株式会社ミチは、音声認識を利用して、製造現場の「人」を可視化する「Hitorigoto」というサービスを提供している。
本稿では、製造現場の課題や音声認識の可能性について、株式会社ミチ 代表取締役 中崎瞬氏(トップ画左)にお話を伺った。(聞き手:IoTNEWS代表 小泉耕二)
人が行う細かな作業を可視化していく
IoTNEWS 小泉耕二(以下、小泉): 音声認識をして、製造現場の生産性向上を支援するサービスを提供しているということですが、具体的なサービス内容について教えてください。
ミチ 中崎瞬氏(以下、中崎): 音声認識を活用して、現場の作業者の方に音声で作業を入力してもらい、どんな作業にどれくらいの時間を使っているのかを可視化し、業務改善に役立ててもらうというサービスです。
数百人規模の少量多品種の製造現場では、班長や職長と呼ばれるリーダーがおり、その班長が生産の計画や進捗の把握、作業指示や品質管理などを行っています。
しかし班長の仕事は煩雑で、現状では膨大なコストと時間がかかっているのにもかかわらず、作業場全体の把握は細かくできていないという課題があります。
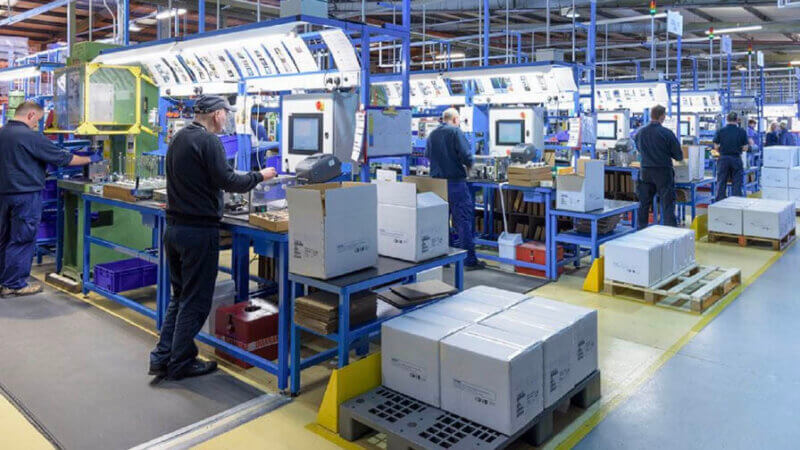
また、班長の技術継承は難しく、今後人手不足になることを考えると、なるべく自動化する必要があります。
そこで、班長の仕事をサポートするために、音声を活用して作業の把握をしたり、作業指示をしたりする「Hitorigoto」という、音声認識を利用したサービスを提供しています。
本来、班長がストップウォッチを持って作業者の作業時間を測る生活分析を行うのですが、作業者が声で「開始」と「終了」を入力すると、作業にかかっている時間を可視化することができます。
また、生産が終了した際に、「生産を終了します」と「Hitorigoto」に音声を入力すると、「終了報告をしてください」といった作業指示を表示することもできます。
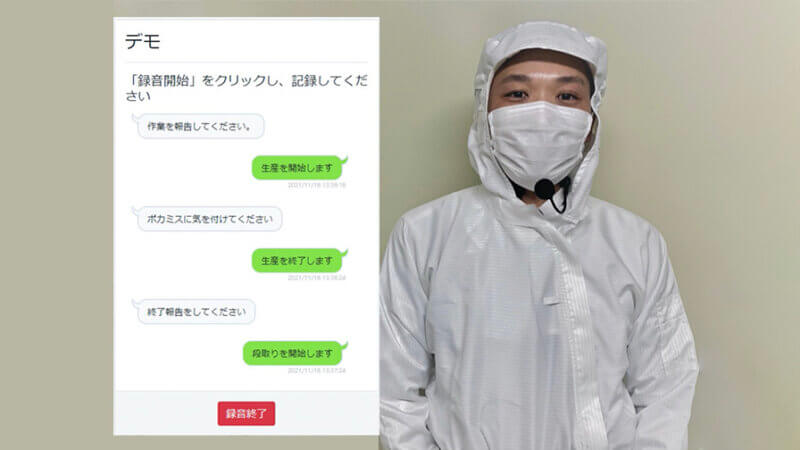
小泉: 少量多品種の製造現場では、工程が自動化されていたとしても、設備に商品を持って行ったり、設備が止まっていないか確認したりと、人が携わっている部分がどうしても出てきてしまいますよね。
そこを細かく可視化することを目的に「Hitorigoto」を導入することで、人の動きも改善していくというサービスなのですね。
現場の導入ハードルを下げるネーミング
小泉: 個人的に「Hitorigoto」というネーミングはすごく良いなと思いました。
中崎: ありがとうございます。実際に「Hitorigoto」を使って作業をしている場面を想像すると、ひとりごとを言いながら作業をすることになりますし、音声を使ったサービスだとイメージがつきやすい名前をつけました。
また、こうしたソリューションで管理思考な名前をつけると、現場の抵抗感を持たれてしまう可能性があります。
そこで現場目線のネーミングにすることで、「管理される」や「人を切られてしまう」というようなマイナスのイメージを払拭したいと考えました。
小泉: 実際に現場としても無駄がなくなり、スムーズに作業を行えた方が、ストレスがないと思いますし、その時間を違うことに回すことができるので、まずは導入してもらうことが大切だと感じました。
「製造業」と「音声」の親和性
小泉: 「Hitorigoto」の仕組みはどのように構築しているのでしょうか。
中崎: Googleの音声認識を活用し、弊社のシステムとAPI連携しています。
作業者の音声を「Hitorigoto」の音声認識がテキスト変換し、その音声データをAPI連携したGoogleの音声認識システムに送ります。
音声データと文字データの変換をGoogleのシステムで行い、「Hitorigoto」のシステムでは「生産」や「終了」といった言葉をタグづけしているので、認識して分析を行い、タグに準じた指示を表示する、という仕組みです。
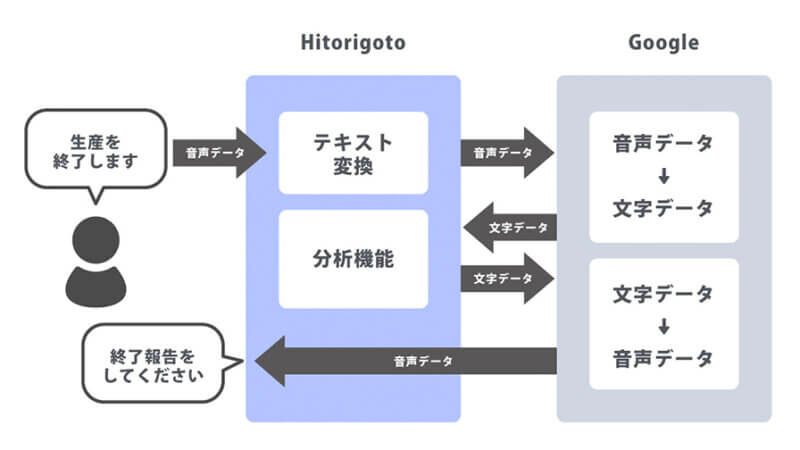
現状では1社ごとにタグを登録しているのですが、将来的には統一してデータを蓄積していき、資産になるような仕組みにしていきたいと考えています。
小泉: 汎用的な音声応答エンジンを業界特化のものにしているのですね。
中崎: そうですね。製造現場に適した音声応答エンジンの活用を、「Hitorigoto」で実現しようとしています。
製造業の現場では作業をしているので手が塞がっていることが多いですし、手袋をしているとスマホを触れないといった状況があります。そうした環境の中でも作業者の作業を可視化しようと思うと、音声は非常に適したツールです。
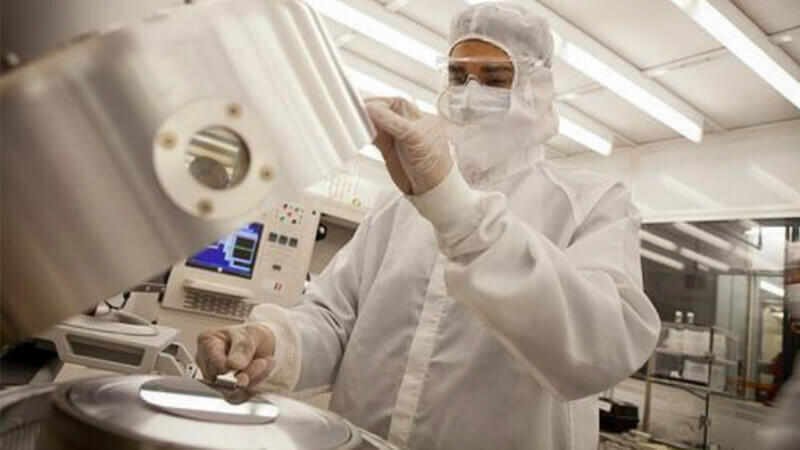
実際に多くの企業から、「音声に興味を持っているが、ベストなソリューションがない」という声を聞くので、そうした企業の手助けになれば、と思っています。
改善余地を探して効率化を実施する
小泉: このサービスはどのようなきっかけで始めようと思ったのですか。
中崎: もともと父親が製造業のコンサルタントを行っていたので、製造業の方と話をする機会が多くありました。そしてディスカッションする中で、現場の課題を感じていました。
多くの企業が、差別化を図るために少量多品種に対応した工場にしていくという流れがありますが、特に受注生産だと完全な自動化は難しいですし、人手不足の問題も深刻です。
製造業を維持するためには何かしらのアイディアが必要だと感じたことがきっかけです。
小泉: 実際に「Hitorigoto」を導入した企業ではどのような効果が得られたのでしょうか。
中崎: 数百人規模の半導体工場に導入して、作業者の見える化を行うことで、「検査」が25%を占めていることが分かりました。検査が25%も必要なのかどうかを確認したところ、「昔から行っているから」という理由だけで今でも実施されていたことが分かりました。
そこで過剰検査を減らすことで、生産性があがったという事例があります。
また、人が休憩している間、設備が稼働していないということが「Hitorigoto」を導入したことにより分かった、という事例もあります。
30分段取りが必要な設備の場合でも、人の休憩の時間は決まっているので、設備の段取りが終わっていなくても休憩に入ります。
それであれば、段取りが終わってから休憩に入る、というふうに、時間を移動させるだけで設備が動いていないロス時間を減らすことができます。
こうした細かな効率化を実施するために、改善余地を「Hitorigoto」によって探すことができます。
小泉: 一人当たりの作業の状態を細かく可視化することによって、何の作業にどれくらいの時間が割かれているかが分かり、それに対して改善ポイントを考えることができるということですね。
今までだと作業に振り回されていた班長も、本質的な改善策を考えるために動くことができますね。
中崎: そうですね。現場の工程は標準化されているので、それを落とし込んでいき、現在の班長の仕事を「Hitorigoto」で賄えるようにしたいと思っています。
ただ、多品種少量だと標準化するのに手間がかかりますし、現状の仕事を回すのが手一杯で、そうした改善活動に時間が割けないという企業も多いので、課題をひとつひとつクリアしていきたいです。
製造現場の管制塔を担う
小泉: それでは最後に、今後の展望についてお聞かせください。
中崎: 最終的には、「Hitorigoto」が現場の管制塔のような役割を担えるようにしたいと思っています。作業者だけでなく、設備や工場もつないでいくことで、全体を把握した上で最適な指示を促していく、というビジョンを描いています。
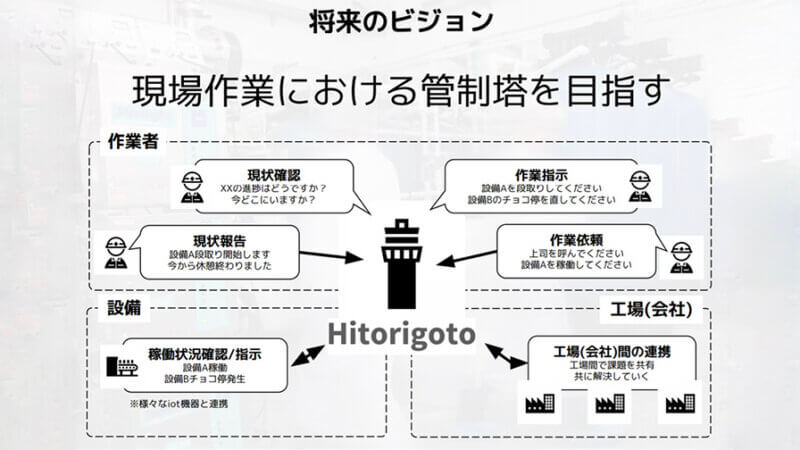
様々な現場を訪問していると、共通の課題に取り組んでいるという印象を受けます。ですから、一つの現場での解決策を見つけたら、それを横展開していき、会社間の無駄を無くしていければと思っています。
また、「Hitorigoto」で取得したデータをAIによって分析をして、人の表彰を行うなどの、評価基準にしていくことも可能なのではと考えています。
小泉: 今後の展開も楽しみにしています。本日は貴重なお話をありがとうございました。
無料メルマガ会員に登録しませんか?
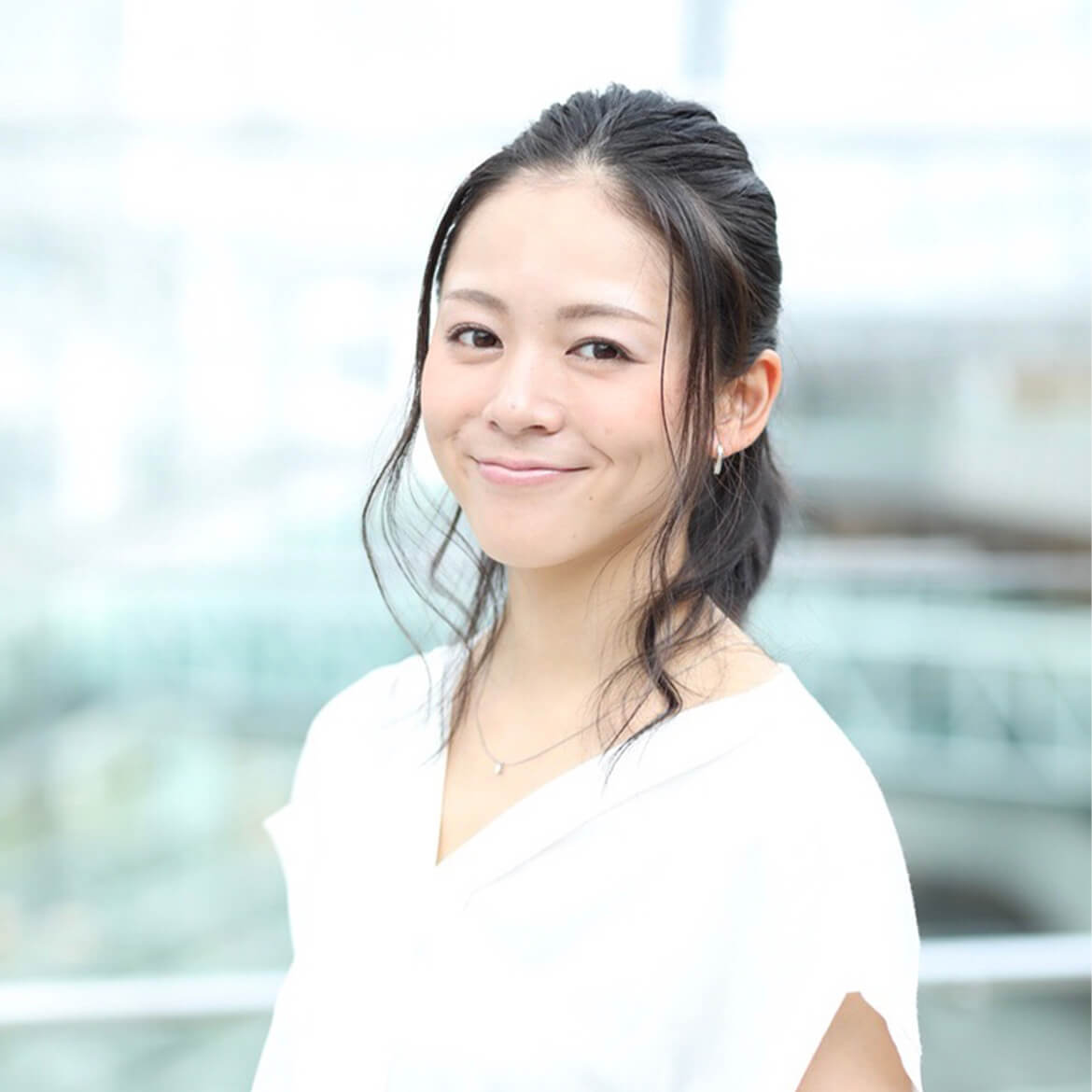
現在、デジタルをビジネスに取り込むことで生まれる価値について研究中。IoTに関する様々な情報を取材し、皆様にお届けいたします。