2022年6月、IoTNEWSの会員向けサービスの1つである、「DX事業支援サービス」の会員向け勉強会が開催された。本稿では、その中からマツダ株式会社 横畑 英明氏のセッションを紹介する。
自動車は、エンジンやタイヤ、車体など様々なパーツで構成されている。そのため、設計・開発の段階で1つでも構造や仕様を変更すると、他のパーツに影響を与えてしまい手戻りが頻発するといった課題が、自動車の製造現場では存在している。そうした課題に対して、マツダは、開発工程をモデルベース開発(以下、MBD)により変革し、効率化に成功した。
マツダ株式会社 役員付 MBD革新担当 技監 横畑 英明氏に、MBDと従来の開発方法との違いや最近の取り組みについて、事例を交えながらご講演いただいた。
目次
従来の開発方法
MBDに取り組む前のマツダでは、車体の設計・開発を行う車両部門とエンジンなど動力源を設計・開発するパワートレイン部門の大きく2つの分野に分かれて設計・開発を行い、完成したパワートレインと車体の製品レイアウトを組み合わせて製品として問題ないかを判定していた。
開発の難しさ:ガソリン車
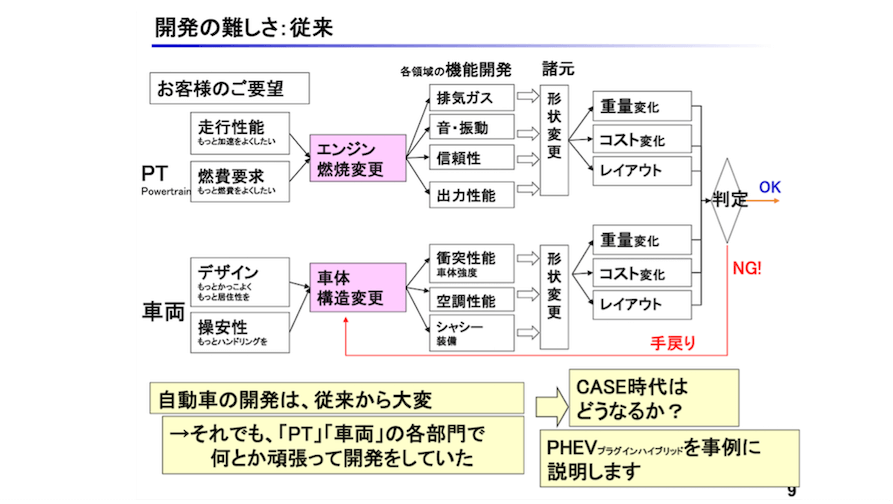
顧客は、自動車に対して、「燃費を良くしたい」や「走りを良くしたい」、「デザインを良くしたい」など様々なニーズを抱いている。開発を行う各部門は、顧客のニーズに応えるため、個々に開発を進めていた。
例えば、パワートレイン部門では、「燃費を良くしたい」や「走りを良くしたい」というニーズに対応するためにエンジンの燃焼変更を行う。その結果、排気ガスの量やエンジン音、信頼性など様々な箇所に影響が出てくる。影響が出た箇所に対して一つ一つ対応していくのだが、結果として、重量やコストが増大し、製品レイアウトも変化する。
一方、車両部門では、「デザインを良くしたい」というニーズに応えるために車体構造を変化させると、衝突性能やシャシー(自動車の基本骨格)などの様々な性能に影響が出てくる。ここでも重量やコストが増大し、製品レイアウトも変化する。
そして、出来上がったパワートレインと車体の仕様だが、それぞれを組み合わせ1台の自動車として製品の完成度を判定すると不適合になる可能性が高く、手戻りが発生し、設計から見直すことになることが多かったという。
開発の難しさ:PHEV(プラグインハイブリッドカー)
自動車業界はCASEというキーワードと共に変革の時代を迎えている。横畑氏はPHEVを例に上げ、CASE時代の自動車開発の難しさを解説した。
ガソリン車とPHEVでは、動力源をパワートレイン部門が設計・開発し、車体を車両部門が設計・開発するという点では開発体制に差異はないが、自動車の構造に大きな違いがある。
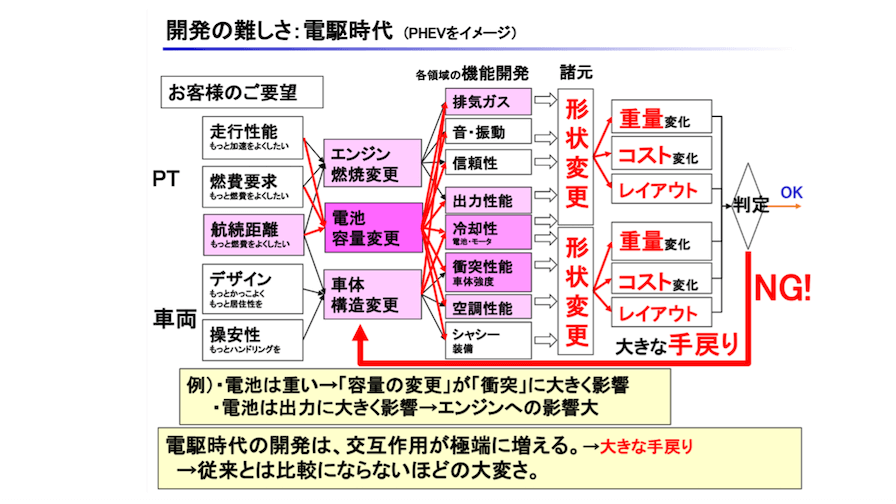
横畑氏によれば、PHEVには、エンジンの他に大きく重たいバッテリーが搭載されており、車体のどこにバッテリーを搭載するかで性能が変わるという。
例えば、バッテリーによる走行距離を長くしたい場合は、搭載するバッテリーの容量を増やす必要がある。バッテリーの容量を増やそうとすると、重たいバッテリーを載せた車体は重くなり、衝突性能に影響が出る。
従来のガソリン車と比較した場合、PHEVの開発の場合は、パワートレインと車両の相互作用が極端に増えてしまうということだ。これは大きな手戻りが発生する原因となってしまう。
そのため、自動車の開発はCASE時代に突入したことにより、従来よりも比較にならないほどの大変さになっているそうだ。そこで、個々の部門で開発する従来の開発方法ではなく、MBDによる開発が重要になるのだと横畑氏は語る。
MBDとは
MBDとは、設計開発において、実際の試作部品ではなく、コンピュータ上で再現したモデルを活用することで、部品試作やテストにかかる時間と手間を大幅に削減し、効率的に開発を行う開発方法である。
一般的にMBDは、「制御モデル」を用い机上で制御開発を行うことを指すのだが、マツダでは、「制御」や「CAE」など机上検討の全てを含めてMBDとしている。
MBDの重要性
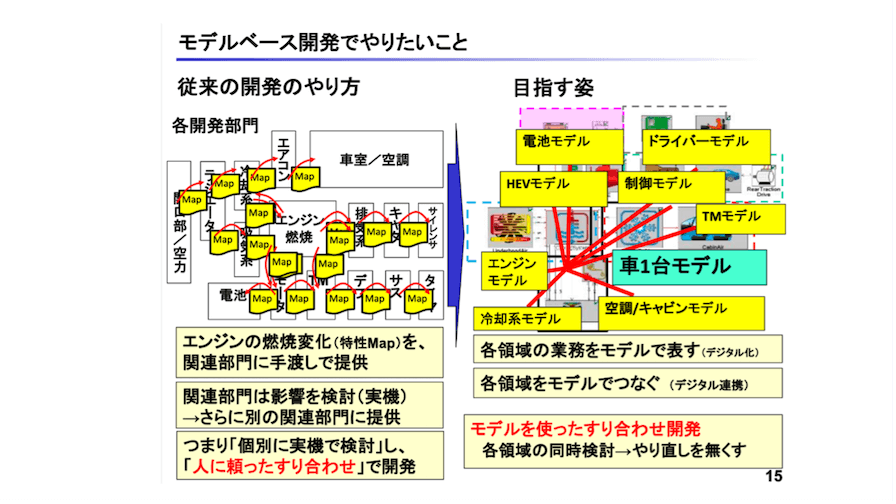
マツダを含めた自動車の製造を行う企業には、部品毎に設計・開発する部門が存在する。例えば、エンジン部門や冷却機部門、モータ部門、タイヤ部門などの部門がある。
エンジン部門がエンジンの燃焼を変えると特性が変わるので、エンジン部門はモータ部門にそのデータを渡す。モータ部門は、エンジンの変化で起きる影響を実験し検討する。そして、その結果のデータをさらに他の部門へと受け渡す。
この様な個別の検討と人に頼ったすり合わせを経て、自動車は開発されてきたそうだ。しかし、部門間でのデータの受け渡しに関するミスの発生リスクは、人が行う以上、必ず存在し、それが影響して大きな問題が発生するという。
マツダは、これまでの開発方法で抱えていた、頻発する手戻りやデータ受け渡し時のヒューマンエラーなどの様々な問題を解決するために、個々の部門で設計・開発をするのではなく、各部門の業務をモデル化し、モデルとモデルをつなぎ合わせることで、開発の効率化を図るMBDを採用した。
MBDで目指す姿
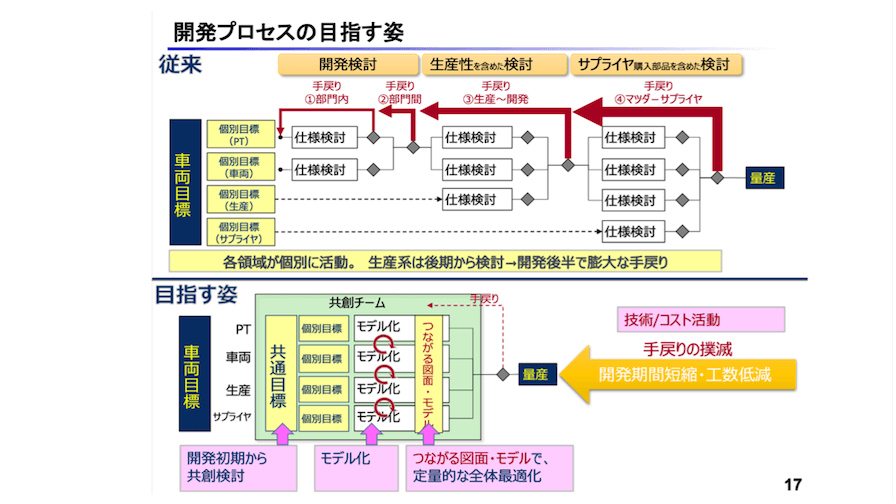
自動車を量産するまでのプロセスでは、設計・開発の問題点を解消した先に、生産部門での検討があり、サプライヤの購入部品を含めた検討へと進んでいくのだが、ここでも手戻りが頻発する。
具体的には、設計・開発で完成した仕様を生産部門へ渡すと、生産部門は、製品レイアウトを見て生産できるかどうかの検討をする。そして、生産できない形状の部品が含まれている場合、設計・開発のプロセスまで手戻りが発生する。
一方、生産部門が、製品レイアウトを見て生産できると判断できれば、サプライヤの選定に進む。しかし、ここでも、サプライヤが対応できるかどうかの判断が入り、対応できない場合は、設計・開発のプロセスか生産性の検討を行うプロセスまで手戻りが発生する。
横畑氏は、「マツダが、MBDで目指す姿は、各部門やサプライヤで、個々に業務を進めるのではなく、全員でモデルを作成し、それらを繋ぐことで、大きな手戻りをなくし、工数の低減や開発期間の短縮を図ることである」と述べた。
モデル作成のための実験
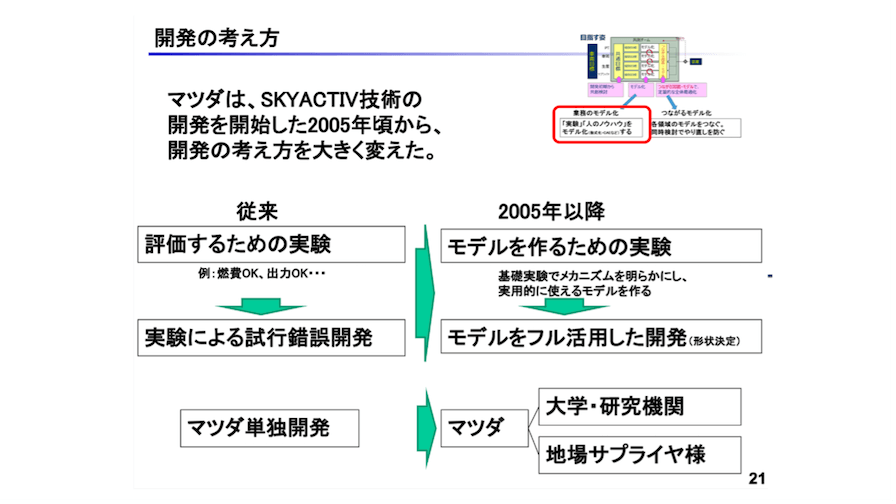
マツダは、2005年に「SKYACTIV技術」の開発を開始した。横畑氏によれば、マツダは、「SKYACTIV技術」の開発当初、従来の開発方法で燃費や出力を評価するための実験を繰り返し試行錯誤していたが、途中からはMBDに切り替え、モデルを作るための実験を行ったという。
従来の開発方法では、マツダ単独で実験を行うしかなかったが、開発方法をMBDに切り替え、モデルを活用することによって、大学や研究機関、サプライヤと共に実験を行えるようになった。
※「SKYACTIV技術」とは、「走る歓び」と「優れた環境・安全性能」を両立するために、車の基本性能をゼロから見直し、最適化したものの総称。SKYACTIVエンジンは、ガソリン、ディーゼルともに、量産エンジンとして世界一の圧縮比「14.0」を実現。圧倒的な低燃費と「走る歓び」を高いレベルで両立した。
共通課題を産学連携で解決
これまで、マツダやサプライヤ、大学は、個々に存在する様々な課題に対して、それぞれで実験を行い解決してきた。しかし、これからは、個々の課題を整理し共通課題とすることで、共同でのモデル作成や研究を実施し、解決を目指す活動を推進している。
事例:大学・研究機関との共同研究
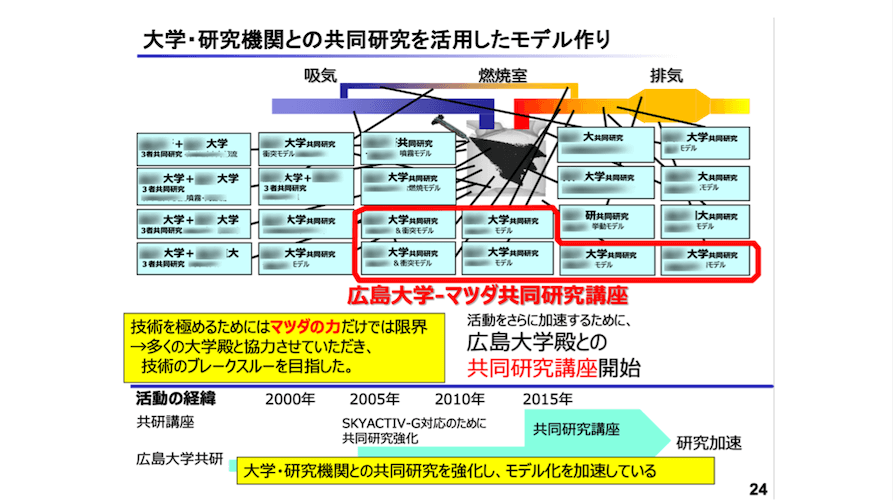
マツダは、大学・研究機関と共同研究を行い、ガソリンエンジン「SKYACTIV-G」の次のステップとなる「SKYACTIV-X」を開発した。
この共同研究で行った取り組みの一例として、マツダおよび大学・研究機関は、燃料を壁に噴霧し、壁に衝突した時の挙動をCAE解析と実験で比較した。当初は、CAE解析の結果と実験結果の挙動に差異があり、その差異を埋めるために試行錯誤した。
横畑氏によれば、試行錯誤を続け、メカニズムを理解し、モデル化に成功したことで、解析結果と実験結果が合致するようになったという。
※「SKYACTIV-X」は、力強いトルク、リニアで正確なレスポンス、高回転までスムーズに伸びていく爽快な加速感など、ディーゼルエンジンとガソリンエンジンのメリットを兼ね備えている。
広島大学との共同研究講座
マツダは、2017年に広島大学との共同研究講座として、広島大学大学院理学研究科内に「次世代自動車技術共同研究講座 藻類エネルギー創成研究室」を開設した。
この取り組みは、広島大学にマツダから教員を派遣し、学生に対して内燃機関についての講義を行い、一方の広島大学からは、マツダに教員を派遣し、自動車について学ぶものである。
事例:サプライヤとのモデル作成
横畑氏は、マツダがサプライヤと行った共同でのモデル作成について、排気形サイレンサーを製造しているヒロテックとの事例を紹介した。
マツダとヒロテックが行った共同研究では、サイレンサーの消音性をCAE解析と実験の結果の比較を繰り返し行ったが、2社では、求める成果を導き出すことができないと判断し、大学を交えてCAE解析と実験を行った。そして、試行錯誤の末、モデルの作成に成功した。
つながるモデル
横畑氏は、「現在マツダでは、単独でのMBDに成功しているが、これからは、サプライヤなどにも普及させ、作成したモデル同士を繋げていきたい」と述べた。
横畑氏は、サプライヤがユニットを作成し、完成品をマツダに納品する業務を例に上げ、MBDにより目指す姿を解説した。
このユニットは、サプライヤA社が製造した部品A、サプライヤB社が製造した部品B、サプライヤC社が製造した部品Cから構成されているとする。
1つのユニットを構成する部品は、バラバラのサプライヤで製造されているため、その製造方法もバラバラであり、基準やモデルの作り方にも違いがある。まずは、A社がB社とC社のモデルをA社仕様に修正する。そのことにより、A社仕様のユニットモデルが完成する。そして、完成したユニットモデルをマツダに納品するのだが、マツダにも基準があるため、マツダ自身でユニットモデルをマツダ仕様に修正する。その結果、完成したマツダ仕様のユニットモデルを活用して、衝突や操縦安定性などの性能を検討することができる。
マツダが目指す姿は、サプライヤA社、B社、C社全てを同じ基準に整理し、標準化するということだ。
MBDを普及する取り組み
横畑氏は、「マツダだけでは、開発部門、生産部門、サプライヤなどの基準を標準化することはできないため、産官学で連携して標準化、MBDの普及に取り組む必要がある」と述べた。
講演では、マツダが産官学と連携して行う、MBDを普及する取り組み「ひろしま自動車産学官連携推進会議(以下、ひろ自連)」、「JAMBE」について紹介した。
広島にMBDを普及する「ひろ自連」
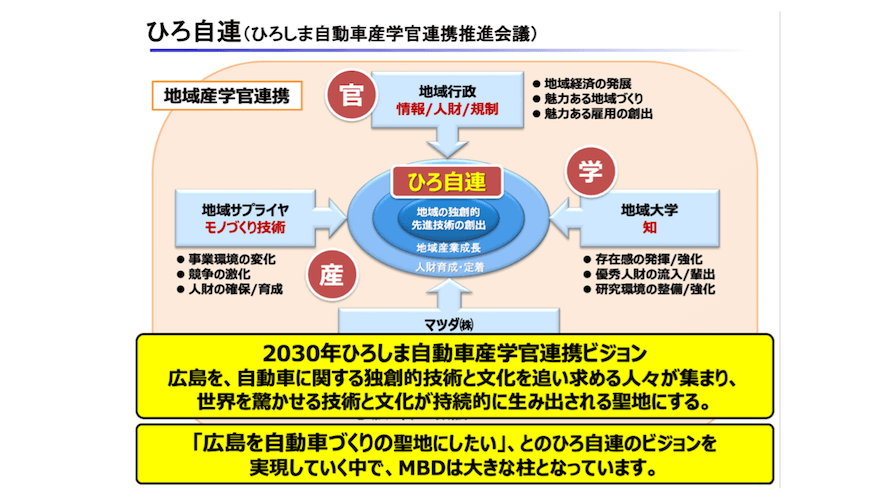
「ひろ自連」とは、広島県や広島市、広島大学、近畿大学、地域のサプライヤ、マツダなどが参画し、産業発展につながるイノベーションのきっかけとなることを目指す産学官連携の推進団体である。
「ひろ自連」は、地域の会社が抱える、設備不足や人材不足の課題を解決するべく、2017年にMBDの研修やCAEの利用環境を提供する「ひろしまデジタルイノベーションセンター」を設立した。2019年には、研究開発や高度産業人材を育成する「広島大学デジタルものづくり教育・研究センター」を設立した。
全国にMBDを普及する「JAMBE」
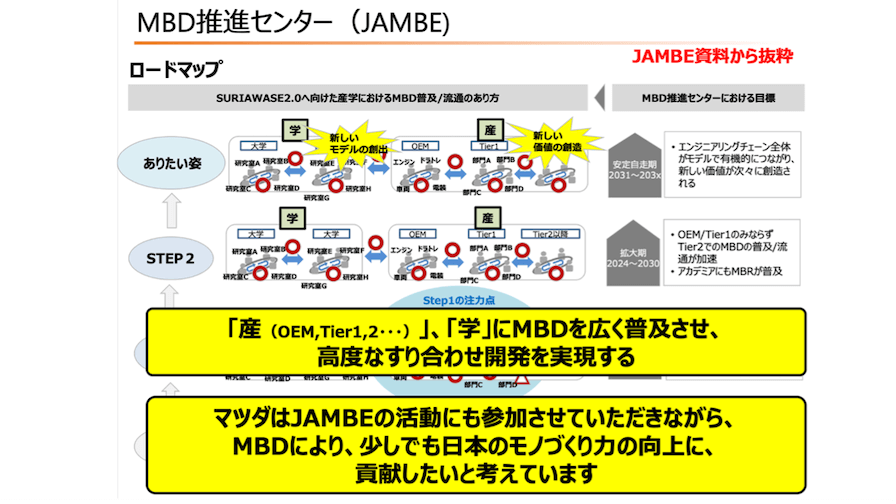
「JAMBE」とは、マツダをはじめとするSUBARU、トヨタ自動車、日産などの企業が2021年の活動開始時から参画し、MBDを広く普及展開し、モデルを用いた高度なすり合わせ開発を実現することにより、日本の自動車産業の国際競争力向上に貢献することを活動方針とする組織である。
「JAMBE」は、カーボンニュートラル対応やCASE等の車両技術革新をMBDで推進しSDGsに貢献することと、すべてのプレイヤーが規模の大小を問わずモデルでつながり高効率な研究開発を推進していることをビジョンに掲げ、MBDの普及推進やモデルの流通推進を活動内容としている。
最後に横畑氏は、「ひろ自連やJAMBEの活動を通して、日本全体をモデルで繋ぎ、日本のものづくりのレベルを劇的に向上させたい。」と講演を締めくくった。
無料メルマガ会員に登録しませんか?
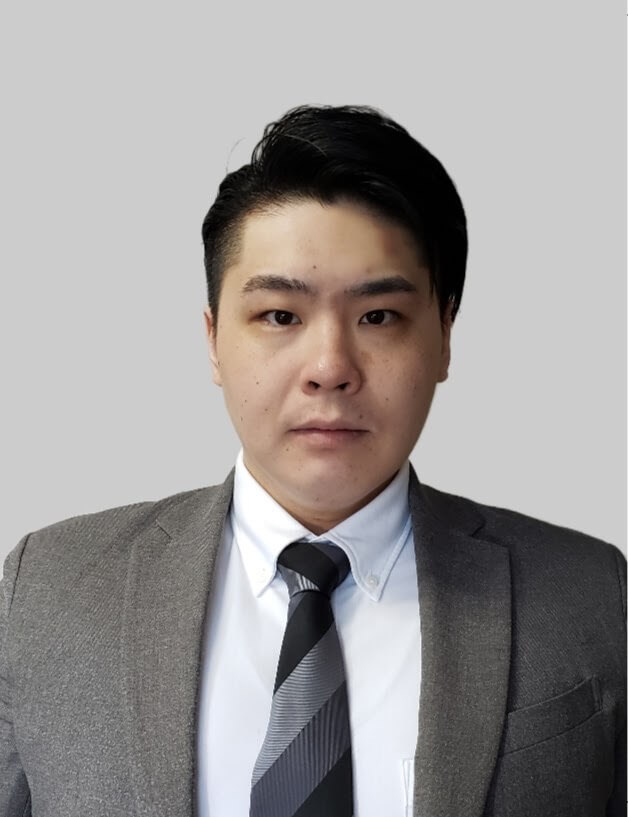
IoTに関する様々な情報を取材し、皆様にお届けいたします。
現在、デジタルをビジネスに取り込むことで生まれる価値について研究中。特にAIの分野に興味あり。