある設備が異常停止し、正常な稼働状態に戻るまで長い時間を要したことがわかったとする。その際、ヘルメットなどに位置センサーを設置しておけば、誰が対応したのかが特定できる。
さらには、稼働停止からそのヒトが現場に駆けつけるまでの時間もわかる。それが長い場合は、初動に余計な時間がかかったことがわかり、なぜ遅れたのか、どう改善するか、といった議論が可能になる。
これらの取り組みは、「現場が監視されている」という印象を持つ作業担当者もいるかもしれない。しかし、実際に導入した企業では、これをきっかけに現場スタッフが気づきを得て、さらに改善しようというアクションが生まれているという。
設備の故障を未然に防ぎ、稼働率を向上
設備の稼働状況は、前述したようにリアルタイムでチェックする以外にも、さまざまな活用の方法がある。
たとえば、現場スタッフがタブレットに表示された過去の稼働データをメンバーと共有しながら、「この設備、最近チョコ停が多いけど、どうなってるの?」と指摘することで、改善ができる。
可視化することで、変化や予兆に対する「気づき」につながり、生産性が向上していくという成功事例が出てきている。
たとえば、総合機械メーカーの東芝機械は、ウィングアーク1stの可視化ツール「MotionBoard」を活用することで、機械の突発故障による機械停止時間を半分以下に削減したという。
可視化したデータから、「ある部品のちょっとした汚れが機械の故障につながっている」という「気づき」を得ることで、工場のメンバーが自発的なクリーニングに乗り出すなど、さまざまなアクションにもつながっているということだ。
他にも、「ドカ停」が起きてしまった2日前のデータを見ると、その兆候と見られる「チョコ停」が確認できたというようなケースもあるという。
熟練者であれば、その兆候を自ら気づき、未然に対策できるということもある。しかし、それらをデータに基づいて管理ができれば現場全体に適用でき、生産性改善につながる。
ある日系企業の海外工場では、東洋ビジネスエンジニアリング株式会社(B-EN-G)のIoTソリューション「mcframe SIGNAL CHAIN」を導入し、設備の稼働状況を可視化した。その結果、1か月で設備異常は従来の3分の1に低下し、さらに2か月後には、その一連のノウハウを、現地スタッフに移管できたという。
この工場では、現地スタッフに任せていることもあり、夜勤中に機械の異常停止が頻発し、朝まで放置してあるなどの問題があった。そこで、まず第2工場の設備3台でPoCを実施してみたところ、1週間で生産性が向上し、全台へ導入したということだ。
予知保全により「止まらない工場」を実現する
前述した、設備の異常停止を未然に防ぐ取り組みだが、可視化のソリューションを使うだけでは、「アナログ感」が拭い去れない。
もっとデジタルの力を使って「止まらない工場」を実現するのが、「予知保全」のソリューションだ。
工場にとって、稼働を止めないことは最も重要な課題だ。稼働が止まると、生産性に大きなダメージを与えるだけでなく、受注を逃すなどの機会損失にもつながってしまう。
機械はメンテナンスをしなければ、やがて故障してしまう。そのため、ある一定の期間で部品の交換や補修を行う「予防保全(時間基準保全、TBM:Time Based Maintanenance)」が一般的だ。しかし、この方法では、それが本当に正しいメンテナンスのタイミングなのかはわからず、ムダがコストが発生している可能性もある。
そこで、設備の状態を把握し、「故障がもうすぐ起こりそうだ」という予兆があったタイミングでメンテナンスをする「予知保全(状態基準保全、CBM:Condition Based Maintenance)」に期待が集まっている。
ファナックのように、機械製品と一体で予知保全のソリューションを提供する機械メーカーも出てきた。工場の現場としては、それらを活用することで予知保全を目指すことができる。
他にも、モーターに振動センサーをとりつけ、機械学習を用いて故障のタイミングを抽出する例がある。簡単には故障しない産業機械の予知保全では、「正常」状態のみをAIが学習することにより「正常稼働モデル」を作成し、そこから乖離したものを「異常」として検知する方法が一般的だ。
これらは、ノウハウやソリューションも充実し、成功事例も出てきている。
IoTソリューション・ベンダーであるFAプロダクツは、半導体工場で真空状態を作り出すためのドライポンプのモーターや軸受、ギヤなどのデータをセンサーで取得し、「正常稼働モデル」から異常状態を検出して予知保全を実現。年間6,000万円かかっていた修繕費用を1,200万円削減したという。
ここまでみてきたように、可視化と予知保全で企業が得られるメリットは大きい。メリットがわかれば、次はPoCに着手しようということになる。しかし、「PoCはまず何から始めていいのかわからない」、あるいは「やってみたけどうまくいかなかった」という声も聴く。そこで次回は、PoCで実行するうえで重要となる具体的なポイントについて解説していく。
製造業のデジタル化において今やるべきこと
無料メルマガ会員に登録しませんか?
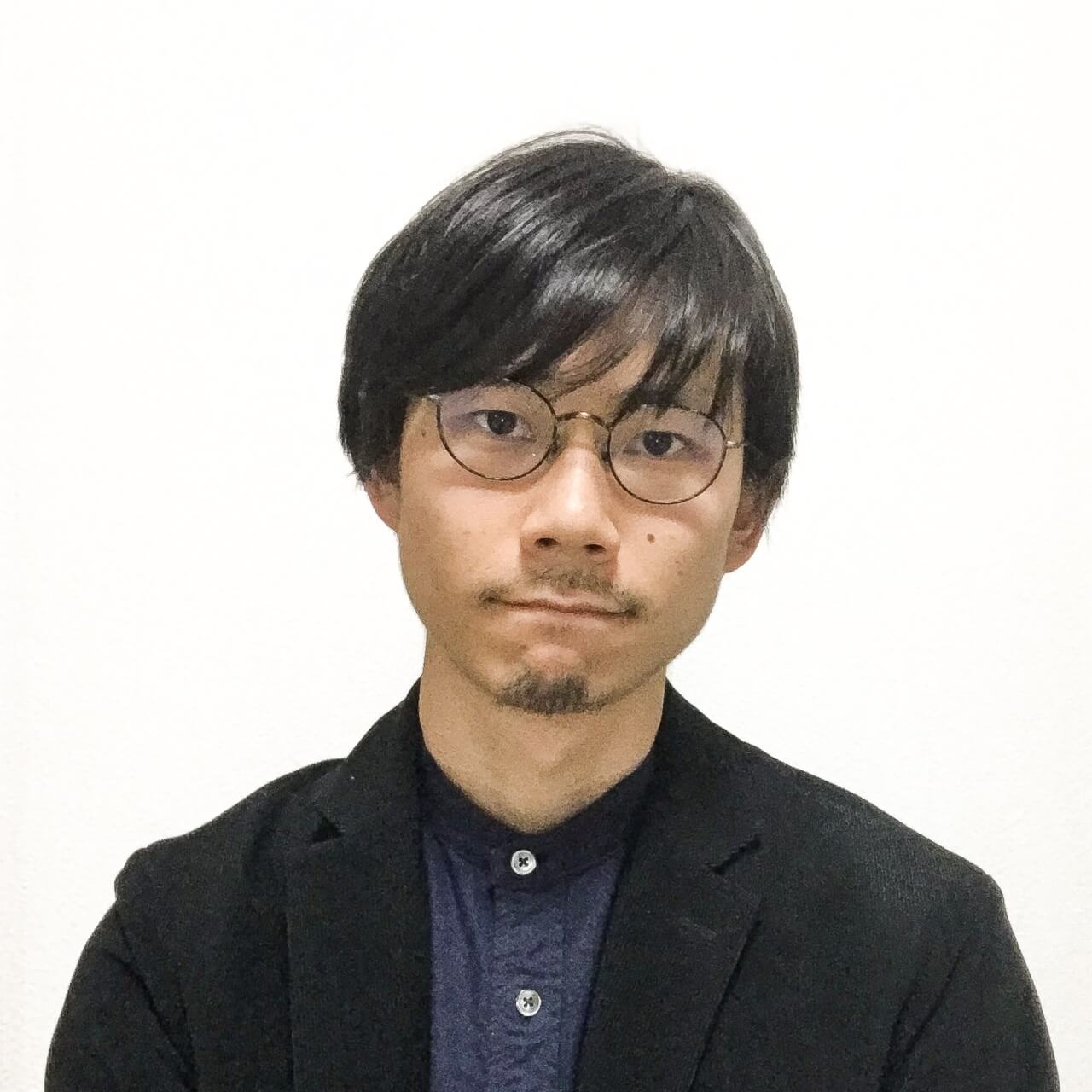
技術・科学系ライター。修士(応用化学)。石油メーカー勤務を経て、2017年よりライターとして活動。科学雑誌などにも寄稿している。