現代の製造業は、人手不足、原材料価格の高騰、顧客ニーズの多様化、そして激化するグローバル競争といった、かつてないほど多くの課題に直面しています。
そんな中、企業にとって最も避けたい無駄の一つが、「手戻り」です。
手戻りとは、一度完了したはずの作業や工程が、品質不良や設計ミス、情報伝達の不備などの理由で、やり直しや修正を余儀なくされることを指します。
例えば、「製造された部品が次の工程で不良と判明し、作り直しになる」「出荷された製品が顧客からクレームを受け、回収して修理することになる」といった状況です。
不良が製造プロセスの初期段階で発見されれば被害は最小限で済みますが、サプライチェーンの下流、あるいは顧客の手元に届いてから問題が発覚すると、その影響は指数関数的に拡大し、企業にとって致命的なダメージとなることもあります。
関連記事:サプライチェーンの基本や最適化について詳しく知りたい方は、こちらの記事も参考にしてください。
サプライチェーンとは?定義や主な構成要素とそれぞれの役割から、業界別の具体例まで徹底解説
サプライチェーンマネジメントとは?定義や目的、データの重要性などについて紹介
この手戻りは、単なる時間のロスというデメリットだけでなく、以下のような影響を及ぼす可能性があります。
- 甚大なコスト増大: 不良品の再加工にかかる労力と時間、廃棄される材料費、追加の輸送費といった実質的なコストに加え、問題対応に追われることで失われる生産機会の損失も大きなダメージとなります。
- 生産性の低下と納期遅延: 手戻り作業は、生産ラインの流れを阻害し、計画通りの生産を妨げます。結果として、納期遅延を引き起こし、顧客との信頼関係を損ねる原因にもなる可能性があります。
- 品質のばらつきとブランドイメージの棄損: 一度手戻りが発生すると、再加工の過程で品質が不安定になり、不良品が市場に出回ることでの企業のブランドイメージが傷つきます。
- 従業員のモチベーション低下: 頑張って製造したものがやり直しになる、あるいは顧客からのクレームに対応するといった手戻り作業は、現場の従業員の士気を著しく低下させる要因にもなります。
こうした事態を防ぐためにも、手戻りをゼロに近づけるための根本的な解決策を講じることが急務となっています。
本記事では、手戻りが発生してしまうメカニズムから、現状の品質管理の課題、そして、その課題を乗り越えるためのデジタル活用の例を紹介します。
「手戻り」発生のメカニズム
手戻りが製造業にとって避けたいムダの最たるものであることは理解いただけたと思います。
では、なぜこの厄介な「手戻り」は発生してしまうのでしょうか。
手戻りは、大きく分けて「品質不良の発生」と「その問題の発見の遅れ」という二つの要素が組み合わさることで発生し、深刻化するというメカニズムを持っています。
品質不良の発生
手戻りの最初の引き金は、製品や製造プロセスに何らかの品質上の問題が発生することです。
これは様々な段階で起こり得ます。
一つ目は、サプライヤーから調達した部品や原材料に、すでに品質上の問題があるケースです。これらは、まだ製品になる前の段階で、手戻りの元となります。
例えば、仕入れた電子基板に微細なハンダ不良があったり、小麦粉に異物が混入していたりといったケースです。
また、部品や原材料自体には問題がなくても、実際の製造プロセスの中で品質問題が発生することもあります。
例えば、作業員のヒューマンエラーや設備の機能不調や設定誤り、あるいは製造環境の不適切な管理などにより、設計通りの製品が製造されない場合などが挙げられます。
他にも、製品の設計そのものに欠陥があったり、顧客の要求仕様が製造部門に正しく伝わっていなかったりするケースもあります。
例えば、特定の条件下でしか発生しない製品の機能不具合が、設計段階で見過ごされていた場合などです。
この場合、設計段階から見直す必要があり、後工程で発覚すると最も大きな手戻りにつながります。
品質問題の発見の遅れ
品質不良が発生しても、それが早期に発見され、適切に対処されれば、手戻りの規模は最小限に抑えられます。
しかし、その工程で行われる検査や測定にミスがあったり、検査が不十分であったり、正確に実施されていなかったりすると、不良品がそのまま次の工程に流れてしまいます。
これは、本来であれば食い止められるはずの不良が、人為的な見落としや測定機器の不備、あるいは体制の不備によって見過ごされることで、後工程への波及を許してしまうメカニズムです。
例えば、製品の寸法検査で、測定器のキャリブレーション(調整・補正)が不十分だったり、検査員の目視判断にばらつきがあったりして、本来は不合格となるべき製品が合格と判断され、次工程へ進んでしまうケースが挙げられます。
加えて、そもそも必要なデータが取得されていなかったり、バラバラに管理されていて横断的に分析できなかったりすることも、問題の発見を遅らせる大きな要因です。
例えば、ある製造ラインで設備の一部に微細な不具合が発生し、それが製品の品質に影響し始めているにもかかわらず、設備の稼働データや品質データが日次・週次でしか集計されず、問題の兆候が数日経ってから初めて認識されるといったケースが考えられます。
この遅れにより、すでにその期間に生産された製品群が全て不良品となってしまい、大規模な手戻りが必要となります。
また、品質問題は、特定の部門や工程だけで完結することは稀です。設計、製造、品質保証、サプライヤー、さらには顧客など、関係者間での情報共有がスムーズでないと、問題の発見や対応が遅れます。
例えば、顧客から製品の不具合報告があったにもかかわらず、その情報が製造現場や設計部門に迅速に伝達されず、根本原因の究明や対策が遅れてしまうというケースが挙げられます。
このように、様々な原因で品質不良が発生し、その品質不良の発見が遅れたり、発見できなかったりすることで、手戻りが発生してしまいます。
従来の品質管理手法が抱える限界
上述した課題を克服するべく、製造業では様々な品質管理手法が用いられてきましたが、手戻りを完全に排除するには限界がありました。
目視検査や抜き取り検査の限界
これまで、多くの製造現場で品質検査の主役だった目視検査は、検査員の熟練度や体調、集中力に左右されやすく、見逃しが発生する可能性を常に含んでいます。
また、人間がチェックできる速度には限界があり、全数検査は現実的でないことが多いため、抜き取り検査が主流でした。
しかし、抜き取り検査では、サンプリングされた製品に異常がなくても、それ以外の製品に不良が潜んでいる可能性があり、不良品が後工程や市場に流出してしまうリスクをゼロにはできませんでした。
これにより、問題が発覚した際には、すでに多くの不良品が生産されてしまっており、大規模な手戻りが発生することになります。
紙ベースの記録や手動入力によるデータ管理の非効率性
品質データは、紙のチェックシートに手書きされたり、Excelに手入力されたりするケースは少なくありません。
この方法では、データの収集や集計に時間がかかり、リアルタイムでの状況把握が困難です。
そのため、問題の兆候があっても、データが分析される頃には手遅れになっている、ということがしばしば発生します。
また、手入力による入力ミスも手戻りの原因となることがあります。
部門間の情報連携不足と品質情報のサイロ化
品質に関わる情報は、設計部門、製造部門、品質管理部門、そして営業や顧客対応部門など、部門間をまたいで発生しますが、それぞれが独自のシステムや管理方法を用いていると、情報が分断されやすくなります。
これにより、ある部門で得られた品質に関する重要な知見が他の部門に共有されず、同じ問題が繰り返し発生したり、問題発生時の原因特定に時間がかかったりします。
問題発生後の対処療法
従来の品質管理では、不良品が発見された後にその原因を究明し、対策を講じるという「事後対応型」になりがちでした。
これは、不良品の発生を許容し、それをいかに素早く排除するかに重点を置くため、根本的な「手戻りゼロ」にはつながりにくいアプローチです。
真に手戻りをなくすためには、問題が起きる前にその兆候を捉え、予防的に対処する「未然防止型」の品質管理への転換が求められています。
これらの限界を乗り越え、手戻りを本質的に削減するためには、データドリブンなアプローチと、サプライチェーン全体を巻き込んだ体系的な仕組みが必要となります。
そして、上述した仕組みを構築するには、デジタル技術の活用が不可欠です。
デジタルを活用した手戻り削減のアプローチ
デジタル技術は、従来の品質管理手法では成しえなかった「データに基づいた客観的な判断」「サプライチェーン全体での連携強化」「予防的な品質管理への転換」を可能にし、手戻り削減を後押しします。
ちなみに、前回の記事では、センサーを活用したリアルタイムなデータ収集と監視を可能にするIoTを品質管理に導入するメリットや具体的な仕組み、導入ステップ、実際の事例について解説しました。
本章では、IoTを含む広範なデジタルを活用した解決策の一例を、前章の課題に対する具体的な仕組みとともに紹介します。
目視検査や抜き取り検査のデジタル化
熟練検査員の経験や勘に頼る目視検査や、全体の一部しか確認できない抜き取り検査は、見逃しや品質のばらつき、そして不良品流出のリスクを常に抱えていました。
そこで、製造ライン上の特定の位置にカメラを設置することで、製品の表面、部品の形状、組立状態などを詳細に撮影し、人間の目では見落としがちな微細な欠陥を客観的に検出できるようにするというアプローチが考えられます。
静止画や動画をデジタルデータとして取り込み、画像処理技術によって製品の輪郭を抽出したり、色や明るさの差を識別したり、特定のパターンを認識することで、キズや異物を検出することができます。
さらに、画像処理で抽出された特徴を、あらかじめ大量の正常品と不良品の画像を学習したAIに入力すれば、「これは人間が不良と判断するだろう」という微妙な色ムラや複雑な形状の変形といった、より複雑で曖昧な基準での判断が可能になるでしょう。
これにより、人間と同等、あるいはそれ以上の精度で全数検査を実施し、不良品が次工程や市場に流出するリスクを低減させることを目指します。
データ入力の自動化やデジタル化
紙やExcelでの手動入力に頼るデータ管理は、情報収集や集計に多大な時間を要し、リアルタイムでの状況把握を妨げていました。また、入力ミスも手戻りの原因となることがありました。
そこで、センサーから取得されるデータを入力情報とすることで、人の手を介さずに直接デジタルデータとしてシステムに送るという方法が挙げられます。このセンサーからのデータの自動収集は、前回の記事でも触れたIoTの重要な機能の一つです。
もしくは、作業員が検査結果を入力する場合も、あらかじめ設定された選択肢から選ぶ方式や、写真や動画のアップロードする方式にするなども有効でしょう。
そして、これらのデータを一元的なデータベースやクラウドプラットフォームに蓄積することで、リアルタイムでの集計や分析が可能となります。
さらに、収集されたデータは、ダッシュボードやレポートツールを活用することで、グラフや数値でリアルタイムに可視化することもできます。
これにより、生産ラインの稼働状況や品質の状態、不良品の発生箇所や傾向などを一目で把握できるようになり、問題発生時の状況認識と意思決定のスピードアップが期待できます。
これにより、手遅れになる前の対応を可能にし、大規模な手戻りの回避を目指します。
部門横断でのデータ共有と一元管理
品質に関わる情報は、設計、製造、品質管理、サプライヤー、顧客など多岐にわたる部門間で発生しますが、それぞれが独立したシステムや管理方法を用いていると、情報が分断され、問題発生時の連携が遅れる原因となっていました。
そこで、生産管理システムやERP(企業資源計画)、MES(製造実行システム)といった統合的なITシステムを導入することで、生産計画、工程進捗、品質データ、在庫情報、顧客情報などを一元的に管理し、部門横断でのデータ共有を実現します。
関連記事:製造業が活用するシステムについて詳しく知りたい方は、こちらの記事も参考にしてください。
生産管理システムとは?導入プロセスやメリットをわかりやすく解説
MES(製造実行システム)とは?機能や導入ステップ、課題などをわかりやすく説明
これにより、ある部門で発生した品質問題や得られた知見が、瞬時に他の関連部門に共有され、共通認識のもとで対策を講じることが可能になります。
また、原材料の受入から製造、検査、出荷、そして顧客までの各工程における品質データを紐づけて管理することも有効です。この品質データには、IoTセンサーから収集された工程内の詳細な情報も含まれます。
これにより、万が一問題が発生した場合でも、その問題がどの工程の、どのタイミングで発生したのかを素早く特定し、影響範囲を限定した効率的な対応が可能になります。
サプライヤーとのデジタル連携を進めれば、原材料段階からの品質情報を共有し、不良品の持ち込みを未然に防ぐこともできるでしょう。
AIで将来の不良発生を予測する
従来の品質管理では、不良品が発見されてから原因を究明し対策を講じる「事後対応型」が主流でした。
これは、手戻りをゼロにするというよりも、いかに早く不良品を排除するかに重点を置くため、根本的な解決にはつながりにくいアプローチでした。
そこで、蓄積された膨大な品質データや稼働データをAIが分析することで、品質不良が発生しやすい条件や傾向を特定し、将来の不良発生を予測するモデルを構築する、というアプローチが考えられます。
これにより、問題が顕在化する前に、予防的なメンテナンスを実施したり、製造条件を最適化したりといった未然防止策を講じやすくなります。
さらに、デジタルで収集されたデータは、品質問題の根本原因を特定するための強力なエビデンスとなります。
このデータに基づき、製造プロセスのボトルネックを解消したり、作業手順を改善したりすることで、不良品の発生そのものを抑制し、品質を継続的に向上させるサイクルの確立もできるかもしれません。
これらのデジタル活用はほんの一例ですが、品質管理にデジタルを活用するイメージを掴んでいただけたら幸いです。
無料メルマガ会員に登録しませんか?
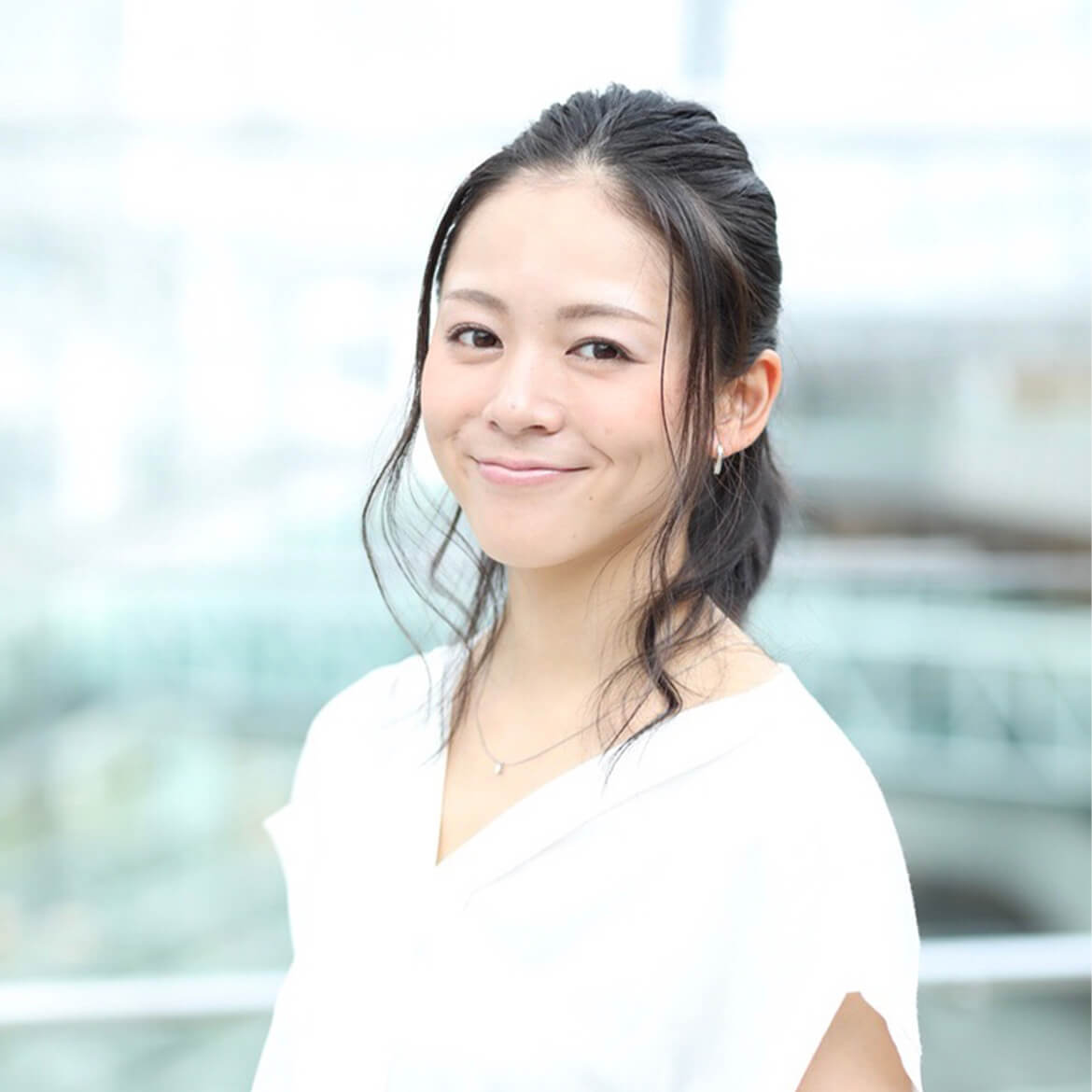
現在、デジタルをビジネスに取り込むことで生まれる価値について研究中。IoTに関する様々な情報を取材し、皆様にお届けいたします。