4. IoTの取組や他社との連携も開始
こうした約8年間にわたる地道なデジタル化の成果もあり、今野製作所の昨年の売上は過去10年で最高額になった 。また、社内の雰囲気も大きく変わってきたという。「新しいツールを使って現状を改善したいという声が現場から上がってくるようになりました。ようやく色々なことにチャレンジしていける土壌ができたと感じています」と今野社長は手応えを語る。
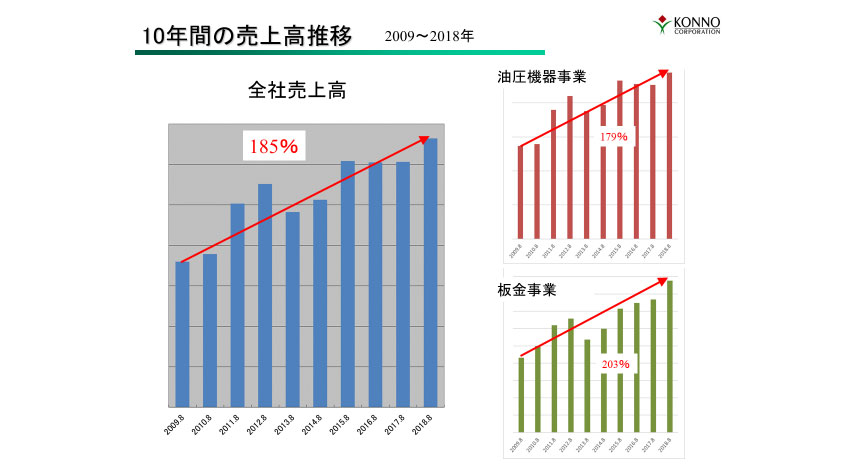
また、社内のデジタル化を進めた今野製作所は、社外との連携も進めている。その一つが、株式会社西川精機製作所(江戸川区)、株式会社エー・アイ・エス(江戸川区)との3社連携による「つながる町工場」の取り組みだ。
互いの強みを持ち寄ることで、「売上拡大」や「新分野開拓」といったそれぞれの課題を達成していくことが目的だ。現在は、今野製作所で構築したシステムを水平展開し、製造工程の連携に取り組んでいる。「東京の町工場は規模が小さく専業化しているので、もともと連携はしていました。ただ、それはヒトとヒトの物理的なつながりにとどまっており、受発注や工程進捗を共有するということは誰もやってきませんでした」(今野社長)
もう一つは、海外メーカーとの連携だ。今野製作所が手がける油圧機器のシリンダユニットは台湾のメーカーに製造を委託している。これまでは、今野製作所で所要量計算をして発注データを作成すると、そこからわざわざエクセルでPDFの注文書をつくり、メール添付して商社を経由して同メーカーに送っていた。しかし、クラウドで両社がつながっていれば、その必要はない。そこで、同社はKintoneを用い、クラウドで簡単に受発注データを共有できるしくみを提案中だ。
また、そのシリンダユニットは今野製作所に届いたあとに全数製品検査を行っているが、出荷前に台湾メーカー側でも検査を行っている。台湾メーカーが実施する検査装置をIoT化し、検査データとその進捗をリアルタイムで共有できれば受入検査を簡略化できる。台北にある貿易商社、今野製作所の東京本社と福島工場のサプライチェーンに関わる各担当者が進捗情報を共有することで、さらに納期は確実になり、顧客に安心を届けられる。
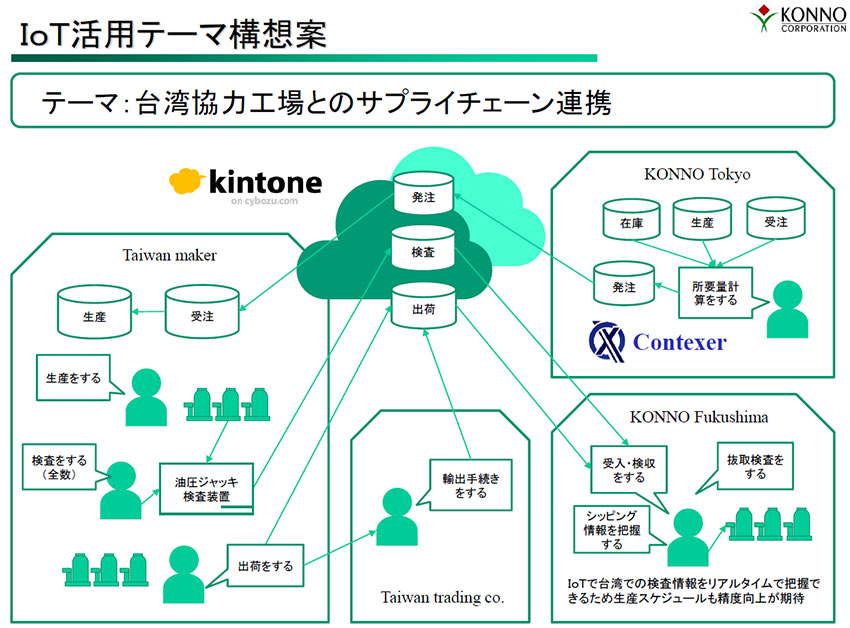
現場でのIoT活用も進めている。前述のエー・アイ・エスと昨年、「東京町工場ものづくりのワ」を立ち上げた。そのプロジェクトの一つである「溶接技術研究所」では、IoTを使ったTig溶接とスポット溶接における「匠の技」のデジタル化に取り組んでいる。
「スポット溶接は一見誰でもできそうな作業です。しかし、熟練者の仕事を若手に任せるととたんに不良が増えます。たとえば、長時間の連続運転で電極が熱をもってしまったり、電極の先端が汚れたりしてしまうと電流がうまく流れなくなる。ベテランはそれを経験からみきわめて、適度にクリーニングしたり、熱くなりすぎたら冷ましたりしていることが明らかになりました。しかし、その『熱くなりすぎ』が何度なのか、新人にはわかりません。ベテランは『これくらい』と感覚でやっていたのです」(今野社長)
そこで、溶接技術研究所ではセンサーで電極の温度や電流値を測り、「何度になったら冷ますか」といったノウハウを若手にも継承できるしくみの構築を目指している。
IoTの取り組みについて、今野社長は次のように語る。
「私も以前は、IoTは自分たちに無縁だと思っていました。それは量産型の工場で、機械の稼働率が利益に直結する場合の話だろうと。でも、そうではないのです。自分たちに何が必要で、ツールを使って何ができるかわかってくると、ITでもIoTでも、アイディアは自然と生まれてくるものです」
無料メルマガ会員に登録しませんか?
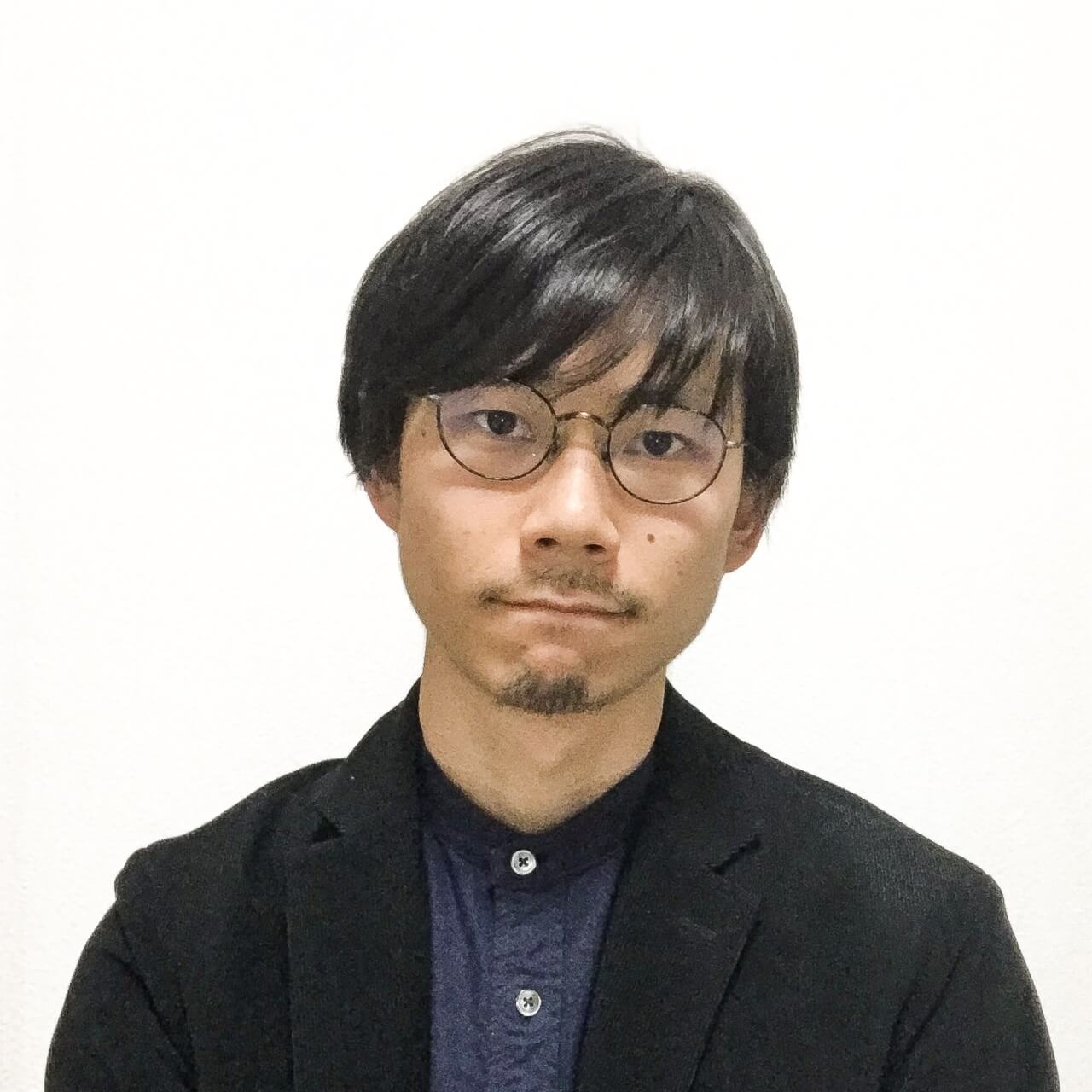
技術・科学系ライター。修士(応用化学)。石油メーカー勤務を経て、2017年よりライターとして活動。科学雑誌などにも寄稿している。