予知保全では、装置の稼働データや、振動、センサーなどの複数の時系列データカラムを分析し、特徴をとらえて判別モデルを生成する。今般、東京エレクトロン デバイス株式会社(以下、TED)は、予知保全を実現する異常判別プログラム自動生成マシン「CX-M」に、原因分析を可能にする「マルチカラム(データ合成なし)モデル生成機能」を追加し、「CX-M ver5.0」として提供を開始した。
CX-Mは時系列が記録されたcsvファイルを登録すると「データクレンジング」「特徴の抽出」「機械学習による判別モデル作成」「判別精度検証」を独自ソフトウェアで行い、異常判別プログラムを自動で生成する専用マシンである。
利用者はデータ分析や機械学習の知識がなくても、数値が記録されたcsvデータを準備するだけで自社基準の設備状態を判別するプログラムを生成できる。生成した異常判別プログラムはCX-Mから取り出して、製造現場や自社のシステムに組み込むなど任意の環境での利用が可能だ。
しかし、これまでのCX-Mでは、複数の時系列データカラムを合成してからデータ分析し判別モデルを生成していたため、判別モデルの判断基準、判別モデルによる判定理由の明確化(定量化、可視化)が困難だった。よって、発生事象の原因分析をすることができず、ユーザーの活用方法は判別モデルの判定結果を用いた予知保全に留まっていた。
CX-M ver5.0では、複数の時系列データカラムを合成せずに判別モデルを生成する「マルチカラム(データ合成なし)モデル生成機能」により、判別モデルの判断基準に各データカラムがどの程度影響するかを定量的に示すことが可能になり、判別モデルによる判定理由の可視化を実現した。ユーザーは判定根拠となったデータカラムをたどって発生事象の原因を分析することで、判別に影響を及ぼす要因に対して製造現場で具体的な対策を講じられるようになる。
具体的な表示方法は以下の通り。
- 判別モデルの判断基準を可視化
- 判別モデルで判定した理由を可視化
- 判定根拠から正常・異常オリジナルデータのグラフ比較
判別モデルの特徴(判断基準となるデータカラムと位置)を定量表示。
判定根拠となるデータ上の特徴(データカラム・位置・自信度)を定量表示。
発生事象の原因を具体的な情報から推定し現場での対策を検討。
関連記事:予知保全について詳しく知りたい方はこちらの記事も参考にしてください。
予知保全とは?IoT・AIの役割や導入プロセス、メリットや課題・事例を解説
無料メルマガ会員に登録しませんか?
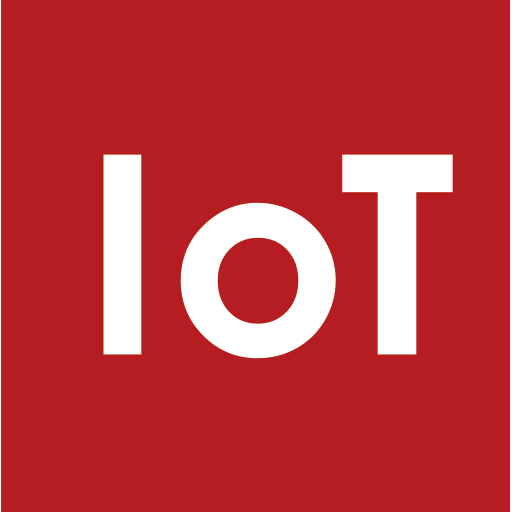
IoTに関する様々な情報を取材し、皆様にお届けいたします。