ビールやRTD(※)などの製造の効率化を図るには、製造現場の担当者が設備の運転状況を理解し、適切な管理を行うことが求められる。そのため、設備の定期的な点検に加え、トラブル発生時には、製造現場の担当者が原因を追究して対応するほか、設備に詳しい設備メーカーの担当者が工場を訪れ、細かい調整を行っている。
設備点検の負荷低減および設備不調による製造ラインの休止時間の短縮は、効率的な製造を行う上で製造現場・設備メーカー双方の課題となっている。
キリンビール株式会社と株式会社前川製作所は、連携してビッグデータ活用による設備管理とIoTを活用した冷凍機の遠隔監視を実施することを発表した。
今回、ビールやRTDの原材料を保管する冷凍機にセンサーを取り付けることで運転状況のデータが蓄積され、ビッグデータを活用することで消耗品の劣化・設備異常の兆候管理が可能となった。
また、冷凍機の周囲にネットワークカメラを配置して遠隔監視を実施し、IoT技術を活用することで、製造現場であるキリンビール工場内のみならず、設備メーカーである前川製作所とも冷凍機の運転状況を迅速に共有できるネットワークシステムを構築でき、設備の異常検知時には迅速な初動対応が可能となる。また、電子帳票の導入による自動帳票作成や分析の自動化が可能だという。
これらにより、工場設備の突発的な故障の防止と稼働効率化、省エネルギー化が見込めるとしている。また、定期点検や現場でのトラブルシューティングといった作業時間の省略化が進むことで、工場現場では約120時間/年の点検時間を削減するなど、両社の業務負荷軽減につながるとのこと。
今回、キリンビール福岡工場において2020年1月より約1年に及ぶテスト展開を実施した結果、冷凍機の稼働効率化・設備点検負荷の軽減が認められ、2021年5月より同運用を開始した。また、前川製作所では同技術を用いたシステムを2021年7月より「スマートチラー」として商品化し、同年9月からはキリンビール仙台工場での展開を予定している。
※ RTD:Ready to Drinkの略。栓を開けてそのまま飲める低アルコール飲料。
無料メルマガ会員に登録しませんか?
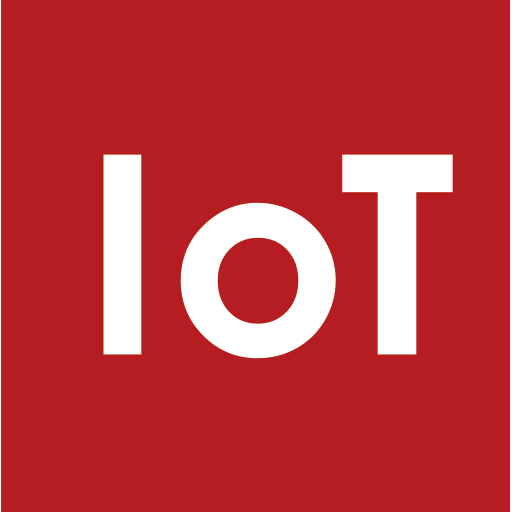
IoTに関する様々な情報を取材し、皆様にお届けいたします。