合成樹脂は、原料投入・製造・製品取出しの工程を1回毎に実施するバッチ生産により生産されるのが一般的で、その際、製品品質を担保するために、反応工程の途中で人によるサンプリングや分析、反応進捗判断の作業を繰り返しながら、調整原料の投入を行う。
これを行うことで、反応工程中だけでなく、反応前工程の温度、圧力などの動向が製品品質に影響を与えるため、全工程にわたる運転状況の把握と考慮が必要となる。
そのため、作業は煩雑かつ属人的になる傾向があり、製品の品質検査合格率のばらつきといった課題があった。
こうした中、DIC株式会社と株式会社日立製作所(以下、日立)は、2021年3月から合成樹脂製造プラントの運転自動化を図るデジタルツイン技術の実用化に向けた協創を開始し、第一フェーズとして、DICの国内3工場で製造される樹脂製品を対象に、「理論モデル」「現場データ」「AI解析」を組み合わせた反応予測モデルの構築と精度の検証を実施してきた。
その結果、これまで熟練者の経験則で感覚的に認識していた反応影響因子を定量的に把握できるようになった。
この実証をもとに両社は、統計分析などを活用したインフォマティクス(情報科学)の手法により、製造条件を最適化する「プロセス・インフォマティクス」を活用したシステムを実用化し、DICの国内プラントで来年1月から本格稼働させると発表した。
このシステムは、AIなどを用いた反応予測モデルにより、サイバー空間上にプラントの運転状況を再現する。加えて、プロセス・インフォマティクスを活用することで、目標とする品質値に向けた調整タイミングや投入量を決めるための最適な運転条件を導き出し、それらをフィジカル空間(現場)にフィードバックすることを可能にしている。
具体的には、目標とする粘度などの品質値を得るための運転条件を自動で算出し、「ヒートマップ」として作業員に明示する。これにより、バッチ生産に適切な運転条件を選択できるようになる。
ヒートマップでは、製造時の追加原料量(縦軸)と追加タイミング(横軸)の組合せにより、製品品質が所定の値に到達するための最短運転時間の予測結果を可視化する。
これにより、作業員は現状の予測結果から高い効果を見込める運転操作を選択可能だ。なお、色の濃淡は運転時間の差を表し、濃いほど短い時間となっている。
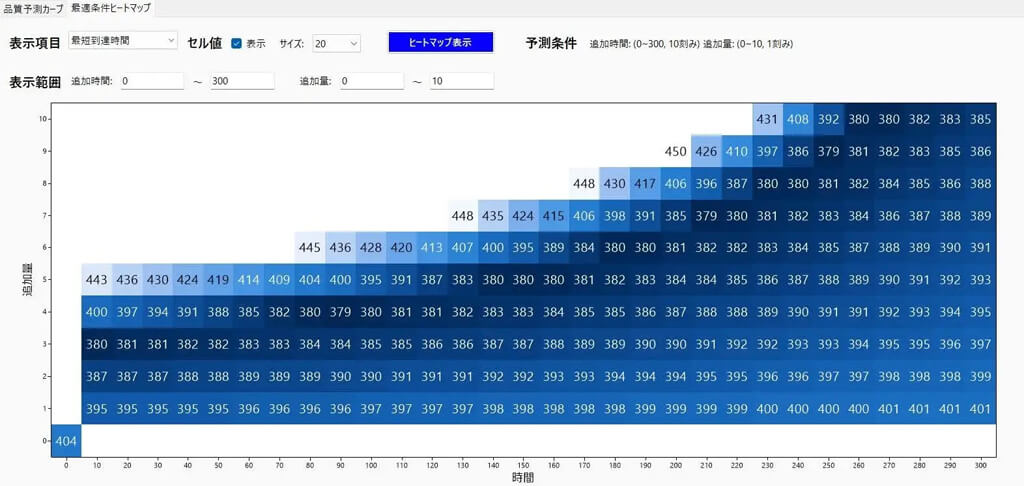
このシステムを活用することで、現場でのサンプリング確認回数の低減、品質の安定化、作業員の作業効率向上、新製品導入時の立ち上げ期間短縮に寄与する。
DICと日立は今後、同システムをDICの国内3拠点、海外1拠点へ展開していく予定だ。
なお、両社が構築した反応予測モデルは、DICにおけるバッチ生産の複数の製品群や連続生産への適用検証を行っており、DICの国内外の樹脂製造全般への展開も見据えているとのことだ。
無料メルマガ会員に登録しませんか?
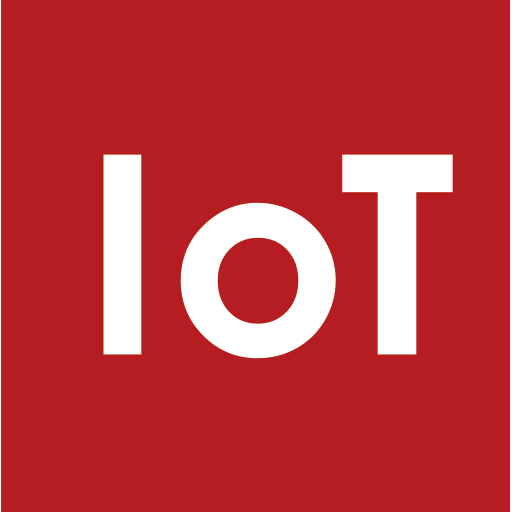
IoTに関する様々な情報を取材し、皆様にお届けいたします。