製造業の現場で日々業務を回す中で、「ウチの仕事って、結局どういう流れになってるんだろう?」「このやり方は本当に効率的なのか?」と疑問に思ったことはありませんか?
この、日々の生産活動を支える仕事の流れのことを、「業務プロセス」と言います。
具体的には、ある特定の目的を達成するために行われる、複数の作業やタスクが順序立てて連携して行われる一連の「活動そのもの」を指します。
例えば、「製品を作る」「お客様に出荷する」といった目的を果たすために、原材料の入荷から始まり、部品の加工、組立、検査、梱包、出荷といった様々な工程をたどる、目には見えない「仕事の流れ」そのものです。
「誰が(担当者・部門)」「何を(作業内容)」「どのように(手順・方法)」「いつ(タイミング)」「何を使って(設備・ツール)」「どの情報やモノが」「どう動くのか」
これら全てが絡み合って、一つの業務プロセスが成り立っています。
このプロセス全体を正確に把握し、最適化することで、会社の生産性や利益の向上、そして競争力を高めることが期待できます。
なぜ今、製造業で業務プロセス改善が急務なのか
業務プロセスを改善した方がいいと思いつつも、これまで行われてきた業務を変えるのは大変な労力と時間がかかるため、なかなか着手できないというケースも多いのではないでしょうか。
しかし、現代の製造業を取り巻く環境が、過去とは大きく変化していることも忘れてはいけません。
一つの変化は、人手不足です。少子高齢化が進む日本において、製造現場の人手不足はますます深刻化しています。
限られた人材でこれまで以上の生産性を維持・向上させるためには、個人の能力に頼るのではなく、プロセス自体を効率化し、自動化できる部分はデジタル技術に任せる必要があります。
また、技術継承の問題もあります。長年培ってきた熟練工の技術やノウハウは会社の宝ですが、彼らの引退が迫る中で、その「勘と経験」をどう次世代に引き継ぐかは喫緊の課題です。
そのため、業務プロセスを明確にし、標準化することで、この属人化を解消し、技術の形式知化を進める必要があります。
さらに昨今は、原材料費、エネルギー費、物流費など、あらゆるコストが上昇傾向にあり、無駄の多い業務プロセスは、そのまま見えないコストとして利益を圧迫します。
プロセスを見直すことで、無駄を排除し、生産効率を高めることが、コスト高を乗り越える重要な手段となります。
こうした背景から、業務プロセスの改善は、「やった方がいいこと」から「やらなければ生き残れないこと」へと変わってきています。
製造現場の「当たり前」に潜む無駄の例
業務プロセスの改善とは、つまりは無駄をなくしていくことですが、普段、何気なく行っている業務プロセスの中にこそ、実はさまざまな無駄が隠されています。
例えば、以下のような無駄が挙げられるでしょう。
- 手戻りによる無駄: 前工程での小さなミスが、後工程で発覚し、製品全体を分解してやり直したり、大きな修正が入ったりする。
- 情報の滞留・共有不足: 紙の帳票や口頭での連絡が多く、必要な情報が担当者間でリアルタイムに共有されない。結果として、指示待ちや確認作業に時間がかかったり、誤った情報で作業が進んでしまったりする。
- 複雑な承認プロセス: 一つの資材発注や工程変更に、何人もの印鑑が必要で、承認に時間がかかり、意思決定が遅れる。
- 過剰な在庫や仕掛品: 「とりあえず作っておく」「もしものために多めに持っておく」といった考えから、必要以上の原材料や中間品が倉庫やライン上に滞留し、スペースや管理コストを圧迫する。
- 特定の個人への依存(属人化): 「あの人にしかできない仕事」があるため、その人が休むと業務プロセス全体が止まってしまう。
- 無駄な移動・手待ち: 作業員が必要な工具や部品を探し回ったり、機械の稼働待ちで手持ち無沙汰になったりする。
これらの無駄は、日々の業務に溶け込んでいるため、なかなか気づきにくいものです。
そこで次の章では、この「見えない無駄」を具体的に「見える化」し、改善していくための第一歩について解説します。
業務プロセス改善の第一歩、現状の見える化と課題特定
業務プロセス改善の重要性は理解できたものの、自社の無駄をどのように見つけ、具体的に何をすればいいのでしょうか。
まずは、現状の業務プロセスを正確に把握し、どこに問題があるかを明確に特定する必要があります。
この章では、そのための具体的な方法のひとつとして、「業務フロー図」の活用法について解説します。
現状の業務プロセスを「業務フロー図」で徹底的に「可視化」する
業務フロー図では、特定の記号や線を使って、作業やタスク、担当者や部門を表し、作業の手順および情報やモノがどのように流れているか、作業を行っている中での意思決定のポイント、各作業で何が投入され、何が生み出されるかといったことを視覚的に表現します。
- アクティビティ(四角): 具体的に行われる一つ一つの作業やタスク内容(例:部品加工、品質検査、日報作成)
- プール/レーン(スイムレーン): 作業を行っている部門や担当者を示す。
- シーケンスフロー/メッセージフロー(矢印): 作業の順番と、情報やモノがどのように流れていくかを示す。
- ゲートウェイ(ひし形): 「OK/NG」「Yes/No」などの判断や意思決定のポイント。
- データオブジェクト: 各作業で何が投入され、何が生み出されるか。
- イベント(丸): プロセスの開始や終了、または途中で発生する出来事を示す。
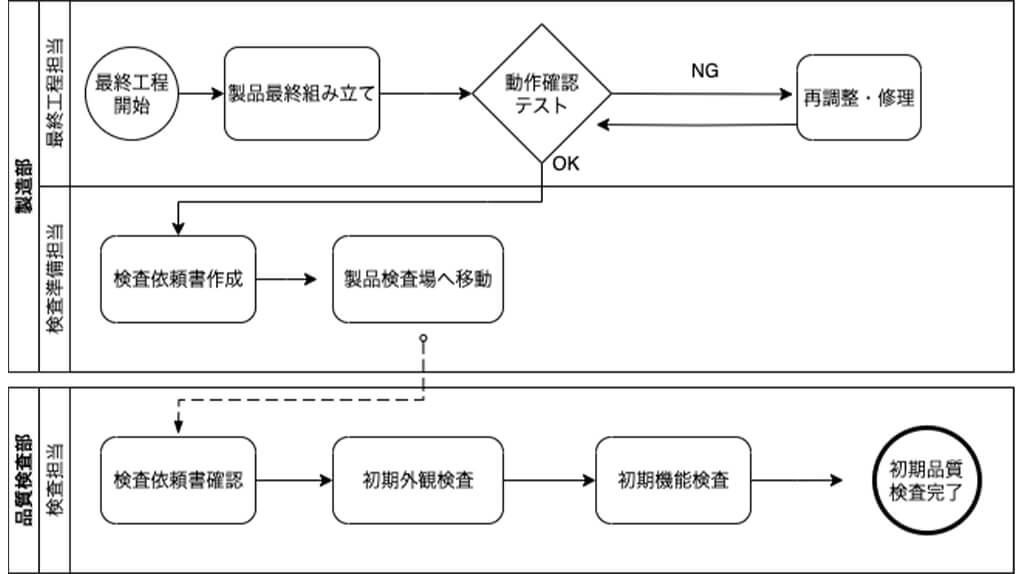
こうした図を作成することで、これまで個人の頭の中にあったり、口頭で伝えられたりしていた業務プロセスが、客観的な形で見えるようになります。
作業の重複や手待ち時間、不要な承認や情報が停滞するボトルネックなどの「非効率な部分」を、図に書き出すことでが浮き彫りにすることができます。
また、関係者全員が同じ「地図」を見て議論できるため、「言った」「言わない」の認識のズレがなくなり、共通認識を形成することができます。
さらに、特定の個人しか知らない作業手順が明確になり、それを他の人も理解できるようにすることで、技術継承や人材育成に役立てることができるでしょう。
なお、上図の表現方法は、「BPMN(Business Process Model and Notation)」という国際標準の表記法を活用しています。
ExcelやGoogleスプレッドシートの図形機能などを活用したフローチャートは、特定のルールがないため、作成者によって記号の使い方が異なったり、図形の色や線の種類がバラバラになったりしがちです。
複数人で作成・更新する場合、表記のルールを徹底しないと、解釈のズレが生じ、共通認識の形成が難しくなることがあります。
また、BPMNを活用した場合、BPMS(ビジネスプロセス管理システム)などのシステムに直接取り込んで業務を自動実行したり、リアルタイムで進捗管理したりすることができます。
BPMNを活用することで、図として可視化するだけでなく、それを直接業務システムに繋げ、DXの次のステップである「自動化」や「実行の最適化」へ移行させることが可能です。
関連記事:BPMNとBPMSについて詳しく知りたい方は、以下の記事も参考にしてください。
BPMNとは?業務プロセスを視覚化する国際標準の表記法
BPMSで、業務改善にとどまらない、業務改革を行う方法
業務フロー図作成のポイント
業務フロー図を作成するためのポイントは、いきなり会社の全業務を描こうとするのではなく、まずは「最も困っているプロセス」や「改善効果が大きそうなプロセス」に焦点を絞ります。
例えば、「最終検査から出荷まで」「特定製品の組立工程」といった改善対象の範囲を限定し、実際にその業務を行っている担当者や現場の作業員にヒアリングします。
そして、「どのように作業しているか」「何に困っているか」「どこで情報を受け渡ししているか」といった、「実際に今、行われていること(As-Is)」を忠実に聞き出し、記録します。
ポイントは「こうあるべき」ではなく「現実」を描くこと。無駄な作業や非効率なステップも、洗いざらい書き出しましょう。
洗い出した現状を、フローチャート作成ツールなどで作成していきます。
なお、現場での実際の作業風景を写真や動画で記録することも、後でフロー図に落とし込む際のヒントになるでしょう。
最後に、業務フロー図の各ステップで発見した「手待ち」「手戻り」「重複作業」「情報の滞留」などの無駄を、赤字や吹き出しなどで図上に具体的に書き込んでいきましょう。
データで裏付ける客観的な課題特定
業務フロー図を作成して「ここに無駄がありそうだ」という仮説が立てられたら、次はそれを客観的なデータで裏付けることが重要です。
「なんとなく」ではなく「数字」で示すことで、改善の説得力が増し、関係者の納得感も高まります。
既に社内にあるデータがある場合は、それらのデータを見直すだけでも、多くのヒントが得られます。
例えば、設備の稼働時間、サイクルタイム、停止時間、不良発生率、生産量などの生産データを見直し、どの工程で非稼働時間が多いか、不良品が多く出ているのはどのタイミングか、といった傾向を抽出します。
また、勤怠データから特定の部門や個人の残業時間を確認することで、一部に業務が集中している「属人化」や「ボトルネック」の兆候を読み取れる場合があります。
さらに、在庫データから特定の中間品や仕掛品がライン上で滞留している期間を把握することで、過剰な在庫や「作りすぎの無駄」を示唆することができます。
「ECRS」の原則で業務プロセスを磨き上げる
現状の業務プロセスを「業務フロー図」で可視化し、どこに無駄や課題が潜んでいるかが見えてきたら、いよいよ改善策を具体的に検討し、効率的な「未来の業務プロセス」を設計する段階です。
業務プロセスを改善するための最も基本的な考え方に「ECRS(イクルス)」というフレームワークがあります。
これは、現状の業務フロー図で洗い出した課題に対し、以下の4つの視点で改善策を検討していくものです。
Eliminate(排除)
普段行っている「作業」「承認」「記録」を見直します。
例えば、形骸化した二重チェック、複数部署への重複した報告書の提出、製品をラインから外して行う不必要な検査などがこれにあたります。
これらを見直し、不要なステップやプロセス自体をなくします。
Combine(結合)
複数の作業やプロセスステップを、一つにまとめられないか検討します。
例えば、品質検査と梱包作業を同じ場所で同時に行う、関連する複数の帳票をデジタル化して一つに統合するといったことです。
関連する作業を統合することで、移動時間や手待ち時間を削減し、効率を高めます。
Rearrange(交換/再配置)
現在のプロセスや作業の順序が適切かどうかを見直し、変えることで効率化を目指します。
例えば、部品の準備作業を前工程の空き時間で先行させたり、検査のタイミングを工程の最初の方に移して手戻りを減らしたりといったことです。
作業の順番や配置を見直すことで、流れをスムーズにし、ボトルネックを解消することを目指します。
Simplify(簡素化)
現在の作業を、簡素化・単純化できないか検討します。
例えば、複雑なマニュアルを写真や動画で分かりやすくする、専用の治具を作成して作業を容易にする、人間の判断が必要だった作業をデジタルツールで自動化するといったことが考えられます。
作業自体の負荷を減らし、誰もがミスなく行えるようにすることで、生産性向上と品質安定に貢献します。
このECRSの原則に沿って、現状の業務フロー図の各ステップを見直すことで、無駄のない新しい業務プロセスを検討します。
関連記事:ECRSについて詳しく知りたい方は、こちらの記事も参考にしてください。
業務プロセス改善のDXで使う「ECRS」とは、具体例や使い方を解説
そして、ECRSの視点で検討したアイデアを元に、「To-Be(理想)プロセス」を設計し、効率的で理想的な業務プロセスを新しい業務フロー図として作成します。
この際、デジタルツールをどこに、どのように組み込むかが、業務プロセス改善の成否を分けます。
例えば、「このステップはIoTセンサーで自動化する」「このデータ入力はRPAに任せる」など、具体的なデジタルツールの活用イメージも盛り込むことがポイントです。
業務プロセスを変革する代表的なデジタルツール
次に、デジタルツールの活用イメージを盛り込むためにも、業務プロセス改善に活用される代表的なデジタルツールとその活用イメージを紹介します。
RPA(ロボティック・プロセス・オートメーション)
RPAは、まるで人間のオフィスワーカーのように、PC上で行われる定型的な事務作業を自動化するソフトウェアロボットです。
繰り返し行われるデータ入力やファイル操作、システム間の情報連携などを、人の代わりに実行してくれます。
例えば、FAXやメールで届く受注情報をRPAが自動でシステムに入力してくれたり、各担当者が入力したデータをRPAが自動で集計し、グラフや表にまとめた報告書を管理者に作成してくれたり、在庫管理システムと連携することで、在庫数が一定値を下回ったらRPAが自動で発注書を作成・送信してくれたりといったことが可能です。
これにより、人が定型業務から解放され、残業時間削減や別の業務に時間をあてられるほか、ヒューマンエラーの激減や人件費抑制に貢献します。
IoT
IoTは、これまでインターネットに接続されていなかった設備などの「モノ」にセンサーなどを搭載し、ネットワークを通じてデータ収集や制御を行う技術です。
これにより、現場の状況をほぼリアルタイムで「見える化」し、迅速な状況判断と意思決定を支援します。
製造業における業務改善でのIoT活用として代表的な例は、設備稼働監視です。製造機械にセンサーを取り付け、稼働状況、温度、振動などをリアルタイムで監視します。
これにより、異常の早期発見や予知保全が可能となり、突発的な故障による生産ライン停止を防ぎ、稼働率の向上に繋げます。
関連記事:予知保全について詳しく知りたい方はこちらの記事も参考にしてください。
予知保全とは?IoT・AIの役割や導入プロセス、メリットや課題・事例を解説
また、原材料棚や仕掛品の置き場に重量センサーを設置し、残量を自動で把握することで、在庫管理を効率化することもできます。
これにより、手作業での棚卸しが不要になり、欠品防止や過剰在庫の抑制に貢献します。
在庫管理について詳しく知りたい方はこちらの記事も参考にしてください。
在庫管理とは?基本知識から目的、システムを活用した際のメリットなどを解説
AI
AIは、人間の思考プロセスを模倣し、学習・推論・判断などを行う技術です。
大量のデータからパターンを認識したり、複雑な状況を分析したりすることで、熟練者の知識や経験を「知能」としてサポート・代替し、業務の高度化や効率化を支援します。
例えば、カメラとAIを組み合わせることで、製品のキズや不良を高速かつ高精度で自動検査することができます。これにより、人手による検査の負担を減らし、見落としを低減させます。
また、過去の生産実績や受注予測、設備稼働状況などのデータをAIが分析することで、最適な生産計画を自動で立案したり、過去の販売データや外部要因から将来の需要を予測し、適切な生産・発注量を計画したりといったことも考えられるでしょう。
これにより、品質向上、生産効率の最大化、コスト削減、熟練者のノウハウ継承などが期待できます。
SaaS(Software as a Service)
SaaSは、ソフトウェアをインターネット経由でサービスとして提供する形態です。
自社でサーバーやソフトウェアを導入・管理する必要がなく、インターネット環境があればどこからでもアクセスできるため、低コスト・短期間で基幹業務をデジタル化することが可能です。
代表的なものとしては、生産計画、進捗、在庫、原価などを一元的に管理できるクラウド型の「生産管理システム」や、スマートフォンやPCから申請・承認ができる「勤怠管理・経費精算システム」、インターネットを通じてリアルタイムで音声・映像によるコミュニケーションが可能な「Web会議システム」などです。
期待できる効果としては、低コストでの導入、運用負担軽減、情報共有の効率化、意思決定の迅速化などが挙げられます。
これらのツールを選定する際のポイントは、「どんなツールを入れるか」から考えるのではなく、ECRSの原則で検討した「どういう業務プロセスにしたいか」という明確な目標に対し、最適なデジタルツールを「手段」として選ぶことです。
また、最初から完璧を目指さず、まずは部分的な導入や、トライアルプランの活用から始めてみるのも有効でしょう。
製造業における業務プロセスの改善事例
ここでは、実際に業務プロセス改善とデジタルツール導入によって成果を上げた製造業の事例をいくつか紹介します。
RPAにより年間16,000時間の工数を削減
とある大手精密機器メーカーは、事業環境の大きな変化とグローバル化を背景に、従業員の働き方改革を含めた業務プロセス改革と、現場の課題解決力の強化が課題でした。
そこで、ECRS原則の「Simplify(簡素化)」と「Eliminate(排除)」の視点から、RPAによる自動化を推進しました。
その結果、経理、人事、総務などの間接業務の定型作業自動化に加え、製品化に必要な試験のパラメータ設定と実験データの取得をRPAで自動化し、IoTとの連携による実験プロセスの自動化などをも実施しました。
その他にも、国内で60プロセスにRPAが適用され、トータルで年間16,000時間の工数削減を達成したほか、国内外23社へのRPA展開を実現しました。
また、現場の社員が自ら課題を発見し、RPAロボットを開発・運用するという、自律的な体質が醸成されたそうです。
これにより、システム化から取り残されていた領域の自動化が加速しました。
IoT活用で設備稼働状況をリアルタイム監視し生産効率を向上
とある医療機器メーカーは、本社工場と3つの工場を合わせて合計4カ所の生産拠点を有していました。
従来の生産管理システムは導入していたものの、伝統的なやり方を大きく変えていなかったため、設備稼働状況のリアルタイム把握が難しく、生産効率の改善が課題となっていました。
また、競争が激化する中で、生産現場の効率を高め、人手不足の解消も狙う必要がありました。
そこで、ECRS原則の「Simplify(簡素化)」と「Eliminate(排除)」の視点から、手作業での稼働状況記録や目視確認といった非効率な作業を排除し、情報収集プロセスを簡素化しました。
さらに、「Combine(結合)」の視点を取り入れ、散在する拠点の情報を一元的に把握できる仕組みを構築しました。
具体的には、複数の生産拠点にある生産設備にIoTシステムを設置し、すべての設備の稼働状況をリアルタイムで収集。収集したデータを統合し、工場内だけでなく、遠隔地からでも経営者やマネジメント層が設備の稼働状況を把握できる仕組みを構築しました。
さらに、蓄積した工作機械のデータを分析して加工計画を策定したり、予実比較や稼働日報を出力したりするシステムを開発しました。
そして、リアルタイムでの稼働状況把握とデータ分析に基づいた作業の見直しといった改善活動を進めた結果、設備稼働率が25%向上しました。
また、複数拠点にまたがる設備の稼働状況を一元的に可視化することで、拠点間の情報共有がスムーズになり、生産計画や進捗管理の精度が向上しました。
加えて、現場の改善点がデータとして浮き彫りになり、作業の見直しや効率化を進めることで、人手不足の解消にも貢献しているとのことです。
AI外観検査で人手不足を解消
とある食品メーカーでは、現場作業者の離職率が高く、熟練者が減少しており、教育コストも課題でした。
一方で、多品種少量生産で商品の製造が複雑化し、要求スキルの高度化が進んでいました。
特に、最終工程での異物混入や不良の有無の目視による抜き取り検査は、熟練スタッフの経験と集中力に頼っており、見落としのリスクや検査精度のばらつき、そして技術が成熟するまでに多大な時間を要することが課題でした。
このため、熟練不要な環境を目指し、人手不足を補い、ルーチン作業を自動化する技術革新が求められていました。
そこで、ECRS原則の「Eliminate(排除)」と「Simplify(簡素化)」の視点から、人手による抜き取り検査をAIによる全数検査に置き換え、検査作業の負担やばらつきを排除し、プロセスを簡素化しました。
また、「Rearrange(再配置)」の視点により、検査員の教育にかかるリソースを削減し、他の業務に再配置することが可能になりました。
このAI外観検査システムでは、包装された製品をカメラで撮影することで、製品内の異物混入がないかAIがチェックし、不良の可能性がある場合はプッシャー式の排除機構によって自動で排除しました。
導入当初は、過検知率30%という課題に直面しましたが、良品の追加学習を重ねることで、過検知率を低減させたそうです。
その結果、これまでの抜き取り検査から全数検査が可能となり、製品内の異物混入チェックを徹底。作業者の熟練度や集中力による検査精度のばらつきがなくなり、安定した品質で商品を製造できるようになりました。
そして、導入直後の過検知率30%という課題に対し、良品の追加学習を繰り返すことで、現在の過検知率は0.8%まで低下し、順調にシステムが稼働しています。
加えて、作業者は長時間にわたる目視検査負担の軽減や、検査員の育成にかかる教育費の削減にも繋がったそうです。
SaaS型基幹業務システム導入で情報連携を強化し業務を効率化
とある機器メーカーは、およそ70名の営業担当者が取引先への製品販売から仕入れ、発注、出荷、請求、回収までの一連のプロセスを担っていました。
以前から販売管理システムは導入していたものの、営業担当者ごとに数字入力の「ルール」がバラバラで、計上基準が統一されていませんでした。
そのため、会社全体としての売り上げや利益の実績が不確かになり、正確な経営状況を把握することが困難でした。
また、旧システムは本来の多機能性を活かせず、単なる「入力装置」としてしか機能していなかったため、各営業担当がExcelで別途集計作業を行うなど、非効率な手作業が頻発していました。
報告を受ける側も、金額の根拠確認に多くの時間を要し、Excelファイルの破損などのトラブルも発生していました。
そこで同社は、ECRS原則の「Simplify(簡素化)」と「Combine(結合)」の視点から、基幹業務システムの刷新と、それによる業務プロセスの標準化・簡素化を推進しました。
基幹業務システムの刷新では、販売、会計、人事給与を統合管理できるSaaS型クラウドサービスに変更し、会社全体としての計上基準を明確に定め、統一ルールでシステムへの数値入力を徹底しました。
また、販売管理システムと統合グループウェアを連携させ、受注や在庫手配、回収予定日の変更、売り上げ確定などの承認プロセスをワークフロー機能で自動化し、結果を販売管理システムに反映させました。
この連携によって、統合グループウェアのワークフロー機能で承認された受注、在庫手配、回収予定日の変更、売り上げ確定などのデータが、自動的に販売管理システムに反映される仕組みが構築されました。
これにより、手作業でのデータ入力や確認の手間が省かれ、業務効率化とデータ精度の向上が図られています。
加えて、Excelでの個別集計作業が不要になり、情報がシステム上で一元管理されることで、業務効率が向上。これまで、得意先1件に複数の営業担当者が対応する場合、評価按分集計作業がExcelで3時間かかっていたところが、10分に短縮されました。
特定の社員では、月約15時間の残業時間がほぼなくなるなど、残業時間削減にも貢献したそうです。
まとめ
これらの事例からわかるように、闇雲にツールを導入するのではなく、まず自社の業務プロセスを徹底的に可視化し、どこに無駄やボトルネックがあるのかを明確に特定することが成功の第一歩です。
デジタルツールありきではなく、ECRSの視点で既存の業務プロセスを見直し、改善できる部分を特定してから、最適なツールを選定することが重要です。
なお、業務プロセスの改善は、一度やれば終わりではありません。変化する市場や技術に合わせて、継続的に見直し、改善していく必要があります。
ぜひこれらの事例を参考に、業務プロセスの改善を検討してみてください。
無料メルマガ会員に登録しませんか?
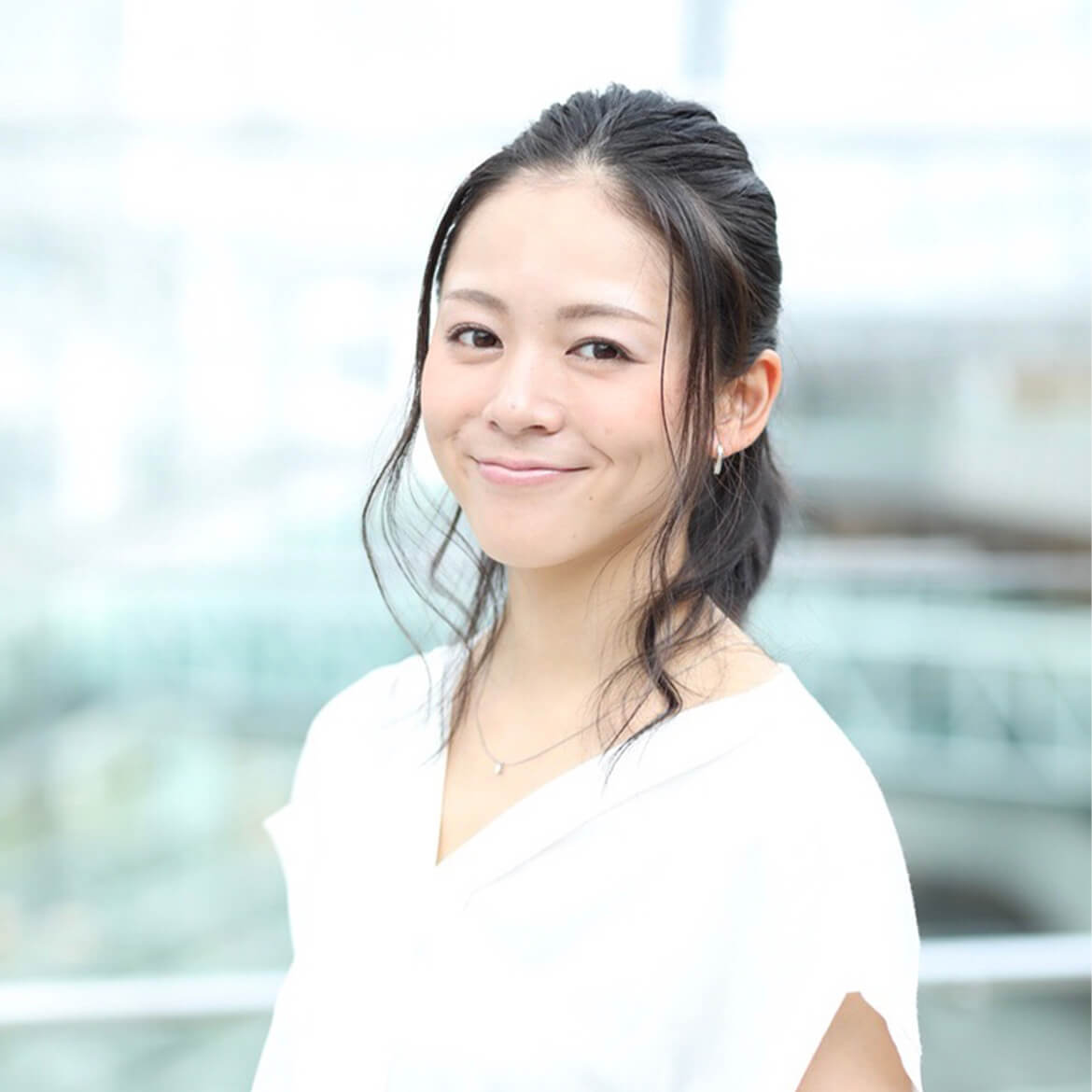
現在、デジタルをビジネスに取り込むことで生まれる価値について研究中。IoTに関する様々な情報を取材し、皆様にお届けいたします。