IoTNEWSの運営母体である株式会社アールジーンは、4月20日、製造業のIoT/AIをテーマにセミナーを開催。本稿では、同セミナーに登壇したウイングアーク1st株式会社 営業・ソリューション本部 製造ストラテジックビジネスユニット ユニット長 荏原光誠氏の講演の内容を紹介する。
ウイングアーク1stは「見える化」を専門とする日本のソフトウェア企業だ。同社が提供するさまざまな製品の中でも、IoTによって現場から上がってくるデータをリアルタイムで見える化する「MotionBoard」は多くの企業に導入されている。
同社は製造業にも注力しており、日本の製造業が中心となったエコシステム、インダストリアル・バリューチェーン・イニシアティブ(IVI)にも参画し、IVIプラットフォームの作成に関わっている。
今回のセミナーでは、「MotionBoard」を使った製造業のリアルタイム情報の「見える化」を中心に、各企業の導入事例やプロジェクトの進め方、IoTで成果を出すためのポイントについて、製造ストラテジックビジネスユニット ユニット長の荏原氏に語っていただいた。
製造業に「見える化」が必要な理由
製造業における情報活用(データの活用)には、2つの軸があると荏原氏は指摘する。一つは、製造現場における「横の軸」だ。IoTによって工場内の設備やモノ・ヒト、あるいは工場と工場をつなげ、そこで得た知見を生産性の向上に活かすといった領域だ。
もう一つは、経営、管理部門、現場の3つの層をつなぐ「縦の軸」だ。管理部門は各現場のデータを集約・分析し、さらに経営側はそれを見て収益を把握し、将来を予測する。
ここでは、現場から上がってくるデータをいかに管理部門や経営者にとって見やすいカタチに「見える化」し、その結果得られた知見を現場にフィードバックできるかが重要となる。
製造業にとって最初の壁となるのが、横の軸。荏原氏によると、製造現場から得られるデータの中で、「整理されたデータ」は20%しかないという。
「整理されたデータ」とは、データベースで管理されており、すぐに見える化や分析に使える状態のデータのことだ。一方、残りの80%は「整理されていないデータ」、つまりすぐには使えないデータだ。
たとえば、設備のデータ。ログデータはたまっていても、分析に活用していない。あるいは古い設備のためデータを取得できないなど、さまざまなケースがある。
他には紙の帳票など、データはそこにあるがデジタルではないものや、匠の経験や勘など、ヒトの”頭の中にある”情報などだ。これらの整理されていない大半のデータをすべて集約し、現場での「見える化」を実現することがまず求められる。
そうした横と縦の一連のしくみを一気通貫で提供するプラットフォームが、ウイングアーク1stの「MotionBoard」だ。セミナーでは実際に荏原氏が「MotionBoard」を起動し、デモンストレーションも行いながら説明した。
「MotionBoard」のクラウドサービスは月額30,000円から利用可能。ダッシュボードでの「見える化」だけではなく、設備が停止したときにタブレットやスマホとも連携して通知するなどのサービスも包括的に提供している。
AI(機械学習)の機能も導入し、不良品を低減するソリューションも提供。たとえば、射出成型機を使って樹脂製品をつくるような場合に、温度や樹脂の均一性などのデータから、どの要素が製品不良に影響しているのかをAIが導くという。
金型メーカーでの事例
工場内に古い設備があり、そもそもデータを取得できるような状態にない場合でも、他メーカーのセンサーやコントローラから「MotionBoard」に接続が可能だ。荏原氏は、金型メーカーT社の事例を紹介した。
T社では、ヒトがレポートに書く情報に揺らぎが生じることを問題に感じていたという。たとえば、11時10分に作業が終わった場合でも、日報には11時に終了したと書いてしまうというようなことがあったのだ。
そこでT社は、1990年代末頃からNC設備を導入し、機械から自動でデータを集められるようにした。しかし、全台を切り替えるわけにもいかず、データを自動で取得できる設備は一部に限られていた。
そこで、ウイングアーク1stはシムトップス社と連携。信号を取得したい電気配線に電流センサーをクランプし(工事なし、取付時間:45分)、シムトップス社の「MC-Web CONTROLLER」を使ってデータを自動で取得し、古い設備でも「見える化」ができるしくみをつくったのだ。
「今では、古い設備でも簡単にデータを集められるツールがそろっている。IoTはとても進んでいる」と荏原氏は述べた。
旧式の設備からデータを集められるようになった結果、T社ではさまざまな気づきを得たという。たとえば旧式のプレスでは、ヒトが報告する作業時間と設備から自動で上がってくる作業時間にずれが生じていることに気づいた。差が大きい時では、設備からわかる作業時間の方が、ヒトが報告した作業時間よりも約3倍も長かった。
その理由を深堀していくと、入力時間の誤差という単純な問題ではなく、担当者によってプレスの打ち方が大きく異なることがわかった。そもそも、そこに「ルール」がなかったことが問題であり、その問題点を共有し、新たにルールをつくることで作業の改善につながったという。
なお、ウイングアーク1stとシムトップス社は、共同開発した「見える化」のしくみを、「MotionBoard for MC-Web CONTROLLER」としてソリューション化し、5月9日より提供を開始している。
「見える化」プロジェクトの進め方
ウイングアーク1stは、「MotionBoard」を通じて蓄積した製造業でのノウハウを活かし、コンサルティング事業も行っている。荏原氏は3つ事例を紹介。今回は、その中から鋼管をつくっている中小製造企業の事例を紹介する。
鋼管業界は今、2020年の東京オリンピックに向けて建設ラッシュが続いており好調だという。そのため、その企業も売上が上がっていた。しかし、受注が好調で忙しくなると、リアルタイムの生産状況や在庫状況を把握できていない、人出が足りていないなど、さまざまな課題が一挙に露呈してきたという。
それらの課題を同社とウイングアーク1stで共有したところ、「売上は上がっているが、利益が出ていない(つまり、コストが大きい)」ということが見えてきた。そして、さらに深堀していくと、新しい設備の購入など投資はしているものの、「その投資がよいのか、悪いの判断をする基準がそもそも曖昧」ということに気づいたという。
そこで、投資の基準を明確にすること、つまり「ものさし」をつくることが必要であり、そのためにまずIoTで現場の実態を把握することで合意し、プロジェクトを開始した。
具体的には、「将来的に目指すべきゴール」を決めたうえで、STEP0からSTEP3まで目的別にステップを分けて取り組んだ(上図)。STEP0は実証実験であり、2か月間にわたって行った。
STEP3終了時にアンケートをとったところ、「工機械の稼働状況と自分の作業量を見える化することで、目標と現在の実績の差がわかり、ペースメイクが可能になった」、「出張先からリアルタイムで工場の様子がわかるようになった」、「ソリューションの使い勝手がいいため、社員の意識が向上した」などの声が聴かれ、さらなるデータ活用の取り組みにつながっているという。
荏原氏は、製造現場のIoTで成果を出すためには、「スピード」が重要だと述べた。「見える化ができたら、それを管理者やマネジメントに早く見せることが大事。データをただ蓄積していても意味がない。何ができるかを早く見せることで、関係者がひろがっていく。関係者を巻き込まなければ、IoTは進んでいかない」(荏原氏)
また、OT(Operational Technology)とITの融合、つまり現場とIT、異なる立場の担当者が協力関係を築くことが重要だと荏原氏は指摘。「ITの人は現場に対し、今見えていないことが見えてくることの楽しさを理解してもらうことが大切。そのためにはまずきっかけづくりが必要で、コミュニケーションやツールを楽しんで使えるような工夫が重要になる」と語った。
【関連リンク】
・ウイングアーク1stの製造業ソリューション
・ウイングアーク1st 導入事例 紹介ページ
・【特別対談】IoT時代に求められる“見なくてもいい”BIツールとは -ウイングアーク1st MotionBoard [PR]
・IVI(Industrial Valuechain Initiative)
無料メルマガ会員に登録しませんか?
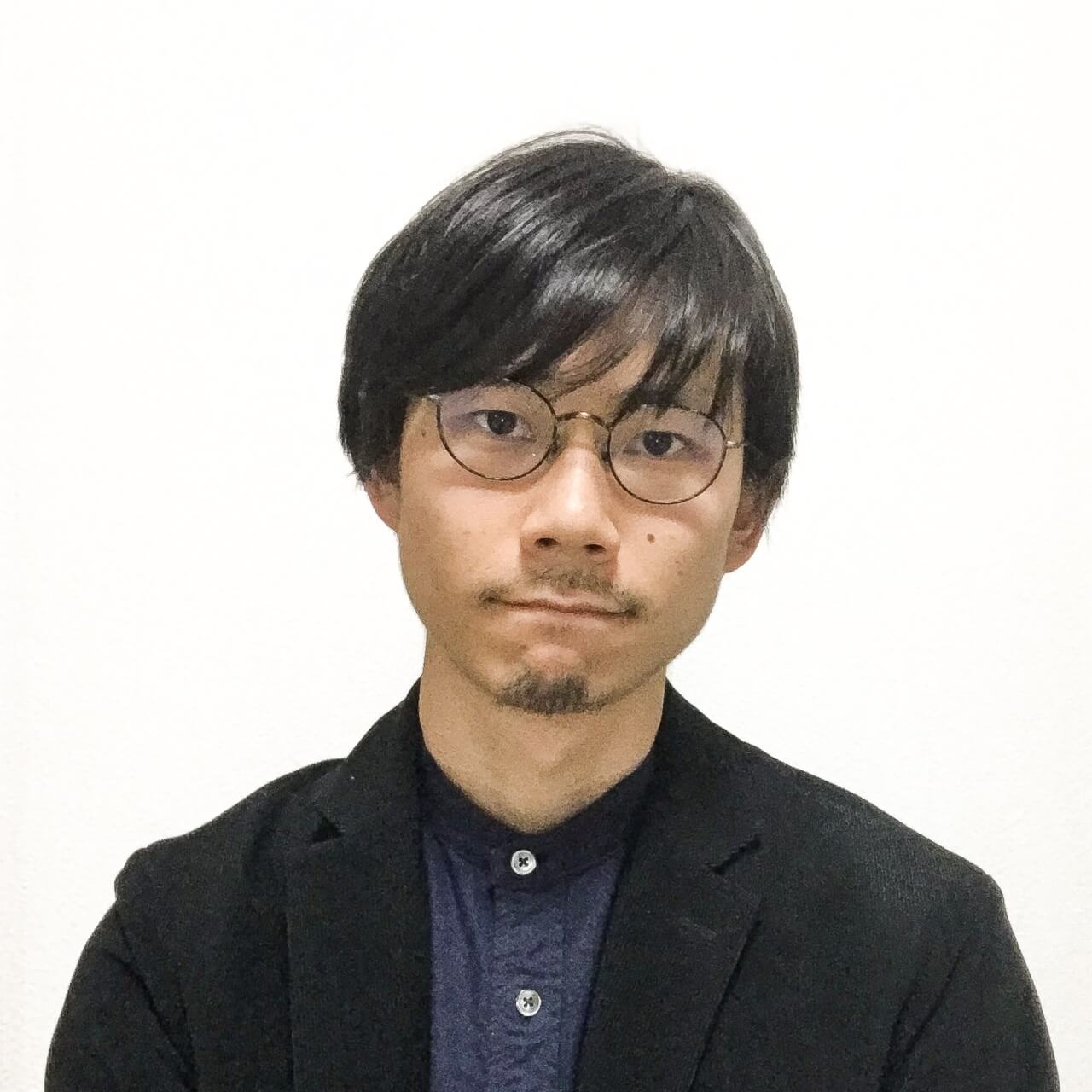
技術・科学系ライター。修士(応用化学)。石油メーカー勤務を経て、2017年よりライターとして活動。科学雑誌などにも寄稿している。