これまで、トラック運送事業者は、競争や荷主ニーズへの対応のために様々な対策を講じてきたが、それらが労働条件の悪化の要因のひとつになっているともいえる。
各運送事業者単体での対策では限界がきており、荷主との協力や連携が重要だ。例えば、荷主とトラック運送事業者の協力による商慣習の改善や、運送条件の見直し、荷主間の連携による共同配送などが挙げられる。
これを実現するためには、ITツールの活用や外部のコンサル発注などが考えられるが、まずは、ステークホルダー間での共通のKPIを定めなければ、どのようなツールを活用すればよいのかすらわからないだろう。
そこで本稿では、ステークホルダー間の協力や連携に焦点を当て、生産性向上の考え方や対策、成功事例が掲載されている「トラック運送における生産性向上方策に関する手引き」をもとに、生産性向上へ向けた取り組みの進め方やポイント、事例などを紹介する。
目次
トラック運送の生産性向上のための4つのKPI
国土交通省では、2016年4月に発表した「物流生産性革命」の中で、物流生産性向上につながる要因を、「付加価値額の増大」「投入労働時間数の削減」と定義している。
その上でこの手引きでは、トラック運送の生産性向上を考えるKPIを、「実働率」「実車率(時間あたり)」「実車率(距離あたり)」「積載率」の4つに整理している。
「実働率」はトラックの稼働時間を大きくすることで、「実車率(時間あたり)」は走行時間を長くすることで輸送量を増やすことができるというものだ。
「実車率(距離あたり)」は、トラックに荷物を積んでいる状態の「実車」と、そうでない「空車」に区別した上で、実車を増やすことだ。「積載率」は、この実車に積む荷物の量をなるべく多くすることで、生産性向上へとつなげる考え方だ。
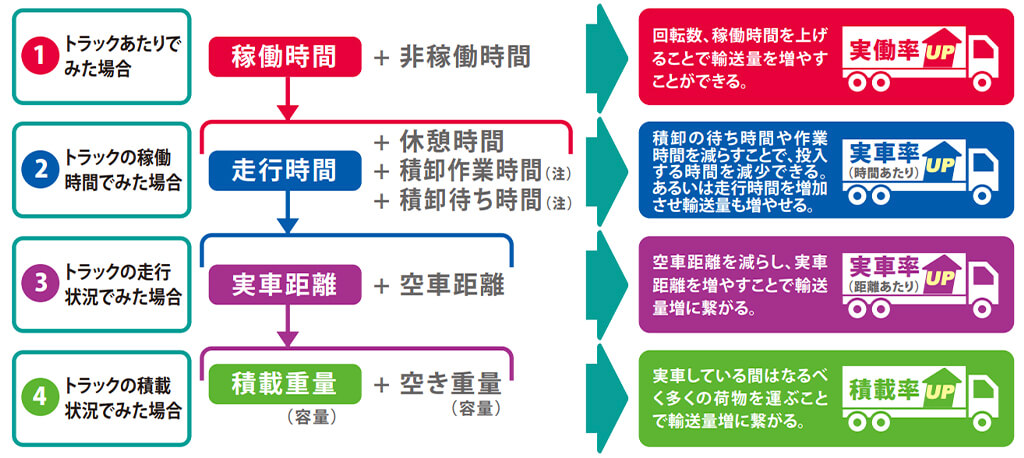
また、上記のトラックの稼働時間には、荷待ち時間が含まれていることも忘れてはいけない。
積み下ろし場所へ入場してから退場するまでの間に、作業時間や待機時間が含まれており、これを省人化したり削減したりすることでも、運送の生産性は向上する。
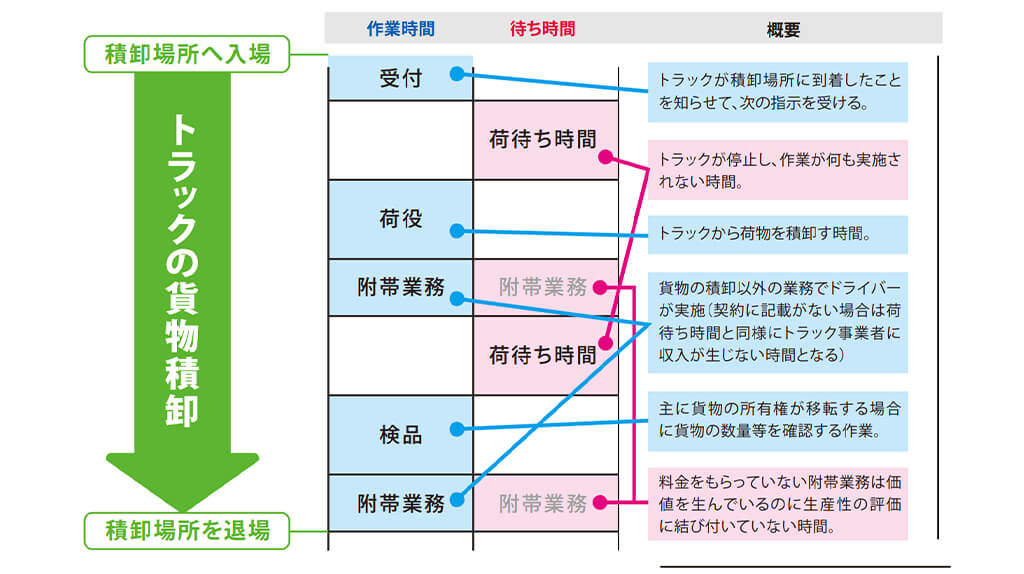
各KPI達成のためのポイント
次に、先に説明した4つのKPIを達成するためのポイントを紹介する。
実働率の向上
まずは、トラックの稼働時間を増やすために、トラックの非稼働時間が大きい輸送を把握する。
例えば宿泊が伴う運送では、大きな非稼働時間が生まれる。これは、一人のドライバーが長時間運送しているために起こってしまう問題だ。
そこで、一人のドライバーにつき250km〜300km程度の日帰りできる距離のみの輸送とし、その先はまた新たなドライバーが輸送を担うという中継輸送を実現することがひとつの解決作となる。
中間輸送を実現するためには、中間拠点の具体的な場所を決め、ドライバーや運送事業者間、荷主の理解を得た上で実施、到着時間のズレなどの課題を抽出して都度調整を行う必要がある。
なお、中継輸送には、1つのトラック運送事業者の複数のドライバ-が実施する形式と、異なるトラック運送事業者間で実施する形式があり、いずれも事前に協定書をパートナーで締結するなど、それぞれ所定の手続を行うことで実施可能となる。
実車率(時間あたり)の向上
走行時間が短くなっている原因のひとつには、積み下ろしや検品といった走行以外の業務をドライバーが行っていることが挙げられる。
そこで、物流拠点や店舗において、仕分けの徹底や機械化、パレットを活用した積み下ろしの効率化を図ることで、結果的にドライバーは空いた時間を運送業務に回すことができる。
また、走行以外の業務を着荷主側が担当するといった方法も、実車率を向上させるのに有効だ。
これを実現するためにも、現状の実態や効率化した際の効果を定量的に関係者に示し、協力を得る必要がある。
実車率(距離あたり)の向上
実車率が低い状態というのは、行きと帰りのどちらかにおいて、荷物が積まれていない運送を指す。
一つの企業では往復させる荷物がない場合は、複数の企業が恒常的に荷物をマッチングさせる方法がある。
実施にあたっては、パートナー企業を探索し、各社の運送量や車両サイズ、配送時間といった運送条件を企業間で調整する必要がある。
実現できれば、実車率の向上だけでなく、燃料費や人件費削減などにも寄与するといったメリットもある。
積載率の向上
積載率の向上のためには、まず自社の積載率の低い路線を把握し、その路線と類似の輸送経路や運送条件となっているケースを探索する。
そして、複数の荷主による共同配送や、物流拠点の共同化を模索し、パートナー候補企業が見つかったら、運送条件の設定を行う。具体的には、積み下ろしの方法や利用車両、コスト負担や既存トラック事業者の取り扱いなどを検討する。
これをもとに、小規模なトライアルを実施し、課題の把握や改善を図る。軌道にのれば、情報システムの統合など、共同化をサポートする仕組みを構築していく。
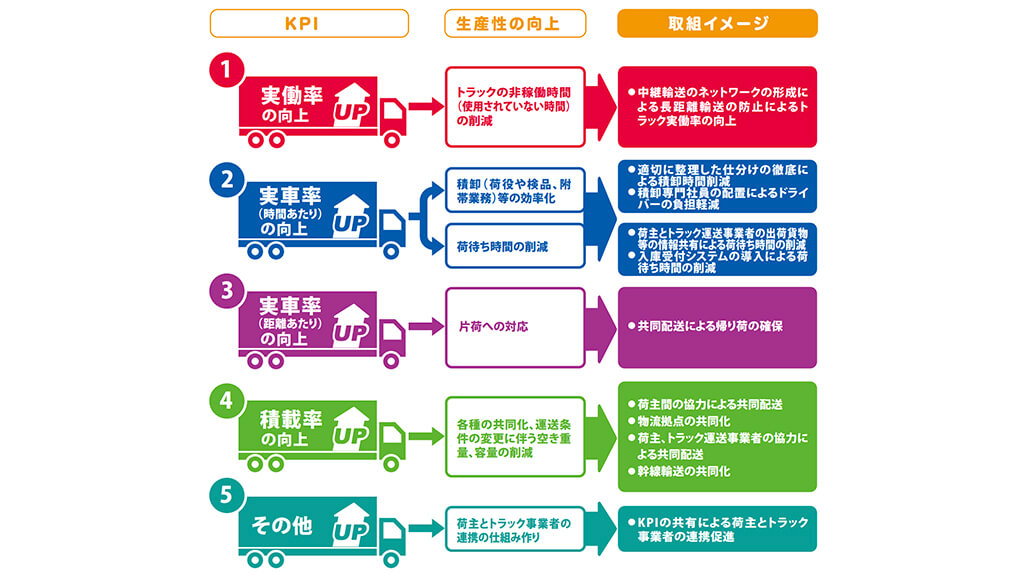
なお、この図では、4つのKPIに加えて、荷主とトラック運送事業者の連携の仕組み作りも記載されている。
4つのKPIをもとに、荷主とトラック運送事業者間での共通KPIを設定し、これをモニタリングすることで現状の共有やPDCAの実施を行うというものだ。
現在、経済産業省は、荷主事業者や物流事業者に対し、物流施設の自動化や機械化に対する機器やシステムの導入などにかかる費用を補助する実証事業を公募している。
この実証事業では、荷主とトラック運送事業者が連携したコンソーシアム形式での申請も可能なため、複数社が連携するために活用するのは良策だろう。
実証事業の概要については、経済産業省のHPおよび以下の記事を参照してほしい。
各KPIの成功事例
最後に、各KPIを設定し、成功した事例を紹介する。
事例①:地場の運送事業者と連携し、中継輸送を実現
この事例では、運送事業者が、千葉にあるメーカから東北の着荷主へと運ぶ輸送において、中継輸送を実現し、実働率を向上させている。
これまでは、複数ある東北の着荷主に対し、発荷主最寄りの陸運拠点から、複数の納品車両が直送で長距離輸送を行なっていた。
この場合、長距離ドライバーが複数必要になるほか、一台あたりの積載量も少なく、採算の合わない路線が多かった。
そこで、東北内にドライバーの乗り換えや貨物の一時保管ができるストックポイントを設け、自社ドライバーが発荷主最寄りの陸運拠点から日帰りで往復できるようにした。
そして、ストックポイントからの運送は地場の運送事業者に委託し、東北エリアの着荷主に対して納品時間を調整した。
さらに、業界の貨物に慣れたドライバーを配置するとともに、誤出荷を防止する自社の情報システムを導入することで品質も高めた。
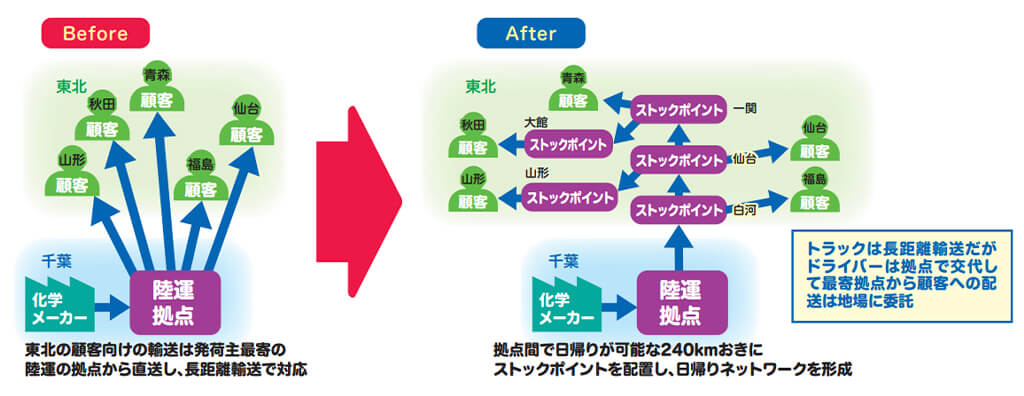
これにより、荷主は顧客へのサービスレベルを向上させることができ、物流コストも抑えることができた。
東北の着荷主にとっては、ストックポイントの在庫品についてリードタイムが減少し、対象メーカが拡大することで納品車両が減少した。
運送事業者は、長距離ドライバーを確保する必要がなくなったため雇用がしやすくなったほか、複数の着荷主の貨物を集約できることから積載率も向上させることができた。
こうした取り組みを進めるポイントとしては、大口荷主に提案を行い巻き込みながら、納品先の他の貨物も日帰りネットワークに組み込む営業を行うことが重要だとしている。
事例②:Web予約システムを活用し荷待ち時間を削減
この事例では、物流事業者の自社の医薬系物流倉庫において、卸売センターで発生している納品時の待機時間を削減し、時間あたりの実車率を向上させている。
これまでは、入庫が先着順であったため、ドライバーが到着してから荷下ろしを開始するまで待機時間が発生しており、10時間近く待機することもあったのだという。
そこで、配車機能、トラックの動態管理機能、ドライバーのナビゲーション機能の3点をシステム化したWeb予約システムを導入した。
これによりドライバーは、入庫作業量に合わせて入庫したい時間を着日の前日に予約することで、早めに来て順番待ちをする必要がなくなった。
また、これまで紙ベースで行われていた入庫時検品を廃止し、納品伝票と受領印の電子化の仕組みに写真付き電子受領書を付与した「e-伝票」を導入。出庫側で商品の情報を入力することで、入庫側へ事前に商品情報を送る仕組みにした。
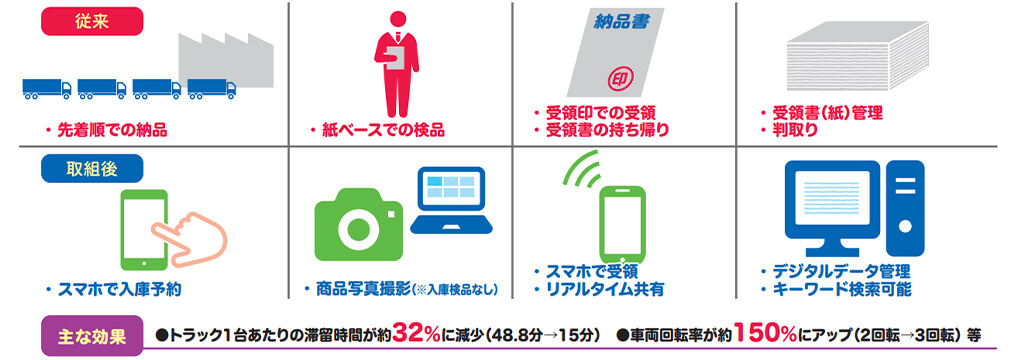
その結果、トラック一台あたりの平均滞留時間が48.8分から役15分に低減することができたほか、検品にかかる工数を省略することができ、荷下ろし時間削減および荷受け作業人数を削減できた。
配送パートナーは、納品の車両回転数が2回転から3回転に向上し、車両台数を削減することができた。
物流事業者は、紙媒体による送付や受領、管理の負担が低減され、車両回転率と実車率を向上することができた。
こうした取り組みを進めるポイントとしては、システム化した仕組みに互換性をもたせることで、他の3PL企業やメーカとの技術共有を進めることが挙げられている。
事例③:空車を有効活用しCO₂排出量を削減
3つ目は、電機メーカと新聞社が協業し、低公害車を活用した異業種間の共同配送を行うことで、距離あたりの実車率を向上させた事例だ。
両社が共同配送に至ったきっかけは、低公害車の活用だ。電機メーカが改正省エネ法に対応するために、バイオ燃料を使ったトラックの利用を首都圏で展開しようとしていたところ、新聞社も同燃料を大口で購入していたことがわかり、情報交換を開始したところからはじまった。
その後、新聞社の車両を用いて、朝刊帰り便によるパレット荷物と通い箱荷物の共同配送を開始した。
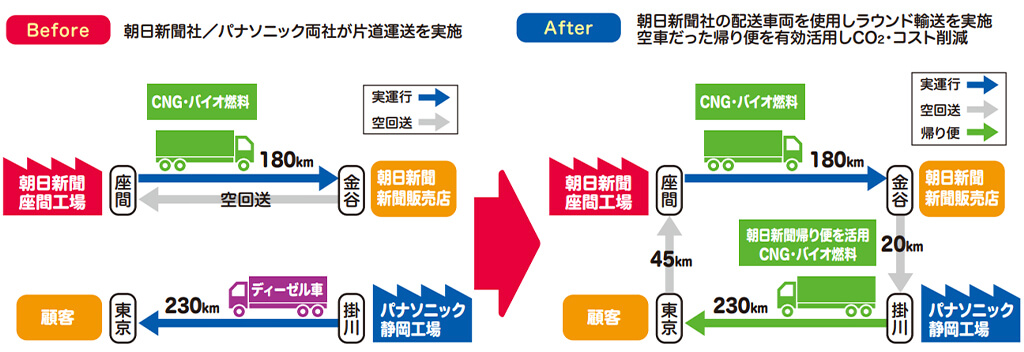
運行時間が合わない場合は、トラックを2台用意し、1台は先行して電気メーカの拠点で前日中に荷積みをしておき、ドライバーが新聞社の販売店に配送後、電機メーカの拠点に移動。そして、すでに荷積みが終了しているトラックに乗り換えていくことで対応した。
加えて両社は、さらなる共同配送の実現を目指し、新聞社の配送エリアマップや、共同配送にいたる検討フローが入ったマニュアルなどを作成することで、電機メーカ社内における全社会議や研究などの機会を通じて周知し、新たな共同配送を実施した。
このマップとマニュアルを電機メーカに広く配布することで、多くの品目へと拡大することができたのだ。
その結果、CO₂排出量を年間67トン削減でき、コストを23%削減することができた。
こうした共同配送を進めるためのポイントとしては、各社の利害を把握して協力を得ることや、荷扱いや運用などに関して連続試行期間を用意したり、荷扱いの研修を実施したりすることや、小ロットで特積みや宅配便を使っている貨物を共同配送の対象とすることなどが挙げられている。
事例④:メーカ11社の共同配送を実現し積載率を向上
最後の積載率向上に関する事例は、物流事業者が、3PL(サード・パーティー・ロジスティクス)の支援を得て、メーカ11社の共同配送を実現したケースだ。
これまで、九州地区の家電物流では、各メーカが個別に物流センタへの配送を行っていたが、積載率の向上が課題となっていた。
一方、福岡市にて物流施設を集積させる構想が検討されているタイミングであり、これが、共同配送の取り組みが検討されるきっかけとなった。
そして、メーカ11社が参加し、3PLの共同倉庫を利用する形式の共同配送を実施した。従来は各社が個別に自社の物流センタから家電量販店の物流センタに配送していたものを、物流事業者が運営する家電物流プラットフォームに集約し、そこから共同配送する取り組みだ。
配送条件に関しては、個社ごとの事業に合わせて必要に応じて商品を集荷するなどのを工夫した。また、配送に関する情報システムも統合するため、各社のデータを読み込めるようなデータ変換ツールを作成した。
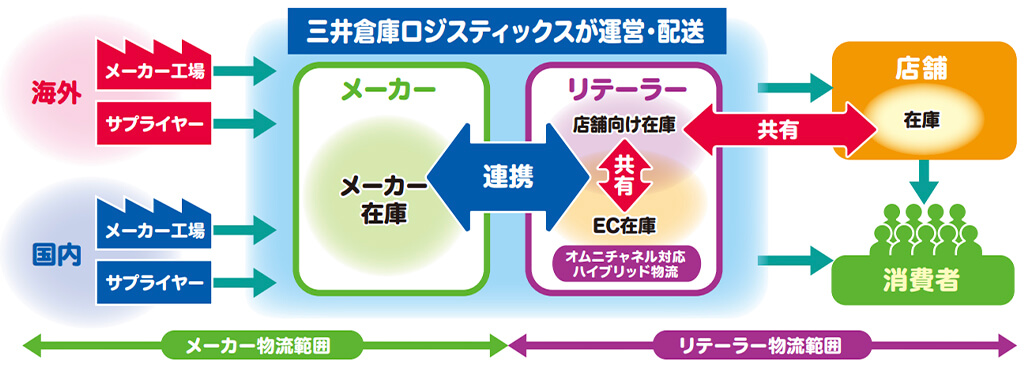
これにより、積載率が50%から80%に向上。トータルで利用する台車が減少し、CO₂排出量も4割削減することができた。
こうした取り組みを進めるポイントとしては、荷主企業の課題やニーズを把握する場を設定し、共同配送のメリットを定量的に伝えるといったことや、各社が求める集配条件を考慮する必要がある。場合によっては、自社による集荷や他社の物流会社も含めた体制構築といった対応が必要だ。
複数社が連携するためのKPIの重要性
このように、きっかけや連携体制、実施した対策やKPIはそれぞれ異なるが、KPIへ向けてステークホルダーが協力し合う必要性がわかる。
先に紹介した経済産業省の実証事業やITツールを活用することも重要だが、どのようなKPIへ向け、どのようなツールを導入して対策していくかを考える際に、是非参考にしてほしい。
運送事業者が発着荷主と交渉をし、KPIを設定して実現していくことは簡単ではないが、サプライチェーン全体の生産性向上は必須であることを関係者全員が理解し、全体最適を目指す取り組みが重要となる。
無料メルマガ会員に登録しませんか?
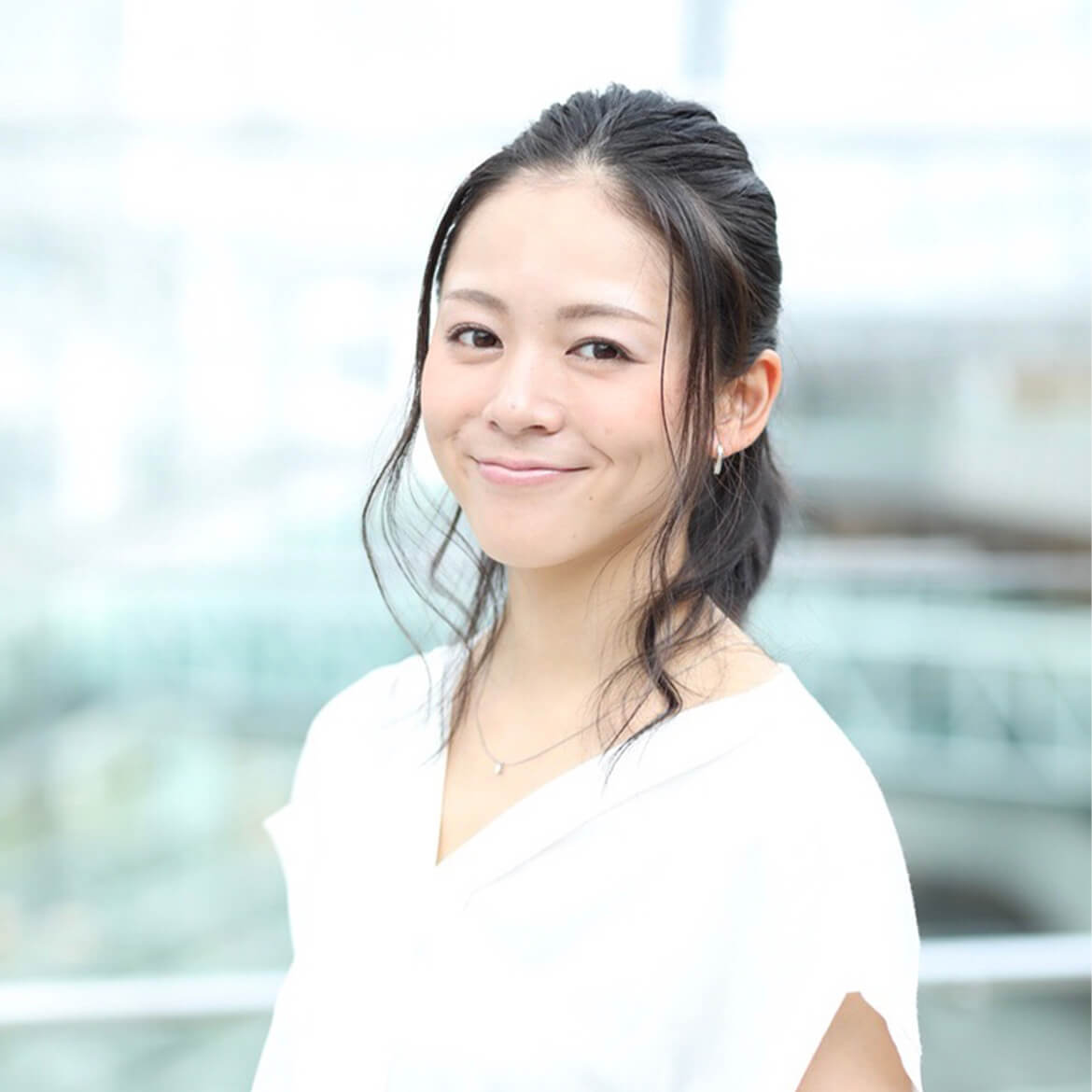
現在、デジタルをビジネスに取り込むことで生まれる価値について研究中。IoTに関する様々な情報を取材し、皆様にお届けいたします。