日本電気株式会社(以下、NEC)は、2018年に共創型体験スペース「NEC DX Factory」を開設した。今回、新たに追加されたデモンストレーションや、NEC DX Factoryに新たに併設されたローカル5Gラボなどを含む、新たな「NEC DX Factory」について取材を行った。
本稿では、NEC DX Factoryのコンセプトや、サプライチェーン全体の改革に関するデモンストレーションなどを紹介する。
目次
NEC DX Factoryのコンセプト
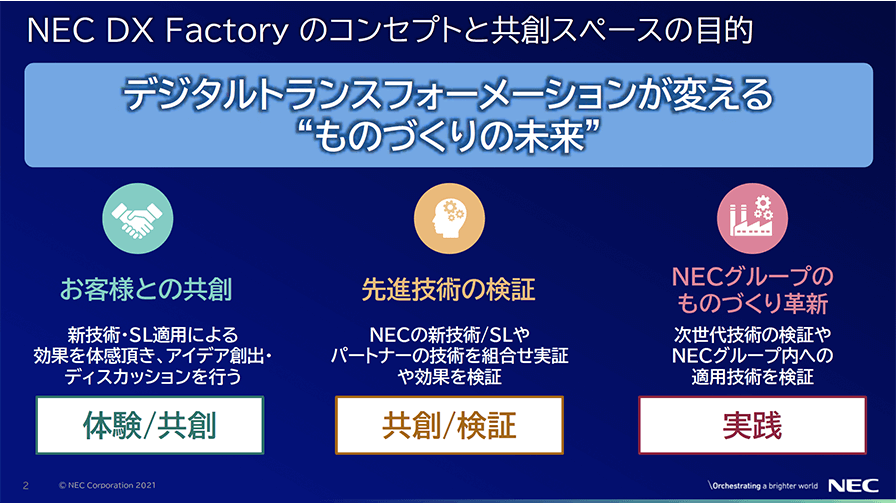
NEC DX Factoryには、
- 顧客との共創
- 検証
- 実践
という3つの大きなコンセプトがある。
顧客との共創
カタログやPowerPointの資料を用いた机上の説明だけよりも、実際に見学し体験を交えながら議論をすることが重要だとNECは考えているという。
実際にデモンストレーションを体験することで、じゃあ自分たちの工場だったらどんなことができるのかを考えるきっかけになるだろう。
検証
IoTやAIの導入を検討する時、カタログスペックだけ見ると、安価なものでも使えそうに感じたり、すごく良いものに感じたりする事がある。しかし、実際に導入してみようとなったら、そんなに簡単ではないことが多いという。プログラミングやティーチングが難しかったり、大量の教師データを用意しなければならなかったりする。
先端技術を現場で運用したいと考えたときに、NEC DX Factoryで実現システムや導入ステップについて具体的な議論をすることができる。
実践
検証の部分で、先端技術が実際に現場で使用できるかを検証していく中で、使用できる目処が立ったものは、NECの工場に適応したり、活用できそうなユースケースに使用してみたりということを実践していっているという。
2018年の開設時から、様々な企業が見学や体験のために来社したという。現在はリモート見学会も実施しているため、遠方の企業も参加しやすくなっており、大人数でリモートで参加しデモンストレーションを見ながらディスカッションを行うということもあるそうだ。
DXにはサプライチェーン全体を意識した最適化が必要になる
NEC DX Factoryの開設時は、工場の中での最適化を体験できるスペースであった。材料や部品が投入されて、加工、検査、出荷という工程を通って行く中での1つの物体を管理するようなデモンストレーションを見学することが出来た。その中で新たに着目した部分があるという。
それは、ものが運ばれる部分には、人が介在するということだ。トレーを回収しなければならない、荷姿を変更しなければならない、形状がそれぞれ違うものを運ばなければならないというシチュエーションにおいては、人が介在して作業を行う必要がある。
工場の中での省人化や、間接業務の遠隔作業化ということも重要であるが、やはり、出庫までの部分を含めて、サプライチェーン全体でものの流れを最適化することが重要である。
デジタル技術やAIを活用しようと考えて、現場のデータを収集したとしても、標準や基準がそもそもない場合は上手くいかない。サプライチェーン全体で基準や標準を決めていくべきであり、ものの流れが決まっているところに、どう効率化していくかを検討するためにデータを使用していく必要がある。
NEC DX Factoryでは、サプライチェーン全体をLEGOブロックで再現したデモライン「SCM改革『Supply Chain World with LEGO Bricks』」が展示されている。NECがこれまでに行ってきたサプライチェーンの改善をデモラインに組み込むことで、ものの流れを見える化し、サプライチェーン全体の最適化とはどのようなことなのかを視覚的に理解することができるようになっている。
SCM改革「Supply Chain World with LEGO Bricks」を使ったデモンストレーション
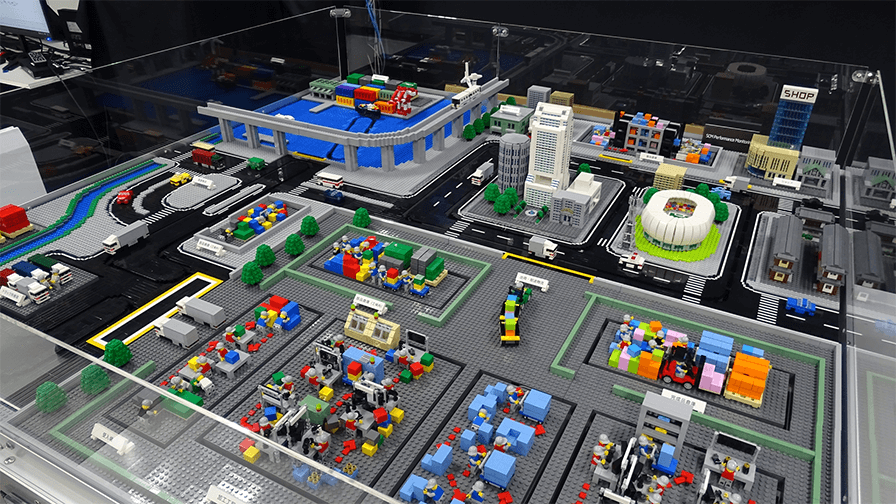
デモンストレーションでは、サプライチェーンの物理的な情報はデモラインで確認することができ、サイバーの情報は、NECが提供している在庫を見える化するツール、「SCM Performance Monitoringソリューション」で管理できるようになっている。
サプライチェーンを改革する大きな目的は、コストの適正化だ。NECでは、その中でも在庫と物流、倉庫代を適正化していくことが必要だと考えているという。
しかし、現状のサプライチェーンには、部分最適KPIという課題があるという。調達部門は部品をたくさん買った方がコストを抑えられると考えているし、製造部門は製品を一度にたくさん作った方がコストを下げられると考えている。営業部門は、需要がある製品の品切れを防いで販売数を増やしたいと考えている。それぞれの考えのまま行動すると、あちこちに在庫の山ができてしまうことになってしまう。
世界の潮流は、全体最適KPIを考え、経営指標に結びつけてサプライチェーン全体での在庫を管理していくという考え方に変わってきている。全体最適KPIにどう対応していくかということが、サプライチェーン全体での在庫管理に必要である。
サプライチェーンを改革するためのポイントは、大きく3つあるという。
まず、工程や工場、部門を物流の流れでつなぐことだ。サプライチェーン全体で連続した仕掛けに作り変えることが重要である。
次に、サプライチェーンが作られたら、それを適正化し維持していくことだ。市場の動向に合わせて生産と購買を動かす仕組みを構築する。最後にグローバルでの在庫を可視化するということだ。適正な在庫を維持するためのネットワークを用意する必要がある。
改革前のサプライチェーンの状態
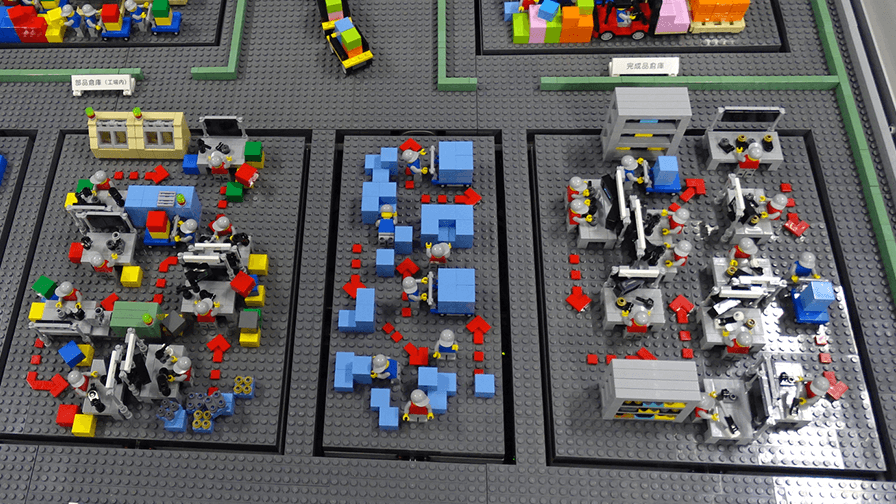
デモラインを使用したデモンストレーションはまず、改革前のサプライチェーンを表している。
工場内の赤線が人の動線を表しているのだが、入り乱れていて、効率が悪い動きになっていることがわかる。工場内にいる人は洋服の色によって役割が分かれている。赤い服は製造担当、青い服は搬送担当などという役割が決められているが、改革前のデモラインでは、配置がバラバラで役割以外の仕事をしている人も確認できる。
実際にNEC DX Factoryに見学に来る企業の中でも、同じような工場の様子になってしまっていることもあるそうだ。
整理整頓がされていなかったり、工場内の流れが悪くなっていたりすると、どこにどのくらい在庫を抱えているのかがわからなくなってしまう。在庫量がわからないと、製造部門は効率性を重視して製品を作りすぎてしまい、更に在庫が増えてしまうという悪循環に陥ってしまう。作りすぎてしまった在庫は倉庫を圧迫し、工場内では収まりきらなくなり、別の倉庫にわざわざ物流コストをかけて移動させて保管する必要が出てきてしまう。
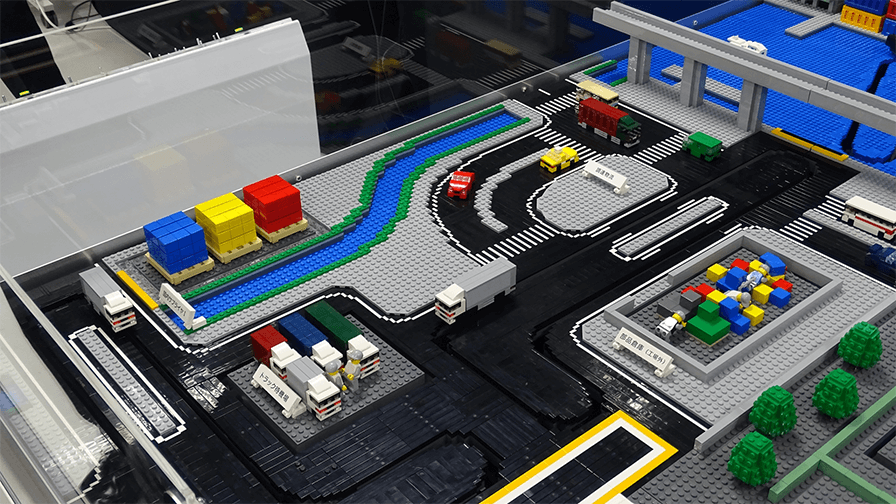
物流の方を見てみると、受け入れ場やトラック待避所が混雑していることがわかる。これは、サプライヤーから荷物を配達してもらうときに、朝に配達が集中してしまっているためだ。一度に沢山の荷物が配達されるため、本来の業務ではない製造担当者まで駆り出されて受け入れ場の整理を行う必要が出てしまっている。
受け入れ場の混雑は、トラックドライバーの負担にも影響している。トラックが工場に到達しても、受け入れ場の体制が整っていないため、搬入までに時間がかかり、本来不要なはずの待ち時間が発生してしまう。
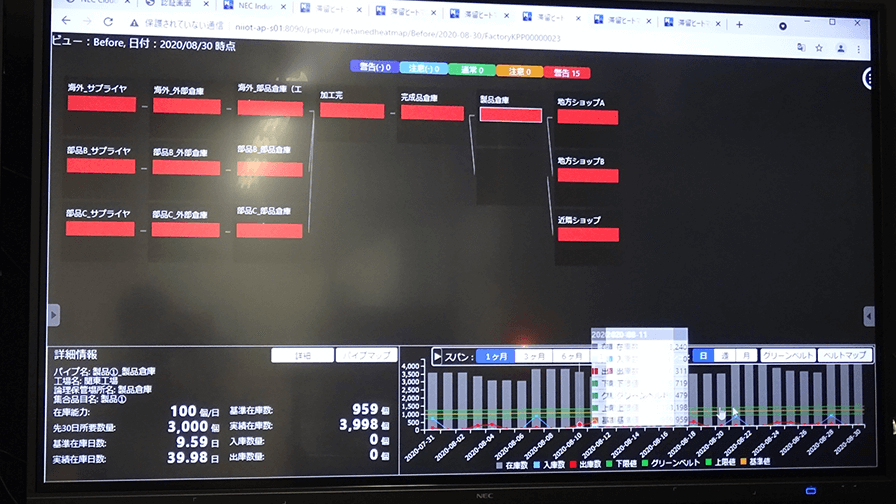
NECでは、こうした状況を「SCM Performance Monitoringソリューション」で可視化することができる。今回のデモンストレーションで使用したのは、同ソリューション内の滞留ヒートマップという機能だ。工程ごとにどれだけ在庫があるかということをヒートマップで見える化することができる。
改革前のサプライチェーンの状況では、どの工程もヒートマップが赤く表示されている。在庫量の他にも、出庫数や入庫数も管理できる。今回のデモンストレーションでは、入庫数と出庫数にはあまり差がないのに、在庫が多いということが見える化して判明した。全体的に在庫が有り余っているということだ。
今ある在庫数など、現状の姿が把握できていないケースもあるため、ツールを使って見える化を行い、余計な在庫を抱えているということをまずは伝えるところから始めることもあるという。
NECが支援する5つの改革ポイント
では、在庫が有り余ってしまっているサプライチェーンをどのように改革していくか。NECでは、5つのポイントでサプライチェーンの改革を支援しているという。
1つ目が、バリュー・ストリーム・マップ手法という、トヨタ生産方式の考えに従って、ものと情報の流れの可視化を行うことだ。2つ目は、効率的な物流網を構築することである。工場外はミルクラン方式、工場内はみずすまし方式を活用し、定時定ルート便を構築する。
3つ目が、平準化生産だ。在庫を一時保管するストックポイントを構築し、そこからカンバンをつけて、必要なものだけ生産する。品目別のストックポイントを作ることで、市場の変動を吸収する狙いがある。
4つ目は、交差比率という考え方である。交差比率とは、在庫が儲かっているかどうかを見るための指標であり、適正在庫を把握するために用いられることが多い。交差比率は、利益と在庫の関係から算出される。経営指標と在庫の回転率を結びつけ、戦略的にどれだけの在庫を持ち、回していくかということをしっかり決めていく必要がある。
5つ目は、在庫の可視化だ。品目別にどこにどれだけの在庫があるかを可視化していく。
改革後のあるべき姿のサプライチェーン
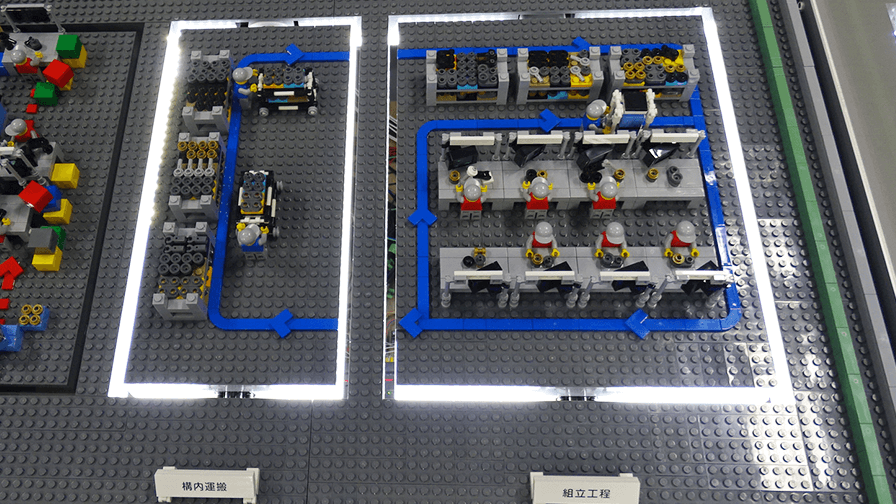
デモラインは、改革後のサプライチェーンの姿に変化し、その様子を見学することができる。
実際に見学すると、改革後のサプライチェーンは、全体的に在庫が整理されて、スッキリしたレイアウトになっていることがわかる。
完成品在庫や製品倉庫は、品番ごとに整理され、在庫が減っているため、業務を行う人員のリソースも削減できている。
工場内の各工程も、動線が整流化され、それぞれの工程で動線が分かれていて、どこでどんなものが作られているかがひと目でわかるようになった。
物流を見ると、定時定ルート便を構築することで、特定の時間に集中することがなくなり、受け入れ場やトラック待避所の混雑もなくなっている。また、海外からの船便の時間に合わせてトラックの巡回を行うように設定されているので、トラックの積載率やドライバーの負担という問題も解決できるだろう。
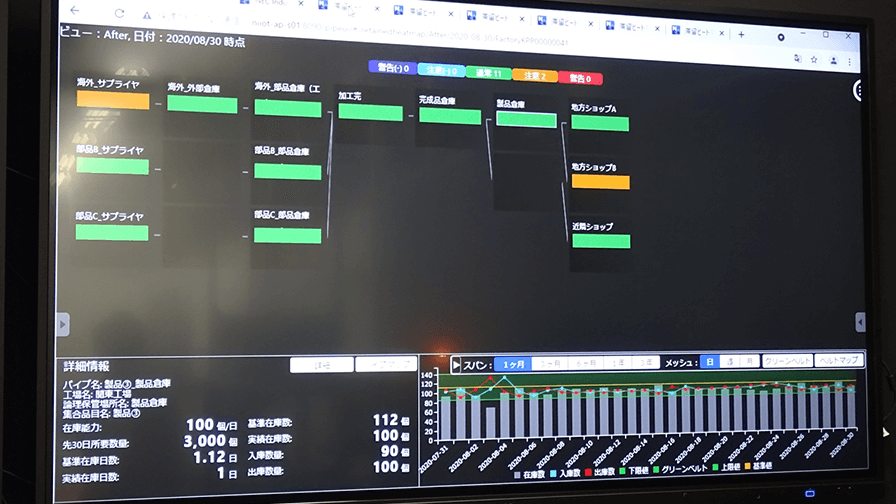
滞留ヒートマップを見ても、各工程の在庫が減っていることがわかる。実績の在庫数や在庫日数も表示されており、数値的にも大きく改善している。
このように、ものの流れに着目することでサプライチェーンの改革が進むことが、デモラインを見学することで視覚的に理解することができる。この改革には、NECが自社工場で進めてきたノウハウが詰まっていて、そのノウハウをNECは匠コンサルという形で顧客に提供している。
会社全体の経営を踏まえた全体最適の検討が必要
実際にデモラインを見学した企業の多くは、あるべき姿はわかるが、実際は日々現場で様々なことが起きていて、実態はあるべき姿とは大きく異なっているという感想を持つそうだ。企業の経営層も多く見学に訪れるが、何をしなければならないか、何から手をつけていくのが良いのかわからないという状態になっているという。
自社だけでは解決できない課題がたくさんある中で、どのようにやっていくのが良いのかということから顧客とNECの間でディスカッションが始まるそうだ。
その中で、一緒に現場を見てほしいという要望が出て、実際に工場を視察すると、一般的に有名な企業でも、とにかく在庫が多く、1日の大半を在庫の運搬に使ってしまっている工場が多いという。
これまでの製造業を振り返ると、製品を作ったら作っただけ売れるような状態が多く存在していた。特に、業績の良い会社であればあるほど、生産性改善を行い生産量を増やし、とにかくたくさん作って売るということを考えてきたという。
その結果、個別最適が進んでしまい、在庫が溢れてしまうという状況になってしまうが、具体的にどう変わったら良いのかがイメージできていない企業もあるという。
デジタル技術を使用してサプライチェーンの改革を行うためには、どこかでライン停止をしてシステムの導入を行う必要があるが、儲かっている企業ほど、納期を守って製品を生産することに必死であり、生産ラインを止める余裕がない状態である。
しかし、いつかは改革に踏み切らなければ、デジタル技術を活用した企業に遅れを取ってしまう可能性があるため、顧客には経営判断をしてもらう必要があるとNECは考えている。
中間在庫置き場や人手で対応している箇所から最適化するという方法は、ライン停止をする必要がないため改革を始めやすいが、費用対効果が出ないため、技術を試す程度で終わってしまうことが多い。
長期的視野に立ち、会社全体の経営を考慮に入れながら、工場としてものづくりをどうしていかなければならないかということを経営層は考えていかなければならない。NECは、コンサルティングという立場で顧客企業の現状と変わらなければならないということをはっきりと伝えた上で、その経営層の考えを実現していくためには、どのような技術が必要なのかを検討していく支援をしている。
関連記事
デモンストレーションを体験することで、ソリューションの自社での展開を考えるきっかけに ー「NEC DX Factory」レポート2
無料メルマガ会員に登録しませんか?
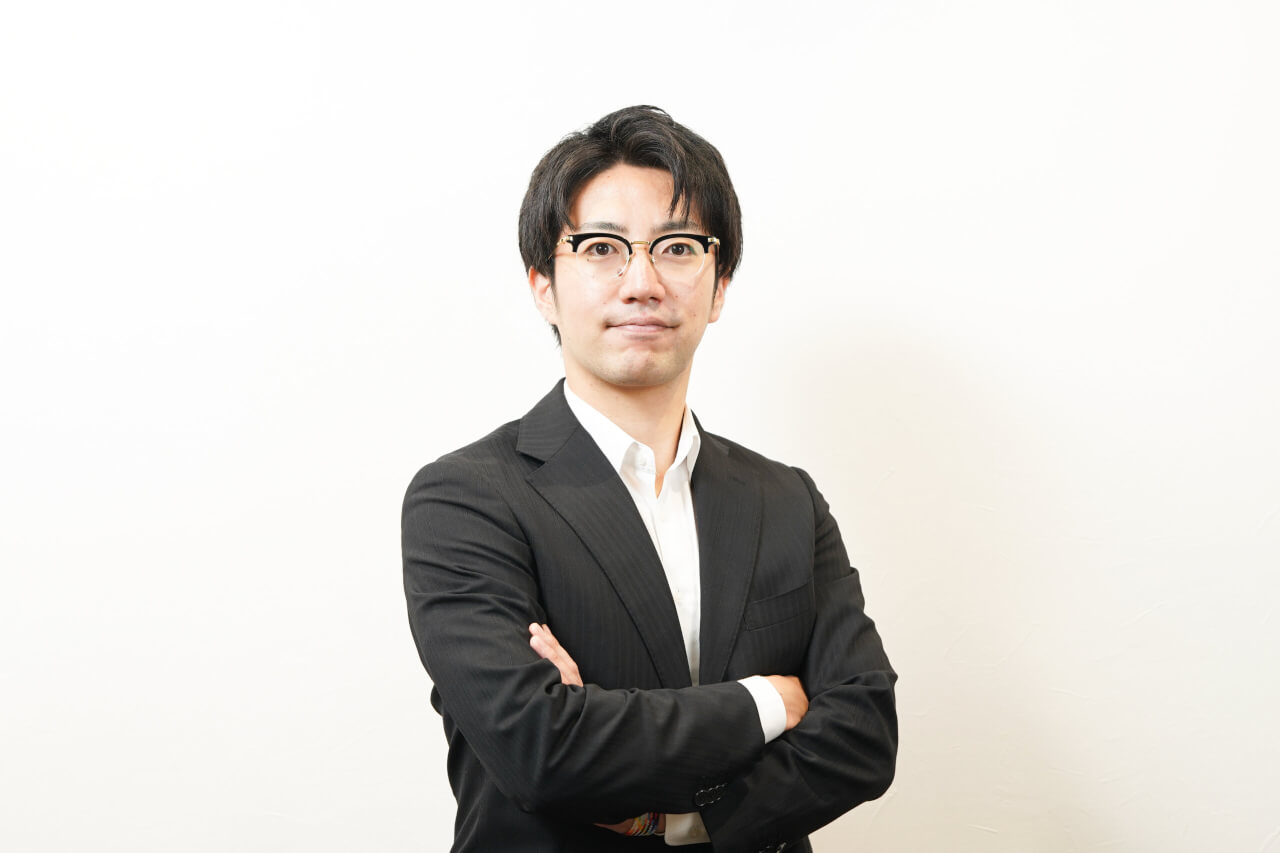
大学卒業後、メーカーに勤務。生産技術職として新規ラインの立ち上げや、工場内のカイゼン業務に携わる。2019年7月に入社し、製造業を中心としたIoTの可能性について探求中。