製造業のデジタルトランスフォーメーションは、現場から経営層まで、さまざまなレイヤーで進んでいる。しかし、現実的には、社会全体でいろんな解決しなければいけない問題があり、それにはかなり具体的な施策が重要になる。
そこで、法政大学デザイン工学部システムデザイン学科教授、IVI理事長の西岡靖之氏に、IVIで進めているいろんな取り組みやお考えについてお話を伺った。
第二回目は、デジタル化が進まない生産現場の課題」についてだ。
西岡靖之氏は、1985年に早稲田大学理工学部機械工学科を卒業。大学卒業後は、国内のソフトウエアベンチャー企業でSEに従事し、1996年に東京大学大学院・博士課程を修了。東京理科大学理工学部経営工学科助手、法政大学工学部経営工学科専任講師、米国マサチューセッツ工科大学客員研究員などを経て、2007年から法政大学デザイン工学部システムデザイン学科教授。
専門分野は、知能工学、経営情報工学、情報マネジメントシステムの標準モデルの研究。一般社団法人IVI(インダストリアル・バリューチェーン・イニシアティブ)理事長も務める。IVIは、モノづくりとITの融合で可能になる「つながるモノづくり」を「ゆるやかな標準」というコンセプトでの実現を目的に設立された製造業を中心としたフォーラム。
人材施策、技術開発、教育をソフトウエア基盤で構築できるかが重要
IoTNEWS 小泉耕二(以下、小泉): 二つ目のテーマは、「製造業の置かれている現状」についてです。一口に製造業といっても「板金」や「組み立て」など様々あります。そこで、大きく全体でみて「製造業」、今どのような状況に置かれているのか、そして今何が問題なのかを教えてください。
西岡靖之 法政大学教授(以下、西岡): これまで日本には、「匠の技」や「日本的なものづくり」「現場改善」などの美しい物語がありました。それはいまだに生きていると思います。ただ、勢い的にはそれを上回るようなデジタルの流れや標準化、グローバルなモノづくりのサプライチェーンなど、スケーラブルな、少し次元の違うモノづくりにシフトチェンジが行われていると感じています。
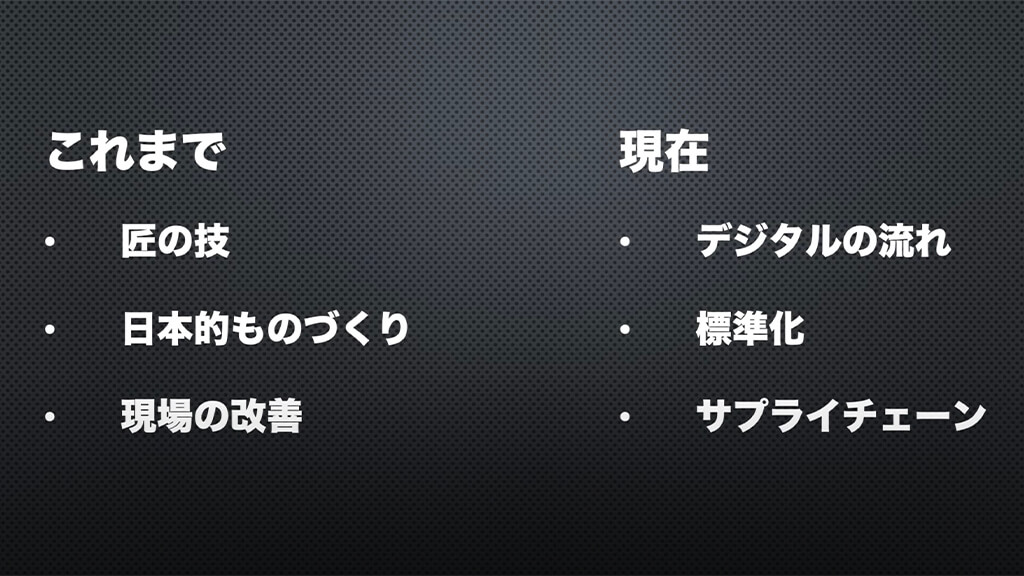
小泉: それは、いわゆる「ものづくりDX(デジタルトランスフォーメーション)」ですよね。
西岡: 「DX」という言葉は非常に多岐的なもので、いろいろな意味合いがあると思います。ドイツ政府の産業政策「第四次産業革命(インダストリー4.0)」は、2011年の発表当時、ディスラプティブ(破壊的)なテクノロジーで、そのターゲットの最優先候補には製造業がありました。
これには、「工場がどんどん自動化することで、今まで行ってきたことを、ソフトウエアに置き換えることができる」または「データが中心になり、データを持っている所がリアルな工場を凌駕(りょうが)する」という、ある意味「脅し」の要素がありました。しかし、実際にデジタル化が進む中で、必ずしもそうした理論が当てはまらないという実感を製造業の人たちは得ています。
ただ、その理論はまだ脈々と動いています。データを持っていなければ品質管理もできないですし、顧客開拓やニーズの把握も難しいでしょう。過去の不具合のデータを持っていれば未然に防げることも、紙の山になっていたり、単に言い訳をしたりしていては、品質を担保することができません。
さらに、データは活用することができます。例えば、M&A(企業の合併・買収)で買った会社に職人が100人いたとして、過去30年のデータを保有していれば、それを解析することでモノづくりに役立てることができます。
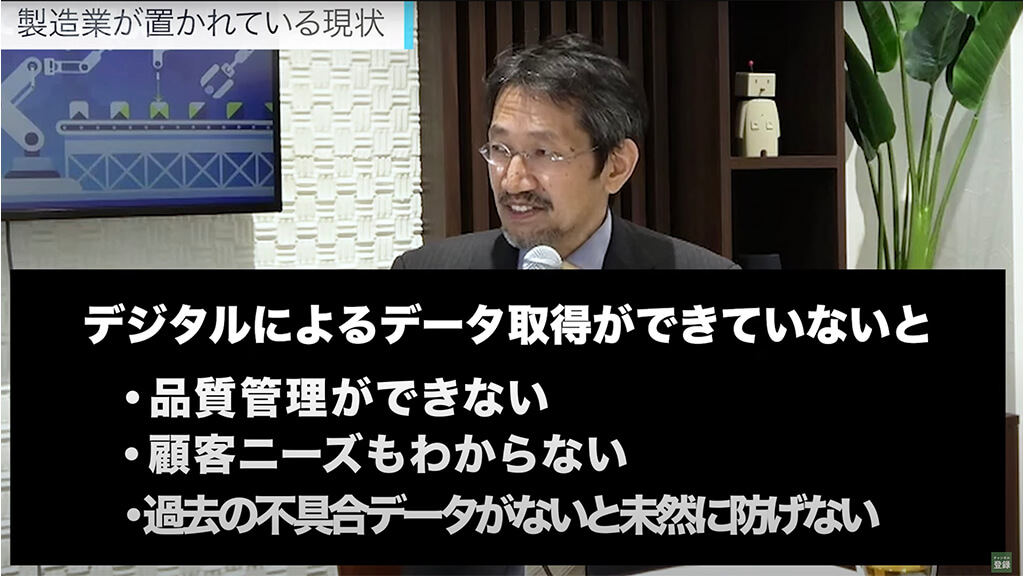
リアルは決してなくなりませんが、そこに対するソフトウエアやデータのレバレッジ(てこの原理)がどんどん効き始めています。そして、それはネットワークでつながっていれば遠隔で実行することが可能です。
また今回、コロナ禍で、遠隔でできることと、できないことがある程度わかってきました。そうした中で「これは現場に行かなくてもできる」「海外工場のオペレーションでも、この部分は出張しなくてもできる」ということが、ある程度学習されてきましたわけです。
一方で、日本の製造業は、工場の中にIT技術者がいないと、IT企業に丸投げの部分があって非常にピンチな状態です。私としては、製造業のDXは「ビジネスモデルや製品のアーキテクチャを変えましょう」というのと同じく、社内の人のスキルや役割分担、競争優位性を出すための技術開発、新しい教育をソフトウエアをベースに構築していけるかだと思っています。このことで製造業ではひとつの大きな仕分けがされようとしていると感じています。
小泉: 工場の中を見ると、ある程度、大量生産の必要があった企業は、それなりの自動化をしています。そういう意味では、広い意味でのテクノロジーをうまく使って、大量生産のときに、なるべくムダがないようにしていくことや、早くしていくということは、以前から取り組まれています。これは、現場で起きていることを把握するために、インターネットを活用して遠隔で見るようなことです。
ここまでは分かるのですが、本当に工場の人たちが悩んでいることは、発注などを生産計画に反映する際、今の工場のキャパがどれくらいあり、どれくらいのものが作れるのかということです。どの程度余力があるのかも分からない。そもそも発注の量もいまいち把握しておらず、営業の人は何となく知っているが、確実に受注できるかどうかも曖昧(あいまい)。うまく生産計画を立てることができない。
さらに現場のこともしっかりと把握しているわけではないため、作りすぎたり、逆にムダを減らそうとして納期が遅くなったりと、機会損失が起きている。こうした所のデジタル化の動きは、どのような状況なのでしょうか?
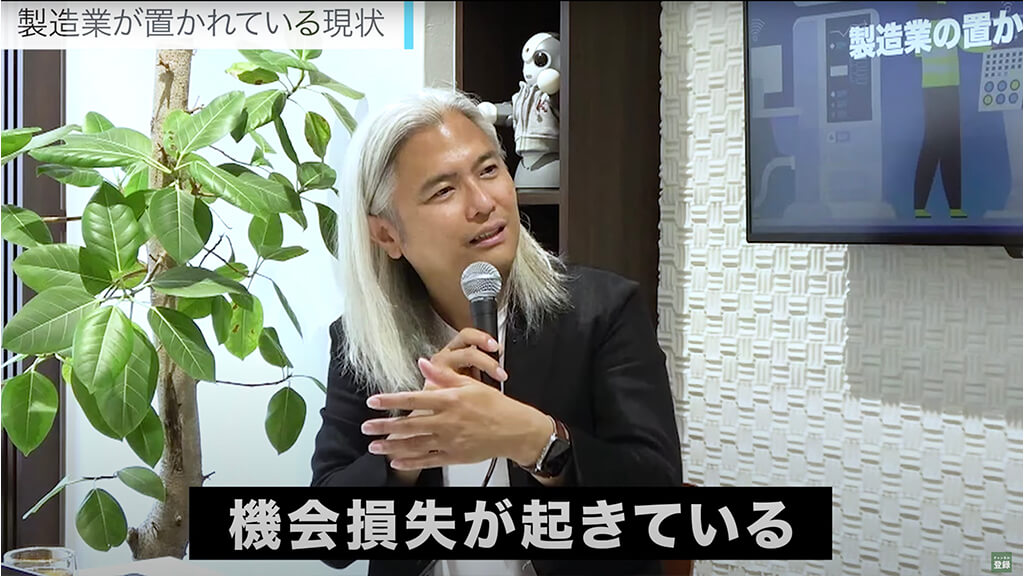
西岡: 通常のIT、情報システムで、まず着手できるのは、QCD(品質・コスト・納期)でいう「D」の部分です。クイックレスポンスやスケジューリング、計画の同期など、いわゆるサプライチェーンとエンジニアリングチェーンのふたつがあるとしたら、「仕入れて生産して、売る」というサプライチェーンの軸は、比較的短期になります。これは、場合によっては前日に注文が来て、翌日には出荷するため、仕入れもその何日か前に発注するという流れです。
こうしたモノの流れと情報の流れがある一方で、設備を作ったりプロセスを変えたり、品質で手戻りがあったときに直したりするエンジニアリング系の軸は比較的長期になるのです。そして、サプライチェーン側は短い分だけITが発揮しやすい。
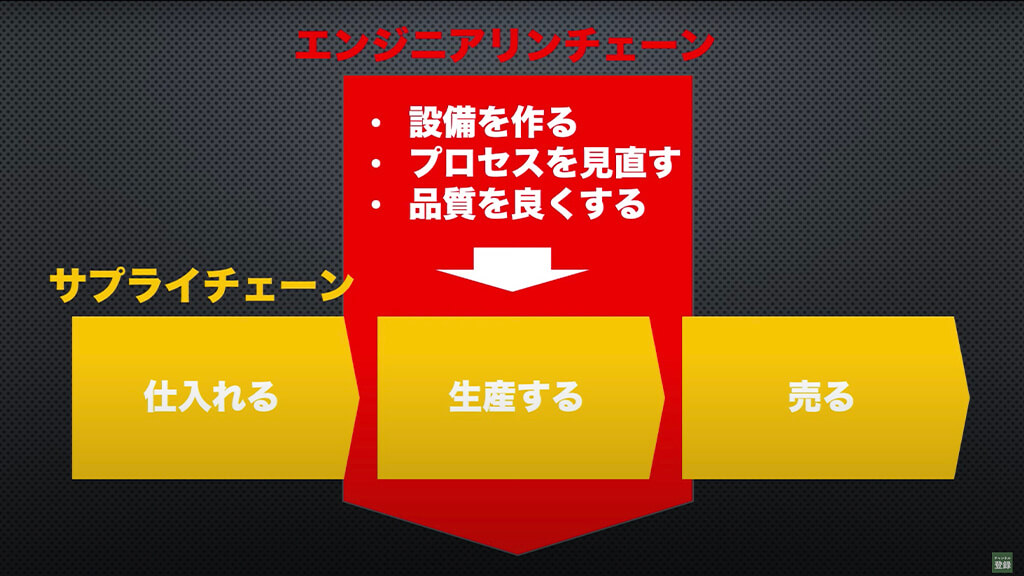
実際に計画を立てるのも、前日の晩に翌日の計画を立てたり、作業手配したりするのは、コンピューターに入力すれば一瞬でできます。エクセルに手で入力していたのでは相当大変だから、コンピューターに任せましょうというわけです。ただ、これを実現しようとすると、ある程度のデータがそろっている必要があります。そして、生産が合わないのは、このデータが取れてないということが多いのです。
計算はロジックさえ組めばできるので、在庫が見えないのは在庫を誰もいちいち入力しないからです。そこでIoTを活用する。そして、5割以上が正確であれば大体回ります。ただ、2割、3割の正確さだと、結局ない方がよいとなるわけです。大量生産で物量を追求する場合には、おそらく人件費の安いところにかないません。
一方で、サプライチェーンでの日々の売り買いではなく、工場やプロセスをひとつひとつ作る効率を上げていく部分が重要です。これは、売ったものがどういう品質であるのか、仕様変更があったときに変えられるのか、過去と同じモノを作ってくださいという、エンジニアリング系の一品一様のもの作りや、オンリーワンでここでしか作れないということになります。
これまでは職人や経験者の知見に頼ってきましたが、それをデータ化して、知識として工場や会社で共有するのです。難しいことのように聞こえますが、人がやっていることなので、それなりに実現することができます。
だから、全部を置き換えようとは思わず、半分から6割ぐらいはデジタルツールに置き換えて、検索できるようにする。それでも困ったときにはOBに聞けばいい。私は、デジタルとアナログを融合する上で、一番効果的なのはエンジニアリングではないかと思っています。
デジタルの利便性は“双方向コミュニケーションができる”こと
小泉: まさにそういった事例を、広島県の中小工場を取材したときに聞きしました。彼らはまず、マニュアルを全部電子化したのです。
これまで新人は業務について経験者に聞いて教えてもらうしかなく、経験者も同じことを何回も聞かれる。そこで、紙のマニュアル作ったけれど検索ができなかった。まずはそれをデジタル化しようと取り組んだ。デジタル化したら、その後は手書きで付け加えたりしながら、マニュアルを育てたそうです。少しずつ育てていると、「秘伝のタレ」のように知見が蓄積されていく。
その工場は変種変量を求められており、毎回違うものを作らなくてはならない。そこで、経験が浅い人でも、ある程度の作業が行えるように、そうした取り組みを行っていました。
エンジニアリングの過程でデジタルを活用する際に、「IoT」や「AI(人工知能)」という言葉に沿って施策を考えるのではなく、この事例のように、地味なことから始めるのも一つの手だと感じたのですが、西岡先生はどう思われますか?
西岡: 基本的にマニュアルは完成したら更新されず、それを守ってくださいというのが一般的です。しかし、本来は新しい製品や仕様に合わせて変更をかけたり、派生したマニュアルができたりとバージョンアップしていく必要があります。
さらに、書く人と読む人の役割を決めるべきではなく、工場側からも現場で感じた課題のフィードバックを行って、品質管理や生産技術の人にも伝える必要があると思うのです。私は、マニュアルはでき上がったものではなく、コミュニケーションツールとしてのメディアだと思っています。
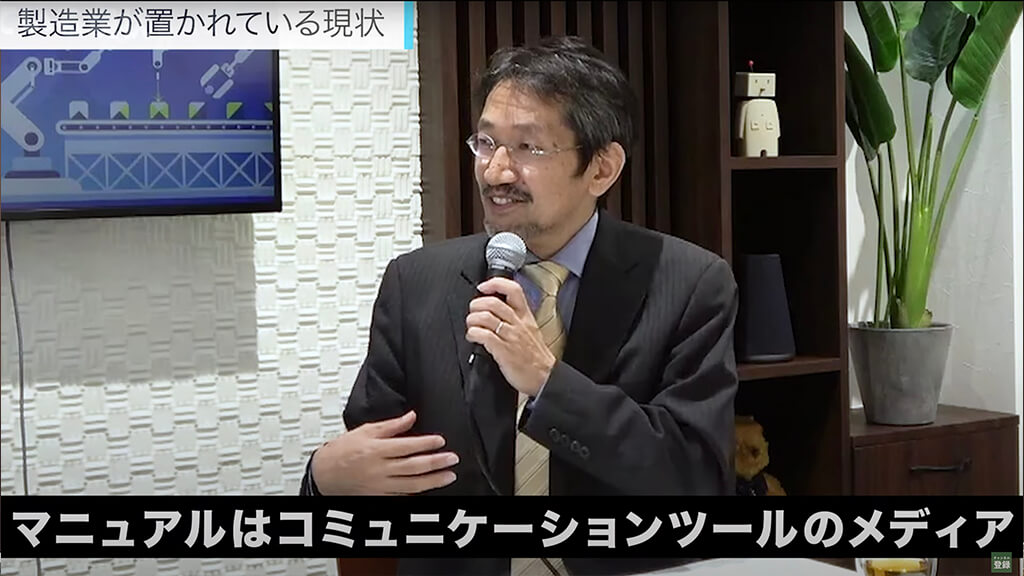
IoTにしろITにしろ、「デジタルで便利になる」という意味合いは、「計算する力」というよりは、「双方向でコミュニケーションができる」という意味です。それぞれ持った知識や実践した結果を相互にやり取りができ、それが蓄積されて、より洗練されて工場に残っていくことが重要なのです。
そのための道具という形で捉えると、企業の大小は関係なく、手書きでもよいのです。手書きが相手にきちんと伝わり、検索できればいい。そういう発想はとても大事だと思います。
小泉: 今回の話をまとめると、製造業ではサプライチェーンとエンジニアリングチェーンの交差するところに問題がある。サプライチェーンは、ある程度のデータがきちんと取れていれば、割と手早く始められる上、取得しているデータは在庫や発注の量といった、割と可視化しやすいものが多く、短期間で実行できる。
一方でエンジニアリングチェーンは、今まで人が手でやってきた部分のため、簡単にはデジタルに置き換えられないけれども、実はできる余地はたくさんある。そうした「余地」をうまく見つけて少しずつ実行していかないと、変種変量に対応できなくなり、サプライチェーンが今度は回らなくなる。
いくらデータが取れて、可視化ができていても、作る人が止まってしまったら結局発注は裁けない。対応しようと思うと、結局はエンジニアリングで効率的なやり方を見つけざるを得ないというわけですね。(第3回に続く)
この対談の動画はこちら
以下動画の目次 製造業の置かれている現状(19:43〜)より
無料メルマガ会員に登録しませんか?
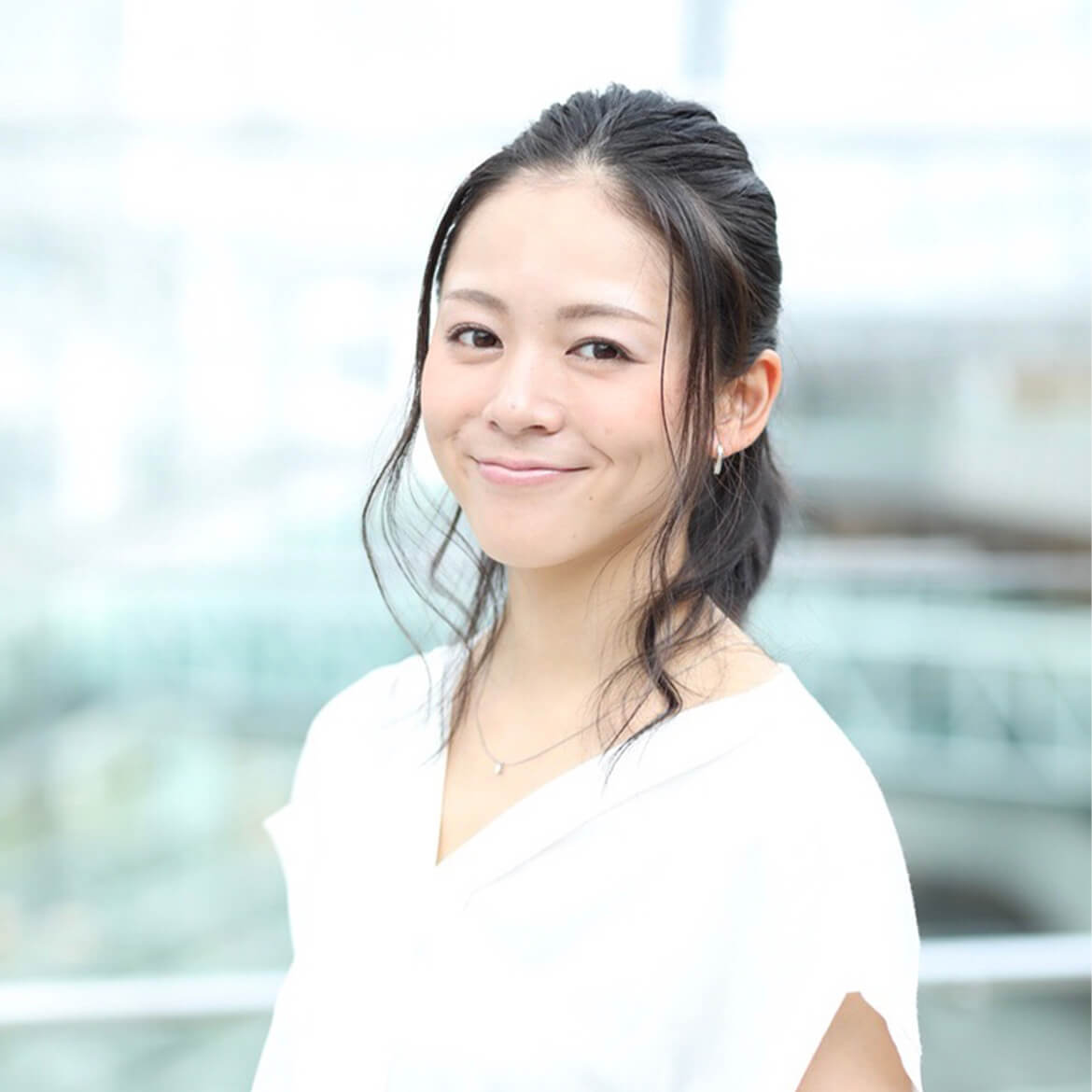
現在、デジタルをビジネスに取り込むことで生まれる価値について研究中。IoTに関する様々な情報を取材し、皆様にお届けいたします。