2017年7月7日(金)、大崎ブライトコアホールにて、IoTNEWSが主催するカンファレンス「IoTConference2017 スマートファクトリーの今と未来」を開催された。
レポートの最終回は、午後最後に行われたパネルディスカッション「スマートファクトリーをいかに導入し、結果をだすのか」のレポートを行う。
登壇者:
株式会社ウフル 専務執行役員 IoTイノベーションセンター所長 兼 エクゼクティブコンサルタント 八子 知礼 氏 ベッコフオートメーション株式会社 代表取締役社長 川野 俊充 氏 東洋ビジネスエンジニアリング株式会社 新商品開発本部 マーケティング企画本部 本部長 入交 俊行 氏 オプテックス株式会社 戦略本部開発センター センター長 中村 明彦 氏
モデレータ:
IoTNEWS代表 小泉 耕二
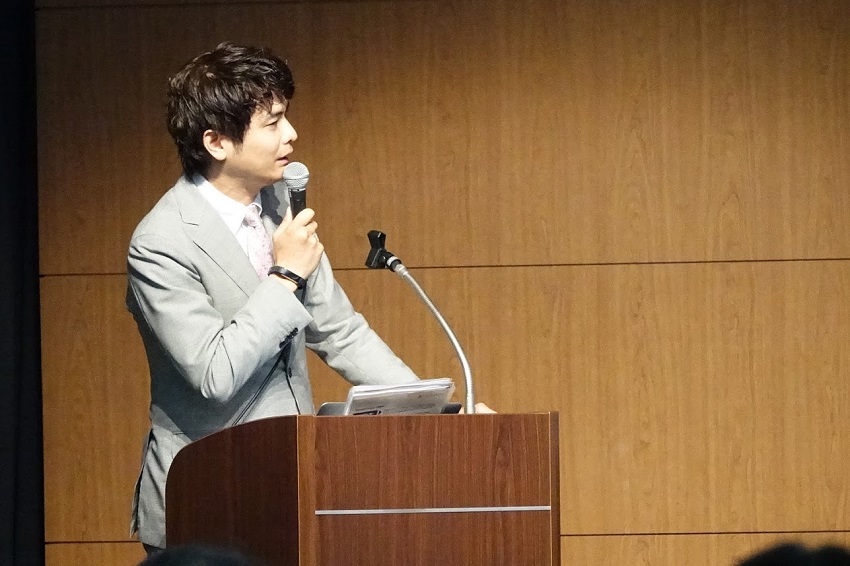
IoTNEWS 代表 小泉 耕二
小泉:
会場の皆さんの中でのスマートファクトリー感が統一されていないと思うので、まずは概念のようなことから話していきたいと思います。
まず、スマートファクトリーの難しさは、製造業には大小の様々な会社があり、また製造している製品がそれぞれ異なるところにあるかと思います。その為、一口に「スマートファクトリー」と言っても、一概に述べることはできないと思います。そもそも、スマートファクトリーの話が出てくるようになったのは、インダストリー4.0の話が出てくるようになったからだと思っております。
インダストリー4.0の本質は、マスカスタマイゼーションという人もいれば、オートメーションの更に先のものとして話す人もいます。
まずは、登壇者の方が、スマートファクトリーについて、どのような見方をされているのか、お話頂いてもよいでしょうか。
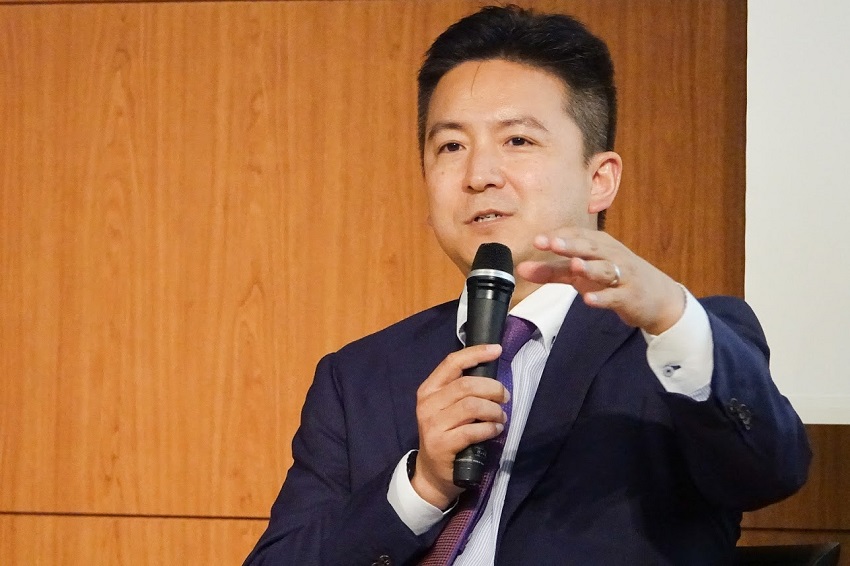
八子氏:
一言で述べると、スマートファクトリーは「人が介在しなくてもよくなるようなもの」だと思います。
その分、人はどこにいくのかというと、工場の工程に中にはいないが、スムーズな機器の動きであったり、需給の調整であったり、マスカスタマイゼーションに関連するところにいくんだと思います。
つまりお客様のニーズを流し込むところと(Input)と出力されるところ(output)のI/Oの部分にいることになり、その間の部分はブラックボックスとなっているのが、スマートファクトリーだと思っております。
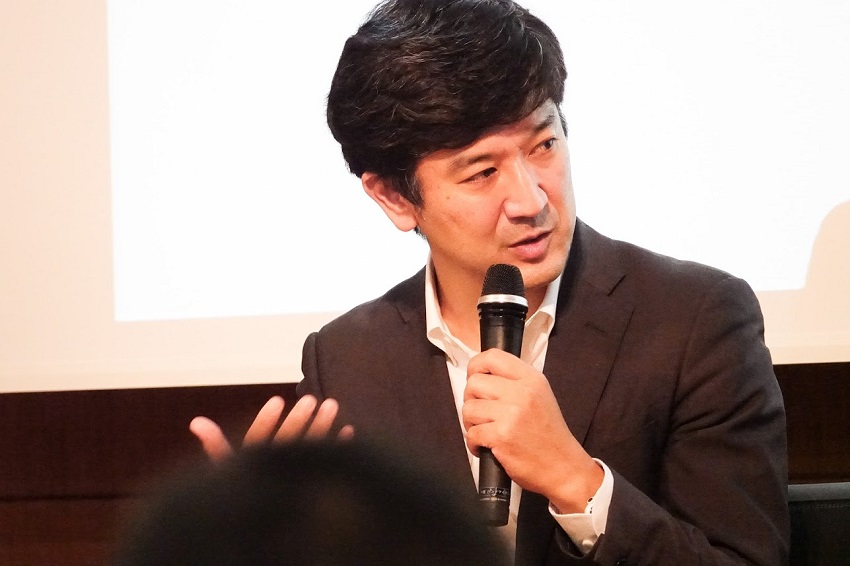
ベッコフオートメーション株式会社 代表取締役社長 川野 俊充 氏
川野氏:
情報を与えたら何でも必要なものが出てくるという、サイバー的な夢世界なものがスマートファクトリーだと思います。
かつても、そろばんが電卓になって、電卓がエクセルになってそしてAIに代わっていくように、オフィスワークでは新しいツールを使用するように自然となってきていますよね。
一方で、製造業はメカの話になる為、オフィスワークのように新しいデジタルツールを次々に使用するには、至っていないです。
一方で、スマートファクトリーの考え方としては、新しいツールを使用することで生産性を高めたりする余地があることかと思います。効率的にそのツールを選び、使用していくことが、スマートファクトリーの次のステップとしてやるべきことだと思いますね。
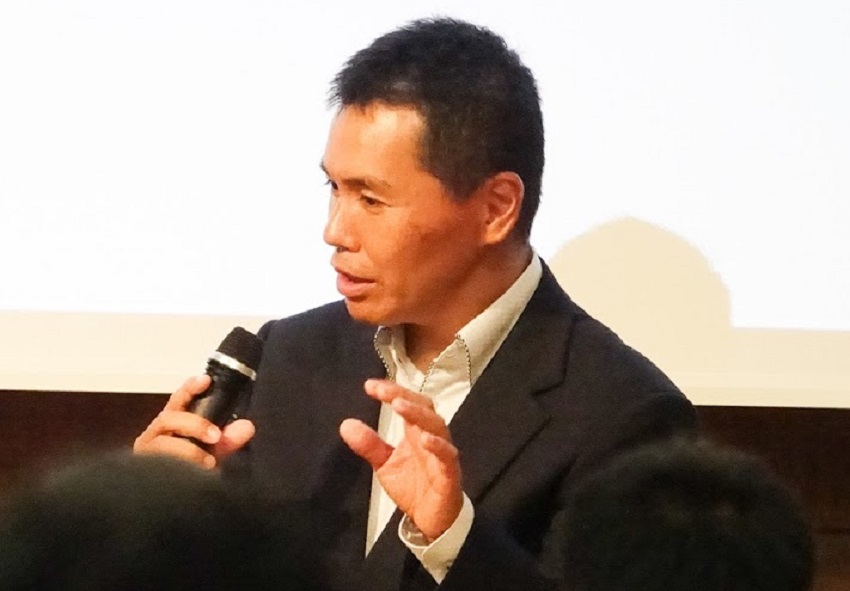
東洋ビジネスエンジニアリング株式会社 新商品開発本部 マーケティング企画本部 本部長 入交 俊行 氏
入交氏:
簡単に・早く・安くできるといことがスマートファクトリーではないかと思います。
生産管理の立場から述べると、現場では、デジタルが嫌い(デジタルがなくても仕事ができる、デジタルにインプットすることが嫌いだ)という感情があと思います。
そういう現状があるが、簡単で分かりやすいデータとして伝えると現場でもその有用性に気付いてくれます。また、「見える化」という言葉が現場では嫌いな部分もあるので、「見たい化」に言葉を改めると、現場・顧客の立場からするとその有用性に気づきやすいですね。
これらを踏まえ、現状のスマートファクトリーでは複雑なデータの取り扱いは難しいと思うので、我々はまずは簡単なデータから取り扱いを提供をしています。このようなデジタルドーピングで今までやっていたことをより楽にできるのがスマートファクトリーの本質ではないかと思います。
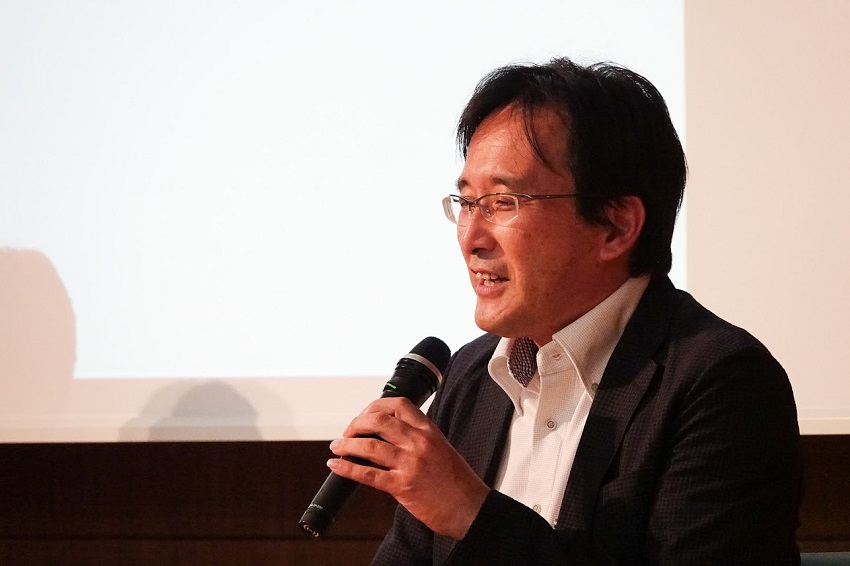
オプテックス株式会社 戦略本部開発センター センター長 中村 明彦 氏
中村氏:
製造業の立場から言うと、「とにかくクレームのない工場であること」がスマートファクトリーの本質であると感じています。様々な製品の製造に対して、工程・人の管理など不具合を起こす可能性がある部分は多いですが、スマートファクトリーを通すことで、それらの不具合が解消できることが重要なポイントであると思います。
小泉:
ありがとうございました。それぞれレイヤーの違うお話を聞けて面白いですね。
特に日本の品質は、中国の品質と比べた際により優良との声を聞くことも多いですので、生産管理技術が優れているのであれば、そもそもその品質に問題は中々起きないと思います。もっと言うとスマートファクトリーは必要ないのではないと思いますが、どのように考えますか。
入交氏:
日本の場合は、過剰品質であると思います。本当に、そのスペックが必要だとは思えないケースがたくさんあります。例えば、コンマ1ミリ差でも品質にそれほど変化は起きないし、それでいてコストが下がるようなことを考える日本の製造業は少ないように思います。
中国と品質を比べた場合、日本の製造は精巧に製品を作ることが多いですが、中国はそうではありません。
しかし、デジタルの力を使った場合、作った後のフィードバックであったり見直す作業が入るので、品質の違いは生まれなくなると思います。ゆえに、クオリティに対するクレームも発生しなくなると思うのです。
小泉:
ということは、クレームがくるということは、まだ改善の余地があるということになりますか。
中村氏:
社内で、こんな面白い話がありました。
生産管理からすると、日本はやはり品質にこだわりすぎている為に、発注が来てから企画して製造するまでのリードタイムのスピード感が中国に完全に負けているという話です。クレームに関わらず、最近ではモノが生産されるまでの時間は明らかに早くなっています。その為、ものを早く生産する為にはどのように対応することが重要か考える必要があります。特に、注文が来てから製造までのリードタイムや製造そのもののリードタイムをもっと縮める必要があります。
例えば、自動車やスマホ以外の産業では、リードタイムが長くなってきています。それをどのようにしたら改善できるかを検討することが必要ですね。
川野氏:
その意味では、駿河精機の例がよい事例となっています。すべての製品を3日以内に製造するというミスミの流れを踏襲した社内ルールが脚光を浴びています。
ドイツの企業に、駿河精機の事例を紹介した時は特に脚光を浴びました。現状では、3日かかる製造時間を1日する、又は注文をもらう前から作り始めるなど、時短を意識したものづくりを検討していく必要があると感じています。しかしながらこれは例外的な事例です。
現状では、品質と国柄との関連性が色濃く表れています。日本の評価は品質面では平均点以上の評価であるが、ドイツでも市場に出荷されているものは日本同様の品質です。しかし、ドイツでは発生してしまった不良品を市場に出さないような取り組み(自動化のテストや各種検査)をしています。生産効率を考えると日本の製造の方が効率は高いのだけれど、幸福度・コスト面を考えるとドイツは定時には帰宅するように豊かな生活ができている、また自動化によるコストの低減ができているのです。
一方で中国の話をすると、新しく工場を設立するときには最新鋭の機械が並び、すべてデジタル化されているかたちとなります。その結果、生産管理などの部分でも情報の共有が大画面を通して組織一体ででき、言うならばゲームをしているような感覚で各個人が作業にあたることができます。品質の部分でも管理が正確に実施されるため、日本同様のクオリティを担保し、且つコストを1/10に抑えるような製造ができているのです。
小泉:
ということは、これから新工場を設立するところは、圧倒的な生産力もって現れているということですね。
ところで、現代の日本の企業は、国内だけの市場を見て活動するのではなく、グローバルな生産活動で世界と競合していくことが必要になっているかと思います。海外製の製品を購買することが多くなっている点がよい例ですが、製造の「現場」という意味で考えると、市場の近くで生産する、又は海外で纏めて製造という観点を持った形態で製造業を行っています。
ある意味、日本の製造業は系列に縛られて活動しているが、グローバル社会で生き残っていく為に日本企業には今後どのようなことが求められるでしょうか。
八子氏:
「スピード」に対する危機感をもつことが世界と競っていく為には必要不可欠であると思います。
昔の話からすると、FAを真っ先に仕掛けたのは日本であり、世界の中である程度まで勝っていたのは事実です。しかしながら半導体・PC・モバイル・液晶などある程度の規模で製造をする分野においては日本企業では、マネージメントが上手く出来なくなり、世界の競合と争えなくなったのです。
プロダクトのライフサイクルが早くなっているのにも関わらず、市場のニーズを汲み取り、効率よく製造作業(企画・調達・製造の工程) を進めるという点で海外に遅れをとっているのです。いわば、スピードの面では負け癖がついているのではないかと思います。
中国が1日でモノを製造するのならば、日本は半日で作れるようなビジネスモデル・オペレーションモデルの構築をするというスピード感をもったチャレンジが日本の企業には必要なのではないかと個人的には強く思いますね。
小泉:
なるほど、ゲームに例えるとゲームがあるのにその場面にうまく乗っかれていない日本の現状があるのですね。
現状の製造は、メカ・エレキ・ソフトなどで構成されていますが、それぞれがバラばらに作成されて、最後に組み合わせるような工程になっていると感じますが、最初から各製品を一緒に企画製造していくような業態にすることはできないのでしょうか。
川野氏:
確かにメカ・エレキ・ソフトの順で製造していくと、ソフトの製造を開始するときには、タイムオバーになっているという話はよくあります。
しかし、最近の大手企業では、企画の段階から各製造が一緒に検討するような構造になっています。各国の製造現場なども含めて、「デジタル大部屋」を準備し、全体像の共有するようなでアプローチをしています。しかしながら、上記のような設備投資ができない(余力が十分にない)中小企業では、大企業のような工程が組むことができないのが現状です。その対策としてはメカ・エレキ・ソフトの全てを出来る人を育てることが必要なのではないかと思います。
小泉:
製造の素人として思うのは、「汎用化する」ことで改善できるのではないかと思うのですが、つまり、製品として使われやすいものの製造、その中で差別化をしていくことはできないのでしょうか。
川野氏:
これまでは、それぞれの部署がコストを下げたり最新の開発環境を作る為に独立して企画などの検討をしてきました。
しかし、これからは、オープンな開発環境で共有しながら進めていくことが大切だと思います(汎用化)。このように対応していくと差別化は難しいけれど、各部署で補完し合いながら進めていくことができます(スピード化の実現)。
つまり、ものづくりで重要なのは規格ではなく、設計の中身にあります。設計の中身(コンセプト)を各部署で共有し合いながら一気通貫のインターフェースを作ること、アイディアや構想がモノにまですぐに落とし込めるように標準品・汎用品を使うことが重要だと思います。
八子氏:
標準品でないと、調達が難しかったりリードタイムがかかってしまったり、自分たちに取り込むまでに時間がかかってしまうので標準品の方がよいですね。
中村氏:
子会社のCCS(LEDのニッチ市場で大きな利益を目指す企業)の事例があります。
大量生産とは一線を引いたコアの技術を活かしたビジネスの展開をすることも一つの解であると思います。大企業とは違ったと中小企業型のビジネス(少量多品種)のビジネスモデルもあります。
八子氏:
マス向けのビジネスとは違い、他のリソースを上手く活用するような中小企業型のビジネスもあります。
中国製の360°カメラの話をすると、CCDカメラはソニーから購入、CPUも載ってないし、iPhoneに繋げると演算を開始するようなカメラです。
光学系のカメラ機能でいうと日本製の品質よりは劣りますが、撮った画像をソフトウェアで補正してスティッチング・ウェブにアップする流れで使用できます。開発が早く、安い、またアプリのアップデートに合わせて性能が向上していくので、他のリソースをうまく利用してビジネスをする考え方も現状は使用されています。
小泉:
なるほど。話は変わりますが、100個しか作らない工場(少量多品種の製造企業)は空いている時間をどのように使っているのですか。
中村氏:
そこは弊社では課題となっているのですが、ヒューマンリソースをどのように保つのか検討をしている段階です。
本来、職人技術をデジタル化することを研究するよりは、新製品の開発検討する方向へ進んでいくので、今の段階では、ヒューマンリソースを活かす為に、日々会議を繰り返すことで、職人技術を使う又は一部を自動化したりなどと検討しながら作業しています。派遣を雇うにしても、技術をレクチャーするところから始まるので、悩ましく思っています。
小泉:
B-EN-Gの製品は、その職人技術をデジタル化するソリューションを検討していたと思うのですが、現状ではどのような段階ですか。
入交氏:
あまり進んでいないのが現状で、ちょっとしたコツなどをトランスすることができる段階にあります。
事例でいうと、F1のエンジンを作るメーカの話になります。コンマミクロンの精度を必要とする為、職人の技術以外、精度を達成することは困難だったのですが、マシニングセンターのプロをドイツより招いて3ヶ月の期間をかけてやっと同様の精度を達成することができました。
どの企業も職人技術をデジタル化することは高額な費用と時間をかけるならば達成できると思いますが、一般の企業が本事例と同様に費用をかけて職人技術を自動化する検討をすることは難しいと思います(このメーカの場合はF1のエンジンの製造なのでたまたまペイできたが)。
実用的に考えるならば、差別化の一因である職人技術をもとに、ITドーピング(ノウハウ・技術を教え込ませる)することで、作業を0から学ぶことなくスタート地点をもっと高次元の段階からスタートさせることが必要だと思います。技術習得に10年とかをかけることなく、短縮することができますしね。
中村氏:
マシニング企業のヒルトップ社の事例でも、職人技術をデジタル化へ移行する際には10年かかったというものもあります。
しかしその結果、普通ならば3ヶ月かかる製品を2日で製造することができるようになったといいます。
ゆえに現在では自動車系の精度を要する部品の生産については大部分の受注を占めていると言います。
技術のデジタル化は共有マシンを各国に配置するだけですべてをDB上で共有するシステムを組んでいます。具体的には、設計(ノウハウ)は全て京都で担当し、それをDB化する、またその稼動ソフトもすべて自前で開発設計するというものです。コスト・時間ともに大きく負担がかかることを通して、デジタル化を達成した事例になります。
しかし、このようなシステム自体の開発検討をどの企業もできるかというと、答えはNoになります。
八子氏:
新しい工場や製品を作るようなタイミングであれば、デジタルに移行することは可能であると思います。
北九州のあるメーカーと話しさせていただいていたところ、スモールスタートの話(まずはできることから可視化すること)を提案していた際に、デジタル化をするならば、「ラインを完全全自動にする!」みたいなインパクトが必要だ、つまり投資をするタイミングですべてを変更することを考えているといわれたこともあります。
小泉:
進むべき方向性はあるが、やることは難しいとのことだと思います。このカンファレンスの趣旨は、明日から変えられる部分は変えていこうという趣旨なので、それについてはどう考えていますか。
川野氏:
経営者の「やるぞ」という意気込みが強ければ一番いいですが、興味すら持ってもらえないことも多いです。
その場合の対策として、現場の方の行動(隠れて実行する)が大事になってくると思います。今までどおりのプロセスは承認を取るまで時間がかかるし、承認されなければそれが無駄になってしまうことが多いです。
ゆえに、仕組みの中ではできないけれど、密かに社内の中でエネルギーのある方を募って、またベンダーも巻き込んでPoCを行うことです。そして、その結果を持って成果と本採用時までの過程を報告をすることで、社内的な承認をとるところまで進んでいくことが大事だと思いますね。
八子氏:
前職のシスコの時代から長く提案していた会社の常務に、密かに進めていたPoCの結果を報告したことがあります。
その会社では、3年以内にスマートファクトリーをするという中期計画があった為、提案をしましたが、一度はリジェクトされました。
その後、現場の人たちと結託し、ITメーカーとセンサメーカなど4社ほどで試験環境を作り始めました。少ない予算で、工場の小さなラインのところにセンサを設置し、上がってくるデータを横抜きしてPoCを作り上げました。その後、再度常務に報告したところ(前回の報告より8ヶ月が経過していたが)、意外な返答が返って来たのです。「これは良いものができている、去年のデータと比較したらどうなるの?」「常務、去年のデータはとっていません」「だから前回進めるように言っただろう」といったやりとりがありました。
前回の段階で承認してもらっていたら、このような皮肉を言われることもなかったと内心感じていましたが、つまり前もってデータをとっていないと新たに見える環境も構築できないので、やはりスモールスタートにはなっていくと思います。
また、全く別のケースでは、食品メーカへ新しい製品を作る場面でアプローチを実施したこともあります。
365日味の違う製品を販売することを念頭に製品を作ろうと提案するものです。その結果、「今のラインからでは絶対に作れない」と予想通りの返答が返ってきましたが、返す言葉でそれならばこの製品が作れるラインを作りませんかとの提案になりました。
何が言いたいかというと、これまでと全く違ったものを作成する際には、全く違った切り口や進め方が必要となることです。つまり全く違ったビジネスモデルや製品からスタートすることになります。
小泉:
入交さんの会社はPoCの製品の引き合いが多いとよく効くのですが、PoCから先に進むためのコツはなんですか。
入交氏:
一番はビックピクチャを描いてスモールスタート。PoCだけでは意味がないです。
現在は汎用的に使用されている技術を組み合わせて、今までできなかったことのソリューションを提案しています。
今後は、その先にできること(例えば、稼動管理だけでなく出来高のバッチ入力など)を選択肢として提案する流れになってきます。現場からの情報を集め、稼動や出来高から需給バランスを把握していくことで、PoCのその先につなげていくことになります。その中で、どのポイントから検証をはじめるかを顧客と相談して決めていくことになります。
また、稼動管理のPoCが成功した場合には、その担当とミドルクラスのマネージャーが取材に来ることが多いです。その際にPoCを踏まえてやりたいこと(次に描く展望)の話につながっていくケースが多いのですね。
ミドルクラスのマネジメント層も経営レベルで考えている部分も多分にあります。実際にPoCを実施して成果を出すことで、事業としてプロジェクトを進めいけるようになりました。何年か前までは開発のシステムとして頓挫してしまうような状況が、現在実施しているPoCでは見られなくなってきました。
環境が変わりPoCからの明らかな成果が見えるようになってきたので、経営レベルでそれを事業として続けていけるようなエビデンスが持てるようになってきています。
中村氏:
10年前にはできなかったことも、技術が整ってきたことで、またコスト的にも安く仕入れることができるようになってきました。まさに環境が変わって試せることが増えています。
小泉:
環境の変化は、割とメーカーになりやすくなったという意味合いでもあります。
部品を作っている企業は部品メーカでしかなかったのですが、技術力があればメーカとして完成品を製造できるようになってきました。メーカーであれば、マーケットを見ながら新しい製品の開発もできるし、新しいものを作ることで道が開けるようになります。下請けの立場では、どうしても顧客のオーダーによって行動が制限されてしまうので、その違いは大きく出ると思います。そういった意味で、どの企業もメーカを目指すべきだと思いますが、そういったことは難しいのでしょうか。
中国を見てみると部品メーカーが完成品メーカーに進化しています。中国の展示会を訪問しても今年はどの企業もメーカーとしての展示しかなく、部品メーカはどこに行ってしまったのかといった感じです。日本の部品企業も完成メーカーにはならないものでしょうか。
中村氏:
確かに中国の部品メーカーは、部品だけの製造をストップしていて、逆に日本のメーカに部品の注文をするようになってきています。ある部品メーカーは、中国では付加価値のある完成品を製造する一方で、日本の部品メーカーに発注するというこれまでの役割と逆転させているといっています。
八子氏:
最近のニュースで業界内で話題になったのが、ファーウェイが日本に工場を作るというものです。
初任給は40万円/月と破格なのがとくに驚くべきことでした。これまでは日本の完成品は性能が高いといわれていましたが、現在は部品レベルで日本製はよいと評価され、少し先の話では日本の従業員はレベルが高いと評価されています。つまり、製造業の民主化が進んできていることで、日本が搾取される側になってきてしまっているのではないでしょうか。
現在は、アイディアや発想があれば、整った環境・ツールを利用して無から実体があるものを作れる時代になってきていると思います。一人製造業や中小企業が完成品メーカになることは、様々な国で増えてきているので、日本の企業としても上流を目指していけるような取り組みをしていくべきです。
コストや人数の勝負ではなく、アイディアでステップアップを目指し、あらゆるツールを活用してそのアイディアを実現する勝負の世界になってほしいですね。
会場からの質問
質問者①:
変種変量生産をデジタル化して全自動にすることは難しいとのお話がありましたが、素人的には、それをする為にIoTがあると思っていました。
川野さんの資料にあった、NVIDIAのオープンイノベーション事例には、変種変量生産のデジタル化に成功しているとありました。デジタル化が難しいとのお話ですが、どこがネックになっているのか、またどこを押さえれば、現場もデジタル化への変更をやる気になるのか教えて頂いても良いでしょうか。
川野氏:
NVIDIAが成功できたのは、部品をすべて標準化したところにあります。
実際のカスタムキッチンにおいては、フリーハンドで書いた設計図通りの完成にはなりますが、点版の厚みやヒンジの仕様、ダボ穴などを、部品を組み付ける部分をすべて標準化しました。具体的には、標準化する品番を増やして(点版だったら厚さ26㎜のモノを数種類を)使用することを前提に、それぞれの部品をどのように組み合わせるか(組付け変更をするのか)を検討していく手法です。
既存の仕様の変更をする際には、組み付ける部品の種類を変更することにより、新たなカスタム体験を引き起こすことができます。カスタム品だからすべてのモノを1から設計検討するのではなく、標準品の種類を増加させてその組み付ける方法だけを変更する仕組みづくりができたことが成功につながりました。
質問者①:
弊社での自動化への対応ができない要因としては、標準品がたくさんありすぎて、また各部品の組合せも大量になる為、計画を作成する時には自動化が難しく人の手が必要となってしまいます。エヌビディアの事例ではAIを使用して、データのとり方を工夫したりしているのですか。
川野氏:
エヌビディアではAIは使っていませんが、生産計画の面でAIを使用するソリューションは出てきています。
AIが計画のすべてを見通してアルゴリズムを通して計画を自動で進めてくれるような仕組みを想定する事業の開発(スタート)が大事です。標準品が多すぎるというところでは、標準品に見えますが、実はカスタム品である可能性があります。なので、標準としてどこを抑えておかなければいけないのか、整理することが必要です。
例えば、天板は自由にするけれど、その厚みは標準にする(変えない)であったり、ヒンジも標準のモノを使用するだとかが必要です。組み合あせる接点の部分を統一規格にするということで、種類の増加も少なくできたり、整理できていくと思います。
八子氏:
後は、カスタマイズした枝番のモノも標準品として認識することはやめるべきですね。枝番を組み合わせることは、デジタル上では、コーディング、さらにはインターフェイスの接合点を新たに検討することになり、組合せの種類を増加させてしまう手間がかかります。
質問者②:
地方創生のプロジェクトをしていますが、東北で、どのようなITを使ってゲームのプロジェクトを創生していくかを考えています。
オートメーション化することで効率化・品質の向上をできると理解していますが、一方で地域の工場で就労している人々が、現状の業務をオートメーションで奪われてしまい、結果その職種を変更せざるを得ないと思いますが(例>手作業で業務をしていた人が、データをサイエンスするということは難しいと思う)。
オートメーション化がすすんだ際に、製造業の中で新たな仕事(オートメーションを監視・管理するような人がやるべき仕事)が生まれることはありますか。例えば、セルフレジができて、レジ打ちの人は減るが、その分レジを監視・管理をする人が増えるようなことはなりますか。
入交氏:
データをたくさん収集するとそのデータのクレンジングにどれだけ時間がかかります。
オートメーションで人は確かに減るが、それを管理することは実はものすごく大変です。これらは、職種の変更になるのだが、その職種には実はノウハウがあるので、マイニング改善の業務フローを作ったり教育する工程を作ったりすることで、改善していくこが良いのではないかと思います。つまり、新しい仕組みを作ることは、新しい管理体系を作ることが必要になるので、その方向へシフトしていくことが重要になってきます。
教育・新たな管理体系の創出には、人々の得意分野を活かす方法を検討することが大切です。例えば、年配の方へのデジタル再教育。逆にスマホネイティブの人たちが業務を学んでいく。それぞれが持つ得意分野を生かしながら共同で新しい仕組みを覚えていくのが良いですね。それが、業務の新たな変革となるので、その業務変革をサポートする仕組みを作ることが必要です。
質問者②:
年配の方が多いので、新しい仕事を覚えることは億劫になっています。現場では、その声が特に強いので、結果経営陣も変更に踏み切りづらい状況になってしまっています。
入交氏:
スマホの例でいうと2通りの人がいます。
スマホを使える人と使えない人です。使える人はデジタル化への対応はさせやすいです。使えないの人への対応には、人を教えてあげたり(今の段階ではAIにできないこと)、ガラケーなりのこだわりの仕事を教えてあげるなど、得意分野への誘導が必要です。
八子氏:
ノウハウをデジタル化する、いわばビデオでとってしまうという方法は効果的です。
機械にいきなり任せてしまうのではなく、3-5分くらいの操作手順などのビデオで、各工程についての説明用の紹介を準備します。コンテンツとなる一歩手前で、人がアプローチしやすい形を作りだすことで、デジタル化の継承をするということは、シスコの時には好評でした。また、IoTをしていくと、データの出力・入力の中で、どことどこが繋がっているのかわからない状況が多くなってきます。
例えば、iPhoneの中に音楽ファイルを入れてあるのか、クラウドに入れてあるのか不明になっているケースが多いです。なので、教育で指導する段階では、どのような手順を踏んだらどんな結果になるのか教えてあげるような、ポイントごとの説明が必要になってきます。
川野氏:
教育の話でいうと、シニアと若手でペアを組んでやることで、良いギブアンドテイクができます。
経験者はアナログ的な知見を伝えたいし受け止めてほしいというのが、願望としてあります。それを若い世代のITエンジニアと組合せることで、新しい体験と成果を作ることができます。世代間を超えた、技術をお互いに知れるし簡単にしていく構造を学んでいけます。扱う内容だけでなく、人対人で伝承ができていくのも一つの魅力です。
小泉:
ところで、オプテックスは昔とは違って、急に社内全体がつながる会社になったと思います。ここ2年以内の話だと思うのですがなぜでしょうか。
中村氏:
マーケットがそうだからというのが一点。開発コストが驚異的に下がったからです。他には、社長決裁だったものが、役職クラスでできるようになったこともあります。専用のツールを使って設定しなければならなかったものが、今はすべてスマホでできます。マーケティングの観点でもコストの観点でも明らかに変わっていることが大きいですね。
最後に
小泉:
最後に「どうする日本の製造業?」という本日テーマで皆さん一人ずつコメントをお願い致します。
中村氏:
直近だとファーウェイが本当にすごいですね。中国へ進出した日本の技術を使って伸びているではないかと思いますが、それは置いておいて、日本でも、我々ができることはまだまだあります。日本の製品が世界に認められる部分もあるし、ニッチなところでグローバルに勝てている部分もあります。
これからは、日本連合(グローバル連合)で地位を確立して進めていくことが大切ですね。そこで、競争・競合・オープンイノベーションを積極的に実施していくことが重要だと思います。
入交氏:
日本人の苦手なところをITの力で手助けできるような、そんな製造業になってほしいと思います。
日本人は、全体の構想を考えて進めること(抽象化)が苦手であり、その一方で製品製造には優れた技術力を持っています。全体のシステムデザインを見通して、各工程で必要な能力をどう発揮させていくかをITの力を駆使してサポートしていけたら、日本の製造業は良い方に進むと思いますね。
川野氏:
製造業に限らず、デジタル化は、競争原理やルールが変わることだと思います。
そのときに自分たちの立場・環境・概念にとらわれずに、自分たちに役立つツールを見つけながら選択をしていってほしいです。
原理やルールの変更は、チャンスとピンチが表裏一体でもあるので、デジタルのツールを使用することの意味と効率性をよく検討した上で、取り入れるという選択をしてほしいと思います。AIに代わることはネガティブな部分だけでないことを強く言いたいですね。
八子氏:
IoTは、「繋がっていなかったもの同士をつないでいくこと」だと個人的には思っています。
様々な部分で境目がなくなるということです。
例えば、取引先との関係、工場の内と外、前工程と後工程、調達とロジ・デリバリなどがその例です。製造業という分類では、すでにその垣根を作ってしまっている状態で、その部分に閉じこもっているだけだと、他への繋がりが見えてこないのです。極端に言えば、製造現場だけがモノを作るのではなく、調達がモノを作れる状況であっても良いと思います。
いわば、関連する部署同士が、互いに補完し合いながら、新しいモデルを構築していくことが製造業の中では大事でしょうね。全体をアレンジするところが製造業が行うことであって、全体を見据えたもっと広い視点でモノづくりをしていくことが新しい価値や日本を元気にしていく為の秘訣ではないかと思います。
またそれが、自社だけでできないのであれば、足りないことを他社と補完し合いながら進めていくことで、スマートファクトリーも進むべき方向性を見つけて進んでいけるようになると思います。
小泉:
皆さん、ありがとうございました。
関連記事:
第一部 どうする?日本の製造業!我国製造業の現状と課題ーConnected Industriesの推進に向けて 「IoT Enabled Solution」がIoT市場拡大を牽引、製造業のとるべきアクションとは? どうする?日本の製造業 第二部 スマートファクトリーをいかに導入し、結果をだすのか
Smart Factoryプロジェクト進まない課題とスモールスタート実例 「経産省スマートファクトリー実証事業のご紹介」〜AIとPC制御により既設設備を活かす産業IoT〜 ~勘と経験のデジタル化で現場が変わる~ものづくりデジタライゼーションで見えてくる未来 スマートファクトリ―!現場・IoTの流れ、特に通信からみての考察 スマートファクトリーをいかに導入し、結果をだすのか
無料メルマガ会員に登録しませんか?
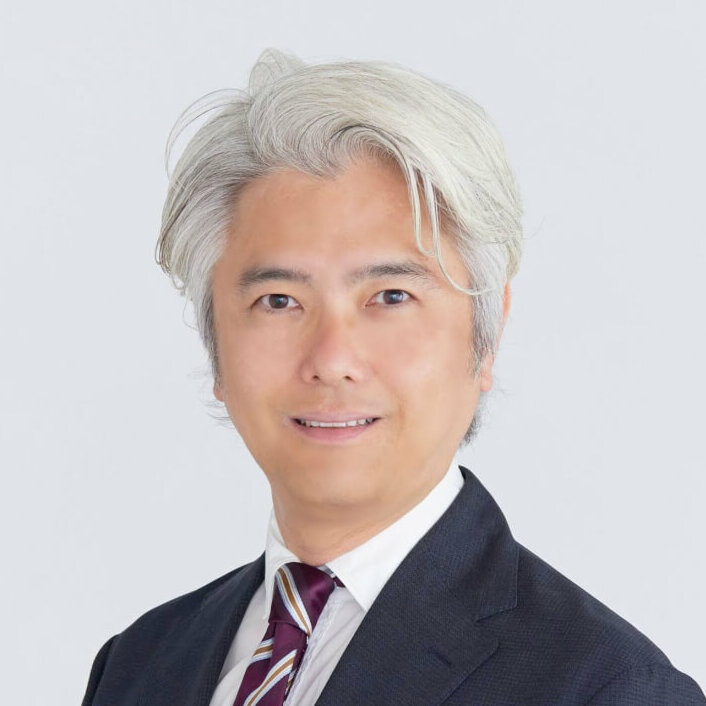
IoTNEWS代表
1973年生まれ。株式会社アールジーン代表取締役。
フジテレビ Live News α コメンテーター。J-WAVE TOKYO MORNING RADIO 記事解説。など。
大阪大学でニューロコンピューティングを学び、アクセンチュアなどのグローバルコンサルティングファームより現職。
著書に、「2時間でわかる図解IoTビジネス入門(あさ出版)」「顧客ともっとつながる(日経BP)」、YouTubeチャンネルに「小泉耕二の未来大学」がある。