日本の製造業にとって、2011年3月に発生した東日本大震災は極めて甚大な被害を与えた。
被災した企業の中にはサプライチェーンの中核を担う重要な部素材を供給する企業も多く存在したため、直接的な被害を受けなかった地域の企業でも、供給がストップした部素材を原材料として使うセクターで経済活動に支障をきたすこととなり、広く国内外の企業に製品供給の影響が及ぶことになった。
原子力発電所事故の影響による計画停電などの電力制約や電力コストの上昇も、エネルギー多消費型の部素材産業などに特に重大な影響を与えたほか、風評被害による日本ブランドへの影響も深刻だった。
しかし、同年6月にはサプライチェーンの立て直しにより鉱工業生産に上向きの動きがみられるなど、早期復旧に向けた懸命な努力を重ね、想定を上回るスピードでの生産復旧を実現する企業も多数あった。
災害で明らかになった産業のダイヤモンド構造
東日本大震災が発生する以前は、自動車等の産業構造はピラミッド構造(トップ画 左図)、のようにイメージされていたが、東日本大震災を契機として、一部の重要部素材メーカーの生産停止が全体に影響を与えるダイアモンド構造(トップ画 右図)、であったことが明らかになった。
例えば、ルネサスエレクトロニクスのマイコン工場被災が国内外に影響を与えた事例があるのだが、特定のメーカーに中核部素材が集中することで、当該メーカーの生産途絶が完成品メーカーを問わず全体に波及するといった構造だ。
震災発生当時、ものづくりサプライチェーンにおける基幹部品や重要部素材の生産が停止したことが、全国的な生産停止や減産につながったため、大手自動車メーカー等はトータルサプライチェーンの可視化、地域的リスク回避、パートナー工場の設備状況の把握などに着手し、危機時においてもサプライチェーンを寸断させないためのリスク分散を進めた。
今後も、気候変動の影響により風水害が頻発することも懸念され、首都直下地震や南海トラフ地震の発生も想定される。過去の経験を活かして、自然災害への備えを強化することが重要である。数々の災害への対応を通じて改善を重ねた経験と組織対応能力が、今後の製造業の強みに変わっていくことが期待される。
(出典:モノづくり白書2019)
INSIGHT
一般的に製造業のサプライチェーンは、1つの企業を起点と考えるとその前後を考えたBCP(Business continuity planning:事業継続計画)を考える。
これは、1つ前のサプライヤにトラブルが生じた場合を想定して、代替サプライヤを考えておくといった計画だ。
しかし、これをもう少し俯瞰してみると、ここで指摘する「ダイアモンド構造」のサプライチェーンが浮き上がる。この事例では、ルネサスエレクトロニクスのマイコン工場被災が広範囲なサプライチェーンに波及するクリティカルポイントとなることが、実際に災害が生じるまで分からなかったのだ。
今後のBCP対策を考えるうえで、サプライチェーンを右から左へ受け渡す「リレー」のように考えるのではなく、川の流れのように上流から下流へ、複数の川が合流、分岐するイメージを持ち、どこか1点に流れが集中する特異点こそ最大リスクと考え、対策をとるべきなのだ。
(IoTNEWS スマートファクトリー領域アドバイザー 鍋野)
無料メルマガ会員に登録しませんか?
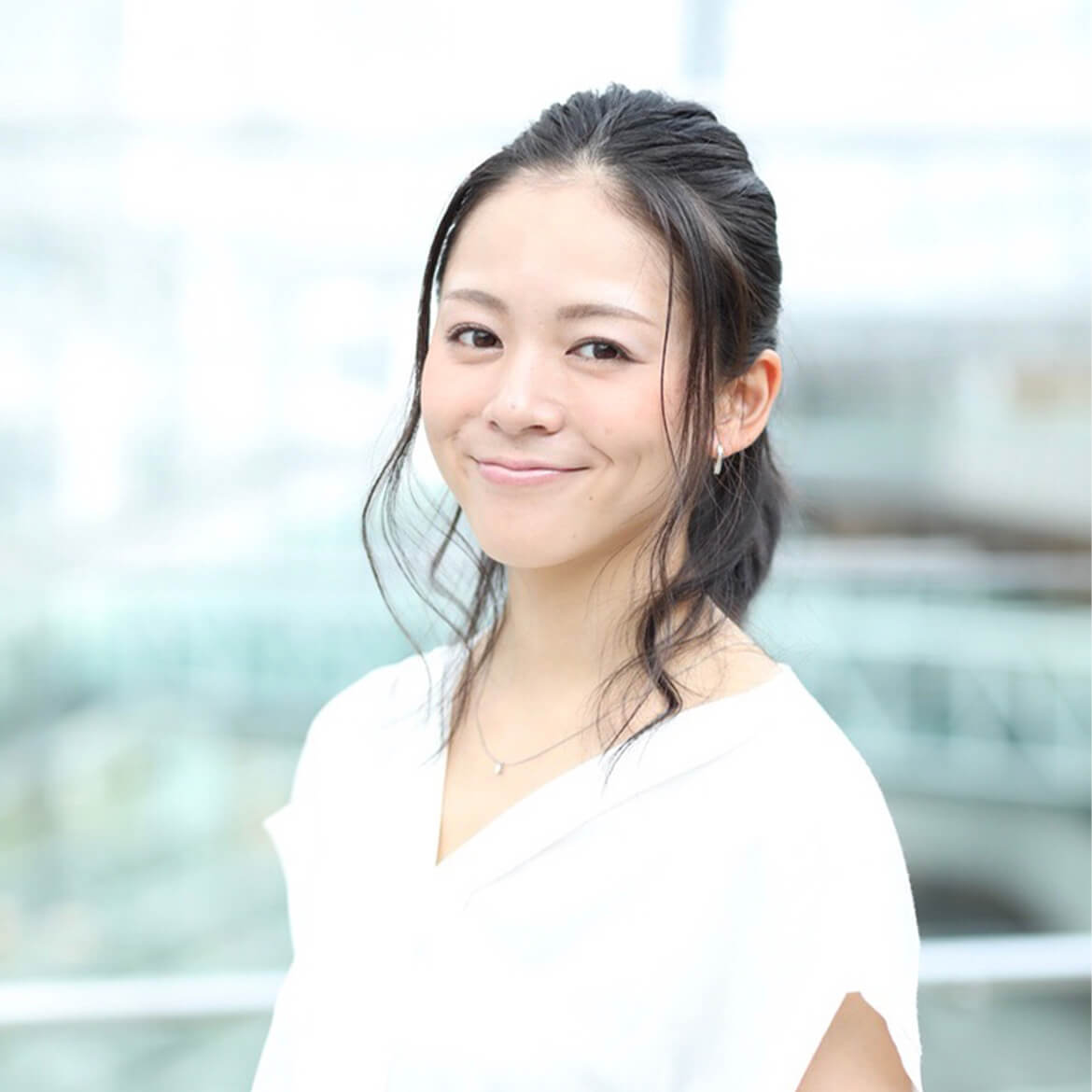
現在、デジタルをビジネスに取り込むことで生まれる価値について研究中。IoTに関する様々な情報を取材し、皆様にお届けいたします。