世界のものづくりを支える工作機械のグローバルリーダー、ヤマザキマザック(略称:MAZAK)。同社が現在、最も注力している分野の一つがスマートファクトリーだ。昨年11月には主力工場である美濃加茂(みのかも)製作所(岐阜県美濃加茂市)をスマートファクトリー化し、稼働を開始している。
美濃加茂製作所のスマートファクトリー化には、大きなチャレンジがあった。それは、第一工場と第二工場の再編だ。
これまでは、それぞれの工場が部品加工から完成品の組立までを一貫して手がけていた。しかし今回、第一工場で組立、第二工場で部品加工を行う一体型の生産体制に再編した。以前のように一つの工場で一つの製品をつくる場合、特定の機種の需要が落ちると工場間で繁閑の差が生じてしまう。しかし、あらかじめ工場別で機能が分かれていれば、大がかりな機種移管を行わずに、需給の変動にフレキシブルに対応できる。
だが、物理的に離れた工場間で生産工程を統合することは、一筋縄ではいかない。特に大変なのがモノの流れ(物流)の管理だ。そこで同社は、新たに物流管理システム「ID TRACKING PLUS」を独自開発することで、難題をのりこえた。RFIDタグを貼付することで、すべてのモノの「位置」「数量」「滞留時間」を可視化し、仕掛品の削減と在庫最適化を実現するソリューションだ。
このほど、「ID TRACKING PLUS」の開発を手がけたヤマザキ マザック株式会社 iSMARTプロジェクト グループリーダー 石田修一氏、主任 藤木周平氏、長谷川雄基氏、植松慎平氏の四名に、同プロジェクトの背景や成果について話をうかがった(聞き手:IoTNEWS代表 小泉耕二)。
「多品種少量生産」ならではの課題
IoTNEWS 小泉耕二(以下、小泉): 「ID TRACKING PLUS」を開発した背景について教えてください。
ヤマザキマザック 石田修一氏(以下、石田): 弊社は2015年に「Mazak iSMART Factory」と銘打ち、スマートファクトリーの取り組みを米国工場にてスタートさせました。愛知県大口町にある本社工場は日本でのスマートファクトリー化の第1号として2017年から稼働しています。そこで構築したソリューションを他工場へ横展開しており、今回は美濃加茂製作所をスマートファクトリーとして刷新し、昨年11月に稼働を開始しました。
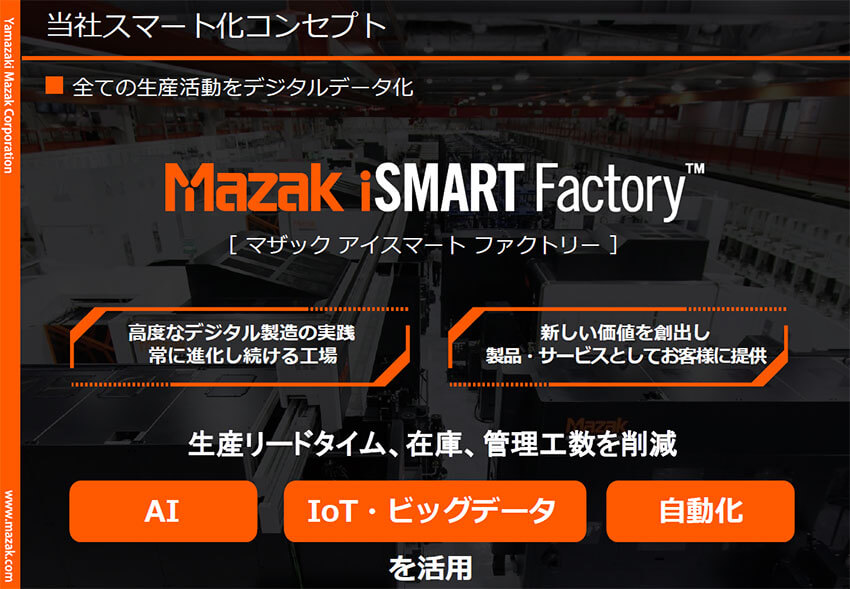
石田: 美濃加茂製作所のスマートファクトリー化のポイントは、第一工場と第二工場の生産工程の再編で、これは本社工場にはない課題でした。美濃加茂製作所ではこれまで、それぞれが部品加工と完成品の組立を一貫して行っていました。第一工場では複合加工機などを、第二工場では中・小型のマシニングセンター(MC)や旋盤を生産していたのです。
しかし今回、二つの工場で一つの製品を一貫生産できるしくみに再編しました。通常ならこれはとても難しいことですが、美濃加茂製作所は第一工場と第二工場のあいだの距離が比較的近い(約1.5キロメートル)こともあり、再編にふみきったのです。
小泉: 物理的に近いとはいえ、やはり別々の場所にあると、大変なことも多いのではないかと想像します。
石田: おっしゃるとおりです。何よりも、加工と組立のラインが別々の工場にありますから、工場間でのモノの流れをきちんと把握できるしくみをつくる必要がありました。そこで開発したのが、物流管理システム「ID TRACKING PLUS」です。RFIDタグを活用して、すべての原材料や仕掛品(以下、「部材」とまとめて表記する) の位置や数量、滞留時間を可視化できるようにしたのです。
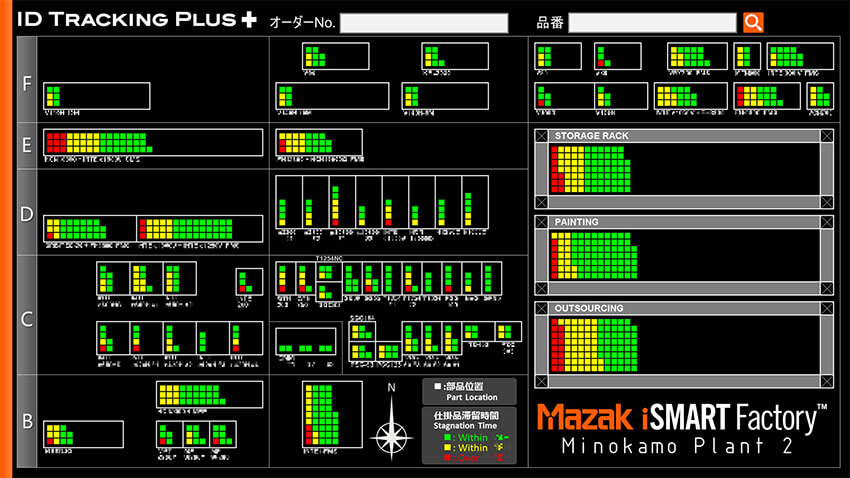
石田: これは、美濃加茂製作所に限らない課題でした。大前提として、工作機械メーカーである弊社は多品種少量生産であり、1台の加工設備で数百種に及ぶ部品加工を行っています。多種多様な加工品が工場内を渡り歩きますので、短納期を実現するには、非常にこまかい工程管理が必要になるのです。
設備機械における可視化は「Smooth Monitor(スムース モニター) AX」という弊社のツールを使ってすでに行っていました。しかし、物流の管理についてはまだまだ属人的な方法に頼らざるをえない状況でした。そこで、美濃加茂製作所の再編をきっかけに、新たな物流管理のIoTソリューションを構築できれば、弊社の他工場のみならず、同じ課題をかかえるお客様に対しても、改善例のご提案になるのではないかと考えたのです。
実際に、今回開発したシステムを使ってモノの流れを可視化することで、意外な場所での滞留や、現場任せであった部材の移動経路やタイミングなどが見えてきました。見えないものは改善することができません。ただ、これまではそうした実態が非常に見えづらかったのです。
無料メルマガ会員に登録しませんか?
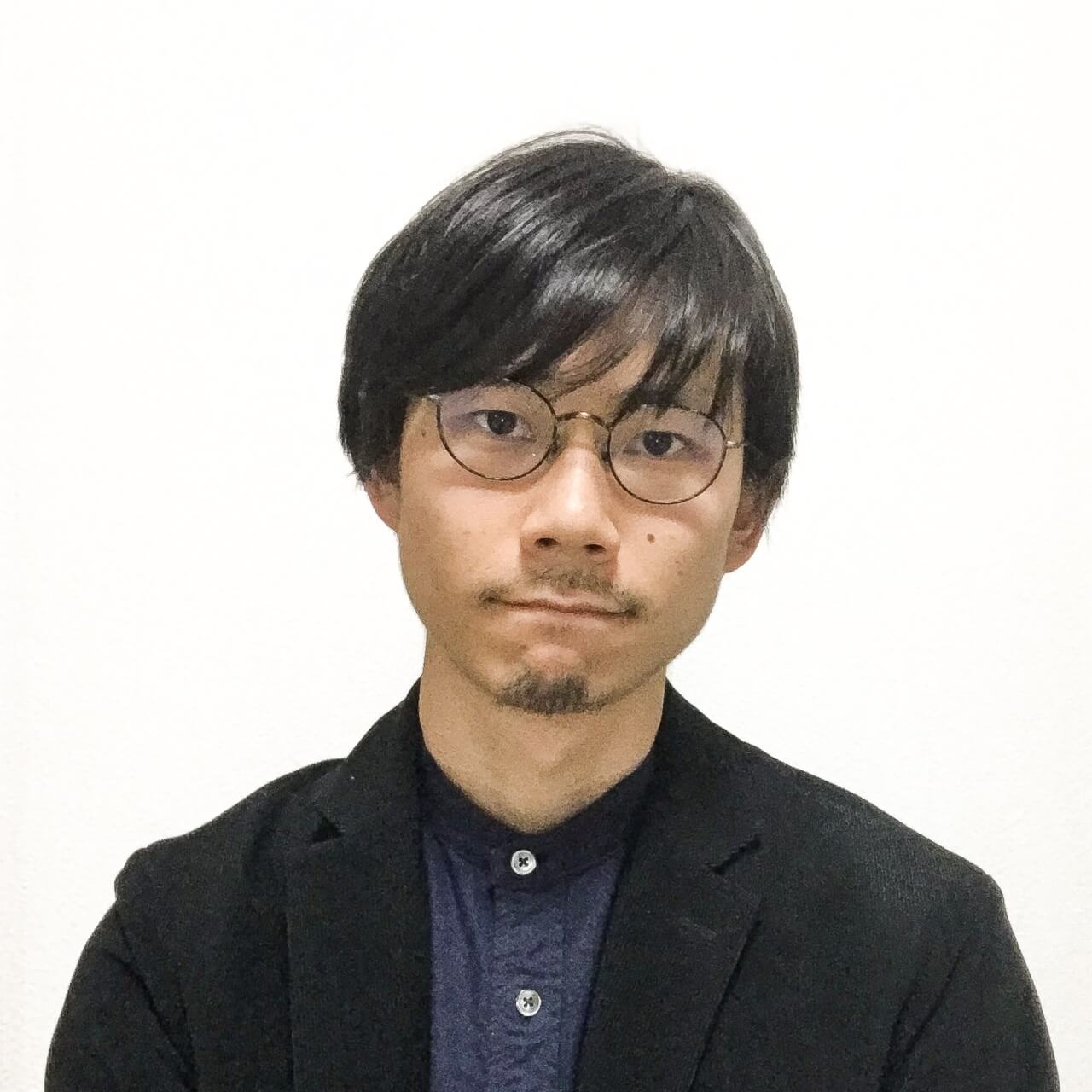
技術・科学系ライター。修士(応用化学)。石油メーカー勤務を経て、2017年よりライターとして活動。科学雑誌などにも寄稿している。