現場の声から、次々と新たなツールが生まれている
小泉: 他には、どのようなツールをつくられているのでしょうか。
植松: 工場間の輸送管理を行うツールが一つです。新しくなった美濃加茂製作所では、第二工場でつくった部材をトラックで運び、1.5 kmほど離れた第一工場へと届けます。このとき、RFIDタグで出荷情報をとっていますから、第一工場の担当者は、ほしい部品が今どこにあるのかが、パソコンやタブレットの管理画面を見ればわかるのです。これまでは、工場の担当者が電話やメールで確認していましたが、その必要がなくなりました。

長谷川: また、応用編として部材の移動と滞留履歴が追えるようなツールもつくっています。出庫から台車での運搬、組立までの履歴情報を分析することで、搬送先や経路の最適化を行い、物流全般の効率化に役立てられます。
石田: あとは、意外と現場に好評なツールが、RFIDタグを探す機能です。専用のハンディターミナルをかざすと、自分が探しているRFIDタグが近くにあれば、画面上で反応するというものです。台車にはたくさんの部品が積まれていて、たまに作業者が見落として「部品が無い」と勘違いすることがあります。そんな時はこの機能を使えば、簡単に目的の部品を見つけだせます。
小泉: そうした様々なツールは、初めからイメージして設計されていたのですか?
長谷川: 想定通りのものが多いですが、あとから「こういう視点もあるんだ」と気づき、新たに開発したケースもあります。繰り返しになりますが、現場から出てきた要望にスムースに対応できるので、さらに現場から要望があがってくるという好循環が生まれています。そうして、次々と新しいツールが生まれているのです。

石田: 「ID TRACKING PLUS」の導入により、部材を探すためにかかる時間を大幅に短縮しました。今回の美濃加茂製作所の再編は、生産性を5割向上させることを目標としています。「ID TRACKING PLUS 」の導入は、この目標達成に向けた生産改善にかなり大きく寄与しています。もちろん、システムだけではなく、現場レベルでのカイゼンも含めてですが。今後は、RFIDから収集したデータを集計・分析して、新たな付加価値を生み出していこうと考えています。
たとえば、組立ラインでは、使い終わった部材のRFIDタグは捨てるのではなく、「使った順番ごと」にスキャンしてデータを残していく。このデータから実現場における「組付け手順」の検証や工程改善ができるし、組立て易い製品設計へ活かすことも可能だと思います。とくに試作は組立手順も試行錯誤しながらですから、生産現場と開発担当者がそういうデータをもとに協力し合って、より良い製品開発に貢献できるような取り組みも行っています。
小泉: 美濃加茂製作所で開発した「ID TRACKING PLUS」のソリューションは、他の工場にも横展開していくのですね。
石田: はい。順次、他工場へ横展開を進めます。「Mazak iSMART Factory」を通じて、お客様に新しい工場のあり方をご提案していく予定です。
小泉: 本日は貴重なお話、ありがとうございました。
同社の取り組みについては、ウイングアーク1st株式会社の事例ページにも掲載されています。ぜひご覧ください(リンクはこちら)。
無料メルマガ会員に登録しませんか?
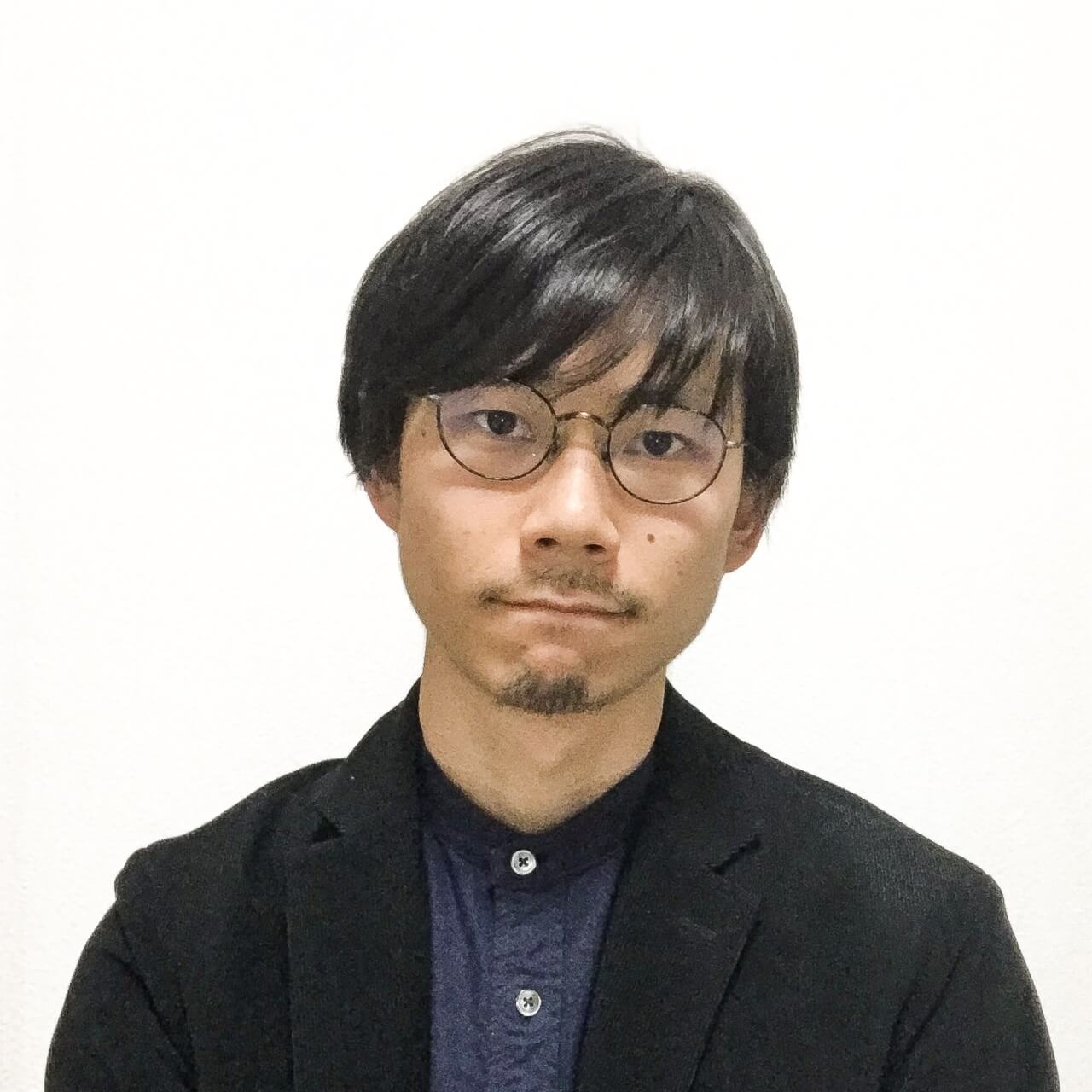
技術・科学系ライター。修士(応用化学)。石油メーカー勤務を経て、2017年よりライターとして活動。科学雑誌などにも寄稿している。