3. 「Contexer」で生産管理システムを自社開発
「業務の見える化」で課題を特定したあとは、ITシステムを活用し、互いに情報共有しながらチームで業務をこなせるしくみをつくろうと今野社長は考えた。しかし、システムをまるごと導入するのはお金がかかる。「当時の経済力では無理でした」(今野社長)。
そこで、当時発売したばかりだったサイボウズのクラウドサービス「kintone」を使い、業務アプリを作成していくことにした。最初は営業の「案件管理」。それまで、「価格の決め方」は営業マンの頭の中にしかなかった。そこで、納期の条件や運賃、予算、他社の置き換え/新規といった情報をシステムに入力することで、誰でも閲覧できるようにした。
次に取り組んだのが「アフターサービス」だ。顧客から工場に製品が返ってくる場合、それはクレームか修理依頼のいずれかである。ただ、かつての今野製作所ではそれがどちらなのかわからなかった。ただ、ある日とつぜん使い古された油圧ジャッキが福島工場に送られてくる。社内で聞いても誰もわからず、大阪の営業マンだけがそれを知っている。そういうことが頻繁にあったのだ。
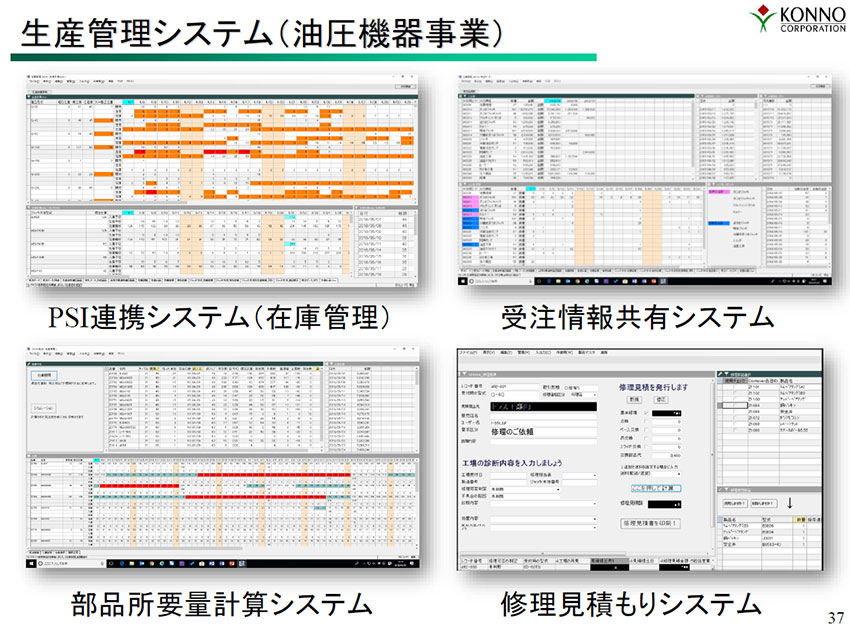
設計部門では並行して3DCADソフト(コンピュータを用いた3次元の設計支援ツール)の導入を本格化。設計データを共有し、「〇〇の製品は××さんしか設計できない」という状況をなくしていった。最近では構造解析ソフトや板金加工のシミュレーションツール、3DCADデータで製品情報の管理および他システムとデータ連携できるPDM(Product Data Management)のしくみも導入した。
一方、Kintoneのような汎用的なしくみを使うだけではなく、生産管理システムの自社開発も、ほぼ同時期の2011年に始めた。具体的には、法政大学教授/IVI理事長の西岡靖之氏によって開発された情報連携ツール「Contexer」を活用し、受注・購買・生産・出荷の一連のサプライチェーンをつなげる生産管理システムを独自開発することを目指したのだ。
当時「IT担当者」はいなかったが、社長自らと、ものづくり技術者として採用した新入社員の二人が、同教授のもとで生産システム構築手法を学んだ。
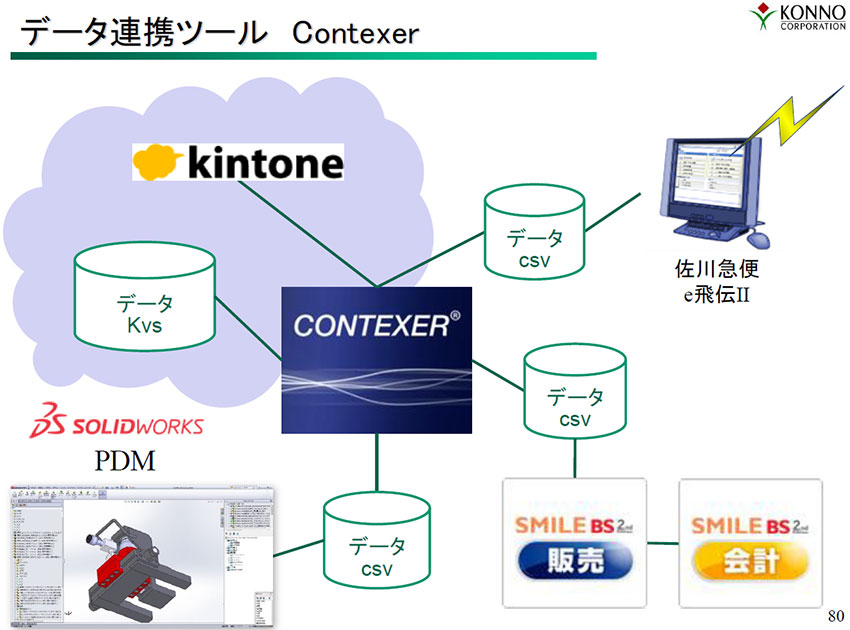
最近では、前述のPDMとContexerの連携に着手。PDMにあるCADの部品構成データをContexerにつなげて発注手配するしくみだ。これまでは、設計者がPDMでつくった部品構成情報をエクセルに打ち直して、さらにもう一度、発注システムに手入力していた。CADと発注システムの間を一気通貫にすることで、設計段階でコストを意識できるとともに、設計者の負荷を減らせる。
「製造業におけるIT化の悩みは、ベンダーさんが提供するパッケージのシステムでは現場の実情に合わないことです。弊社は小さな会社ですが、板金事業と油圧事業では管理のポイントがかなり違います。これらを一つの生産管理システムでまかなえる製品はないかと探しましたが、どうしても見つかりませんでした。そこで出した結論は、自分たちでつくるしかないということでした」(今野社長)
次ページ:4. IoTの取組や他社との連携も開始
無料メルマガ会員に登録しませんか?
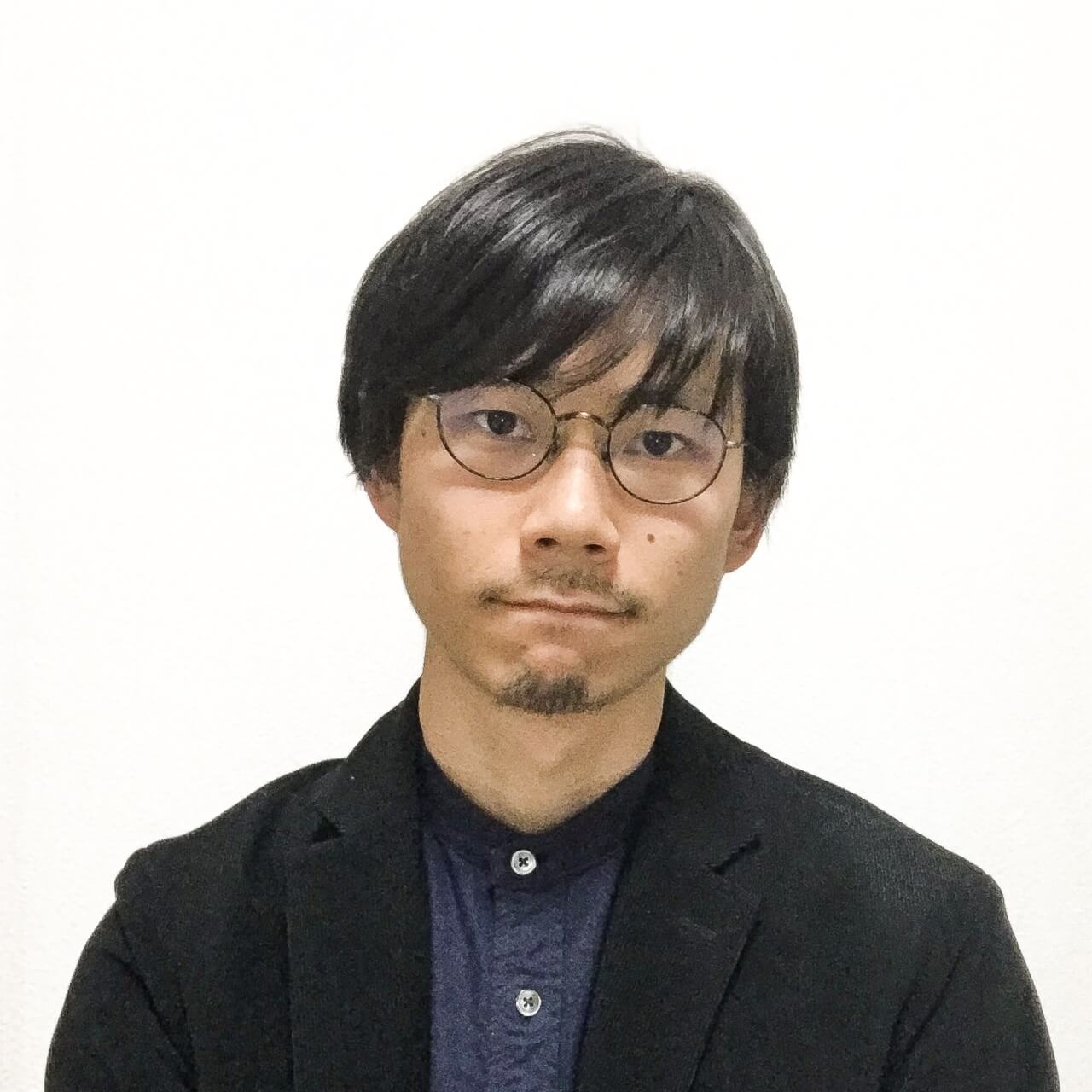
技術・科学系ライター。修士(応用化学)。石油メーカー勤務を経て、2017年よりライターとして活動。科学雑誌などにも寄稿している。