化学プラントなど、複数の製造工程を連続的に行うプロセス系プラントでは、各日再現する際工程で発生したプロセスの変動によって品質や生産量のばらつき等が発生する可能性がある。そのため、各工程で綿密な制御する必要がある。これまで、時間によって複雑に変化する入出力関係を適切に数値化・可視化することが難しく、最適な制御パラメータを特定する際は、専門的な知識を有するコンサルタントが調査・検討を重ねて改善を行ってきた。
NTTコミュニケーションズ株式会社(以下、NTT Com)は、横河電機株式会社と横河ソリューションサービス株式会社の3社で共同開発した「プラント向けデジタルツイン」を用いた実証実験で、自動探索した制御パラメータ値が実際の化学プラントの制御改善に有効であることを確認した。
プラント向けデジタルツインとは、NTT Comの「蒸留塔状態予測モデル」(※1)と横河電機の「プラント制御シミュレータ」(※2)とを組み合わせた仮想的な化学プラントの挙動を再現する仕組みである。
同実証実験では、プラント向けデジタルツイン上で、状態予測値に加えて化学プラントの挙動そのものをシミュレートし、最適な制御パラメータ値を約2500パターンの中から自動探索した制御パラメータ値と、横河ソリューションサービスのプラントコンサルタントが導き出した結果を比較検証したところ、両者が一致することを確認した。
また、NTT Comの持つ可視化技術「時系列アトリビューション解析技術」(※3)を用いてディープラーニングで生成された蒸留塔状態予測モデルを可視化し、専門家の知見と照らし合わせながら化学プラントの挙動を正しく再現できているか確認しながらプラント向けデジタルツインを構築した。
今後3社は、同実証実験で得られた成果をさらに高度化させ、プロセス系プラントにおける省エネルギー化の実現や生産の安定化に向けた技術開発を続けていく方針である。
※1 蓄積されたプロセスデータから反応器の状態変化を予測するモデル。
※2 制御対象に対して、測定値と設定値の偏差・積分・微分によって操作量の大きさを導出する制御手法(PID制御)を仮想的にシミュレートするもの。
※3 ディープラーニングを適用した予測モデルにおいて、予測結果に与える各入力の影響を数値化することが困難という問題に対し、時間変化する各入力の影響を可視化する技術。同実験では、”どの程度の遅れ時間をもって”、”正負のどちらの方向に影響を与えるのか”を可視化し、専門家の知見と照合した。
無料メルマガ会員に登録しませんか?
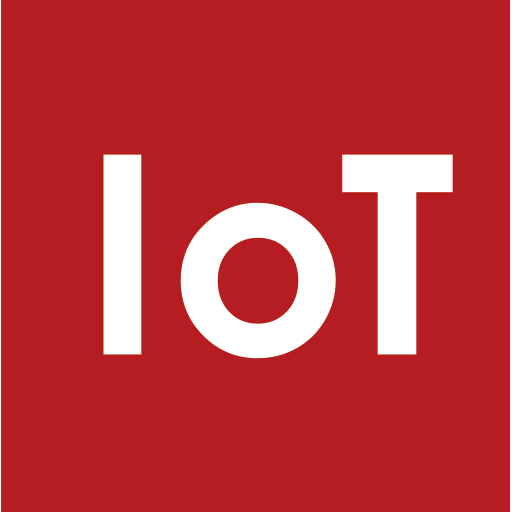
IoTに関する様々な情報を取材し、皆様にお届けいたします。