第四次産業革命や国内の人材不足の深刻化にともない、日本の製造業における「デジタル化」の取り組みが注目を集めている。ただ、ものづくりの現場はつくる製品や会社規模によって状況がさまざまであり、デジタル化の目的や使いどころは一概に語れるものではない。
株式会社今野製作所(東京都足立区)は、板金加工や油圧機器のものづくりを手がける社員数36名の町工場だ。同社は2010年から業務の見える化や生産管理システムの自社開発などに取り組み、社内変革を実践してきた。
その地道な活動の成果が実り、昨年は過去10年で最高額の売上を達成 。また、「中小企業IT経営力大賞」(経産省、2012)、「つながるものづくりアワード2016」(IVI、2016)、「地域未来牽引企業」(経産省、2018)といった多くの賞を受賞し、2018年度「ものづくり白書」では中小製造業におけるIT活用の先進事例として紹介されている。
このほど同社を訪問し、今野製作所がどのようにデジタル化を進めてきたのか。その歴史を追った。
1. きっかけは2008年のリーマンショック
今野製作所は1961年に東京都北区で創業。板金加工を軸に、主に医療理化学の分野で使われるステンレス製品を手がけてきた。一方、1976年には油圧爪つきジャッキ「EAGLE」の販売を開始。5~10トンのモノを簡単に持ち上げることができるEAGLEは主に工作機械の搬入時などで使われる他、文化財や鉄道の保守メンテなど利用シーンは幅広い。国内シェアは現在7割を占める。
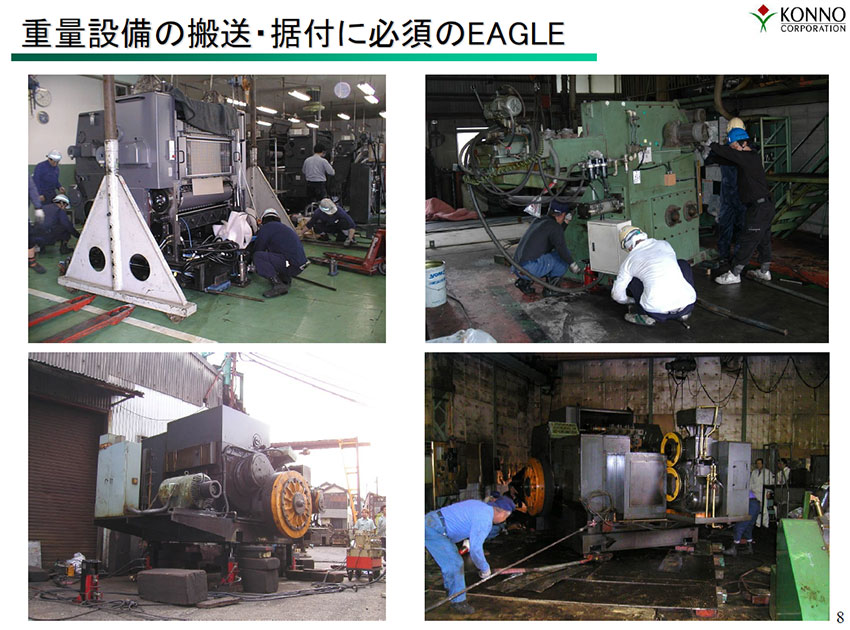
油圧機器と板金加工の2つの事業を柱に順調に売上をのばしてきた同社だが、やがて危機が訪れる。2008年のリーマンショックだ。とくに定番品の油圧機器が大ダメージを受け、2009年の売上は45%も落ち込んだ。
そこで、今野浩好社長(2代目)は方針を変えた。油圧機器事業の「特注品」に力を入れ、もともと個別受注生産だった板金事業との相乗効果を狙ったのだ。油圧機器に多くの経営資源を割いたこともあり、量産を基本とする板金の主流からは「とりのこされた」という思いがあった今野社長。しかし、「匠の技」を駆使し、多品種少量生産でオーダーメイド品に対応する「一品料理」のものづくりは今野製作所の強みだった。その強みを活かし、信頼性の高い製品をつくる方向に舵を切ったのだ。
ホームページもつくりかえ、「個別ニーズに対応します」と積極的に提案営業を続けた。すると、ニーズはあちこちで見つかり、仕事は増えた。個別ニーズ対応の戦略はうまくいったように見えた。しかし、今度はまったく予期していなかった問題が起きた。2010年頃になり、とたんに忙しくなってきたのだ。売上がのびているわけでもないのに、社員が毎日のように遅くまで残業をしている。「最初は何が起きているのかわかりませんでした」と今野社長は振り返る。

発端は、特注品の対応が増えたことにあった。特注品の場合、決まった作業を繰り返すだけではないので、業務は複雑になる。そのうえ、見積もりの回数も増えるため、マスター登録していない製品がたくさんあり、出荷はしているのに伝票が発行されておらず、顧客から「請求書はいつくるの?」と言われる事態に何度も見舞われた。
また、今野製作所は本社工場、大阪営業所、福島工場と事業所が3つに分かれている。もし、すべての社員が同じ場所にいれば、ヒト対ヒトですぐに解決できることもあるかもしれない。しかし、離れているために事態は収拾しにくかった。さらに、ちょうど人が入れ替わるタイミングも重なり、混沌とした状況が続いた。
「このままだと会社はつぶれてしまうかもしれない」。途方にくれた今野社長はある日、知人の中小企業診断士やITコーディネーターに会社の現状を打ち明けた。そこで、紹介されたのが「バリューチェーンプロセス協議会(VCPC)」だった。
無料メルマガ会員に登録しませんか?
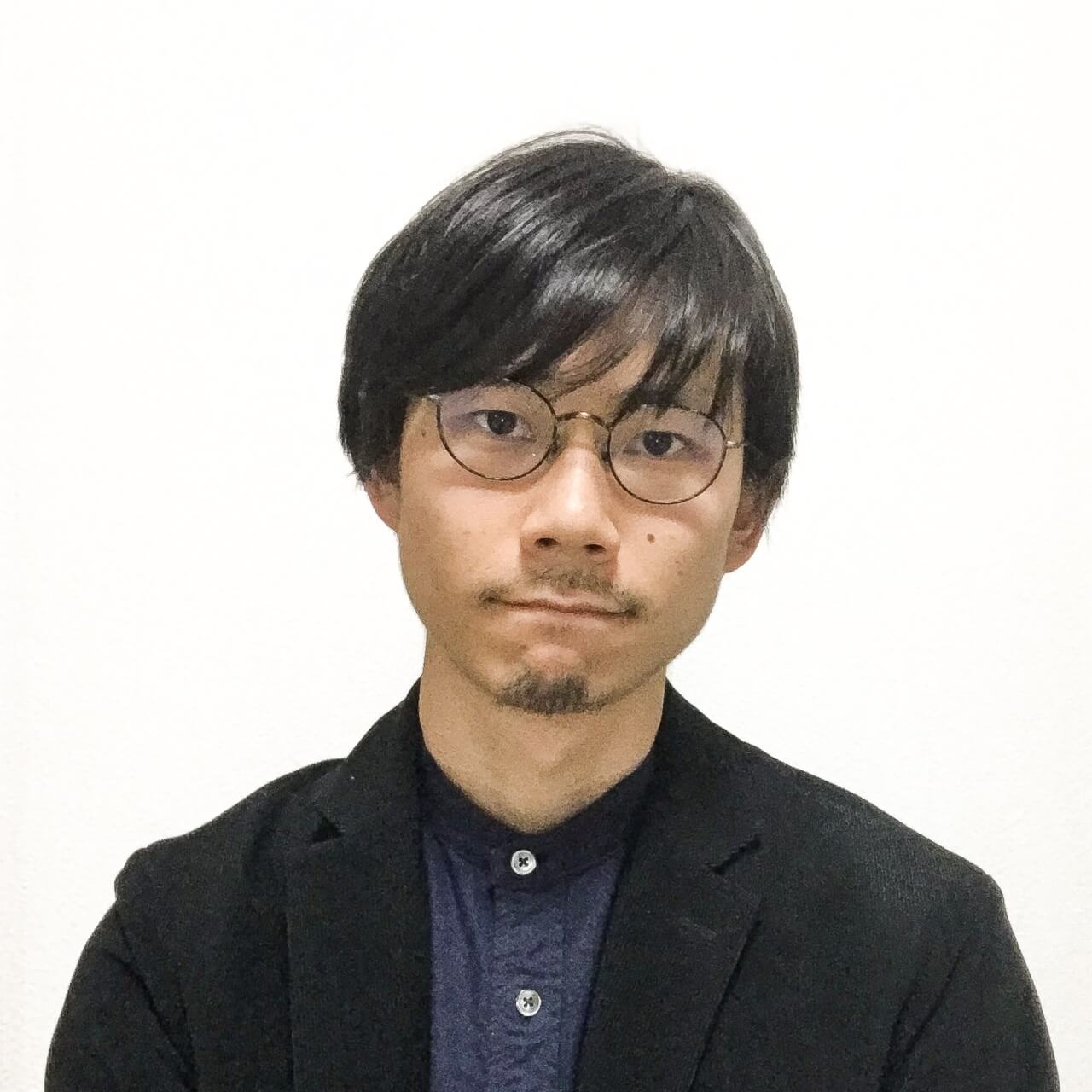
技術・科学系ライター。修士(応用化学)。石油メーカー勤務を経て、2017年よりライターとして活動。科学雑誌などにも寄稿している。